Expert Details
Food Packaging, Retail Products Packaging, Foodservice Packaging, Packaging Materials and Processes
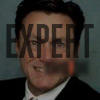
ID: 723751
California, USA
Expert has successfully developed a wide range of packaging in his 20+ years as a packaging engineer. In doing so, he has often worked in cross-functional teams that included marketing, engineering, procurement and operations. He has the ability to read and adapt to situations so is effective at moving his projects forward to completion in different environments and cultures. Most of his 20+ years was spent in the food industry working for companies such as ConAgra Grocery Products and Yum! Brands. He has been offering his services as a consultant for the past 9+ years. During that time he has completed projects for General Mills Yoplait, H.J. Heinz, 7-Eleven, Black & Decker/Kwikset, Pharmanex, and POM Wonderful to mention just a few of his clients. While at ConAgra he developed a new plastic material blend that allowed the production of clear cups on an aseptic thermoform/fill/seal machine for the first time. This breakthrough resulted in a major marketing advantage versus competitors. He worked on the commercialization of yogurt stick pack pouches during their inception for Yoplait. This product was the first of its kind and spawned various new products to be put on the markeet in similar packaging. Expert has many more examples of successful packaging he has developed. He has gathered much knowledge in this area over the years and also has a passion for what he does.
Expert has developed successful packaging from many different material types, in many different package forms. He has worked with glass, metal, rigid plastic, flexible plastic films, paper, paperboard and corrugated board. Most of his project work has required the developement of packaging systems that incorporate these various materials. He typically will develop not only the primary package, but the secondary and tertiary packaging as well. He has build a solid base of knowledge while working with these materials over the years. While this is the case, he has focused most of his efforts on plastic materials. These materials are both complex and versatile, and are growing in use. He has recently completed graduate level course work in polymer science to keep up on the advances in this area.
Array
Challenge:
Complete development of new yogurt package, integrated with new FFS equipment and support start-up on an accelerated production ramp-up schedule.
Work Performed:
Finished the development and implemented unique "stick pack" packaging for a new yogurt product called "Go-Gurt”. Was a member of a team that worked in partnership with the equipment supplier to design, build and troubleshoot new concept form/fill/seal machines to efficiently package the product. Gathered equipment performance and package quality data. Analyzed data and made recommendations for improvements that were incorporated into packaging and equipment.
Results:
Successful product launch. Production equipment was able to meet very aggressive ramp-up schedule. High quality product was shipped on time with no shortages or deletions occurring.
Challenge:
A QSR's packaging department did not have adequate resources to complete demanding marketing calendar projects and various cost savings projects.
Work Performed:
Developed and implemented numerous food packages that included: box and carryout bag, wraps, rigid food containers, promotional packaging, plastic "cruiser" drink cups, pouch material cost reduction and conversion from #10 can to pouch.
Results:
One of these package types, a family of rigid food containers, provided a cost savings of $2,000,000 while at the same time greatly increased package function, aesthetics and consumer appeal.
Challenge:
A health and personal care company lacked resources to develop packaging for an upcoming launch of a new line of products.
Work Performed:
Developed packaging for a new line of personal care products that included shampoo, conditioner, styling gel, styling foam and body wash. This included the retail packaging and sampler packaging for each product.
Results:
Successful on-time product launch. Packaging could be run at high efficiencies by co-packer. New product line was well received by distributors.
Challenge:
A large consumer products company needed packaging developed, sourced and implemented for a complete new line of upscale residential door fixtures. The packaging needed to communicate the image of high quality while still being cost effective and acceptable for store handling at Home Depot.
Work Performed:
Developed packaging for 14 different products. Primary, secondary and tertiary packaging was designed for each. Designs were verified through drop and vibration testing.
Results:
The new packaging was used in the on-time launch of the new product line. The products were well received by Home Depot.
Challenge:
A nutritional supplement company had quality problems with their highest volume product. Pills of the supplement, sourced in Asia, were degrading during shipment.
Work Performed:
Performed an analysis of the supplement’s distribution environment. Researched various pouch film barrier materials, film structures, their costs, and potential suppliers.
Results:
Recommended new pouch film specification for the product and potential sources. Tests with the new film proved the elimination of supplement degradation. The company shifted all of these supplements to this type of film.
Education
Year | Degree | Subject | Institution |
---|---|---|---|
Year: 1979 | Degree: BS Packaging | Subject: Packaging Engineering | Institution: Michigan State University |
Year: 1986 | Degree: MBA | Subject: Business | Institution: Southern Illinois University |
Work History
Years | Employer | Title | Department |
---|---|---|---|
Years: 1997 to Present | Employer: Undisclosed | Title: Consultant | Department: |
Responsibilities:He is the principal of Employer. He performs packaging development work such as concept creation, package structural design, cost analysis, equipment requirements, sourcing, commercialization and troubleshooting. |
|||
Years | Employer | Title | Department |
Years: 1996 to 1997 | Employer: YUM! Brands - Taco Bell | Title: National Manager, Packaging | Department: |
Responsibilities:He was responsible for all packaging used in-store nationally. Either leading or a member of multi-department teams, he developed packaging for new products and promotions. He reduced systemwide packaging costs by $4MM by identifying and implementing a new packaging platform. |
|||
Years | Employer | Title | Department |
Years: 1986 to 1996 | Employer: ConAgra Grocery Products | Title: Project Leader | Department: Packaging R&D |
Responsibilities:Held positions of increasing responsibility in the areas of packaging equipment engineering and later Packaging R&D. He conceived and implemented many packaging innovations for low-acid aseptic food products. An example of one of these was a clear form of plastic cup thermoforming stock that could be run at high efficiencies on the company's numerous thermform/fill/seal machines. Prior to this all cup stock was opaque. The clear material became the industry standard for this type of machine. He also developed packaging for frozen food products, pouched sauces, dry mixes, the club store channel and special promotions. |
|||
Years | Employer | Title | Department |
Years: 1985 to 1986 | Employer: Chervon Chemical | Title: Plant Engineer | Department: Engineering |
Responsibilities:He was the plant packaging engineer at an agricultural chemical division plant in Missouri. He improved the performance of multiple packaging lines by de-bottlenecking, streamlining material flow and addressing line operator's ergonomic issues. |
|||
Years | Employer | Title | Department |
Years: 1980 to 1985 | Employer: Norcliff Thayer, now Glaxo SmithKline | Title: Assistant Manager of Pkg. Ops. | Department: Packaging Operations |
Responsibilities:He was responsible for the day-to-day management of 30-60 packaging department employees. The packaging department ran 14 different packaging lines that filled liquids, lotions, tablets and powders into packages that included various plastic bottles, foil/film wraps, vials and cartons. |
Career Accomplishments
Associations / Societies |
---|
A longstanding member of the Institute of Packaging Professionals (IoPP) and its Consultants Council group. Served as Chair, Vice-Chair and Secretary of the Consultants Council over a period of six years. |
Licenses / Certifications |
---|
He is a Certified Packaging Professional (CPP) having met all the professional and academic requirements set by the IoPP Certification Board. |
Additional Experience
Training / Seminars |
---|
Gave in-house training seminars on the fundamentals of packaging for department personnel. These were given while an employee of ConAgra and also later while consulting. |
Vendor Selection |
---|
Have extensive knowledge of the packaging supply chain for plastic resins, glass and plastic bottles, closures, labels, foodservice packaging, paperboard folding cartons and corrugated. He has sourced all of these items at some point during his consulting project work. |
Marketing Experience |
---|
He has worked with many marketing groups in the developement of new packaging. While he is not a marketing professional he has an true understanding of marketing principles and customer requirements. He knows how to develop packaging that harmoniously blends the needs of the consumer with the effeciencies and function of the manufacturing operation. |
Fields of Expertise
package cost reduction, packaging evaluation, packaging development, packaging material, packaging material selection, retail product packaging, food service packaging, aesthetics, packaging innovation, harvest machinery, metal packaging process, viscous material packaging, package design, over-the-counter drug packaging, gas flush packaging, foil laminate, bulk packaging material, barrier film technology, gas transmission, preservative effect, food marketing, food packaging material, packaging automation, powder filling, barrier polymer, bag-in-box packaging process, food shelf life extension, glass packaging material, package regulation, moisture-resistant packaging, foodboard, permeable packaging material, packaged product, food wrap, corrugated packaging material, packaging specification, package handling, acetate film, packaging material system, recyclable packaging material, dairy product packaging material, dairy product packaging process, package integrity, food package, Food and Drug Administration CFR-21 part 175, flexible packaging laminate, food packaging equipment, American Society for Testing and Materials packaging standard, biodegradable packing material, protective packaging material, packaging migration, Food and Drug Administration drug packaging regulation, package-food product interaction, packaging technology review, packaging machine, packaging system, tamper-evident package, extended shelf-life packaging material, active packaging material, rigid packaging material, flexible packaging material, microwave food packaging process, plastic food package, packaging design review, packaging testing, packaging technology, packaging document, moisture-barrier packaging process, modified atmosphere packaging, paper-product wrapping, environmentally friendly packaging material, biodegradation, foil packaging material, foil package, packaging equipment, plastic packaging material, moisture barrier material, packaging film, case sealing, aseptic filling, food packaging plastic, wrapping material, biodegradable material, solid packaging process, beverage packaging process, bagging material, package, unitizing, repackaging, palletizing, packing material, packaging paper, packaging engineering, packaging process, package testing, liquid packaging process, greaseproof paper, freight handling, food packaging process, cushioning material, controlled-atmosphere packaging process, package closure, boxboard, bag, aseptic packaging process