Expert Details
Welding Engineering ,Weld Overlay Cladding Technology , Welding Metallurgy, Lean Welding Manufacturi
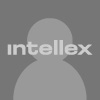
ID: 729909
France
30 Years Expertise of Worldwide Projects, Marine Loading Systems for liquefied natural Gas (LNG) and others liquid products (Oil, LPG, Suffer liquid ...) Wellhead Equipments, International Experience as Welding Engineer and Metallurgist Expert. Welding Engineering and Production Manager, Including Research’s, Education and Practical Applications. Industry Experiences of LNG, Non LNG & Offshore Marine Loading Arms, Weld Overlay Cladding of Wellhead Equipments. Members of the International Trim© Clad Committee Expert of FMC Technologies Inc. Houston (Honors).
Expert Has worked multiple roles as welding engineering, metallurgist consultant, production manager and even technical support for factory production.
Consulted with a company on welding process for root pass pipes and high performance welding.
Worked with company to follow customer specifications in accordance to corrosion properties and chemical levels.Worked with client to get high performance welding process, quality and cost saving.
Worked with compagny to solve PTA Weld Overlay process (Stellite 12/ AISI 410) for seats valves
Worked with austalian compagny for thrid Party Inspection of pressure vessel Equipment
Education
Year | Degree | Subject | Institution |
---|---|---|---|
Year: 1987 | Degree: Internal Post Graduate Research (PhD) | Subject: Welding Engineering & Welding Metallurgy | Institution: Welding Institute of Paris |
Year: 1979 | Degree: Welding Engineer & Metallurgist Expert | Subject: Welding Engineering, Welding Metallurgy, Corrosion , Welds Design Optimisation, Weld Overlay Cladding, | Institution: Welding Institute of Paris |
Year: 1974 | Degree: Welding Specialist | Subject: Welding Technology, Weldability, Corrosion, Design of Welds | Institution: Welding Institute of Paris |
Year: 2006 | Degree: Educator for Post Graduate School | Subject: Welding Engineering, Manufacturing Engineering | Institution: Engineers School (ItII Auxerre) France / 89100) |
Year: 2007 | Degree: Continuing Education | Subject: Welding Engineering , Weldability, Corrosion of Welds, Computational Welding Mechanic (CWM) | Institution: Welding Institute of Paris, Institute Internationale of Welding (IIW), |
Work History
Years | Employer | Title | Department |
---|---|---|---|
Years: 2007 to 2010 | Employer: FMC Technologies Inc | Title: Site Expert Welding Manager | Department: LNG Loading Sytems & Wellhead |
Responsibilities:In charge to analysis and recommendations on welding specifications requirements for the customers; Studies and evaluated the Welding Processes Technologies improvements costs reductions. Establishes policies and standard for all the welding activities, |
|||
Years | Employer | Title | Department |
Years: 2005 to 2007 | Employer: FMC Technologies | Title: Industrial & Technology Manager | Department: LNG Loading Sytems & Wellhead |
Responsibilities:In Charge to Manage and Directed the Production Engineering Department. Provide Welding expertise to the Production, Engineering, Sourcing, Customers services departments.Reengineering process (Production & Engineering) productivity improvement, cost reductions, reinforcement to the Production Engineering Department . Analysis and recommendations on welding specifications requirements for the customers, Lead the Welding technology improvement. Weld Assistant, Software implementation. Apply the principle of Kaisen for pressure piping by standardizing on One Wire, One Flux, One Gas and One welding system. Study & Managed the major new projects investments and increased the efficiency. |
|||
Years | Employer | Title | Department |
Years: 2003 to 2004 | Employer: FMC Technologies | Title: General Production Manager | Department: LNG Loading Sytems & Wellhead |
Responsibilities:In Charge to Manage & Directed the Loading Systems Production Department, Analysis and recommendations on welding specifications requirements for the customers, Lead the cost reduction actions, externalization for the low values components, integration of sub contractors. Lead the new Welding technology, the productivity improvements, the costs saving and the new projects investments to increase efficiency. |
|||
Years | Employer | Title | Department |
Years: 1999 to 2002 | Employer: FMC Technologies | Title: Industrial Technologies Manager | Department: LNG Loading Sytems & Wellhead |
Responsibilities:In Charge to Manage & Directed the Manufacturing Engineering department,Analysis and recommendations on welding specifications requirements for the customers. Managed the two product lines, to lead the new Welding Technology, the productivity improvements and the costs savings actions. Study & Managed the new projects investment and increased efficiency and Savings |
|||
Years | Employer | Title | Department |
Years: 1989 to 1998 | Employer: FMC Technologies | Title: Production Manager | Department: LNG Loading Sytems & Wellhead |
Responsibilities:In charge to Manage & Directed the Loading Systems Production Departments. Directed the Welding & Cladding & Overlaying activities for the Loading Systems and Wellhead (LS & WED), the machining and assembly activities for the Loading Systems (LS).Analysis and recommendations on welding specifications requirements for the customers; Lead productivity improvements, costs savings and actions for applying Lean to the Welding Management. Study & Managed the Loading Systems Factory Plant Extension, the new projects investments and increased efficiency and Savings. |
International Experience
Years | Country / Region | Summary |
---|---|---|
Years: 2002 to 2003 | Country / Region: Alaska | Summary: Welding of Super Duplex Pipes for Marine Loading Arms, Valdez,Alaska |
Years: 2006 to 2006 | Country / Region: CANADA | Summary: Welding Technologies for LNG Marine Loading Arms |
Years: 2007 to 2007 | Country / Region: Algerie | Summary: Revamping of LNG Maring Loading Arms development of Welding processes for cryogenic applications |
Additional Experience
Expert Witness Experience |
---|
Expert services in welding, joining process and contractor surveys, qualities and audits. |
Training / Seminars |
---|
Multiple seminars in welding. |
Vendor Selection |
---|
All aspects of sourcing in regards to welding equiptment and facilities. |
Marketing Experience |
---|
Industry insights into multiple areas as current employment works directly with welding companies specifically. |
Other Relevant Experience |
---|
Skills in developing welding tools and procedures. Lean Welding Manufacturing |
Language Skills
Language | Proficiency |
---|---|
french | |
German | |
English |
Fields of Expertise
pressure vessel welding application, weld corrosion, weld metal, weld overlay, weldability, welded joint design, welding automation, welding code, welding engineering, welding technology, weldment corrosion resistance, argon arc welding, automatic welding, dissimilar material laser welding, dissimilar material welding, arc welding, dissimilar metal welding, electroslag welding, explosive welding, ferrous metal heat treatment, fillet weld, flux-cored arc welding, friction welding, fusion welding, gas-metal arc aluminum welding, gas-metal arc welding, gas-tungsten arc aluminum welding, gas-tungsten arc weld, gas-tungsten arc welding, high-nickel alloy welding, laser weld, laser welding, low-alloy steel welding, overlay, plasma-arc welding, shielded arc welding, stainless steel welding, submerged-arc welding, welding, welding quality, welding quality control, welded pipe, alloy, alloy corrosion, aluminum, aluminum alloy weld performance, aluminum cutting, aluminum fusion welding, aluminum welding, aluminum welding filler alloy, American Petroleum Institute, arc spray, argon, ASME boiler and pressure vessel code, ASME piping code, ASME Section IX Code Welding, automated manufacturing, automatic soldering, automotive engineering, base metal (welding), bend test, butt weld, butt welding, carbon arc, carbon arc welding, carbon dioxide arc welding, carbon steel, carbon steel corrosion, carbon-steel welding, conduction welding, electric arc, ferrous metal, ferrous metal casting, ferrous metal corrosion, ferrous metal machining, ferrous metal recycling, ferrous metal refining, ferrous metallurgy, gas welding, induction welding, inert gas-shielded arc welding, laser cladding, metal welding, Monel, Monel welding, nickel alloy corrosion, nickel alloy weld corrosion, nine-percent-nickel welding, pipe welding, pipeline, pressure vessel, pressure welding, repair welding procedure, shielded metal arc welding, specific material welding, stainless steel weld corrosion, structural welding application, weld, weld porosity, welded joint, welding application, welding effect on stainless steel corrosion resistance, welding effect on steel corrosion resistance, welding equipment, welding machinery, welding stress analysis, wire welding, metallurgical testing, arc interruption, ferrous metal annealing, robotic welding, corrosion-resistant aluminum coating, distortion control, corrosion-resistant metal, corrosion-resistant material, Magnetarc welding, magnetically impelled arc butt welding, welding testing, bare-metal arc welding, nonferrous metal corrosion, welding fumes, aluminum torch welding, gas torch, film welding, alloy steel, welding effect on nickel alloy corrosion resistance, welding effect, welding failure analysis, pulp-and-paper industry welding, flue gas desulfurization scrubber welding, corrosion-resistant alloy, metal alloy, welding robot, welding certification, electron-beam welding, magnetic flux welding, electroslag casting, design engineering, coating material, lead welding, tack welding, welding standard, industrial engineering, metallurgy, helium, metal friction welding, foil seam weld, flow welding, corrosive wear, corrosion prevention, backhand welding, arc spot weld, arc seam weld