Expert Details
Welding Engineering: Application, Arcs, Laser, Base Metal, Troubleshooting, Pressure, Nuclear, Code
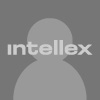
ID: 107879
Colorado, USA
Expert has written procedures and welded with manual, semi-automatic, and robotic welding processes. He enjoys the challenges presented by all types of welding opportunities, especially automated and robotic welding.
Expert practices a service-oriented approach to managing the business of fabrication and manufacturing. He is an advocate for the value of time at work, increasing return on investment, and helping companies provide long-term employment.
He has welded titanium, zircaloy, reactive metals, inconel, stainless, aluminum, HSLA, and plain carbon steel. Expert has used most cutting processes, including oxyacetylene, plasma, mechanical, laser, and electric discharge machining. He is familiar with most welding and joining processes (e.g., arc welding, resistance, electron beam, lasers, soldering, brazing, ultrasonic bonding, and adhesives). He has developed and tested processes, procedures, and standards for real-time radiographic and ultrasonic examination.
Early in Expert's career, he started learning welding metallurgy and inspection as an Industrial Engineer. As he experienced more challenging welding procedures and nondestructive evaluation requirements, he chose to further his formal education at The Ohio State University. While there, he learned structured problem-solving methodologies for various additional types of welding (electron beam, lasers, robotic applications, etc.).
While a Graduate Research Associate at the OSU Welding Engineering Department, he helped design and patent wet welding (underwater welding) electrodes, wrote proposals for government grants, developed and tested flux mixtures, reviewed finite element analysis for weld bead profiles, used computer-aided welding design techniques for ship-building and aerospace applications and taught underwater welding and NDT classes.
While working as a welding applications engineer with a national shielding gas supplier, Expert dealt with hundreds of industrial users of argon and helium welding gas mixtures. He conducted management seminars and extended courses on health-safety-environmental issues, including benchmarking and financial analysis for many types of manufacturing and fabrication.
Expert provides troubleshooting expertise for numerous manufacturing and fabrication processes. He systematically works with sales, cost accounting, design engineers, materials (purchasing, receiving, and storage), welding processes, quality assurance, and warranty claims to solve welding problems.
For three decades Expert has dealt with the challenges of being a professional welding engineer and a non-destructive testing engineer. For example, he has interacted with presidents, vice-presidents, department managers, academic researchers, design engineers, manufacturing engineers supervisors, repair personnel, welders, robots, quality engineers, and NDT technicians. He has interpreted and certified code compliance and piece-rate labor incentive programs throughout the USA and in court cases.
Expert developed the QC programs and documented welding procedure specifications for dozens of pressure vessel fabricators. The vessels and tanks were used for oil and gas processing, refineries, chemical plants, and pharmaceutical and food processors. As an advocate of "Zero Accidents," Expert is consistently involved in safety seminars, training, and thorough accident investigation. He believes that accidents do not just happen, they are planned.
Expert has designed, witnessed fabrication, and inspected pressure vessels manufactured with carbon steel, stainless steel, and vessels clad with titanium and zirconium. Wall thickness ranges have been from .035" zirconium through 8" steel. Pressures ranged from vacuums to 5000 psi.
While working as a Senior Welding Engineer with Siemens Power Corporation-Nuclear Division, Expert as part of a team that manufactured zircaloy nuclear fuel rods for commercial reactors. He contributed to globalized welding operations in the US and Germany for "world-class quality" standards. He received official Siemens corporate recognition for the MECAZIR research & development contract for a French reactor research program.
Expert designed, tested, verified, and published a technical review on an alternative manufacturing process for second pass acceptance of fuel rod end closure welds. Customer recognition and intangible benefits were enormous, with annual savings to a single customer exceeding $450,000 USD.
He was a vested team contributor for process controls with a 23 person manufacturing quality team for consistent daily production of 3100 GTAW fuel rod welds (.375" diameter and approximately 300 psi internal pressure). His team set world records for first-pass acceptance of welds.
Expert was a co-inventor and tested a revolutionary underwater "wet welding" electrode. He developed and published the marketing plan for a $2.0 MM annual revenue and 45% profit, 200% ROI. He is a founding member of an underwater cutting committee and co-author of an underwater welding specification. He is the lead author for writing the testing scheme for underwater welds as inspected by Certified Marine Welding Inspectors. He is also a Certified PADI Open Water Diver and has welded underwater.
Expert teaches and applies the AWS, ASME, API, ANSI, and Military specifications, standards, and codes. As an AWS Certified Welding Educator and Certified Welding Inspector, he teaches short courses for examination reviews and to improve the overall quality of weld inspection services. He has interpreted codes and standards as a first-line supervisor and fabrication manager and industrial engineer. He formed his consulting firm to specialize in the application of technology, training, and testing of welds per codes and standards and forensic engineering.
As a director of engineering, metallurgist, and supervisor of NDT technicians, Expert wrote inspection plans and procedures and inspected steel buildings, steel mills, ladle and furnace fabricators, bridges, and food processing equipment plants. He developed sales forecasts, project cost estimates, and American Council of Independent Laboratory (ACIL) Certification documents. He is knowledgeable of the application and proficient in teaching radiography (RT-Gamma and X-ray), ultrasonic (UT-contact and immersion), eddy current (ET), liquid penetrant (PT), magnetic particle (PT), visual (VT), leak testing (LT), and visual (VT) techniques.
As a welding specialist, Expert often serves as a third-party inspector for major welding projects. He has been engaged in welding, metallurgical evaluations, destructive and non-destructive testing for most of his professional career. He remains active worldwide, expanding corporate capabilities and certifying laboratories to provide structural and construction material evaluations, welding inspection, shop inspection, and field erection of structural steel, real-time inspection of welding processes, strain gauge measurements, residual stress, and distortion analysis, and welding process improvements.
As an industrial engineer, Expert has written brazing and soldering procedures for electronic assemblies, circuit boards, power supplies, waveguide components, and wiring harnesses for telephone microwave systems. At a manufacturer of heat pump switching valves, Expert performed troubleshooting and improved process reliability for production brazing and in-process testing of 1100 units per shift.
Expert has experience with the installation of cladding materials on the interior of pressure vessels. This is accomplished with zirconium or titanium while the structural components of the pressure vessel remain carbon steel. Dissimilar metal welding is necessary at the transition between these components while welding attachments such as nozzles and couplings. Similarly, he is experienced with dissimilar metal welding applications while gas tungsten arc welding titanium tubes to zircaloy tubes with an argon shielding gas in the nuclear fuel rod fabrication industry. It was a successful project and required weld metallurgy considerations during the design stages.
Expert develops welding procedures and provides training courses about titanium welding on a regular basis. He knows the details of cleanliness, purging tubes, providing adequate shielding gas, and above all else cleanliness. Base materials and filler metals must be cleaned with acetone, along with adequate shielding gas before initiating the arc, during welding, and a few seconds after the arc is extinguished.
Compliance: Expert worked on-site to solve welding problems in manual and automated robotic GMAW processes for numerous materials and products, solved weld-cracking problems, and tested and implemented appropriate welding procedures.
Technology: He developed welding procedures and solved welding problems.
Training: Expert has trained managers, engineers, technicians, and personnel in sales and design on topics covering materials, processes, quality, and warranty issues.
Testing: He runs an independent testing agency and certifies processes and personnel.
Failure Analysis: Expert has been an expert witness in numerous litigation issues concerning misinterpretation and misapplication of welding codes.
Education
Year | Degree | Subject | Institution |
---|---|---|---|
Year: 1992 | Degree: Ph.D. | Subject: Welding Engineering | Institution: The Ohio State University |
Year: 1989 | Degree: M.S. | Subject: Welding Engineering | Institution: The Ohio State University |
Year: 1982 | Degree: M.B.A. | Subject: Business | Institution: University of Southwestern Louisiana |
Year: 1969 | Degree: B.S. | Subject: Industrial Engineering and Management | Institution: Oklahoma State University |
Work History
Years | Employer | Title | Department |
---|---|---|---|
Years: 1996 to Present | Employer: Undisclosed | Title: Founder and Senior Consultant | Department: |
Responsibilities: |
|||
Years | Employer | Title | Department |
Years: 1993 to 1996 | Employer: Siemens Power Corporation | Title: Senior Welding Engineer, Nuclear Division | Department: |
Responsibilities: |
|||
Years | Employer | Title | Department |
Years: 1992 to 1993 | Employer: Praxair Corporation | Title: Senior Welding Engineer | Department: |
Responsibilities: |
|||
Years | Employer | Title | Department |
Years: 1987 to 1992 | Employer: The Ohio State University | Title: Research Associate | Department: |
Responsibilities: |
|||
Years | Employer | Title | Department |
Years: 1990 to 1992 | Employer: Dresser-Marion Power Shovel Inc. | Title: Welding Foreman | Department: |
Responsibilities: |
|||
Years | Employer | Title | Department |
Years: 1978 to 1995 | Employer: Grantham Engineering Services/Owners Laboratory | Title: Welding Engineer | Department: |
Responsibilities: |
|||
Years | Employer | Title | Department |
Years: 1975 to 1978 | Employer: Waukesha Pearce Industries, Inc. | Title: Project Manager | Department: |
Responsibilities: |
|||
Years | Employer | Title | Department |
Years: 1971 to 1975 | Employer: Redman/Winston Industries, Inc. | Title: Corporate Engineer | Department: |
Responsibilities: |
Government Experience
Years | Agency | Role | Description |
---|---|---|---|
Years: 1998 to 1999 | Agency: Marine Corps Logistics Base | Role: Consultant | Description: He worked to improve weld quality and welding certification. |
International Experience
Years | Country / Region | Summary |
---|---|---|
Years: 1993 to Present | Country / Region: Germany | Summary: Expert conducted exchanges of technical information and engineering data to improve welding processes and nondestructive testing techniques for nuclear fuel rod manufacturing. |
Years: 1992 to Present | Country / Region: Canada | Summary: He worked on metallurgical analyses and nondestructive testing techniques for titanium aluminides and robotic welding troubleshooting and process qualification. |
Years: 1989 to Present | Country / Region: Israel | Summary: Expert worked on technical reviews of international welding and metallurgy for oilfield production and refinery equipment integrity. |
Years: to Present | Country / Region: Taiwan | Summary: He made presentations and technical reviews of international welding and metallurgy for cutting and welding consumables. |
Years: to Present | Country / Region: Korea | Summary: Expert gave technical reviews of international welding and metallurgy for aerospace and shipbuilding in Korea. |
Career Accomplishments
Associations / Societies |
---|
Expert is co-founder of an underwater welding institute and of a well-known chapter. He is a member of the Edison Welding Institute and FMA. As an active member of a number of technical and professional societies, Expert has held numerous offices locally and nationally. Examples include the American Welding Society (21 years), ASM International, the American Society of Naval Engineers, the National Society of Professional Engineers, the National Academy of Forensic Engineers, the Colorado Professional Engineers, and the OSU Welding Engineering Alumni Association. |
Licenses / Certifications |
---|
He is a Registered Professional Engineer in Louisiana, Texas, Ohio, Washington, Colorado, Wyoming, and New Mexico. Expert has been a Registered Professional Engineer since 1975, certified ASNT Level III, a AWS Certified Welding Inspector, and a AWS Certified Welding Educator. |
Professional Appointments |
---|
He has served as an AWS Acadiana Section chairman, an AWS Inland Empire Section chairman, the Denver AWS Section 039 Chairman, and the AWS District 20 Director. |
Awards / Recognition |
---|
Expert has received many honors, including the Arsham Amirikian Memorial Maritime Award, the W.A. Hobart Memorial Metal Award, and the C.E. Jackson Award. He is a Welding Advisory Board Member for Pikes Peak Community College. Expert remains especially proud of several accomplishments while at Siemens Power Corporation - Nuclear Division, Richland. These include MECAZIR assembly and welding, with receipt of the prestigious "Rock Award" and cost, throughput, quality, and safety improvements. |
Publications and Patents Summary |
---|
His recent publications are in the fields of processes, consumables, testing, and safety and management. |
Additional Experience
Expert Witness Experience |
---|
Expert has been involved in numerous litigation issues. These include misinterpretation and misapplication of welding codes, non-adherence to established quality assurance programs, failure analysis by metallurgical evaluations, OSHA safety investigations, explosions, equipment failures, accident investigation, analysis, reconstruction, bridges, pipelines, tanks, and testing materials. To date, his forensic experience exceeds two dozen cases. |
Training / Seminars |
---|
Expert's most recent seminar was presented at several locations across the USA (Baltimore, Detroit, and Chicago) with the Fabricators and Manufacturers Association (1999). He recently presented a seminar for the American Society of Nondestructive Testing (ASNT) Colorado on nondestructive tests for welds. His latest presentation was for the National Association of Corrosion Engineers (NACE). He presented welder training to a national sign manufacturer on SMAW, FCAW, and GMAW with hands-on demonstrations. At the Society of Manufacturing Engineers in Cleveland, Expert presented a seminar. He has performed many other presentations. These are just to name a few. |
Vendor Selection |
---|
Expert has experience locating vendors of the following: facility audits, manufacturing assessments, quality assurance compliance/verification, welding procedures development, and welder/process certification. |
Marketing Experience |
---|
Underwater Welding Electrode--sales, engineering, metallurgical evaluations, and field tests on prototype welding electrodes; investigated and secured Ohio Department of Economic Development funds to invent and test a revolutionary "wet welding" electrode. Engineering, Project Management, and Inspection Services--design and manufacturing of offshore oilfield structures, drilling, production skids, and living quarters; developed marketing and financial plans and applied ASME, API, AWS, SAE, and Military standards to welding operations. Quality Assurance and Testing Services--established QC programs for ASME code U-Stamps and NBIC R-Stamps; designed and installed equipment for hydrogen sulfide service in remote locations, food preparation tanks, and aerospace fuel containers. Construction Materials Inspection and Testing Services--developed a marketing plan, operating strategy, and procedures for certification by the American Association of Laboratory Accreditation (AALA) and the American Council of Independent Laboratories (ACIL); specialized in construction materials testing (CMT) of structural steel; worked with improved data acquisition and reporting system for nondestructive testing, destructive testing, and metallurgical evaluations in a laboratory. Manufactured and Steel Structures--implemented piece-rate labor incentive; conducted seminars with routine surveillance of performance with plant management and labor; interpreted and applied NLRB guidelines. Subresonant Vibratory Stress Relief Equipment--served as a marketing representative for Bonal International for welding management equipment; gave demonstrations and technical presentations on weld conditioning and stress relief. |
Other Relevant Experience |
---|
Expert is knowledgeable of boilers, pressure vessels, nondestructive testing, offshore platforms, process piping, underwater welding, welding safety, and welding equipment. |
Fields of Expertise
base metal (welding), welding application, welding engineering, pressure welding, carbon-steel welding, structural welding application, arc welding, welding, underwater welding application, welding troubleshooting, metal nondestructive testing, underwater inspection, underwater melt cutter, underwater nondestructive testing, welding certification, pressure vessel welding application, quality, nuclear welding application, laser welding, welding code, nondestructive testing, brazing, solder, dissimilar metal welding, dissimilar material welding, titanium welding, automatic welding, robotic welder, robotic welding, welding automation, bend test, welding quality, welding quality control, welding testing, metal weldment, welding standard, metal welding, welding technology, repair welding procedure