Expert Details
Surface Texture and Operational Characteristics of Machines
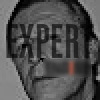
ID: 723015
Ohio, USA
The expert selected tribology as a primary concept because a subset of tribology, mathematical description of the surface texture and contact interaction of rough surfaces was a subject of his Ph.D. dissertation. The expert considers that understanding and utilization of this subject is very important to properly address many engineering factors and procedures including design specifications of machine components, contact stiffness/contact stress analysis, friction, wear, heat transfer and temperature generation, estimation of the minimum required oil film thickness in the sliding and rolling bearings, cost of the machining, noise and vibration of the sliding units, optical properties, resistance to fluid flow, etc. During his professional career, the expert was able to efficiently utilize knowledge of this subject in connection with some of the mentioned engineering areas.
The expert comments that wear typically results in change of micro-and macrogeometrical parameters of the contacting surfaces, modification of their physico/chemical structure and generation of wear debris. Depending on a function of a wearing unit, operational conditions and service time, a beneficial run-in wear may transfer into objectionable wear pronounced in reduction of reliability of the unit and the correspondent mechanism or machine and degradation of their performance. To combat the wear effect, various engineering means exist. These include construction of the unit in such a way as to reduce or prevent wear through selection of certain designs, geometries, materials, coatings, lubricants and operating conditions. Important part in reduction of wear is a proper maintenance. For example infringement on the required oil change intervals of the engine may result in degradation of the motor oil to the level that it cannot prevent separation of the interacting surfaces. As a result, wear of the piston rings, cylinder bore, piston and bearings will ensue. The expert came up with an ingenious wear proof design of a mechanism in scroll compressors (see his patent). In this wear design the difference between both the shear strength of an elastomeric shim and friction force at the interface of two contacting metallic surfaces is successfully employed to eliminate a relative motion of the metallic surfaces (and thus eliminate their wear) and to transfer it in the shear deformations of the elastomeric shim.
The expert knows that one of the purposes of wear modeling is to identify different manifestations of wear with their underlying mechanisms in order to successfully combat, predict or estimate wear. He adds that in a number of occasions wear demonstrates itself through single forms like abrasive, adhesive, corrosive, erosive, and fatigue wear. However, in many actual situations these forms of wear are often intermingled and wear occurs as a complex process. This complicates prediction of wear analytically and advances wear testing to the front of activities related to a proper selection of materials and design for a potential wear reduction. The expert cautions that one should consider also that wear demonstrates large variability and statistical methods are often employed to analyze wear data. One of the unfortunate phenomena of wear is that it has a low rate of reproducibility, that is results of wear studied on small samples may not be represented in the actual machine. Accordingly, full-scale friction/wear tests of a developed mechanism are needed to justify estimation of wear for this mechanism. These tests are often performed as durability tests. For better familiarities with wear prediction one can be referred to the expert’s articles.
The expert mentioned that wear resistant material and coatings are intuitively associated with hard surfaces. He cautions however that this view is in general incorrect. Wear resistance is often achieved by using special coatings having a property of self-lubrication. An example of this type of coatings is a so-called Tuffram produced by Magnaplate Corp. in NJ. The coating represents a layer of hard anodized aluminum infiltrated by self-lubricants like PTFE and MoS2. This coating gives a slippery feel and absence of adhesion between the mating surfaces during the operation. The expert believes that these properties are attained due to presence of large and inert fluorine atoms in the structure of PTFE and transfer of the PTFE from the coating onto the counter surface. Despite its good anti-adhesion/anti-wear properties, coefficient of friction of the assemblies with PTFE coatings is not necessarily small.
The expert has experience in dealing with friction and wears in different machines and mechanisms including components of the IC engines, railroad and automotive brakes and components of the refrigeration and air compressors. He feels that experience accumulated in fighting wear in these products, and his tribological background in general, is in many ways transferable to other big and small industrial products including magnetic media devices, robotics, MEMS, medical devices. He noted that wear is associated not only with materials, but it substantially depends on design properties of the unit or machine as a whole. Depending on a type of a mechanism, reduction or minimization of wear may require completely different approaches. For example, in the non-lubricated units, a relative motion between some wearing components needs to be constricted to prevent their wear. At the same time in the lubricated mechanisms, the related components need to be provided with freedom of motion to ensure good lubrication.
During his employment at WABCO, Copeland and Bendix he often was considered as consultant.
Based on in-depth tribological understanding of the friction squeal, proposed a concept of a low noise friction material which was implemented.Developed precision software for prediction of the braking temperatures in single and multiple braking events in the railroad and automotive brakes.Developed concepts and design of a variety of friction/wear testers for simulation of wear of the components of scroll compressors. He is probably one of the first in the engineering community who understood the effect of three-dimensional distortions of the piston rings on their conformability. Subsequently he spearheaded development of the analytical methods for analysis of the ring distortion/conformability effect and obtained (in collaboration with S. Alexandrov) a computer code for estimation of this effect.Based on understanding of the interaction between the surface texture height of the honed cylinder bore and rigidity/distortion of the cylinder block, proposed design of a clamping fixture of the block that minimized bore distortions.
Education
Year | Degree | Subject | Institution |
---|---|---|---|
Year: 1965 | Degree: MSME | Subject: Mechanical and production engineering | Institution: Riga Technical University, Riga, Latvia |
Year: 1975 | Degree: PhD | Subject: Technology of mechanical engineering | Institution: Riga Technical University, Riga, Latvia |
Work History
Years | Employer | Title | Department |
---|---|---|---|
Years: 1993 to 2005 | Employer: Bendix Commercial Vehicle Systems LLC | Title: Senior Staff Engineer (Dept. manager 2001) | Department: Air Compressors |
Responsibilities:· Oversaw a full range of engineering activities in support for a current compressor production and new development utilizing particularly CAD and CFD tools and compressor testing, for a $200M market.· Led highly professional team on development of the enabling technology represented by novel air brake compressors. - Pioneered development of the AMESim compressor-test rack simulation model. · Based on in-depth understanding of the compressor tribology and interaction with the leading research organizations investigated and implemented activities for improvement of compressor performance. -Was pivotal in resolving various compressor failures and thus prevented potentially multimillion dollar losses. Investigated EGR effects on oil degradation and compressor performance. |
|||
Years | Employer | Title | Department |
Years: 1987 to 1992 | Employer: Copeland Corp | Title: Sr. Staff Engineer-Tribologist | Department: Applied Mechanics |
Responsibilities:· Organized a Tribology lab and was responsible for solving friction, wear and lubrication problems in all reciprocating and scroll compressors thus expediting launch of new products. |
|||
Years | Employer | Title | Department |
Years: 1980 to 1987 | Employer: Westinghouse Air Brakes Co. | Title: Sr. Staff Engineer | Department: Friction materials |
Responsibilities:· Developed and implemented precision mathematical models and software for prediction of the friction temperatures and other performance characteristics of the friction materials in disk and tread brakes that saved to company $1M over 5 years. Developed novel friction material formulations and processes that boosted sale and image of the Co.· Developed and implemented efficient software for evaluation of compressor performance |
|||
Years | Employer | Title | Department |
Years: 1976 to 1979 | Employer: Diesel Locomotive Plant, Riga, Latvia | Title: Design engineer | Department: Stress analysis group |
Responsibilities:Stress analysis of the various components of the diesel locomotivesand cars. |
|||
Years | Employer | Title | Department |
Years: 1977 to 1979 | Employer: Institute for advanced training of engineers, Riga, Latvia | Title: Lecturer | Department: |
Responsibilities:Lecturer in machine design and tribology |
|||
Years | Employer | Title | Department |
Years: 1971 to 1975 | Employer: Riga Technical University, Latvia | Title: Research engineer | Department: Dept. of automatization |
Responsibilities:Tribology and performance studies of a diesel engine, post graduate work |
|||
Years | Employer | Title | Department |
Years: 1969 to 1971 | Employer: Riga Diesel Engine plant, Riga, Latvia | Title: Plant engineer | Department: Production |
Responsibilities:Overseeing operation of production lines for the main powertrain and valvetrain components. |
Government Experience
Years | Agency | Role | Description |
---|---|---|---|
Years: 1980 to 1987 | Agency: Federal Railroad Adm. | Role: Test engineer | Description: As an employee of WABCO he conducted mandatory tests (for FRA) for verification of stop distances of the railroad disk and tread brakes. |
International Experience
Years | Country / Region | Summary |
---|---|---|
Years: 1993 to 1993 | Country / Region: Germany | Summary: He investigated reasons for wear and breakage of the reed valves in the reciprocating refrigeration compressors used by Leybold Pumps Co. in Colon. |
Years: 1967 to 1979 | Country / Region: Latvia | Summary: During his employment in Latvia, before emigration into the USA, he was working as reliability engineer at Dies and Molds plant and Diesel locomotive plant. Also, as an engineer at Riga Diesel Engine Plant he coordinated production of the ValveTrain and DriveTrain components of the diesel engines, was involved in implementation of a diamond honing equipment. |
Career Accomplishments
Associations / Societies |
---|
He is a member of The ASME, STLE, SAE and a member of the ASTM committee on development of the universal tester for piston rings. |
Licenses / Certifications |
---|
He is a certified reliability engineer. |
Professional Appointments |
---|
He was a former secretary of STLE Tribotesting section and Vice Chairman of the Tribotesting II sessions at the 2002 annual STLE convention; Chairman for DriveTrain Lubrication sessions at 2005 STLE convention and paper solicitation chairman for 2006 STLE convention. He is currently Chair of Engine Drive Train Technical Committee. |
Awards / Recognition |
---|
He received awards for presentations at STLE and SAE annual convetions. |
Publications and Patents Summary |
---|
He has over 30 publications, 6 patents and two books (on friction units of machines and accuracy of metal cutting tools) where he was a translation editor. He was instructor in Durface Metrology, Tribology and Six Sigma. |
Additional Experience
Training / Seminars |
---|
Conducted seminars on surafce texture, surface metrology, tribology, machine design, piston rings, bearings. As an active developer of a modern theory of piston rings and their conformability to the distorted cylinders, gave SAE and STLE sponsored presentations on the topic. |
Vendor Selection |
---|
He was often involved in search and location of the most suitable vendors for the various greases and self lubricated components in connection with development of the advanced compressors. |
Marketing Experience |
---|
His precision temperature prediction software was actively utilized in connection with customer requests on properties of the developed friction materials. The low noise friction materials developed under his guide were implemented in production. |
Other Relevant Experience |
---|
Based on understanding of the interrelationships between the parameters of the surface texture, he developed analytical methodology for estimation of a cylinder bore wear based on measurement of worn surface only. This methodology substantially reduces a cycle time for wear measurements. In connection with this and his other developments, has consulted researchers and scientists in various countries. |
Language Skills
Language | Proficiency |
---|---|
Russian | He is fluent in English and Russian which is his native language |
German | He can read with dictionary |
Fields of Expertise
surface science, tribology, wear design, wear effect, wear modeling, wear prevention, wear testing, wear-resistant coating material, material wear, compressor bearing, bearing temperature, anti-seize compound, tool wear, piston wear-resistant coating material, bearing material, bearing application, abrasive blasting, bearing system, metal alloy wear resistance, lubricant coating material, lubricant testing, friction measurement, stainless steel wear, nonmetal bearing, boundary lubricated bearing, engine bearing, bearing wear, bearing noise, acceptable quality level, abrasion testing, metal abrasion, steel bearing, power shaft wear, benchmark, engine wear, seal wear, bearing lubrication, triboluminescence, tire tread wear, metal wear testing, slippery coating material, surface physics, capability study, bearing design, polymer wear, lubrication equipment, grinding (machining), fatigue testing, metal bearing, galling, industrial machine design, bearing life, compressor design, rolling element bearing, machine design review, statistical quality control, industrial machinery, burn-in, surface-fatigue wear, metal-forming friction testing, magnetic media friction, erosion-corrosion, bushing (shaft lining), lubrication process, bearing selection, abrasion-resistant coating material, abrasion, machine design, hardness testing, mechanical test, split bearing, plastic wear-resistant coating material, lubricant, sleeve bearing, plane bearing, lubricant selection, hydrodynamic fluid film bearing, friction, fretting corrosion, durability, corrosive wear, bearing, antifriction bearing, adhesive wear, abrasive wear