Expert Details
Flexible Packaging Processes: Rotogravure Printing, Extrusion Coating/Lamianting, Dry Bond
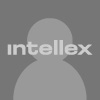
ID: 726164
North Carolina, USA
He has developed flexible packaing laminations for food and pharmaceutical applications. Designed laminations considered lowest cost for the required application, barrier properties requirements, and sealant needs and requirements. Laminates have been developed for lidding, dry food, wet food, retortable food, pharmaceutical packaging, child-resistant pharmacetical packaging, and puncture resistant pharmaceutical packaging applications.
He has also developed sterilizeable packaging for various medical and medical device applications
He has experience with all flexible packaging materials to include PET, MPET, OPP, MOPP, LLDPE, nylon, oriented nylon, coextruded films, and cavitated films. He has experience with a multitude of thermoplastic resins including EVA, EAA, Surlyn, Nylon 6, EVOH, LDPE, LLDPE, HDPE, MDPE, PET
He has experience with utilizing CC and DC foils in various pharmaceutical, food, and industrial packaging applications. Foil thickness contemplated and utilized ranged from 0.0003" up to 0.0025" in both CC and DC varieties. Additional strong understanding of aluminum foil alloys and uses.
He has developed foil laminations for food and pharmaceutical pouch operations, pharmaceutical blister operations, as well as foil-based puncture resistant and sterilizeable pouchs for the medical device and diagnostic industries.
He has experience installing and running rotogravure presses up to 10-colors. He has experience with register systems, gravure ink systems, and common issues/solutions associated with gravure printing.
He has a strong understanding of gravure ink systems and typical print layouts required to make gravure printing issue free.
He has experience developing packaging for EtO and gamma sterilized medical devices. Strong understanding of materials for required applications which create best value packages.
He has developed packaging utilizing aluminum foil, SiOx and AlOx coated PET's, as well as other barrier packaging materials. Strong understanding of material component needs by barrier requirement.
He has developed multi-layer packaging laminates and coextruded laminates. Strong understanding of best value approach to packaging, with an emphasis on packaging to meet the requirement, as opposed to over packaging. Strong understanding of developing sustainable packaging alternatives through use of source reduction and newly developed organic films and resins.
He has developed OTC packaging for both child-resistant and non-child resistant applications.
He is strongly familiar with package cost reduction methods including substitution of lower cost materials, supply-chain enhancements, and creating synergies within the entire packaging value chain.
He has created packaging specifications, business presentations, and technical presentations which document packaging uses and benefits.
He is a degreed Chemical Engineer from a top-10 engineering college with a 25 year career emphasis on packaging and polymer science.
He has a strong understanding of papers utilized in the packaging industry to include C1S, C2S and MG sheets.
He is stongly familiar with rotogravure printing to include line and process printing on paper, PET, OPP and other packaging substrates.
He is strongly familiar with all packaging processes including rotogravure printing, flexo printing, dry bond laminating, wet bond laminating, solventless laminating, extrusion coating and laminating, blown film, cast film, blown coextrusion, cast coextrusion, plastic film orientation.
He has significant experience printing and laminating standard oriented PET films. Printing experience includes line and process printing methodologies.
Education
Year | Degree | Subject | Institution |
---|---|---|---|
Year: 1979 | Degree: BS | Subject: Chemical Engineering | Institution: University of Illinois, Urbana, IL |
Work History
Years | Employer | Title | Department |
---|---|---|---|
Years: 1983 to 2005 | Employer: RJR Packaging | Title: Production Manager | Department: |
Responsibilities:He is responsible for flexible packaging production processes including extrusion laminating/coating; rotogravure printing, dry and wet bond lamination, slitting, finishing, and packing |
|||
Years | Employer | Title | Department |
Years: to Present | Employer: Undisclosed | Title: Research Engineer / Process Engineer | Department: |
Responsibilities:Hi is responsible for blown and cast film product and process development |
Career Accomplishments
Awards / Recognition |
---|
Chairman's Award |
Publications and Patents Summary |
---|
Has has (3) patents and (1) patent application |
Additional Experience
Vendor Selection |
---|
Sourced rotogravure printing equipment. Sourced extrusion coating/laminating equipment. Developed and sourced vendors for extrusion resins. Developed and sourced vendors for laminating films. Developed and sourced vendors for laminating coatings and adhesives. |
Marketing Experience |
---|
Well aquainted with customer attitudes and trends in pharmaceutical packaging |
Other Relevant Experience |
---|
Statistical process control Design of experiments |
Fields of Expertise
cold seal packaging process, foil package, packaging material, flexible packaging laminate, packaging film, packaging material selection, flexible packaging material, foil laminate, foil packaging material, gravure printing, gravure printing press, rotogravure printing, medical device packaging material, moisture-resistant packaging, moisture-barrier packaging process, multi-layered packaging material, plastic packaging material, over-the-counter drug packaging, package cost reduction, packaging document, packaging engineering, packaging paper, packaging printing, packaging process, polyester film, polyester thin film, active pharmaceutical ingredient, metal packaging process, package design, gas transmission, barrier polymer, packaging ink, package regulation, pharmaceutical coating material, permeable packaging material, gravure ink, packaged product, solventless adhesive, packaging specification, packaging material system, recyclable packaging material, ointment packaging, tablet packaging process, powder packaging process, roll packaging, package integrity, drug labeling requirement, packaging adhesive material, form/fill/seal packaging machine, packaging machine performance, packaging migration, pharmaceutical industry, Food and Drug Administration drug packaging regulation, web handling system, printing press control system, paperboard gravure printing, packaging technology review, packaging system, tamper-evident package, extended shelf-life packaging material, plastic food package, packaging design review, packaging testing, packaging evaluation, packaging development, packaging technology, packaging-material management, packaging machinery design, medical product packaging process, medical device packaging process, medical device packaging design, environmentally friendly packaging material, adhesive material, moisture barrier material, photosensitive material packaging material, gravure photoresist, packaging stress analysis, sterile packaging process, food retorting, package testing