Expert Details
Supply Chain Cost Reduction, Contract Services Management, and Batch Process Design, project management
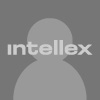
ID: 722800
Texas, USA
He has experience in designing facilities to exclude oxygen from materials that oxidize or decompose in the presence of air or moisture.
He has experience in changing a business process to reduce costs and get results faster.
He worked with both hazardous and corrosive chemicals and the design of facilities to contain them. Chemicals he has worked with includes solvents such as xylene, orthodichlorobenzene, monochlorobenzene, and methanol; as well as others including chlorine, phosgene, acetic acid, sulfur dioxide, anhydrous ammonia, metallic sodium, tetrahydrofuran, caustic soda, methomyl, magnesium, copper chloride, helium, isocyanates, herbicides, fungicides, insecticides, mercaptans, amines, diamines, and carbon monoxide.
Expert participated in several retrofits where he and his colleagues changed the equipment to make completely different chemicals with different hazards and process requirements.
Expert worked on the design, construction, and startup of four different chemical processes that involved toxic, corrosive, and flammable materials. His experience is in both batch and continuous processing.
As sourcing manager, he evaluated contractors versus in-house performance to determine which services to outsource, and then implemented several outsourcing programs with very positive results.
Expert has extensive experience designing batch processes for agricultural chemicals. This includes special attention to the containment of toxic and corrosive materials as well as biologically active chemicals.
In his role as project leader for several batch processes, he designed several processes which had built-in safety systems based on the arrangement of the equipment.
He has worked with site management to develop training programs to help their people deal effectively with new equipment and chemical processes.
He started up four different complex batch processes including operator training as well as final equipment checkout and improvement and change of operations to meet business objectives.
He developed a written safety incident investigation procedure for his company’s plant site. This helped those who were involved to focus on the facts and get to explicit solutions to defined problems.
Expert designed the batch processes for three new products from their chemistry onward. This included definition of additional information needed as well as directing the design efforts of a 20-person team to achieve the business objectives for these new processes. The materials handled included toxic, flammable, corrosive, and biologically active chemicals.
Expert wrote a new procedure to help those investigating incidents to get all the relevant facts and then follow a defined process toward a list of clear conclusions and recommendations which could be accomplished.
Through his project work, he has implemented several sets of safety systems that give multiple layers of protection according to the level of risk for various chemicals. His processes were started up without incident and remain injury free after years of operation.
Expert has implemented chemical safety philosophy compatible with OSHA and the AIChE chemical safety guidelines. This was applied to many chemicals with diverse hazards.
Expert has conducted many incident investigations following the protocol specified by OSHA 1910 and the assessment of cause associated with the 14 points on the hazard "wheel."
He has helped design facilities to make confined space entry easier. This includes isolation of lines with extra valves, allowance of extra access space for such work, and detailed procedures such as a list of blanks, isolation spools, power cuts, etc. necessary before safe entry of a vessel.
He has audited construction contractors for their safety procedures and conducted investigations where they had incidents.
He has participated in several fire investigations to define root cause and develop clear recommendations for future prevention.
Expert has experience designing processes using flammable liquids and combustible solids. The designs included plans to prevent combustible mixtures and also avoid static sparks.
While doing process design work, Expert has defined options to reduce the amount of flammable materials present and prevent explosive/flammable mixtures from existing during operation. As part of the design, he and his colleagues also assessed the need for fire protection systems and how they should be activated.
Expert has designed facilities to handle flammable solvents, corrosive materials such as mineral acids, toxic materials such as chlorine and phosgene, and chemicals with biological effects such as carcinogens.
He implemented a system to handle industrial gases in bulk instead of individual cylinders, which saved money as well as improved process safety.
He has experience designing facilities to handle flammable and toxic solvents and some that are corrosive.
As part of his company’s process design work, he made the designs "friendly" toward lock, tag, and try procedures. This included physical location of isolation valves and instruments as well as allowing suitable access area for maintenance work.
Expert has experience in the design of facilities to handle flammable solvents, wet solids, slurries, and dry solids. This includes odor control as well as dust collection.
Throughout his 30 years of experience with DuPont, he has been involved with all phases of safety from concepts to actual operation.
For him, safety engineering was a part of normal design work. He had to be very creative to develop systems to deal with new issues such as occupational health and containment of biologically active chemicals.
Education
Year | Degree | Subject | Institution |
---|---|---|---|
Year: 1967 | Degree: B.S.Ch.E. | Subject: Chemical Engineering | Institution: University of Massachusetts |
Year: 1969 | Degree: M.S.Ch.E. | Subject: Chemical Engineering | Institution: Pennsylvania State University |
Work History
Years | Employer | Title | Department |
---|---|---|---|
Years: 1998 to Present | Employer: Undisclosed | Title: Consultant | Department: |
Responsibilities:Following his retirement from DuPont in 1998, Expert has published five articles in Chemical Engineering Progress and remains active in the trade doing part-time consulting. |
|||
Years | Employer | Title | Department |
Years: 1966 to 1998 | Employer: DuPont | Title: Sourcing Manager | Department: Agricultural Products |
Responsibilities:Expert worked in chemical process design, lead project execution, lead process development, as a sourcing manager, contracts manager,safety analysis and in service supplier cost reduction. Manager of special projects. |
International Experience
Years | Country / Region | Summary |
---|---|---|
Years: 1980 to 1980 | Country / Region: Puerto Rico | Summary: Expert worked on the startup of a batch granulation process for a new agricultural product. |
Years: 1992 to 1992 | Country / Region: France | Summary: He did a design and estimate for an agricultural chemical process in Cernay, France. |
Career Accomplishments
Licenses / Certifications |
---|
Texas Professional Engineer since 1973 |
Additional Experience
Training / Seminars |
---|
Expert developed a course for training senior citizens on internet usage. |
Vendor Selection |
---|
He has reviewed service supplier credentials for contract work. |
Language Skills
Language | Proficiency |
---|---|
French | Expert can speak and Expert French, and can engage in conversation-level communications. |
Fields of Expertise
accident, air-sensitive material handling, business process re-engineering, contract service management, supply chain cost reduction, chemical handling, chemical manufacturing facility evaluation, chemical plant, outsourcing, chemical plant design, chemical plant layout, chemical plant management, chemical plant start-up, chemical process safety engineering, chemical process design, chemical processing plant accident investigation, chemical processing system safety, chemical safety, chemical safety management, confined space safety, contractor safety, fire investigation, fire prevention, fire risk analysis, hazardous material handling, industrial gas safety, in-plant solvent handling, lock out tag procedure, materials handling, safety, safety engineering, supply chain, contracting, batch process design, emergency management, accident causation, business process management, business strategy, employee protection, contract manufacturing, chemical exposure, chemical plant operation, gas handling safety, injury prevention, enterprise resource planning, environmental safety, electrostatic-discharge safe, process-engineering safety, federal safety regulation, contractor safety management, fall protection, construction safety management, off-the-job safety, excavation safety, construction contract, business re-engineering, solid material handling, Occupational Safety and Health Administration, disaster planning, materials handling equipment, chemical process safety analysis, materials safety data sheet, fault tree analysis, process safety, industrial safety, process safety management, material storage, occupational safety, toxic chemical safety code, fluid handling, explosion safety, explosion investigation, construction safety, accident investigation