Expert Details
Glass Technology and Manufacturing
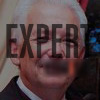
ID: 108272
California, USA
GLASS TECHNOLOGY; GLASS BATCH FORMULATION; GLASS DEFECT IDENTIFICATION. Expert has established and specified raw material quality standards and vendor partnerships. He has defined batch formulations for desired glass properties, color development, and optimized melting properties. He has worked to define quality specifications and processing requirements for glass recycling and has evaluated alternate raw material substitutions. He is also familiar with glass testing requirements, defect identification, and fracture analysis procedures.
Consulting areas:
- Batch Formulation Calculations
- color changes, color development & control
- glass defect identification and elimination
GLASS MELTING FURNACES. A significant portion of Expert's career has been involved with all phases of continuous glass melting furnaces. He has designed, purchased, constructed, operated, and audited all-electric and gas, electric boosted, and oil fired regenerative furnaces. These efforts have included budget development, specifying refractories, choosing combustion equipment, contractor selection, choosing instrumentation. He has also determined operating procedures for optimizing energy efficiency, satisfying glass quality requirements, and optimizing furnace life. Expert is very knowledgeable about issues involving 100% oxygen fired melting conversions. He also conducts customized training programs for operators and technicians.
GLASS MELTING FURNACE AIR EMISSIONS. Expert has had significant involvement with air emission generation and control issues for glass melting furnaces. This has included efforts to minimize particulate, SOX, and NOX by process modifications and evaluating alternative add-on control equipment. He has played an active role in the process for California (CARB & SCAQMD) and Federal (EPA) Rule Development for glass furnaces.
Consulting areas:
- Project concept and scope definition, budget development and control
- Refractory Applications, Design Review, and Purchasing considerations
- Contractor Selection, Compliance Control, Schedule Development, Cost Control, Owner Representation
GLASS MELTING OPERATIONS. Expert has performed audits and troubleshooting of furnace and forehearth areas. He has worked with energy conservation and cost reduction programs. Additionally, he has conducted refractory inspections for life expectations and replacement considerations.
Consulting areas:
- Audits, Training and "Trouble Shooting" of Furnace and Forehearth areas
- Energy Conservation and Cost Reduction programs
- Refractory Inspections for life expectations and replacement considerations
- Optimization of operating parameters
- Training to develop improved Employee performance
RAW MATERIALS
Consulting areas:
- specification and quality monitoring systems
- vendor assessments
- material substitutions
ENVIRONMENTAL CONCERNS
- Operation optimization for Particulate, SOx, NOx
- Compliance assessment and review
GENERAL CONSIDERATIONS
- Industry Orientation Presentations and Introductions
- Meeting / Workshop Development, Representation, Reports
- Technology Assessment / Feasibility Studies / Executive
- Summary Reports / Topical Seminar Presentations
Education
Year | Degree | Subject | Institution |
---|---|---|---|
Year: 1965 | Degree: B.S. | Subject: Ceramic Engineering | Institution: University of Illinois |
Work History
Years | Employer | Title | Department |
---|---|---|---|
Years: 1992 to Present | Employer: Undisclosed | Title: Glass Industry Consultant | Department: |
Responsibilities:Independent Consultant since 1992; background and abilities to assist organizations in a number of important areas. From a phone consultation or document review, to an office or site visit. |
|||
Years | Employer | Title | Department |
Years: 1977 to 1992 | Employer: Kerr Glass Mfg. Corp | Title: Divisional VP | Department: Batch and Furnace Engineering |
Responsibilities:Manager of corporate technical staff, responsible for supporting glass container manufacturing plants. Implement technology improvements into production operations for increasing productivity, cost reductions, and energy efficiency.- Glass Technology: Raw Material Specifications and technical communications with suppliers, Batch Formulations, and Glass Quality target definitions for maximizing production and improving costs. - Furnace Design: Refractory selection for optimizing service requirements, design parameters for operating performance, Instrumentation and Combustion system selection. - Furnace Rebuilds: Direct responsibility for all refractory material purchasing, contractor selection, field construction supervision, design evaluation, project coordination and cost control. - Furnace Operations: Monitoring of daily plant operating data. Support plant personnel with establishment of operating procedures, training seminars, routine audits. Assist with plant programs for cost reductions, quality improvements, and tighter process control. Coordinate environmental compliance requirements for air emissions. - Budget Development: cost justification, and project management (typical project size $3-5 million+) - Corporate Reporting: of furnace performance, glass production, costs and energy consumption analyses - Environmental Issues: compliance responsibility for furnace air emissions (NOX, SOX & Particulate) and hazardous waste disposal of refractory flue debris |
|||
Years | Employer | Title | Department |
Years: 1972 to 1977 | Employer: Federal Glass | Title: Department Mgr. - Glass Development and Furances | Department: |
Responsibilities:Responsible for all glass production of soda-lime and borosilicate tableware operations. Department consisted of two engineers, three supervisors, and 33 hourly employees. Activities included developing new glass colors into production, melting furnace fuel conversions, energy conservation, and cost reductions in raw material substitution programs. |
|||
Years | Employer | Title | Department |
Years: 1968 to 1972 | Employer: Glass Containers Corp. | Title: Area Furnace Engineer | Department: |
Responsibilities:Corporate Staff support of nine production plants for operational training and "trouble shooting." Responsibility to Engineering for projection of furnace rebuild forecasts and inspection of construction for compliance with design specifications. |
|||
Years | Employer | Title | Department |
Years: 1965 to 1968 | Employer: Anchor Hocking Glass Co. | Title: Department Head of Batch and Furnace | Department: |
Responsibilities:Joined immediately after college graduation and entered extensive training program for placement into their manufacturing division. Responsible for start-up of new batching facility in Fla. Two years as Department Head of Batch & Furnace in Calif. |
Career Accomplishments
Associations / Societies |
---|
Phoenix Award Committee; member Glass Problems Conference Advisory Board 1984-2009 (15 papers presented) |
Professional Appointments |
---|
Glass Packaging Institute (Industry Trade Assn.)- Glass Firing Task Group; Chairman Phoenix Award Committee; Chairman |
Awards / Recognition |
---|
American Ceramic Society; Fellow Society of Glass Technology; Fellow |
Publications and Patents Summary |
---|
Expert has authored, presented, and published a number of technical papers relating to glass production issues. Glass Problems Conference Advisory Board 1984-2009 (15 papers presented) American Ceramic Society (4 technical papers) |
Additional Experience
Expert Witness Experience |
---|
Expert has performed services as an expert witness in jury trial and both domestic and international arbitration. |
Training / Seminars |
---|
Expert teaches a variety of seminars at American Glass Research regarding glass melting operations. He also conducts on site training on a variety of production subjects at manufacturing sites. |
Vendor Selection |
---|
Expert has experience locating vendors of glass making raw materials, glass container manufacturing equipment, glass furnace refractories and combustion/ temperature process control. He has access to the following resources to aid in vendor location: personal experience and industry contacts. |
Marketing Experience |
---|
Expert does not get involved with Sales/Marketing issues, but can discuss a variety of manufacturing issues which contribute to manufacturing costs. |
Fields of Expertise
glass batch formulation, glass container, glass defect identification, glass engineering, glass furnace, glass furnace air emission process, glass furnace air emission product, glass manufacturing, glass technology, regenerative glass furnace, soda-lime glass, soda-lime glass manufacturing, combustion engineering, furnace refractory system, glass batch material, container industry, glass quality, glass fracturing, industrial glass, bottle glass, glass sand, technical management, furnace design, fracture analysis, glass cullet, molten glass, color formulation, furnace air emission product, emission control, container glass, glass property, nitrogen oxide emissions reduction, scrap glass, nitrogen oxide compound environmental effect, stationary source sulfur dioxide control, stationary source particulate control equipment, stationary-source particulate control, stationary source nitrogen oxide control, energy-efficient clay processing, energy-efficient glass processing, very high-temperature furnace, sulfur oxide compound environmental effect, particulate pollution process, air pollution process, energy-efficient stone processing, energy-efficient temperature control, glass chemistry, process modification, sulfur oxide compound, oxygen, temperature control, particulate material, natural gas, glass ceramic, gas furnace, combustion furnace, combustion control, ceramic property