Expert Details
Materials Engineering for New Designs, Cost Reduction, and Yield Improvement
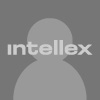
ID: 722821
Illinois, USA
1) Working with mechanical and electrical engineers to help make decisions about the materials and processed used to manufacture a product. The decisions include consideration of cost, manufacturability, materials and components lot-to- lot variations, reliability, materials availability, and environmental restrictions.
2) Working with manufacturing and quality engineers on understanding the impact of materials, processes, and supplier quality on manufacturing yields.
3) Materials selection, characterization, and implementation for cost reduction and quality improvement.
4) Working with suppliers to help them understand the effects of their processes on the materials characteristics and quality of the final product.
5) Developing tests to evaluate the reliability of materials used to make a product.
Expert has provided support to help designers understand in-house and supplier manufacturing and assembly capabilities. Examples include deciding which components could be masked off for a powdercoat process, the realistic plating tolerances for an electronic leadframe, and grain size tolerances for a steel making process.
Expert is experienced working with in-house manufacturing and suppliers to identify the key materials characteristics to monitor in order to evaluate component and assembly quality. He is also familiar with many of the analytical techniques used to evaluate materials characteristics. Some of the materials evaluations with which he is experienced are: grain size, composition, hardness, tensile behavior, layer thickness, viscosity, rheometry, microstructure, adhesion, and surface contamination. Some of the analytical techniques that he is familiar with include: optical microscopy, scanning electron microscopy (SEM), energy dispersive x-ray spectroscopy (EDS), x-ray fluorescence spectroscopy (XRF), atomic absorption (AA), atomic emission spectroscopy, differential scanning calorimetry (DSC), thermogravimetric analysis (TGA), thermomechanical analysis (TMA), Fourier infrared spectroscopy (FTIR), and various high vacuum surface science techniques.
Expert has worked as a process engineer and is familiar with statistical process control. As a design engineer he has experience writing specifications for materials and components.
Expert has been involved in various cost reduction efforts involving materials or supplier changes. These include: aluminum component supplier change for $50,000 annual savings; elimination of Sn plating from a contact for $150,000 annual savings; switching solder paste suppliers for $500,000 annual savings; and changing sheet steel suppliers for $1,000,000 annual savings. All these changes involved understanding the characteristics, quality, and reliability of the new materials.
Expert is working on a project to determine the feasibility of eliminating tin plating from the surface of a stainless steel part.He worked on a project to determine the root cause of a steel cosmetic defect, add the information to the supplier material requirements, and help qualify a new supplier. Expert worked on a project to characterize the effects of various metal fnishes on the adhesion of a sealant material to the surface.He helped with a competitive analysis to understand the relationship between the components' performance, materials properties, and cost. Expert worked on a project to understand the material and testing requirements to ensure final parts with good fatigue performance.
Education
Year | Degree | Subject | Institution |
---|---|---|---|
Year: 1991 | Degree: Ph.D. | Subject: Materials Science and Engineering | Institution: Northwestern University |
Year: 1987 | Degree: M.S. | Subject: Metallurgical Engineering | Institution: University of Illinois - Urbana |
Year: 1985 | Degree: B.S. | Subject: Metallurgical Engineering | Institution: University of Illinois - Urbana |
Work History
Years | Employer | Title | Department |
---|---|---|---|
Years: 2004 to Present | Employer: Undisclosed | Title: President | Department: |
Responsibilities:Available upon request. |
|||
Years | Employer | Title | Department |
Years: 1999 to 2004 | Employer: Motorola | Title: Principal Staff Engineer | Department: Automotive Electronics |
Responsibilities:Expert was responsible for materials selection, evaluation and implementation for: 1) new designs, 2) cost reduction, 3) quality improvement, and 4) manufacturing yield improvement. |
|||
Years | Employer | Title | Department |
Years: 1997 to 1999 | Employer: Motorola | Title: Principal Staff Engineer | Department: R&D |
Responsibilities:He was involved in the development of new processes for electronics manufacturing. |
|||
Years | Employer | Title | Department |
Years: 1991 to 1997 | Employer: Motorola | Title: Process Engineer | Department: Semiconductor Products Sector |
Responsibilities:Expert was a process engineer in an integrated circuit factory. He was responsible for cost reduction, yield improvement, cycle time reduction, development and implementation of new processes. |
Career Accomplishments
Associations / Societies |
---|
Expert is a member of ASM, IEEE, SMTA, and IMAPS. |
Licenses / Certifications |
---|
He is a Registered P.E. in Illinois. |
Professional Appointments |
---|
Expert was program chair for his local ASM chapter, and served on the Technical Book Committee for ASM International. |
Publications and Patents Summary |
---|
He has five publications, and is working on a sixth. He has two patents. |
Fields of Expertise
design engineering, design for cost, electrical product design, electrical product development, electronic product development, engineering design, electronics design engineering, high volume, low cost product design, material design, design-for-quality, material product development, new product development, product design, design for manufacturability, quality evaluation, quality standard, cost engineering, supplier quality engineering, automotive design, electronics nondestructive testing, design review, scale-up, design for assembly, design for environment, design for manufacture and assembly, process engineering, quality engineering, quality control