Expert Details
Traffic Accident Reconstruction, Motorcycles, All-Terrain Vehicles ATVs/ROVs/UTVs, Industrial Accident Reconstruction, Amusement Ride Accidents, Product Defect and Failure Analyses
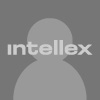
ID: 732537
North Carolina, USA
Extensive investigation experience in motor vehicle crash reconstruction of cars, light trucks, commercial tractor trailer trucks, motorcycles, all-terrain vehicles (ATVs), recreational off-highway vehicles (ROVs) and pedestrian collisions. Expert has extensive knowledge of commercial tractor-trailer trucks; He has a Class A Commercial Driver’s License (CDL); Very familiar with the Federal Motor Carrier Safety Regulations 49CFR 100-185 Hazardous Materials; 49CFR 300-399 for commercial tractor-trailer trucks which includes the air brake systems, pre-trip, during-trip and post-trip inspections, professionally driving and operating tractor-trailer trucks.
Expert has hazardous materials training and certification. Avid motorcycle rider and expert in the function, handling of motorcycles, product defect and failure analyses and motorcycle crash reconstruction which includes impact velocity calculations. He has extensive knowledge, training, experience and engineering education in analyzing complex vehicle and pedestrian crashes, incorporate state-of-the-art computer video simulation software technology to demonstrate and animate how a motor vehicle, commercial tractor trailer truck, motorcycle or pedestrian crash takes place; Extensive training, knowledge and experience in imaging and analyzing the crash data reports stored in a car or light truck’s event data recorder (EDR) and a commercial tractor-trailer truck’s electronic control module (ECM) data.
He has been involved in product defect and failure analyses of cars, light trucks, heavy commercial vehicles, motorcycles, ATV’s, ROV’s and their components; Create CAD drawings for trial exhibits. Can build models for trial exhibits; Has written and submitted expert reports for state and federal courts for trial; Has given expert deposition and courtroom trial testimony; Attend and participate in various seminars regarding research in imaging and analyzing a vehicle’s crash data reports and heavy commercial trucks ECM data; Attend and participate in staged motor vehicle collisions and associated analyses for research involving cars, light trucks, commercial heavy trucks, motorcycles and pedestrians.
Since 2003, expert has more than 15 years of experience providing forensic engineering services in industrial accidents to law firms and insurance companies. He has approximately 20 years of industrial work experience including machine design, gantry crane design, conveyor design and quality assurance; Automotive engineer; Worked in the automotive industry for approximately nine years; Extensive investigation and reconstruction experience of many types of industrial accidents. He worked for the inventor of the forklift and manufacturer of heavy off-road earth moving machinery namely Clark Equipment; Machined and assembled rough terrain forklift and rough terrain crane drive train components including transmissions, driver steer axles and differential units. The process equipment used to machine component parts were both the older type NC tape operated controllers as well as the modern CNC controllers using G,M,T,S,D,P,N codes; Have 1000+ hours of experience in the day-to-day operation of forklifts over a five year period which included material handling operations. He has worked as a mechanical design engineer for various companies which involved OSHA safety regulations 29CFR1910, 1926, 1928, process machine design, continuous improvement projects and quality assurance.
Expert also provide forensic engineering service to investigate the cause of Amusement Park Ride accidents; has been retained in cases involving patron go-karts rides, patron ride restraint system design, patron ride machines incorporating gondolas, ride machine support structural failure by applying his engineering education and training, knowledge and experience in mechanical machine design as well as the interpretation of the Amusement Park Ride ASTM F24 Committee standards. Expert will determine whether or not the amusement rides device is designed properly for its intended purpose or is defective by design and what component(s) failed in service and why it failed to cause an accident. Expert will also opine on Amusement Park Ride Standards of Maintenance and Standards of Care.
Expert has setup a warehouse for forklift use and FIFO, has thousands of hours of experience operating gantry cranes during process machining and assembly operations. He has design engineering experience in overhead gantry cranes and belt conveyors as well as other types of industrial process equipment; Have investigated industrial accidents while working as a staff engineer in industry and have investigated many industrial accidents as a litigation expert since 2003.
Have extensive engineering education, knowledge, training and experience in analyzing complex vehicle and pedestrian crashes, incorporate state-of-the-art computer video simulation software technology to demonstrate and animate how a commercial tractor trailer truck, motorcycle, ATV or pedestrian crash takes place; Extensive training, knowledge, experience and equipment in imaging and analyzing the crash data reports (CDR) stored in a car or light truck’s event data recorder (EDR); Extensive training, knowledge, experience and equipment in imaging and analyzing commercial tractor trailer truck’s Electronic Control Module (ECM) run data concerning speed, engine rpm, hard stop braking and last stop; Involved in product defect and failure analysis of cars, light trucks, heavy commercial vehicles, motorcycles, ATV’s, ROV’s and their components; Create CAD drawings for trial exhibits. Can build models for trial exhibits; Have written and submitted expert reports for state and federal courts for trial; Have given expert deposition and courtroom trial testimony; Attend and participate in various seminars regarding research in imaging and analyzing a vehicle’s crash data reports and heavy commercial trucks ECM data; Attend and participate in staged motor vehicle collisions and associated analyses for research involving cars, light trucks, commercial heavy trucks, motorcycles and pedestrians.
General Industry and OSHA Safety:
Chesapeake Consulting: Constraint Management Applications. Certificate
Mesa Consulting Group Incorporated: Six Sigma. Certificate
North Carolina State University: ISO 9001: 2000 Internal Quality Auditing. Certificate
Forsyth Technical Community College: Pro-Engineer 2001 CAD Software Training. Certificate
Guilford Technical Community College: General Contractor’s Licensing Preparation Course including
OSHA General Industry Regulations and OSHA
Measuring and Improving Boiler Efficiency – Advanced. Certificate
OSHA 29 CFR 1926 Construction Industry Regulations and Major Hazard and Prevention Strategies. Certificate
OSHA Industrial Accident Investigation. Certificate
Forklift Operation Safety, Certification and Licensing Course. Certificate
Combined Heat and Power – Utilities Power Generation. Certificate
Chiller Plant Optimization. Certificate
Forklift Operation Safety, Certification and Licensing Course. Certificate
DOT Hazardous Material Transportation Regulations Training and Certification
Amusement Park Ride Safety
International Association of Amusement Parks and Attractions (IAAPA): Operators Forum for
the American With Disabilities Act.
Motor Vehicle Crash Reconstruction:
Traffic Crash Reconstruction involving cars, light trucks, school buses, bicycles, heavy
commercial trucks, motorcycles, bicycles and pedestrians.
At-Scene Investigation and Evidence Mapping.
Slow and High Velocity Collisions, Drag Factor, Skid Analyses, PDOF, ΔV, Closing Velocity, Conservation Linear and Angular Momentum, Conservation of Mechanical Energy, Crush Damage Analyses, Crush Energy, Critical Velocity and Circular Motion, Dynamic Weight.
Car/Light Truck Event Data Recorder (EDR) Report Imaging, Analysis and Interpretation.
Heavy Commercial Tractor Trailer Truck Crash Investigation.
49 CFR 100-399 Federal Motor Carrier Safety Regulations.
Commercial Tractor-Trailer Truck Electronic Control Module (ECM) Operational Data
Imaging Analysis and Interpretation.
School Bus Accidents.
Motorcycle Crash Reconstruction.
Shift, Falls, Flips Vaults, Rollovers.
Lamp Filament Analyses.
Airbag Operation and Failure Analyses.
Seat Belt Operation and Failure Analyses.
All Terrain Vehicles (ATVs) Crash Reconstruction.
Recreational Off-Highway Vehicles (ROVs) Crash Reconstruction.
Motor Vehicle Product Defect and Failure Analyses.
Motor Vehicle Inspections.
Vehicle Standards of Care.
Product Defect and Failure Analyses.
Vehicle Crash Testing.
Vehicle Braking and Skid Testing.
Vehicle Suspension and Handling Testing.Industrial Accident Investigation/Reconstruction:
Amusement Ride Accidents/ASTM F24 Standards/Standards of Maintenance/Standards of
Care and Operation/Product Defect and Failure Analysis.
Industrial Accidents/OSHA Safety/Machine Guarding/Hazard Investigations/ Product Defect
and Failure Analysis Investigations:
»Workman’s Compensation Cases.
»Machine Guarding Accidents.
»Poultry Process Equipment Accidents.
»Fabric Rollup Machines Accidents.
»Conveyors Accidents.
»Construction Equipment Accidents: Scaffold Failures, Scissor Lift Failures,
Ladder Failures, Folding Benches, Belt Sanders, Saws.
»Automatic Storage and Retrieval Systems (AS/RS)(AGV) Forklift Accidents.
»Scissor Lift Accidents.
»Forklift Accidents.
»Pallet Jack Accidents.
»Ladder Accidents.
»Loading Dock Accidents - Dock Lift, Dock Leveler and Dock Plate Accidents.
»Power Plant Accidents.
»Power Tool Accidents: Belt Sanders, Radial Miter Saws.
»Exercise Strength Training Equipment Accidents.
»Lawn Mower Accidents.
»Lawn Aerator Accidents.
»Escalators Accidents.
»Crane Accidents.
»High Voltage Power Line Tower Structures Failure Accidents.
»Product Safety Signs, Symbols, Warnings and Labeling.
»Product Safety Information in Product Manuals, Instructions and Other Collateral
Materials.
»Wood Working Machine Accidents.
»Abrasive Shotblaster Accidents.
»Motor Vehicle Coil Spring Compressors Accidents.
Education
Year | Degree | Subject | Institution |
---|---|---|---|
Year: 1990 | Degree: Bachelor of Science | Subject: Mechanical Design Engineering | Institution: North Carolina State University |
Year: 1990 | Degree: Associate in Science | Subject: College Transfer Curriculum | Institution: Mitchell Community College |
Work History
Years | Employer | Title | Department |
---|---|---|---|
Years: 2002 to Present | Employer: Undisclosed | Title: Crash Accident Reconstruction | Department: |
Responsibilities:Traffic Crash Reconstruction involving cars, light trucks, school buses, bicycles, heavy commercial trucks, motorcycles, bicycles and pedestrians.At-Scene Investigation and Evidence Mapping. Slow and High Velocity Collisions, Drag Factor, Skid Analyses, PDOF, ΔV, Closing Velocity, Conservation Linear and Angular Momentum, Conservation of Mechanical Energy, Crush Damage Analyses, Crush Energy, Critical Velocity and Circular Motion, Dynamic Weight. Car/Light Truck Event Data Recorder (EDR) Report Imaging, Analysis and Interpretation. Heavy Commercial Truck Crash Reconstruction. 49 CFR 100-399 Federal Motor Carrier Safety Regulations. School Bus Accidents. Motorcycle Crash Reconstruction. Shift, Falls, Flips Vaults, Rollovers. Lamp Filament Analyses. Airbag Operation and Failure Analyses. Seat Belt Operation and Failure Analyses. All Terrain Vehicles (ATVs) Crash Reconstruction. Recreational Off-Highway Vehicles (ROVs) Crash Reconstruction. Motor Vehicle Product Defect and Failure Analyses. Motor Vehicle Inspections. Vehicle Standards of Care. Product Defect and Failure Analyses. Vehicle Crash Testing. Vehicle Skid Testing. Vehicle Suspension and Handling Testing. |
|||
Years | Employer | Title | Department |
Years: 2002 to Present | Employer: Undisclosed | Title: Industrial Accident Investigation and Reconstruction | Department: |
Responsibilities:All OSHA 29CFR1910, 1926 and 1928 Industry Safety Regulations andApplicable ANSI, ISO, ASME, UL, ASTM, ASTM F24 Standards. Machine Operator Safety and Practice. CNC Machine Program Coding for Component Production. Machine Guarding. Shipping/Receiving/Loading Docks. Lockout/Tagout Requirements. Process Equipment Maintenance and Standards of Care. Product Defect and Failure Analyses. Product Safety Signs, Symbols, Warnings and Labeling. Yard Machines. Forklift Accidents. Crane Accidents.. Hand Operated Tools. Many other types of industrial process equipment and standards of care. Amusement Park Ride Accident Investigation. |
|||
Years | Employer | Title | Department |
Years: 2005 to 2006 | Employer: K&S TOOL AND MANUFACTURING COMPANY | Title: Quality Control, Process Engineering, Maintenance and Safety Manager | Department: |
Responsibilities:ISO 9001:2000 registered contract manufacturer of machined, formed, punched, fabricated, welded and assembled parts and subassemblies. Machined, formed and fabricated, welded and assembled component parts and subassemblies for client companies.Managed the quality control department and had supervisory responsibilities. Responsible for the ISO quality system, quality manual and other similar documentation and files. Involved in APQP and PPAP for special customers. Made changes and updates to the quality system as needed. Acted as ISO management representative for the company. Organized and scheduled training sessions for company employees on matters of ISO 9001:2000 standards, OSHA safety, human factors and newly hired employees. Managed and performed monthly internal quality audits on quality system elements. Lead and motivated employees to quality check their product. Performed first article inspections with report documentation for both customers and employees utilizing company measuring equipment. Created, followed up, closed and filed quality action plans, corrective action reports, preventive action reports, continuous improvement reports and other similar documentation. Also managed the maintenance program. Assisted in the design of a bearing press machine for functionality, safety and human factors. Managed and documented all maintenance activities and schedules. Hands-on from time to time. Managed the installation of all purchased and incoming machinery. Managed all facility related matters concerning building maintenance, HVAC and electric utilities. Acted as resident company engineer in all engineering matters including plant engineering, machine and tool design and OSHA 29CFR1910 safety audits and OSHA regulations. Was company Safety Manager. Created and distributed plant facility evacuation charts. Performed safety audits on all plant facilities and equipment including kinetic energy punch presses, hydraulic presses, automatic laser cutting machines, vibratory media deburring and cleaning equipment; press brakes, automatic robotic welding machines, CNC machining centers and hazardous chemicals including water based metal cutting coolants and petroleum based oils. Managed the distribution of MSDS and audited all MSDS books. When a safety issue was discovered, the safety issue was corrected. Worked with the shipping/receiving department regarding the inspection and management of damaged containers and product that were received from domestic and over seas companies. (Worked for K&S Tool temporarily to earn capital funds) |
|||
Years | Employer | Title | Department |
Years: 2001 to 2002 | Employer: SPHERION GREENSBORO | Title: Process Verification-Validation Engineer | Department: Contract Engineering |
Responsibilities:Provided engineering services to Bristol Myers Squibb, a manufacturer of ostomy, wound care products and pharmaceuticals.Assisted in the modification and retrofit of production machinery for ostomy pouch manufacturing. Created and implemented process validation protocals IQP, PQP, OQP and DOE and statistical methods with reports per FDA GHTF and cGMP guide lines for approval to launch MK4 ostomy pouch process into production. Provided engineering support to a new prototype Digital Label Printing Line. Benchmarked the process, gathered downtime data, trouble-shooting of equipment designs, and made recommendations to engineering manager on how to improve up-time. Decreased downtime by 40%. Created written PM schedules and trouble-shooting guides. Designed and installed a protective cover for a 15 watt class 4 marking laser to meet OSHA, ANSI and ISO safety requirements of a class 1 laser. (Contract assignment was completed) |
|||
Years | Employer | Title | Department |
Years: 1999 to 2001 | Employer: ERICO INCORPORATED ABERDEEN | Title: Mechanical/Manufacturing Engineer | Department: |
Responsibilities:ISO-9002 and UL Listed manufacturer of grounding, electrical and structural support systems for the residential and commercial construction industry. Utilized Microsoft computer software and AutoCad 14 extensively.Expedited and managed capital and expense projects, cost reduction, continuous improvements integration of OSHA 29CFR1910 safety requirements for ergonomic and lean manufacturing which included spot welding, wire drawing, copper plating, rod straightening, kinetic energy punch presses and cut-to-length operations. Used Six Sigma, SPC, problem solving, root cause analysis techniques, lean manufacturing, PFMEA, DFMEA, APQP, QIP, CIW and Kaizen extensively. Established and led cross-functional teams for Centers of Excellence throughout the corporation. Established and led Six Sigma, QIP, CIW and Kaisen teams to reduce downtime, increase productivity, train personnel in lean manufacturing techniques, equipment operation theory and preventive maintenance. Developed and implemented a Six Sigma based statistical process and quality control system (SPC) for all departmental processes. Documented and tracked all project time lines, cost, cost savings, downtime reduction and process improvements. Monitored production schedules, inventories, production issues, product scheduling, and scrap levels. Communicated with production scheduler and production manager concerning production runs and production concerns. Created and controlled line documentation such as process flow mapping, work instructions, quality standards instructions, tooling specifications, tooling layouts and control plans. Coordinated and relocated a complete automated roll forming line from Ohio to the North Carolina facility. Redesigned blanking press die tooling for 75 ton Minster OBI strut pre-notch punch presses. Implemented SMED. Installed safey blocks required by OSHA 29CFR1910. Installed a coolant spray system to add lubricity to a formally dry punching operation. Human factors studies were performed during the design process. These changes increased tool life three times and reduced replacement tooling cost achieving a total yearly cost savings of $100,000. As a result of these continuous improvement projects, reversed a negative $110,000 per month variance to a positive $40,000 per month variance and reduced setup time by 75%. Designed and installed an enclosed in-process automated spraying system to apply a rust preventative to strut products to eliminate oxidation problems creating a superior product compared to the competition and met all OSHA 29CFR1910 safety requirements. Redesigned Flexibar assembly tooling to eliminate scrap and customer claims and achieved a yearly cost savings of $20,000. Designed and supervised the installation of a hazardous chemical containment area for the storage of acids, bases and oxidizers per OSHA 29CFR1910 hazardous material regulations. Designed a 30 foot belt conveyor for strut operations with an ergonomic and easy-to-use automatic ejection mechanism to replace an existing manual conveyor and saved $8000 by designing and building it in-house. The conveyor was guarded to meet OSHA 29CFR1910 regulations. Human factors studies were performed during the design process. Performed a complete design load and stress analysis on an existing in-house fabricated below-the-hook lifting device per ASME B30.20 standard. This lifting device was used for tranfering 6500 pound sheet metal rolls from pallet to process equipment. It was determined that the lifting device design had not been tested by a second party testing lab and did not have the ASME B30.20 required data plate. The lifting device was permanently removed from service and replaced with a commercially available below-the-hook lifting device. |
|||
Years | Employer | Title | Department |
Years: 1998 to 1999 | Employer: GKN AUTOMOTIVE ROXBORO, | Title: Automotive Engineer Mechanical Design/Manufacturing/Process | Department: |
Responsibilities:Manufacturer of automotive constant velocity half shaft assemblies. Responsibilities included expediting and managing capital projects, cost reduction, continuous improvement, ergonomic integration of OSHA 29CFR1910 safety requirements for the assembly of automotive constant velocity half shafts in a Tier 1, ISO9001 and QS9000 facility.Utilized Japanese philosophies of Kaizen, Poka Yokes, Zero Defects, Brainstorming, Waste Elimination, 5-S, FMEA, lean manufacturing and Kan Ban material control systems. Used Six Sigma, problem solving and root cause analysis techniques extensively. Extensively utilized a Six Sigma based statistical process and quality control system (SPC) for all assembly cells. Documented and tracked all project time lines, cost, cost savings, downtime reduction and process improvements. Created and controlled line documentation such as process flow mapping, work instructions, quality standards instructions, tooling specifications, tooling layouts, control plans and SPC documents. Designed and built special ergonomic assembly tooling and fixturing that met OSHA 29CFR1910 regulations for continuous improvement and new program launches. Human factors studies were performed in the design process. Monitored production schedules, inventories, production issues, product scheduling, scrap levels and communicated with production coordinators concerning production runs and production concerns. Processed ECN’s in department. Was directly responsible for the hands-on repair and maintenance of assembly equipment, machine downtime tracking and improvement flashes across three shifts 24 hours per day. Coordinated maintenance activities with maintenance manager. Was directly responsible for ordering and inventories of all machine component maintenance items, new program, improvement design and replacement tooling. Facilitated and managed quality improvement processes and continuous improvement workshops with respect to each cell, it’s operators and equipment.Managed the installation of new assembly cells for new program launches. Inspected and assessed equipment to meet safety requirements of OSHA 29CFR1910 regulations. Performed machine capability studies, PSW, product master samples, tooling plans, control plans and documented changes for PPAP submission to customers. Created all line documentation for process production launches. Heavily involved in hands-on maintenance of process and material handling equipment. (Resigned position to seek other employment) |
|||
Years | Employer | Title | Department |
Years: 1997 to 1998 | Employer: COPELAND CORPORATION HARTSELLE | Title: Mechanical/Manufacturing Engineer | Department: |
Responsibilities:Manufacturer of residential HVAC refrigeration compressors. Responsibilities included expediting and managing capital projects; cost reduction; continuous improvement; ergonomic integration of OSHA 29CFR1910 safety requirements for machining aluminum pistons and rods, cast iron cylinders blocks and heads.Utilized Japanese philosophies of Kaizen, Poka Yokes, Zero Defects, Brainstorming, Waste Elimination, 5-S, FMEA, ergonomic lean manufacturing. Used Microsoft computer software extensively and AutoCAD for design purposes. Redesigned a two machine 4-axis CNC work cell eliminating 3 operators saving $94,000 in direct labor cost. Human factors studies were performed in the design process. Assisted in the redesign of all compressor bodies for more efficient work holding. Redesigned CNC machining center work holding clamps to match the body redesign for scrap reduction. Processed ECN’s in department for product design changes. Heavily involved in hands-on maintenance of process equipment. Created work instructions, machinery setup instructions and machinery operation parameters. Created bid packages for capital equipment quotation, cost justifications, appropriations requests. Coordinated maintenance activities with maintenance manager. (Due to future marriage and relocation, resigned position to accept new position with GKN Automotive) |
|||
Years | Employer | Title | Department |
Years: 1995 to 1997 | Employer: KOYO BEARINGS ORANGEBURG | Title: Automotive Engineer Mechanical/Manufacturing/Process | Department: |
Responsibilities:Manufacturer of high performance automotive wheel bearings. Responsibilities included expediting and managing cost reduction, and continuous improvement projects, integration of OSHA 29CFR1910 safety requirements for CNC turning, grinding and automatic assembly of SAE1055 and SAE 52100 steel bearing inner and outer rings.Utilized Japanese philosophies of Kaizen, Poka Yoke, Zero Defects, Brainstorming, Waste Elimination, 5-S, FMEA, ergonomic lean manufacturing and Kan Ban material control systems. ISO9002 certification was awarded to Koyo during May of 1996. Was heavily involved with documentation development for certification. Extensively utilized automated statistical process and quality control system (SPC) which was built into all manufacturing processes. Traveled to Osaka, Japan to prove off $6,500,000 of capital equipment including completely automatic CNC Murata MW series and LE type Miyano two axis turning centers, Koyo and Toyo shoe type centerless grinders and plunge type forming grinders and automated assembly machines. Personally performed floor lay out and supervised equipment installation upon arrival. Assisted in the creation of work instructions, quality standards instructions, tooling specifications and tooling layouts for processes. Performed continuous improvements of bearing manufacturing process through extensive carbide insert and grinding wheel testing. Saved Koyo $157,000 per year in tooling cost by changing metal cutting fluids and through carbide insert testing. Heavily involved in hands-on maintenance of all automated process and material handling equipment. Received classroom training on how to successfully write CNC coded programs utilizing the G,M,T,S,D,P,N coedes to setup a multi-axis machining center for component part production. Modified Machining CNC programs to reduce cycle time and increase tool life. Redesigned the loading mechanism of an automatic ABS pulser ring assembly press for changing from an INA to FAG pulser ring meeting safety requirements of OSHA 29CFR1910 regulations.Authored company math textbook and taught mathematics in classroom setting for testing and screening potential full-time hourly employees. (Resigned position to accept new position with Copeland Corporation) |
|||
Years | Employer | Title | Department |
Years: 1994 to 1995 | Employer: DML INDUSTRIAL PRODUCTS | Title: Mechanical/Manufacturing Engineer | Department: |
Responsibilities:Manufacturer of high speed steel tooling for the wood and metal working industry.Responsibilities included expediting and managing cost reduction, and continuous improvement projects, integration of OSHA 29CFR1910 safety requirements for CNC and NC turning and grinding operations. Responsibilities included expediting and managing capital projects, cost reduction, continuous improvements and ergonomic integration of OSHA 29CFR1910 safety requirements for manufacturing high speed steel tooling. Designed, built and installed an ergonomic manufacturing process to support a Lindberg homo steam tempering furnace for applying a high temperature dark blue ferric oxide surface treatment for high speed steel drill bits. Designed, built and installed a 60 foot structural steel overhead monorail crane for lifting furnace payloads in excess of 2,000 pounds per ASME B30.11 standard. Crane and equipment met the requirements of OSHA 29CFR1910 crane regulations. Human factors studies were performed in the design process. Created written operation and setup manuals for this operation. Assisted in the design of an ergonomic manufacturing cell to produce high speed steel S&D drill bits. Equipment included a Hertlein spiral flute grinder, two centerless grinders, a relief grinder, a Winslow drill pointer, tables and gravity conveyors. Human factors studies were performed during the design process. Created written operation and setup manuals for this cell. This cell eliminated three operators and saved DML $112,320 per year in direct labor cost. Also processed ECN’s in department. Performed grinding wheel tests on Hertlein spiral flute grinders to improve grinding wheel performance and life. Grinding wheels used and tested were made by Norton and Carborundum. Installed a coolant recycling system to recycle used coolant. Created written operation and setup manuals for this system. This system saved DML $6,000 per year. Created bid packages for capital equipment quotation, cost justifications, and appropriations requests. Coordinated maintenance activities for process and material handling equipment with maintenance manager. (Accepted new position with Koyo Corporation due to imminent layoff and plant closure) |
|||
Years | Employer | Title | Department |
Years: 1994 to 1994 | Employer: CONTROLS SOUTHEAST INCORPORATED | Title: Mechanical Design Engineer | Department: |
Responsibilities:(Temporary Contract Position)Was under temporary assignment to assist the design engineering department in the planning, design, manufacture and assembly of a testing apparatus to run experiments and gather transient heat transfer data in the form of Temperature vs. Time in order to generate temperature tables and graphs for the analysis of data to determine the overall heat transfer coefficients and time transients of various heat transfer cements during startup heat flow. Was responsible for all testing and data collection. After testing and data collection was completed, created a detailed scientific report and submitted it to the company management for their future use. (Contract assignment completed) |
|||
Years | Employer | Title | Department |
Years: 1993 to 1993 | Employer: FISHBURNE INTERNATIONAL | Title: Draftsman | Department: |
Responsibilities:(Temporary Contract Position)Modified engineering drawings for existing products. (Contract assignment was completed) |
|||
Years | Employer | Title | Department |
Years: 1992 to 1993 | Employer: FOXCROFT TEMPORARIES | Title: Draftsman | Department: |
Responsibilities:(Temporary Contract Position)Created detailed instrument drawings for existing products for a client company. (Contract assignment was completed) |
|||
Years | Employer | Title | Department |
Years: 1992 to 1992 | Employer: B&W NUCLEAR TECHNOLOGIES | Title: Tool Design Engineer | Department: |
Responsibilities:Manufacturer of nuclear fueled electric power generation facilities. Responsibilities included the design of manufacturing tooling for Uranium 235 commercial nuclear reactor fuel assemblies. Managed cost reduction and continuous improvement projects and integration of OSHA 29CFR1910 and NRC safety regulations for manufacturing Uranium 235 commercial nuclear reactor fuel assemblies.Developed tig spot welding jig and a spring compression leaf jig for assembling rod cluster control assemblies (RCCA). Reduced assembly time 30 minutes per unit, a 99% reduction in assembly time. Human factors studies were performed during the design process. Performed detailed design load analysis for all fuel assembly lifting fixtures. It was determined through the analysis that fixtures met OSHA 29CFR1910 and NRC regulations. Performed safety audits. Tested personal protective equipment human body harness and lanyard equipment used on personnel lifts. Determined that the lanyard design was dangerous and had it removed from service permanently. All tooling design was performed using Personal Designer 3-D modeling CAD software. |
|||
Years | Employer | Title | Department |
Years: 1991 to 1991 | Employer: MORRIS AND ASSOCIATES GARNER | Title: Assistant Engineer | Department: |
Responsibilities:Responsibilities included modifying engineering hand drawings for existing products.(Resigned to seek other employment) |
|||
Years | Employer | Title | Department |
Years: 1984 to 1984 | Employer: VICKERS FLUID PUMPS | Title: Factory Technician | Department: |
Responsibilities:Was employed by Vickers during a summer job while in college to machine component parts, assemble and test gear pumps. Operated OD grinders to precision grind the OD’s of the gear shank and gear teeth. Operated an automated brush machine that polished the gear teeth sides. Worked in assembly to assemble gear pumps. Also operated a test stand to test the pumps for output pressure, function and break-in. Left Vickers to go back to attending college classes at the end of the summer. (Returned to university after summer break) |
|||
Years | Employer | Title | Department |
Years: 1978 to 1983 | Employer: CLARK EQUIPMENT | Title: Automotive Machinist/Assembly Technician | Department: |
Responsibilities:Manufacturer of heavy off-road earth moving machines, cranes and forklifts. Clark Equipment invented the forklift and the Bobcat and was the main competitor to Caterpillar.Assembled drive steer, road grader and telescoping crane axle assemblies on both a moving assembly line and fixed assembly bench. Also assembled and tested transmissions and differential units. Ergonomically modified assembly bench cell layout and increased assembly production from 5 Gallion axles per shift to 10 Gallion axles per shift. Was commended by plant manager for production increase. Human factors were taken into consideration during the design process. Setup and operated high production high precision automatic CNC operated and NC tape operated metal cutting machining centers including vertical and horizontal multiaxis turrent lathes, broaches, multispindle drill presses and tapping machines, milling machines, transfer lines, shaft spline rollers, gear shapers and shavers and boring machines. Set up and operated OD, ID and surface grinders using resinoid and vitrified bonded grinding wheels. Assisted heat treatment department in heat treating spur and spiral bevel ring and pinon gears, shafts and spindles using methods of oil quenching and induction hardening. Was a licensed forklift operator for the duration of employment. When required, performed plant wide material handling responsibilities by driving forklifts to load machine cells with pallets of component parts and also distribute materials throughout the facility. Have over 1000+ of hands-on day-to-day experience operating forklifts. Enrolled at Mitchell Community College evenings part-time for college transfer courses. |
|||
Years | Employer | Title | Department |
Years: 1978 to 1978 | Employer: BERNHARDT FURNITURE COMPANY | Title: Machine Operator | Department: |
Responsibilities:Machine Operator (Pre-College Work Experience)Manufacturer of home wood furniture. Set up and operated various wood working machines and machined wood furniture components to print specifications. Machine types included turning and knife lathes, routers, shapers, sanders, boring machines and dove tail machines. |
|||
Years | Employer | Title | Department |
Years: 1978 to 1978 | Employer: BEAUTYMAID MILLS | Title: Machine Operator | Department: |
Responsibilities:Manufacturer of feminine textile products.Setup and operated cloth handling machines to unfold and transfer cloth from one spool to another. Unfolded rolls of cloth to be used for product manufacturing. Operated electric knives to shear and cut several layers of cloth to the shapes of a paper patterns. |
|||
Years | Employer | Title | Department |
Years: 1975 to 1978 | Employer: KEWAUNEE SCIENTIFIC FURNITURE CORPORATION | Title: Shipping Clerk | Department: |
Responsibilities:Manufacturer of scientific laboratory furniture.Loaded and unloaded commercial tractor trailer trucks using hand trucks and pallet jacks. Operated dock levelers to allow tractor trailer trucks access to shipping and receiving. Also operated various wood working machines to machine wood furniture components to print specifications. |
Career Accomplishments
Associations / Societies |
---|
National Society of Professional Engineers American Society of Mechanical Engineers National Academy of Forensic Engineers National Association of Professional Accident Reconstruction Specialists Society of Automotive Engineers American Motorcyclist Association American All-Terrain Vehicle Association International Association of Amusement Parks and Attractions North Carolina Truckers Association |
Licenses / Certifications |
---|
PROFESSIONAL LICENSURE North Carolina Board of Examiners for Engineers and Surveyors Florida Board of Professional Engineers South Carolina Board of Registration for Professional Engineers and Land Surveyors Georgia State Board of Registration for Engineers and Surveyors Louisiana Professional Engineering and Land Surveying Board Tennessee Architect and Engineering Board Virginia Board For Architects, Professional Engineers and Land Surveyors New Jersey Board of Examiners for Engineers and Surveyors Washington, DC Board of Professional Engineers West Virginia State Board of Professional Engineers Mississippi Board of Licensure for Professional Engineers and Surveyors Maryland State Board of Professional Engineers. |
Professional Appointments |
---|
AMERICAN NATIONAL STANDARDS SUBCOMMITTEES ANSI/ASSE A10.8 – Scaffolding Safety Requirements. PROFESSIONAL TRAINING AND DEVELOPMENT Public Speaking and Communications: Dale Carnegie Course: Public Speaking and Public Relations. Certificate Mitchell Community College and North Carolina State University Public Speaking Courses. Degrees Midlands Technical Community College: Train The Trainer. Certificate Traffic Accident Reconstruction: North Carolina Commercial Drivers Licence (Class-A CDL) for Driving and Operating Commercial Tractor-Trailer Trucks License. Endorsements: Tanker, HazMat and Triples. DOT Hazardous Material Transportation 49CFR 100-185 Training and Certification North Carolina School Bus Training; have Passenger and School Bus Endorsements North Carolina State University: Machine Design, Dynamics and Mechanics of Machines and Vehicles, Motor Vehicle Traffic Accident Reconstruction Sciences. BSME University of North Carolina: Introduction To Forensic Engineering. Certificate Northwestern University Research in Traffic Accident Reconstruction Institute For Police Technology and Management Research in Traffic Accident Reconstruction National Academy of Forensic Engineers: Forensic Engineering Seminars Collision Safety Institute: Automotive Crash Research Testing & Training. Certification Collision Safety Institute: Bosch Diagnostics Crash Data Retrieval System Download and Analyses Training and Certification iWitness Close Range Photogrammetry. Certificate Insurance Institute for Highway Safety and Highway Loss Data Institute: Vehicle Crashing Test Comparisons and Ratings. Seminar Chief Automotive Technologies: Vehicle Construction Technology and Trends. Seminar SAE Tractor-Trailer Event data Recorder Symposium ARC-CSI Vehicle Crash Conference Crash Data Retrieval Systems Summit Houston Texas. Certificate. Vehicle were crash tested at these summits. Aras 360 HD/Reality 4 day Crash Simulation training Course. Certificate Engineering Dynamics Corporation: Advanced Vehicle Dynamics and Crash Simulation 5 Day Course. Certification ARC-CSI Boot Camp and Crash Conference; Crash Testing of Motor Vehicles. Certificate ACTAR Examination Preparation Course Northwestern University – Traffic Crash Investigation/At-Scene Investigation/Evidence Mapping (15) Northwestern University – Commercial Truck Crash Reconstruction Northwestern University – Pedestrian Vehicle Crash Reconstruction Truck Pro: Commercial Tractor Trailer Truck Air Brake Seminar Northwestern University – Commercial Truck ECM Data Imaging and Analyses DOT Hazardous Material Commercial Transportation Regulations 49CFR 100-185 Training and Certification. Motorcycle Riding and Training: Avid motorcyclist for over 30 years riding both trail, motocross and street motorcycles. Dirt Bike Motocross Racing/Trail Riding Motorcycle Safety Foundation: Advanced Rider’s Training. Certification Harley Owners Group: Chapter 3446 Group Riding Class. Certificate Big Bear Choppers: How To Build a Custom Motorcycle Bike Safe North Carolina – Instructed by the Cary Police Department in cooperation with the North Carolina Highway Patrol. Certificate Currently own and ride two street motorcycles: 2012 Harley-Davidson CVO Screamin Eagle Road Glide Custom and a 2018 Harley-Davidson Fatboy. ATV Riders Training: ATV Safety Institute - ATV Rider Course: ATV Rider Certification Owned and rode a 2007Honda FourTrax TRX 420 TE/FE Rancher. Many more examples available upon request. |
Awards / Recognition |
---|
North Carolina State University MAE Hall of Fame |
Publications and Patents Summary |
---|
TECHNICAL PAPERS AND PUBLICATIONS The Physics of a Collision Product Design, Product Manufacturing and Product Quality Control Forensic Engineering Analysis of Hazards Associated with Operating an ATV by a Paraplegic Forensic Engineering Analysis of an ATV Accident Involving Two Riders on a Type 1 ATV Designed for One Driver and No Passengers More information available upon request. |
Additional Experience
Expert Witness Experience |
---|
Traffic Accident Reconstruction: North Carolina State University: Machine Design, Dynamics and Mechanics of Machines and Vehicles, Motor Vehicle Traffic Accident Reconstruction Sciences. BSME University of North Carolina: Introduction To Forensic Engineering. Certificate Northwestern University Research in Traffic Accident Reconstruction Institute For Police Technology and Management Research in Traffic Accident Reconstruction Collision Safety Institute: Automotive Crash Research Testing & Training. Certification Collision Safety Institute: Bosch Diagnostics Crash Data Retrieval System Download and Analyses Training and Certification i Witness Close Range Photogrammetry. Certificate Insurance Institute for Highway Safety and Highway Loss Data Institute: Vehicle Crashing Test Comparisons and Ratings. Seminar Chief Automotive Technologies: Vehicle Construction Technology and Trends. Seminar SAE Tractor-Trailer Event data Recorder Symposium ARC-CSI Vehicle Crash Conference Crash Data Retrieval Systems Summit Houston Texas. Certificate. Vehicle were crash tested at these summits. Aras 360 HD/Reality 4 day Crash Simulation training Course. Certificate Engineering Dynamics Corporation: Advanced Vehicle Dynamics and Crash Simulation 5 Day Course. Certification ARC-CSI Boot Camp and Crash Conference; Crash Testing of Motor Vehicles. Certificate ACTAR Examination Preparation Course Northwestern University – Traffic Crash Investigation/At-Scene Investigation/Evidence Mapping Northwestern University – Commercial Truck Crash Reconstruction Northwestern University – Pedestrian Vehicle Crash Reconstruction Truck Pro: Commercial Tractor Trailer Truck Air Brake Seminar Northwestern University – Commercial Truck ECM Data Imaging and Analyses DIVISION I: Motor Vehicle Crash Reconstruction Traffic Crash Reconstruction involving cars, light trucks, school buses, bicycles, heavy commercial trucks, motorcycles, bicycles and pedestrians. At-Scene Investigation and Evidence Mapping. Slow and High Velocity Collisions, Drag Factor, Skid Analyses, PDOF, ΔV, Closing Velocity, Conservation Linear and Angular Momentum, Conservation of Mechanical Energy, Crush Damage Analyses, Crush Energy, Critical Velocity and Circular Motion, Dynamic Weight. Car/Light Truck Event Data Recorder (EDR) Report Imaging, Analysis and Interpretation. Heavy Commercial Tractor Trailer Truck Crash Investigation. 49 CFR 40, 303, 325, 350-399 Federal Motor Carrier Safety Regulations. Commercial Tractor-Trailer Truck Electronic Control Module (ECM) Operational Data Imaging and Analysis. School Bus Accidents. Motorcycle Crash Reconstruction. Shift, Falls, Flips Vaults, Rollovers. Lamp Filament Analyses. Airbag Operation and Failure Analyses. Seat Belt Operation and Failure Analyses. All Terrain Vehicles (ATVs) and Recreational Off-Highway Vehicle (ROV) Crash Reconstruction. Recreational Off-Highway Vehicles (ROVs) Crash Reconstruction. Motor Vehicle Product Defect and Failure Analyses. Motor Vehicle Inspections. Vehicle Standards of Care. Product Defect and Failure Analyses. Vehicle Crash Testing. Vehicle Braking and Skid Testing. Vehicle Suspension and Handling Testing More Expert Witness Experience in Other Relevant Experience section. |
Training / Seminars |
---|
PUBLIC SPEAKING EXPERIENCE Dale Carnegie Course Public Speaking. College Public Speaking Classes. Industrial Classroom Teaching. Court Trial Testimony. National Engineer’s Week – Various Local Middle Schools. National Society of Professional Engineers Presentations. Society of Manufacturing Engineers Presentations. National Academy of Forensic Engineers Presentations. PRESENTATIONS/TEACHING Mathematics Teacher: Taught basic math to potential hourly employees for the purposes of screening for future employment. Created math text and testing materials for classroom use. Society of Manufacturing Engineers – Subject Forensic Engineering Professional Engineers of North Carolina – Subject Forensic Engineering Raleigh-Wake County Paralegal Association – Subject Forensic Engineering Guilford County Paralegal Association – Subject Forensic Engineering Casualty Insurance Adjusters Various Chapters – Subject Forensic Engineering North Carolina Paralegal Association – Subject Forensic Engineering Local Middle Schools – National Engineer’s Week – Subject Engineering Profession North Carolina State University ASME Student Section. Subject Forensic Engineering Piedmont Community College – Subject Forensic Engineering National Engineer’s Week – Subject Careers in Engineering and What Engineers Do Professional Engineers of North Carolina – Subject NASA’s Saturn V Moon Rocket IADA Conference – Vehicle Crash Data Retrieval and Traffic Accident Reconstruction National Academy of Forensic Engineers – ATV Accidents Professional Engineers of North Carolina – Motor Vehicle Crash Reconstruction |
Other Relevant Experience |
---|
Expert Witness Experience Cont. DIVISION II: Industrial Accident Investigation/Reconstruction: Industrial Accidents/OSHA Safety/Machine Guarding/Hazard Investigations/ Product Defect and Failure Analysis Investigations: »Workman’s Compensation Cases. »Machine Guarding Accidents. »Poultry Process Equipment Accidents. »Fabric Rollup Machines Accidents. »Conveyors Accidents. »Construction Equipment Accidents: Scaffold Failures, Scissor Lift Failures, Ladder Failures, Folding Benches, Belt Sanders, Saws. »Automatic Storage and Retrieval Systems (AS/RS)(AGV) Forklift Accidents. »Scissor Lift Accidents. »Forklift Accidents. »Pallet Jack Accidents. »Ladder Accidents. »Loading Dock Accidents - Dock Lift, Dock Leveler and Dock Plate Accidents. »Power Plant Accidents. »Power Tool Accidents: Belt Sanders, Radial Miter Saws. »Exercise Strength Training Equipment Accidents. »Lawn Mower Accidents. »Lawn Aerator Accidents. »Escalators Accidents. »Crane Accidents. »High Voltage Power Line Tower Structures Failure Accidents. »Product Safety Signs, Symbols, Warnings and Labeling. »Product Safety Information in Product Manuals, Instructions and Other Collateral Materials. »Wood Working Machine Accidents. »Abrasive Shotblaster Accidents. »Motor Vehicle Coil Spring Compressors Accidents. DIVISION III: Amusement Ride Accidents/ASTM F24 Standards/Standards of Maintenance/Standards of Care and Operation/Product Defect and Failure Analysis. Go-Kart crashes with kart inspection. Samba Balloon Ride Gondola support failure with the inspection of the entire machine structure. The main superstructure was cracked in multiple locations. Engineer advised the client to take the ride out of operation and either repair the superstructure or destroy it. X-Factory Ride; Inspection of the machine’s patron restraint system design. |