Expert Details
Silicone Molding Process Development, Silicone tooling, Silicone Sheeting, Silicone Extrusion, Silicone Dipping, and Silicone Molding Troubleshooting
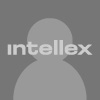
ID: 735085
California, USA
Since 1985, Expert has been using various types of high-consistency (HCR) silicone materials, two-part cure material, one-part cure material, RTV, as well as using an extensive variety of compression molding machines to develop compression molding processes. He successfully implemented these processes to manufacturing with zero failure. All development were based on the “Scientific Molding Process Development” principle.
Since 1985, Expert has been using various types of liquid and high-consistency silicone materials, two-part cure material, one-part cure material, RTV, dispersion, and coatings for Dacron, Felt, and Reemay to develop coating processes. He successfully implemented these processes to manufacturing with zero failure. All development were based on the “Scientific Molding Process Development” principle.
Since 2000, based on his extensive silicone molding knowledge, Expert has been providing silicone mold tool design and conceptual ideas, and has successfully completed several mold design projects. He has also qualified various mold tooling based on client, FDA, and CFR 21 requirements.
Using his decades of experience with medical device manufacturing and silicone extrusion, Expert has successfully investigated and performed systematic root-cause analysis using the DIMAC process, and fishbone principle with 6M elements. He has resolved issues ranging from typical injection molding problems to multi-component molding processes.
Expert has been using the scientific molding process and lean manufacturing principles (one-piece flow) to reduce overall costs from development to product launch, thereby reducing the costs of the finished goods to clients. This provides for an increased margin for sales, or reduced prices to end-users.
Expert has served as a consultant to:
Edwards Lifesciences, Allergan Medical, Halyard Healthcare(Avanos Medical, Inc), Fisher and Paykel Healthcare, Zimmer Biomet, and other firms.
Education
Year | Degree | Subject | Institution |
---|---|---|---|
Year: 1983 | Degree: B.S | Subject: Electronic Engineering | Institution: An Yang University |
Work History
Years | Employer | Title | Department |
---|---|---|---|
Years: 2012 to Present | Employer: Undisclosed | Title: Senior Manufacturing Engineer, Project Engineer | Department: Molding |
Responsibilities:From 2012 to present, Expert has been responsible for the following:1. Training entry-level engineer 2. Training manufacturing associate. 3. Equipment qualification 4. Process Qualification 5. Support quoting Engineer. 6. Provide concept design for molding and extrusion 7. Purchase molding equipment 8. Oversee daily molding manufacturing status 9. Support maintenance department to solve equipment troubleshooting and malfunctioning. 10. Molding tool qualification 11. Establish and qualify new supplier as requires. 12. Create and document manufacturing procedures |
|||
Years | Employer | Title | Department |
Years: 2008 to 2012 | Employer: Medtronic Neurosurgery | Title: Principal Engineer | Department: Silicone Molding, Extrusion, and Super-Critical Extrusion |
Responsibilities:As Principal Engineer, Expert was responsible for:1. Training entry-level engineer 2. Training manufacturing associate. 3. Equipment qualification 4. Process Qualification 5. Support quoting Engineer. 6. Provide concept design for molding and extrusion 7. Purchase molding equipment 8. Oversee daily molding, calendaring (silicone sheeting), dipping, and extrusion manufacturing area 9. Support maintenance department to solve equipment troubleshooting and malfunctioning. 10. Molding and extrusion tool qualification 11. Establish and qualify new supplier as requires. 12. Provide support to other Medtronic business units. 13. Create and document manufacturing procedures |
|||
Years | Employer | Title | Department |
Years: 1985 to 2008 | Employer: Speclialty Silicone Fabricators, inc. | Title: Manufacturing Engineer | Department: Molding and Assembly |
Responsibilities:As Manufacturing Engineer, Expert was tasked with:1. Equipment qualification 2. Process Qualification 3. Support quoting Engineer. 4. Provide concept design for molding and extrusion 5. Purchase molding equipment 6. Oversee daily molding manufacturing status 7. Support maintenance department to solve equipment troubleshooting and malfunctioning. 8. Molding tool qualification 9. Establish and qualify new supplier as requires. 10. Create and document manufacturing procedures |
International Experience
Years | Country / Region | Summary |
---|---|---|
Years: 1995 to 1995 | Country / Region: South Korea | Summary: Provided extensive tooling knowledge to initiate new projects |
Years: 1996 to 1999 | Country / Region: South Korea | Summary: Provided extensive Silicone (raw material) knowledge to cosmetic surgeon to initiate new projects (Chinese Market) |
Career Accomplishments
Awards / Recognition |
---|
MD&M Minneapolis Conference Team invited as a speaker |
Publications and Patents Summary |
---|
Expert holds a patent for his Compressible Foam Wound Dressing. This gel is applied to a skin-facing surface of the foam sheet to foam skin-contacting layer. The resultant wound dressing maybe stretched and placed upon a person’s skin to overlie a wound and provide a fluid impermeable barrier between the wound and the external environment. |
Additional Experience
Training / Seminars |
---|
2001: Engel Training Class: Controller and Processing 2002: Engel Training Class: Completed Processing and Mold Set up 2004: Engel Training Class: Completed Elast/LIM Machine 2005: Engel Training Class: Processing and Set-up 2006: Community college: Completed AutoCad Class 2007: Toshiba Electric injection press processing 2008: Attended Nusil Technology Silicone Institute Workshop and completed courses 2011: Kepner Tregoe Problem Solving Decision Making 2012: Community college: Completed Solidworks Class 2013: Arburg Allaround Machine Set-up, Controller, and Processing 2015: Community college: Completed Solidworks Class 2016: Completed Arburg Plastic Technology Course 2017: Community college: Completed PLC (Programmable Logic Control) Class |
Vendor Selection |
---|
Based on client and project requirements, Expert has successfully solicited for and selected vendors for raw materials, equipment, auxiliary equipment, tooling and machining services, and automation software. Equipment: Arburg Machine, Engel Machinery, Battenfeld, Boys Machine, Tung Yu Machinery, Wabash machine, Hull Machine, Graco (Fluid Automation) Inc, 2KM Metering, mixing and dispensing. Mold: Kipe Mold, Rhombke Mold, DMT Mold, Kingson Mold, Roembke MFG & Design Raw Material: Nusil, Dow Chemical, Shin-Etsu Silicone, GE silicone, Blue Star silicone, Wacker Silicone. Poly-Ond |
Marketing Experience |
---|
Created and provided complicate Solidworks drawings and 3D models per customer requirements. |
Language Skills
Language | Proficiency |
---|---|
Korean | Native language |
Fields of Expertise
thermoset injection molding, compression mold, vacuum molding, scientific molding, molding press, molding device, molding, low-pressure molding, liquid injection molding, transfer molding, double-shot molding, injection molding machine, dip molding, hot runner molding, compression molding, co-injection molding, injection molding, injection compression molding, dip coating, plastic tooling, tooling, machining tooling, extrusion troubleshooting, medical device manufacturing troubleshooting, cost reduction, training procedure, employee training, technical education, skill training