Expert Details
Chemical Engineering, Trouble Shooting of Chemical Plants, Fats & Oils, Biodiesel, Biofuels
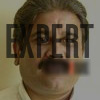
ID: 723348
Costa Rica
He has also conducted HAZOP studies of various installations and new add-on systems. He had active involvement in implementation of TPM and WCM, GMP, ISO 9002, ISO 14001 and ISO 18000 systems. The project management from scratch to reality: successful timely completion is one of his strengths.
Successfully installed commissioned 5MMGAL plant located in Costa Rica under the banner of Quimiocos Vesgtales SA. The Plant primary feed stock is Palm oil using inhouse catalyst preparation and methanol as reactant (2005).
Successfully designed, erected, commissioned and started 4.5MMGAL trans-esterification plant in AGROSA, LEON, NICARAGUA (2006).
Designed 10 MMGAL plant with palm oil feed stock in CIA NUMAR, Costa Rica (2007).
Designed 10 MMGAL plant with palm oil feed stock for Jaremar Biodiesel, Honduras (2007).
Designed 6.5MMGAL plant for multi-feed stock capable to handle any type of feed stock with any level free fatty acid for Carbon Neutral, Madison GA.
He is an expert in the Shutek process for biodiesel. Shutek Oleo has developed its unique process which meets all international quality standards parameters at optimal cost of operation. The Shutek process is very competitive cost wise.
The process consists the following steps which guarantee maximum yield and better quality: Feed preparation, Catalyst preparation, Trans-esterification ( Batch / Continuous), Separation of Glycerols, Continuous Counter current ester Washing, Vacuum drying, Filtration, Methanol recovery and rectification, Vent scrubbing, and Glycerin purification.
Advantages of Shutek process includes: Zero effluent & Zero emission of gases (environment friendly), Built in accordance to API standards (increased safety), 100% Methanol recovery (lower operating cost), Continuous Glycerin separation (increased conversion yield), Flexibility for batch and continuous operation, More than 98% conversion yield in short time, Incorporated heat recovery system (lower energy consumption), Advanced process control with high degree of instrumentation (increased reliability), Vertical start of the plant, operator friendly, Layout (short project duration), and cost competitive with best quality product (lower capital investment).
Conversion of existing petroleum fuel fired furnaces to biomass fired furnaces for lower cost of operation and protecting environment. Currently doing changes in Costa Rica to burn palm fiber.
Education
Year | Degree | Subject | Institution |
---|---|---|---|
Year: 1997 | Degree: MBA | Subject: Operation Management | Institution: Indira Gandhi National Open University , New Delhi, India |
Year: 1991 | Degree: MS | Subject: Operation Technology | Institution: Birla Institute of Technology & Science,Pilani, India |
Year: 1988 | Degree: AMIE | Subject: Chemical Engineering | Institution: Institution of Engineers, India |
Year: 1983 | Degree: DME | Subject: Mechanical Engineering | Institution: Government Polytechnic, Kanpur , India |
Work History
Years | Employer | Title | Department |
---|---|---|---|
Years: 2006 to Present | Employer: Undisclosed | Title: Board member | Department: Board of Directors |
Responsibilities:Responsible for development of technologies to produce biodiesel and extraction of precious components of palm oil like tocotrinol, tocopherol and beta-carotenes. |
|||
Years | Employer | Title | Department |
Years: 2002 to 2006 | Employer: Quimicos Vegetables S A | Title: VP | Department: Technical |
Responsibilities:Responsible for trouble shooting, de-bottle-necking, operation and maintenance of an Oleo-chemicals complex attached with saponification plant and effluent treatment plant. Have gained hands on experience in Fractionation under high vacuum, methyl ester, amides production . Work involves the management of Just in Time production, quality control, plant maintenance and improvement in process as well as in quality. The major achievement in process improvement in BIODIESEL plant, quality enhancement of soap product, cost reduction in utilities and chemical consumption. Reporting to President and responsible for over 80 personnel. |
|||
Years | Employer | Title | Department |
Years: 2001 to 2002 | Employer: IFFCO (M) Sdn. Bhd. | Title: Dy. General Manager | Department: Technical |
Responsibilities:Responsible for trouble shooting, de-bottle-necking, operation and maintenance of an Oleochemicals complex attached with saponification plant and effluent treatment plant. Have gained hands on experience in oil & fat hydrogenation, distillation & fractionation of various fatty acids, oil & fat splitting, glycerin distillation, effluent treatment, boilers & utilities, tank farm and saponification plants. Work involves the management of Just in Time production, quality control, plant maintenance and improvement in process as well as in quality. The major achievement in process improvement in fatty acid fractionation plant, quality enhancement of soap product, cost reduction in utilities and chemical consumption. Reporting to Managing Director and responsible for over 60 operating and maintenance personnel. |
|||
Years | Employer | Title | Department |
Years: 1997 to 2001 | Employer: Pan Century Edible Oils Sdn Bhd | Title: Senior manager Production | Department: Production |
Responsibilities:Responsible for the management of Malaysia’s largest palm oil refinery at single location, fatty acid distillation, hydrogenation of oil & fat, utilities, Hydrogen gas generation plants. Work involves just in time production, manpower scheduling, evaluation of plant performance, de-bottle-necking, process improvement quality control WCM, ISO 9002, ISO 14001, plant maintenance and modifications. The major achievement in revamping of oil refinery, quality improvement, implementation of new distillation plant, cost reduction in utilities consumption and improvement in process yield. The work involves trouble shooting of oil refinery and fatty acid distillation plants, process modification, capacity enhancement and project implementation. Reporting to the Vice President (Technical) and responsible for over 35 operating and staff personnel. |
|||
Years | Employer | Title | Department |
Years: 1994 to 1997 | Employer: Indo Gulf Fertilizer & Chemical ltd. | Title: Shift Engineer Ammonia | Department: Production |
Responsibilities:Responsible for smooth, efficient & safe operation of Ammonia plant including start up, shut down and emergency handling. Work involves manpower scheduling evaluation of plant performance, debottlenecking, troubleshooting quality control, TPM, ISO 9002, pollution control and maintenance of plant equipment. The job involves the trouble shooting of cryogenic operation, rotating machines, catalytic reactors, furnaces, heat exchangers, distillation, absorption and striping columns, high pressure boilers and Carbon Dioxide Removal system and their efficient operation and annual turn around maintenance. The major achievement in Purge gas Recovery plant commissioning, de-bottle-necking of CDR plant, implementation of naphtha fired furnace and plant capacity enhancement. Reporting to the plant manager and responsible for 15 shift operating personnel. |
|||
Years | Employer | Title | Department |
Years: 1991 to 1994 | Employer: Reliance Industries Ltd. | Title: Process Safety Engineer | Department: Production |
Responsibilities:Responsible for erection, commissioning and operation of GLYCOLs & ETHYLENE section including the enhancement of occupational safety. The work involved safety training, jetty operations, safety audit of Ethylene Oxide installations of customer’s industries. The job involved cryogenics operations like handling liquid Ethylene and liquification of vapours, tank farm management and MIS and co-ordination with shipping division & jetty operating personnel. Reporting to the production manager and responsible for 14 operating personnel. |
|||
Years | Employer | Title | Department |
Years: 1983 to 1991 | Employer: Krishak Bharti Cooperative Limited | Title: process controller | Department: Production |
Responsibilities:Responsible for erection, pre-commissioning, commissioning and process control of 2x1350 MTPD Kellogg Gas Based Ammonia Plants. The work involved catalyst handling & reduction, operation of furnaces, high pressure boilers, centrifugal compressors, catalytic steam reformers, shift conversion and ammonia synthesis, refrigeration and cooling towers. The major achievements are in the pant performance and capacity improvement in Purge Gas Recovery Plant. Reporting to the Dy. Manager and responsible for 7 operating personnel. |
International Experience
Years | Country / Region | Summary |
---|---|---|
Years: 1997 to 2002 | Country / Region: Malaysia | Summary: Responsible for trouble shooting, de-bottle-necking, operation and maintenance of an Oleochemicals complex attached with saponification plant and effluent treatment plant. Have gained hands on experience in oil & fat hydrogenation, distillation & fractionation of various fatty acids, oil & fat splitting, glycerin distillation, effluent treatment, boilers & utilities, tank farm and saponification plants. Work involves the management of Just in Time production, quality control, plant maintenance and improvement in process as well as in quality. The major achievement in process improvement in fatty acid fractionation plant, quality enhancement of soap product, cost reduction in utilities and chemical consumption. |
Years: 2002 to Present | Country / Region: Costa Rica | Summary: Responsible for trouble shooting, de-bottle-necking, operation and maintenance of an Oleo-chemicals complex attached with saponification plant and effluent treatment plant. Have gained hands on experience in Fractionation under high vacuum, methyl ester, amides production . Work involves the management of Just in Time production, quality control, plant maintenance and improvement in process as well as in quality. The major achievement in process improvement in BIODIESEL plant, quality enhancement of soap product, cost reduction in utilities and chemical consumption |
Language Skills
Language | Proficiency |
---|---|
English | |
Spanish | |
Malay | learning stage |
Fields of Expertise
chemical manufacturing facility evaluation, chemical plant, chemical plant design, chemical plant layout, chemical plant management, chemical plant operation, chemical plant start-up, chemical process design, chemical industry, new chemical process operations, pilot plant scale-up, plant operations management, product cost reduction, production control, production engineering, production management, saponification, biodiesel startup, biodiesel technology, biodiesel technology development, biodiesel fuel, biomass, biomass fuel, biofuel, tank farm, chemical emissions, oil treatment, oil fire, operations engineering, oil refining technology, ISO 14000 Environmental Management Standard, ISO 9000 training, ISO 9000 auditing, ISO 9660, ISO 9000 implementation for software, ISO 9000-3, ISO 9004, ISO 9003, ISO 9002, ISO 9001, ISO 9000 series quality system standard, ISO standard, ISO 9000 quality system documentation, ISO 9000 registration system, alternative-fuel combustion, ISO 10303, technology innovation, enterprise application integration, productivity improvement, ISO 9000 implementation, production process, productivity measurement (quantity), research and development, research and development management, automotive diesel engine emission control specification, design process, common soap, International Organization for Standardization, research and development productivity, alternative fuel