Expert Details
Surface Treatment, Shot Peening & Blasting, Zinc Plating, Phosphating, Carburizing, Heat Treatments
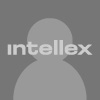
ID: 724740
India
Expert has expertise in case hardening especially Carburizing, Nitriding, and carno nitriding. His expertise is in Sealed quench Furnaces (Batch Integral Quench Furnace), Continuous mesh belt Furnaces, Rotary retort furnaces, and rotary hearth furnaces.
He has solved problems like wavy case, low surface carbon, low hardness and hardness variation within the gear etc.
He has expertise on different atmosphere like Natural Gas+ Nitrogen, Endo Gas + Nitrogen, LPG+Methanol, LPG+ methanol+ Nitrogen, Nitrogen less atmospheres for carburising, wtc.
He has saved cost on processing gas consumption, optimised the process parameters which can save process duration and cost. One can count on Expert, on his strength on process issues on Carburizing, hardening and tempering in any combination of atmosphere.
Expert has expertise in case hardening, case carburizing, Induction hardening, Induction softening, Carburizing, Nitriding and carbo Nitriding.
His expertise are in Sealed quench Furnaces (Batch Integral Quench Furnace), Continuous mesh belt Furnaces, Rotary retort furnaces, and rotary hearth furnaces. He has good exposure to Walking beam furnaces, shaker hearth furnaces, Plug hardening and press quench operations.
He has focus on Process time reduction, energy cost reduction, process quality improvement and expert in proving the results.
Expert has expertise in various plating processes. He has specialised in fastener coating, to have modified surface characteristics.
His expertise are in Chloride zinc, Alkaline zinc, Chloride copper, Alkaline copper, cyanide copper plating operations. Also he has expertise in Zinc Phosphating, Manganese Phosphating and Mechanical plating operations.
He has optimised the process parameters to reduce the process time, to improve the through put, and less water consumption. He has saved significantly, to many electroplaters by optimising the process parameters.
His expertise in education to the operators on plating process control and bath control are very classic in nature.
Plating test is one of the favorite of Expert. He has expertise knowledge in checking the surface characteristics after plating.
His Expertise are testing and interpretation of these tests and advising the plating process correction. He is expert in Plating thickness testing, Sald spary testing, Cyclic corrosion testing (CCT), Copper accelerated Acetic acid test (CASS), Cyclic salt/sulfer di oxide spray (FOG) test, Multi gas test, chip resistance test, solvent resistance test, Hydrogen embrittlement test, Bend test, adhesion test, cross hatch test, Abrasion test, Gravelometer test, and many more...
Expert has expertise in various zinc plating processes. He has specialised in fastener coating, to have modified surface characteristics. His expertise are in Chloride zinc, Alkaline zinc, with various chromating finishes are very useful. He has very good exposure to change the co-efficient of friction in fastener coating application.
He has also helped the fastener industry, in identifying the Hydrogen embrittlement failures, and eliminating the effects of hydrogen embrittlement effect by improving the cathode efficiency and by introducing the baking process to de-embrittle the fasteners. He has also developed the test methods and fixtures to check the fastener hydrogen embrittlement effect.
Expert is also an expert in DIP Spin coating process like Dacromet, Geomet, Magni, PTFE coatings and Electroless process like Autophoretic and mechanical plating process.
He took a consulting project for Jai parabolic springs on specific model parabolic leaf spring, which has failed in less than 5000 cycles on fatigue loading. The entire process of manufacturing the spring including the stress shot peening process parameters has been established to have a fatigue life of more than 100, 000 cycles. The product was accepted by one of the major auto OEM.He had took a consulting project with Sterling tools Limited to established the zinc plating process and zinc phosphating process. The existing seven tank process has been reestablished to double the production without any capital investment. Another project taken by him in Sterling tools limited on Rust complaint from overseas customer has been resolved within no time. after going through the application of rust preventive oil on phosphated fasteners. The methodology of the oil application was changed to solve the problem.
Education
Year | Degree | Subject | Institution |
---|---|---|---|
Year: 1998 | Degree: BS Metallurgy | Subject: Metallurgical Engineering | Institution: Indian Institute of Metals |
Year: 2003 | Degree: Diploma - Energy Management | Subject: Energy conservation | Institution: National Productivity Council |
Work History
Years | Employer | Title | Department |
---|---|---|---|
Years: 2006 to Present | Employer: Undisclosed | Title: General Manager | Department: Manufacturing |
Responsibilities:He is responsible for steel foundry operations, supplying to Valve industry, involving Nobake Molding, IMF auto loop, Induction melting, tea kettle pouring, Fettling, Planning, Maintenance etc |
|||
Years | Employer | Title | Department |
Years: 2003 to 2006 | Employer: Sundram Fasteners Limited | Title: D. Manager | Department: Surface treatment Division |
Responsibilities:He is heading surface treatment division having Zinc plating, Zinc Phosphating, Continuous mesh belt furnace heat treatment, carburising, hardening, nitriding, tempering, etc. Also he was responsible for Effluent treatment plant, Energy conservation, Kaizen pillar chairmen in TPM |
|||
Years | Employer | Title | Department |
Years: 2000 to 2003 | Employer: Jai Parabolic Springs Limited | Title: Works Manager | Department: Manufacturing |
Responsibilities:He was heading the works of Manufacturing unit of laminated leaf spring for automobile application, Steel selection and approval as part of steel supplier approval process. The process involved were special purpose hot rolling, hot forming, Parabolic rolling, camber quenching, Autophoretic coating, spray painting and Stress shot peening to improve the parabolic leaf spring's fatigue life. |
|||
Years | Employer | Title | Department |
Years: 1991 to 2000 | Employer: Tata Timken Limited | Title: Manager | Department: Heat Treatment |
Responsibilities:He was responsible for green field project in Erection and commissioning of Heat treatment furnaces. Sealed Quench furnaces, rotary hearth furnaces, rotary retort furnaces, mesh belt hardening furnaces, walking beam furnaces, shaker hearthe furnaces. etc.He was heading the heat treatment division doing Carburising, Carbo Nitriding, Press quenching, Tempering, Soft nitriding, Normalising, stress relieving, annealing, etc. |
|||
Years | Employer | Title | Department |
Years: 1988 to 1991 | Employer: TVS SUZUKI Limited | Title: Foremen | Department: Surface Treatment department |
Responsibilities:He was working as shift incharge for heat treatment plant, copper and zinc plating plant and effluent treatment plant. |
International Experience
Years | Country / Region | Summary |
---|---|---|
Years: to Present | Country / Region: Sri Lanka | Summary: A fastener application failure at the customer end was studied and frequent failure of the fastener arrested. |
Career Accomplishments
Associations / Societies |
---|
Associate Member of the Indian Institute of metals Member of the Madras Metallurgical society |
Licenses / Certifications |
---|
Certified Lead auditor for ISO 14000 Environmental management systems Qualified Energy manager |
Awards / Recognition |
---|
Won the national Kaizen award on TPM |
Publications and Patents Summary |
---|
Presented a paper on “ Friction modifiers in Fastener coating” at National Metallurgist Day held at Indian Institute of Technology in Nov 2004 Presented a paper on “ Nitrogenless atmosphere in case Hardening” at National Metallurgist Day held at Indian Institute of Technology in Nov 2004 Presented a Paper on” Fatigue Behaviour of 50 Cr V 4 springs when subjected to Stress shotpeening” in the ASTM International Surface treatment conference helt at Chennai during Jan2004. Presented another paper on “ Case Hardening – A shop floor managers Perspective” at international conference ASTRA held at Hydrabad in Nov 2003” |
Language Skills
Language | Proficiency |
---|---|
English | |
Hindi | |
Tamil |
Fields of Expertise
blast cleaning, case hardening, heat treatment, plating process, shot peening, plating testing, zinc plating process, quench factor analysis, plant maintenance, heat treatment equipment, anti-corrosive coating material, surface protection, heat treating furnace, continuous heat treatment, maintenance coating material, surface structure, rotary hearth furnace, planing, metal protective coating material, thermal oxidizing agent, acid wash, thermal process, surface property, maintenance engineering, metal pickling, maintenance control, maintenance management training, maintenance scheduling, maintenance planning, maintenance safety, surface modification engineering, plant management, metal-stress relieving, batch heat treatment, peening, nitriding, surface preparation, maintenance, tempering, preventive maintenance, metal finishing process, maintenance management, clean room, austenitizing