Expert Details
Thin Film Deposition, Specializing in Reactive Sputtering
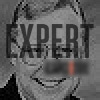
ID: 722891
California, USA
Expert has been instrumental in the use of DC sputtering for many applications starting with the deposition of numerous metallic films and with the reactive sputter deposition of conductive hard coatings such as the nitrides of titanium, zirconium, hafnium, vanadium, and niobium. He has prepared superhard, superlattice coatings of TiN/VN and TiN/NbN with hardnesses approaching about 50 GPa with DC reactive sputtering combined with a DC bias on the substrate.
Expert’s entire professional career of now over 32 years has been spent in the field of thin film deposition technology. He is responsible for the development of the high-rate reactive sputtering process for which he holds a US patent, for the development of the multi-cathode unbalanced magnetron sputtering technology, for the development of multi-layered polycrystalline superhard superlattice coatings, for the use of pulsed DC power for the reactive deposition of insulating films, and most recently for the use of high power pulsed magnetron sputtering for the deposition of conducting and insulating films.
Throughout his professional career, Expert has used direct current (DC) power for the sputter deposition of conducting films and for the substrate biasing of conducting films. He has used both conventional DC power and pulsed DC power for the sputter deposition of coatings. Most recently he has been involved with the development of high power pulsed magnetron sputtering (HPPMS) using very high power DC pulses that result in a very high degree of ionization of the sputtered material.
Expert notes that ion sputtering is a form of sputtering where the generation of the ions is separated from the sputtering operation. He has used linear ion sources for the sputter deposition of materials, for the cleaning of substrate surfaces, and for an ion-assisted deposition.
Expert has used magnetrons for magnetron sputtering of a variety of materials. He notes that magnetron sputtering provides a higher rate of deposition compared to diode sputtering, and it also provides for a cooler deposition.
Expert began his career in sputter deposition as magnetron sputtering was introduced. He has used magnetron sputtering throughout his career combined with DC, pulsed DC, RF, and now high power pulsed magnetron sputtering power for the deposition of a very wide variety of films. He was instrumental in the implementation of unbalanced magnetron sputtering for multi-cathode systems, which greatly expanded the use of magnetron sputtering for many industrial applications.
Expert has used planar magnetron sputtering for the deposition of many different materials. He has used planar magnetrons in many different sizes and shapes including rectangular, circular, and rotating cylindrical magnetrons. He was instrumental in the development and use of multi-cathode unbalanced magnetron planar magnetrons system, which opened up sputtering to many new industrial applications.
Expert has spent his entire career since graduate school in the field of reactive sputtering. He is the inventor of the high-rate reactive sputtering process for which he holds a U.S. patent, and he was one of the first people to apply pulsed DC power to the reactive sputter deposition of insulating films. Recently he has been involved with multiple-gas reactive sputtering and with the use of reactive high power pulsed magnetron sputtering for depositing insulating films. He has developed and marketed a reactive gas control system for controlling the partial pressure of up to two reactive gases simultaneously.
Expert’s entire career has revolved around the sputter deposition of coatings. He has been involved with the sputter deposition of both conductive and insulating films with the latter mostly deposited using pulsed DC power and reactive sputter deposition. He has been involved in many advancements for sputter deposition such as high-rate reactive sputter deposition, multi-cathode unbalanced magnetron sputtering, reactive sputter deposition of insulating films using pulsed DC power, and high power pulsed magnetron sputtering.
Expert has used a wide variety of sputtering targets over the course of his career in sputter deposition. He has used elemental, alloy, and compound targets. He was instrumental in the use of Ti-Al targets for the reactive sputter deposition of TiAlN coatings for the cutting tool industry. He has used sputtering targets in many sizes and shapes from a small 1-inch diameter circular target up to almost 4-meter long targets for the glass coating industry.
Expert was one of the first people to reactively sputter deposit multi-layered superhard polycrystalline superlattice coatings. He was able to obtain hardnesses in these superlattice coatings of over 50 GPa, which matched the hardness of similar single crystal superlattice coatings. This pioneering work has resulted in polycrystalline superlattice coatings being used today for dry machining operations.
Expert has been involved in the deposition of thin films throughout his professional career. He was instrumental in the development of reactive unbalanced magnetron sputtering processes that are now used today for the deposition of thin films for the cutting tool industry.
Expert’s entire career has been involved in the deposition of thin film. Highlights include the deposition of hard wear-resistant thin films for cutting tool applications; the development of superhard, superlattice thin films; the reactive sputter deposition of insulating films using pulsed DC power; and most recently in the use of high power pulsed magnetron sputtering power for the deposition of both metallic and insulating thin films.
Expert has been responsible for the development of several processes for thin film processing. He is the inventor of the high-rate reactive sputtering process, which can provide deposition rates for materials such as TiN that are the same rate as that of the metal film. He pioneered the use of multiple unbalanced magnetron cathodes for the deposition of hard coatings, and he was one of the first people to use pulsed DC power for the reactive sputter deposition of insulating thin films. He has developed and marketed two-gas reactive gas control system for the reactive sputter deposition of thin films.
Expert has been instrumental in the development and application of thin-film technology for PVD hard coatings, control of reactive sputtering processes, multiple cathode unbalanced magnetron sputtering, high-rate reactive sputtering of insulating films, and high power pulsed magnetron sputtering.
Expert was one of the first people to demonstrate that it is possible to use physical vapor deposition to reactively sputter deposit titanium nitride films using closed-loop control of the partial pressure of the reactive gas. This finding resulted in the development of a closed-loop control system for the reactive gas partial pressure that has since been commercialized.
Expert has sputtered titanium for the deposition of metallic films and for compound films. He notes that titanium films were deposited for a special anti-corrosion device for an automotive cooling application where it was important to accelerate corrosion of a protective membrane in order to release a protective anti-corrosion agent for the overall system. He has also reactively sputtered metallic titanium in the presence of oxygen and/or nitrogen to deposit titanium nitride, titanium oxide, and titanium oxynitride coatings.
In addition to the reactive physical vapor deposition of sputtered titanium nitride thin films, Expert extended the technology for the physical vapor deposition by reactive sputter deposition for zirconium nitride thin films. As with the titanium nitride coatings, he showed that zirconium nitride films could be reactively sputter deposited at very high rates, in this case up to 95% of the metal deposition rate, by controlling the partial pressure of the reactive gas.
Expert has sputtered zirconium mainly during the reactive sputter deposition of zirconium nitride and zirconium oxide. Using partial pressure control of the reactive gases (nitrogen and oxygen), zirconium nitride and zirconium oxide films can be reactively deposited at rates approaching that of the metal deposition rate.
Expert implemented a closed-loop reactive sputtering control system for encapsulation of OLEDs.He designed and constructed a multi-gas reactive sputtering control system. Expert assisted a client with the development of a multi-layer coating system to provide wear/corrosion resistance and to be visually pleasing.He provided guidance and assistance for a client to understand the benefits of high power pulsed magnetron sputtering. Expert worked with a client to help him expand the applications for his vapor deposition technology.
Education
Year | Degree | Subject | Institution |
---|---|---|---|
Year: 1975 | Degree: PhD | Subject: Materials Science Engineering | Institution: Brown University |
Year: 1968 | Degree: ScM | Subject: Materials Science Engineering | Institution: Brown University |
Year: 1966 | Degree: ScB | Subject: Materials Science Engineering | Institution: Brown University |
Work History
Years | Employer | Title | Department |
---|---|---|---|
Years: 2005 to Present | Employer: Undisclosed | Title: President | Department: |
Responsibilities:Expert provides consulting services to the thin film industries, specializing in sputtering and reactive sputtering processes. |
|||
Years | Employer | Title | Department |
Years: 2002 to 2005 | Employer: Advanced Energy Industries, Inc. | Title: Senior Scientist | Department: |
Responsibilities:He was responsible for developing reactive sputtering control systems and for mentoring up-and-coming scientists and engineers. |
|||
Years | Employer | Title | Department |
Years: 1999 to 2002 | Employer: Reactive Sputtering, Inc. | Title: President and Founder | Department: |
Responsibilities:Expert was resposnible for developing a reactive sputtering control system. |
|||
Years | Employer | Title | Department |
Years: 1997 to 1999 | Employer: Sputtered Films, Inc. | Title: General Manager for Magnetic Products | Department: |
Responsibilities:He was responsible for the sputter deposition product line for the magnetic thin film head industry. |
|||
Years | Employer | Title | Department |
Years: 1987 to 1997 | Employer: Northwestern University | Title: Manager of the Thin Film Deposition Group | Department: Basic Industrial Research Laboratory |
Responsibilities:Expert was responsible for developing programs to transfer thin film deposition technology to industry. |
|||
Years | Employer | Title | Department |
Years: 1977 to 1987 | Employer: Borg-Warner Corporation | Title: Senior Scientist | Department: Research Center |
Responsibilities:He developed thin film deposition processes for applying hard coatings to enhance the wear life of components. |
|||
Years | Employer | Title | Department |
Years: 1975 to 1977 | Employer: American Can Company | Title: Scientist | Department: Research Center |
Responsibilities:Expert was responsible for developing sputtering processes to apply coatings to enhance the life of can-forming tooling. |
|||
Years | Employer | Title | Department |
Years: 1968 to 1972 | Employer: U.S. Navy | Title: Line Officer | Department: |
Responsibilities:He was an engineering officer and division officer on two ships. |
International Experience
Years | Country / Region | Summary |
---|---|---|
Years: to Present | Country / Region: Europe | Summary: Expert has given many invited talks on sputtering and reactive sputtering at numerous international meetings in Europe. |
Years: 2004 to 2004 | Country / Region: Netherlands | Summary: He provided expertise and guidance for the implementation of a reactive sputtering control system. |
Career Accomplishments
Associations / Societies |
---|
Expert is a member of AVS The Science and Technology Society, and the Society of Vacuum Coaters. |
Professional Appointments |
---|
He is co-editor of Surface and Coatings Technology. |
Awards / Recognition |
---|
Expert received the AVS Thornton Award and the SVC Mentor Award. |
Publications and Patents Summary |
---|
He has 137 publications and 11 U.S. patents. |
Additional Experience
Training / Seminars |
---|
Expert teaches one or two day short courses on Tribological Coatings, Hard Coatings by PVD Methods, Sputter Deposition, and Reactive Sputtering. |
Vendor Selection |
---|
He is knowledgeable of component and equipment suppliers for the vacuum deposition industry. |
Marketing Experience |
---|
Expert developed and brought to market a two-gas reactive sputtering control system, which was subsequently sold to a major equipment manufacturer. |
Language Skills
Language | Proficiency |
---|---|
French | When necessary Expert can read French, and he can speak the language slowly. |
Fields of Expertise
aluminum sputtering, DC sputtering, deposition technology, direct current, ion sputtering, magnetron, magnetron sputtering, planar magnetron, reactive sputtering, sputter deposition, sputtering target, superhard material, thin film, thin-film deposition, thin-film processing, thin-film technology, titanium nitride physical vapor deposition, titanium sputtering, zirconium nitride physical vapor deposition, zirconium sputtering, helium mass spectrometry, thin film science, atomic layer deposition, tool wear, vacuum vessel, vacuum technique, vacuum environment, deposition analysis, black thin film, friction measurement, vacuum outgassing, titanium adhesion, diode, vacuum test, chromium sputtering, copper sputtering, tungsten sputtering, indium tin oxide sputtering, gold sputtering, vacuum leak testing, diamond-like carbon, ion-beam etching, argon sputtering, indium tin oxide, aluminum deposition, metal film, high-purity material, high-purity aluminum, high-purity metal, mass spectroscope, vacuum gage, high vacuum system, high-vacuum technology, metal to ceramic adhesion, deposited material, vacuum system design, vacuum leak detection, reactive ion etching, vacuum measurement, ion plating process, ion etching, deposition, transparent conductive thin film, ultra-high vacuum system, vacuum system, cathode, vapor deposition, vacuum technology, vacuum pump, ultra-high vacuum, triode sputtering, tribology, titanium, semiconductor processing equipment, semiconductor metallizing, radio-frequency sputtering, metallizing, high vacuum, friction, film coating process, diode sputtering, coating