Expert Details
Rubber Molding Processes. Flocking and Post Flocking Rubber Processes. Extrusion Rubber Processes
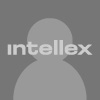
ID: 730802
Spain
Goal:
To design and develop a post-flocking process for the rubber weather-strips.
Achievements: The flocking process was developed. A new Heating machine (Owen) was developed, tested and introduced in mass production. Quality Issues were reduced to meet customer´s targets. Process Transfer to the subsidiary in Morocco was done successfully.
Goals:
To establish of a new “company culture” and the Organization related to support it which will allows the company to compete on the market in ADVANTAGE with regard to the competition.
Plan Steps:
1.-Integration Process (Human Resources) (BUY-IN)
2.-STRATEGY Design and establishment of Operative Goals coordinated between them.
3.-ORGANIZATION Design
Organization Structure.
Design of the Value Chain (Operative Plans).
Design of the Support Chain.
4.-BUY OFF.
Achievements: Supported and drove strategic planning; organization’s corporate goals and objectives were defined, as well as the Industrial Organization needed. Developed a complete Cost Structure following ABC Methodology. Conducted the Chain Value Analysis. Define and implemented the new Industrial Organization.
Goals: To define the chain value and eliminate all the “no added value task”. To define the “ideal” working time to accomplish every task. To simplify the flow of goods around the shop. To determine and implement “the best manufacturing sequence”. To design a new manufacturing process.
Achievements: “Ideal” Working time was determined for each work station following MTM methodology and OIT recommendations. A new inbound logistic was design and implemented, which simplify the flow of goods. A new work sequence was established (2 days leather- 3 days fabrics) which led the company to balance the final packaging line and increase the real working time. The lead time was reduced to less than 5 days for Leather sofas, and 3 days for fabric ones.
Goals:
To determine the real manufacturing time for each work station (on-line) and out-line (pre-assembly).
To design and implement a new inbound logistic.
Achievements:
• Work time was determined for each work station (in-line) and the pre-assembly work-shops (out-line), following MTM methodology and OIT recommendations.
• A new inbound logistic was design and implemented.
• All the assembly lines were balanced.( Task re-distribution for work stations)
• The real working time increases from 5 hours, to, 7,5 hours.
• The Out-put increases from 12 minutes/ unit, to 8-9 minutes/unit, depending on motorcycles models.
Education
Year | Degree | Subject | Institution |
---|---|---|---|
Year: 1990 | Degree: Aeronautical Engineer | Subject: Special Materials | Institution: Universidad Politécnica de Madrid. EUITA. |
Work History
Years | Employer | Title | Department |
---|---|---|---|
Years: 2011 to 2012 | Employer: Undisclosed | Title: INDUSTRIAL CONSULTANT | Department: Undisclosed |
Responsibilities:Goal:To design and develop a post-flocking process for the rubber weather-strips. Achievements: The flocking process was developed. A new Heating machine (Owen) was developed, tested and introduced in mass production. Quality Issues were reduced to meet customer´s targets. Process Transfer to the subsidiary in Morocco was done successfully. |
|||
Years | Employer | Title | Department |
Years: 2006 to 2011 | Employer: Undisclosed | Title: INDUSTRIAL CONSULTANT | Department: Undisclosed |
Responsibilities:He has established new processes, which reduced costs, enhanced efficiency, improved production methods and simplified equipment. |
|||
Years | Employer | Title | Department |
Years: 2003 to 2006 | Employer: Undisclosed | Title: PRINCIPAL CONSULTANT-RUBBER | Department: Undisclosed |
Responsibilities:He has established new processes, which reduced costs, enhanced efficiency, improved production methods and simplified equipment. |
|||
Years | Employer | Title | Department |
Years: 2002 to 2003 | Employer: Undisclosed | Title: DEPUTY GENERAL MANAGER | Department: Undisclosed |
Responsibilities:To manage the set of the Industrial Activity and introduce new technologies of Manufacturing processes. To develop and implement best practices and major improvements to processes (Re –engineering). To develop and manage an effective plant-wide communication process in order to assure alignment between activities in the shop-floor and business objectives. To provide coaching and training for all manufacturing supervisors. To Plan and Control of the Production, Follow-up, analysis and improvement of the Coefficient of Filling. |
|||
Years | Employer | Title | Department |
Years: 2001 to 2002 | Employer: Undisclosed | Title: PLANT MANAGER | Department: Undisclosed |
Responsibilities:To develop and implement best-practice ways of working (LEAN MANUFACTURING). |
|||
Years | Employer | Title | Department |
Years: 1999 to 2001 | Employer: Undisclosed | Title: TECHNICAL MANAGER/LEAD ENGINEER | Department: Undisclosed |
Responsibilities:To design and develop a weather strips systems according to customer specifications. |
|||
Years | Employer | Title | Department |
Years: 1993 to 1999 | Employer: Undisclosed | Title: MANUFACTURING ENGINEER | Department: Undisclosed |
Responsibilities:Design for Manufacturing (DFM).Processes Improvement. Project Management Clients Technical Assitance |
Language Skills
Language | Proficiency |
---|---|
SPANISH | |
FRENCH | |
PORTUGUESE |