Expert Details
Refractories and Ceramics: Raw Materials, Manufacturing and Applications
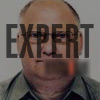
ID: 724099
United Kingdom
He is also well experienced in the development and production of the whole range of silicon carbide kiln furniture (clay, oxide, silicon nitride and sialon bonded) for both fine ceramics and for technical ceramics. He has developed mullite and high alumina kiln furniture for white ware technical ceramics.
During the last two years, he has developed an advanced, dense, high strength, oxidation resistant, thin sectioned silicon nitride/sialon bonded kiln furniture product for fast firing of porcelain and bone china, technical ceramics and other engineering applications. This product is made by either slip casting, particularly for beams, or by pressure casting, which is mainly used to make flat ware.
He has other areas of expertise including porcelain, bone china and sanitaryware production. He has given technical assistance to companies in UK and Indonesia to improve their quality and yield. This has included a full examination of raw materials, froming and glazing techniques, as well as drying and firing cycles and schedules. In collaboration with Norton Refractories, technical assistance was given to a major worldwide sanitaryware manufacturer at the UK plant to improve the firing cycles by using low mass kiln furniture and hollow beams to replace the standard cordierite-mullite kiln furniture.
He is mainly concerned with advanced sialon bonded silicon carbide for kiln furniture. In the past, a considerable amount of work was done with cordierite slips for spray drying and pressing for specialised kiln furniture applications. Also work on slips for casting and spray drying of bone china and porcelain for isostatic pressing to modernise the production of these products. He has also introduced pressure casting techniques to a sanitaryware manufacturer in Indonesia to increase the productivity and general quality.
He has spent the last twenty years working on the development, production and quality control of silicon carbide product, mainly silicon nitride bonded silicon carbide for a wide range of applications, including kiln furniture, non-ferrous metals, blast furnace linings, acid domes, cyclones and wear resistance application, thermocouple sheaths, incinerator linings and firing of technical ceramics. This work has include the development of various manufacturing techniques, including pressing, vibration casting and extrusion. He has also developed slip casting and pressure casting techniques for the manufacture of advanced sialon bonded silicon carbide products for kiln furniture, engineering and wear resistance applications. This product has a thin section, high density, very high strength, excellent thermal shock resistance, high wear resistance and excellent thermal shock resistance. Apart from being used in porcelain and bone china manufacture for fast firing and automatic loading and unloading of kilns, it is used for firing sanitaryware and technical ceramics, wear resiatant applications, such as cyclones, and other engineering applications.
For the past eight years, He has spent a considerable amount of time working on monolithic products, including the development of a wide range of dense castables and ramming mixes. However, the main development work has been spent on new dry ramming products, as well as the improvement of existing products for induction furnace linings for melting both ferrous and non-ferrous metals and alloys. These developments have been based on a wide range of raw materials from alumino-silicates, such as andalusite and chamottes, to high purity fused and sintered raw materials such as white and brown fused aluminas, mullite and zircon.
He was involved with the production of refractory brick products, in general, including mid and high alumina, mullite, zircon and zirconia. In addition, he spent time working to develop and investigate refractory special shapes manufactured by ethyl silicate casting technique was examined for refractories used in the glass and steel industries. He has also had some experience of developing dense refractory products by spray drying and isostatic pressing.
Expert has over 36 years experience of building and operating various types of kilns. This has encompassed tunnel kilns, intermittent kilns and controlled atmosphere kilns, using a variety of fuels – gas, electricity and oil.
His experience has also covered a range of industries and can probably be best summed up according to industry.
Sanitaryware:
The majority of the time has been spent working with tunnel kilns for the production of sanitaryware, although some involvement with intermittent kilns for re-firing to correct glaze faults. This work has been done for major companies in UK, namely Ideal Standard, who are part of the World Standard Group and Doulton Sanitaryware, and at PT Inax International Corporation Indonesia. PT Inax is a large family owned business set up originally by the Japanese, Ina Sanitaryware.
In all cases, his role was to optimise the kiln cycle and atmosphere to ensure a maximum output and product yield. In UK, Ideal Standard and Doulton Sanitaryware operated different systems, the former being open flame tunnel kilns and the latter muffled tunnel kilns. This meant completely different firing cycles were required because the heat transfer in a muffle kiln is by radiation only, affecting the gas circulation.
At PT Inax, the major objective was to increase the yield of first quality products, which was initially 40%. This was found to be due to raw materials, amount of recycled product added and the kiln firing cycle and setting of sanitaryware on the kiln cars, i.e. the setting densities were too high.
Sanitaryware is produced in a single firing operation, viz the glaze is applied to the dried green ware and during the firing cycle the body densifies and the glaze is cured. The major changes that have occurred in the production of sanitaryware over the last few years are related to the amount of kiln furniture required. There has been a move towards low mass kiln furniture to increase the product yield and the efficiency of the kiln. This involved a change to the firing cycle and also to ensure that the kiln atmosphere was retained.
Porcelain and Bone China:
Porcelain and bone china are fired in several stages. In the first stage, the green body is fired to produce a piece which is hard enough to be handled but not necessarily dense, known as the biscuit firing. Glaze is then applied to the piece, which is then fired for a second time to densify the body and cure the glaze. Further firings are then required as decoration is applied. This is necessary because different colours are cured at different temperatures.
Biscuit firing for both porcelain and bone china are in oxidising conditions, although the firing temperatures are different. During the glaze firing for porcelain, the atmosphere varies, being oxidising up to about 900oC and is then reducing between 900oC and 1100oC (CO content = 2 – 4%). This is to produce a blue-white colouration. Above this temperature and up to 1450oC, the atmosphere is oxidising. During the glaze firing for bone china, the atmosphere is oxidising throughout the cycle.
Whilst working in Indonesia, Expert was responsible for adjusting and monitoring the firing cycles and kiln atmospheres of both tunnel kilns intermittent kilns for firing porcelain ware. The main problems relating to both the biscuit firing and glaze firing were too high a density of products on the kiln cars and lack of atmosphere control. The glaze firing was particularly bad during the reduction part of the cycle, which was very poorly controlled, ranging from being too low affecting the colour to too high resulting in carbon deposition in the glaze. This proved to be a difficult problem because of the lack of proper instrumentation.
Expert has been involved with the design and construction of both gas fired and elctrically fired controlled atmosphere kilns. He has also been involved with development and implementation of firing cycles of these kilns because this is an important part of the manufacturing process.
For silicon nitride, silicon oxynitride and sialon bonded silicon carbide products; he has designed, built and operated nitrogen/argon controlled atmosphere kilns. These electrically fired kilns have had to have more sophisticated controls because of the exothermic nature of the reaction and because the heat is applied directly to the product, unlike a gas fired controlled atmosphere kiln. The kilns were designed so that, if the rate of temperature increase exceeded that of the set point (ie the exothermic reaction started to generate its own heat in the kiln), nitrogen being injected into the kiln chamber was switched off and replaced by argon stopping the reaction. When the temperature had fallen below that of the set point, the nitrogen flow was restored. Thus the rate of reaction was controlled at all times.
Specialist Induction Refractories Ltd - developed a range of dry vibratory ramming products, as well as other monolithic products, castables, rammable, washcoatings etcCUMI, India - initial benchmarking exercise followed by improvements to the manufacturing processes, product improvements and new product developments. The products included the full range of silicon carbide refactories, high alumina and mullite pressed refractories, as well as some insulation brick.Dyson Ceramic Products - rationalisation of the range of cordierite kiln furniture to reduce the number of batch compositions and raw materials and to develop a new light weight cordierite kiln furniture. Generally, improve production techniques to reduce waste and fired losses.Lianyugang Yun Chan Special Refractories Plant, China - supply of technology, installation and commissioning of the plant, after sourcing equipment, training of personnel and setting up QC and production/process controls to manufacture silicon nitride bonded silicon carbide products.Personal - Development and patenting of a range of high strength, thin sectioned sialon bonded silicon carbide product for fast fire kiln furniture and protective body armour using pressure casting techniques.
Education
Year | Degree | Subject | Institution |
---|---|---|---|
Year: 1966 | Degree: BSc | Subject: Applied Chemistry | Institution: Huddersfield University |
Year: 1970 | Degree: PhD | Subject: Solid State Chemistry | Institution: Huddersfield University |
Work History
Years | Employer | Title | Department |
---|---|---|---|
Years: 1993 to Present | Employer: Undisclosed | Title: Technical Consultant | Department: Self Employed |
Responsibilities:Offering technology, know-how, plant design and training for the manufacture of refractory and ceramic products. Technical advise on raw materials, equipment, product and process improvement, new product development, feasibility studies, market surveys and litigation. |
|||
Years | Employer | Title | Department |
Years: 1991 to 1993 | Employer: Zirceram Ltd | Title: Technical Manager | Department: Technical |
Responsibilities:Responsible for the development of high alumina and zircon grinding media. Plant design, installation and commisioning for the production of grinding media, using spray drying and isostatic and hydraulic techniques. QC and production control of existing production of zircon powders. |
|||
Years | Employer | Title | Department |
Years: 1989 to 1991 | Employer: Refractory Mouldings and Castings Ltd | Title: Technical Sales Manager | Department: Sales |
Responsibilities:Resonsible for maintaining sales of cast and isostatically pressed crucibles and other ethyl silicate cast items for the metal and glass industries. To develop new markets. |
|||
Years | Employer | Title | Department |
Years: 1985 to 1989 | Employer: Carborundum Resistant Materials | Title: Technical Manager | Department: Technical |
Responsibilities:Responsible for all European Technical Services, production, QC/QA, customer technical services for the manufacture of silicon carbide, high alumina, mullite and zirconia refractories for steel, non-ferrous, glass, ceramic and power generation industries. New product development and process improvements. |
|||
Years | Employer | Title | Department |
Years: 1975 to 1985 | Employer: Dyson Refractories Ltd | Title: Senior Products Manager | Department: R & D Laboratories |
Responsibilities:Development of new products - silicon carbide, silicon nitride, alumina and zirconia for refractory and ceramic applications. Product and process inprovements to cordierite kiln furniture, ethyl silicate cast products and high alumina products. |
|||
Years | Employer | Title | Department |
Years: 1973 to 1975 | Employer: Sheffield University | Title: Post Doctoral Research Fellow | Department: Ceramics, Glass and Polymers |
Responsibilities:Investigation of kinetics and mechanism of ferrite formation. Supervision of tutorials |
|||
Years | Employer | Title | Department |
Years: 1970 to 1973 | Employer: Barnsley Technical College | Title: Lecturer | Department: Chemistry |
Responsibilities:Lecturer in inorganic chemistry |
International Experience
Years | Country / Region | Summary |
---|---|---|
Years: 1994 to 1994 | Country / Region: Germany | Summary: Review of production techniques and practices to improve efficiency of production. Followed by implementation and practice. |
Years: 1996 to 1999 | Country / Region: China | Summary: Supply of technology, sourcing of raw materials and equipment, plant construction and commissioning and training of personnel for a silicon nitride bonded silicon carbide plant. |
Years: 1994 to 1996 | Country / Region: Indonesia | Summary: General product and process improvements and controls for the manufacture of stoneware, porcelain and sanitaryware products, as well as the introduction of new production techniques - spray drying, isostatic pressing and pressure casting of the various products. |
Years: 1997 to 1998 | Country / Region: Malaysia | Summary: General improvements to the quality of decorative garden pots and a quality improvement to increase the frost resistance. |
Years: 2004 to 2005 | Country / Region: Thailand | Summary: Two benchmarking project - one at a refractory plant and the second at a house brick plant. the objective was to improve the general practices at the plants and introduce new production techniques currently used worldwide, also to recommend product improvements where applicable. |
Career Accomplishments
Associations / Societies |
---|
CChem, MRSC, MInstRE |
Licenses / Certifications |
---|
Internal Auditing Certificate for ISO 9000. |
Publications and Patents Summary |
---|
He has 6 publications and 2 patents. |
Additional Experience
Expert Witness Experience |
---|
He investigated premature failure of a lining in an induction furnace. The result was an agreed settlement out of court. He has investigated the failure and cause of explosion of a zinc distillation column and made recommendation to try to prevent this happening in the future. |
Training / Seminars |
---|
Various papers, including 1st and 2nd International Simposiums on Refractories in China. Paper on silicon carbide refractories to RABG. Training course on Internal Quality Auditing. Organised and delivered a training session on Domestic Waste Incineration and the Refractories Used for a Korean Company. |
Vendor Selection |
---|
He has supplied technical expertise in several countries and been involved with sourcing, testing and approval of raw materials worldwide, in general, and locally in particular. He has also specified and sourced production equipment for the plants. |
Marketing Experience |
---|
Currently involved with developing a new type of body armour to UK MOD, which involves standard production of sialon bonded silicon carbide by slip casting and a new production technique - Spark Plasma Sintering (SPS). This new technique of SPS produces a fully dense product equivalent to boron carbide at a lower temperature and pressure, i.e. at a lower cost. Development and installation of a plant to manufacture slip cast sialon bonded silicon carbide kiln furniture for fast firing of porcelain and bone china. |
Other Relevant Experience |
---|
He has worked worldwide supplying technology, improving products and services, sourcing raw materials and equipment, benchmarking, training personnel, and commissioning plants. Countries include China, Malaysia, Indonesia, India, as well as Euopean and North American countries. |
Fields of Expertise
ceramic kiln furniture, ceramic slip casting, high-temperature non-oxide ceramic material, monolithic refractory, refractory, kiln, electric kiln, brazed carbide, borax, furnace refractory system, monolithic ceramic, ceramic joining, advanced ceramic material, ceramic component manufacturing, brown alumina, white alumina, fused aluminum oxide, ceramic binder, ceramic mechanical property, ceramic physical property, ceramic extrusion, technical ceramic, mullite, alumina substrate, ceramic drying technology, ceramic slip production, ASTM standard refractory test, synthetic cordierite, refractory metal brazing, ceramic powder, ceramic material manufacturing, ceramics drying, ceramic powder characterization technology, ceramic fracture strength, ceramic particle suspension, ceramic creep, ceramic material selection, ceramic technology, refractory testing, refractory compound, zirconium oxide, ceramic material, refractory nondestructive testing, refractory mechanical property, refractory thermal property, ceramic corrosion, ceramic packaging process, plastic material, heat-resistant material, refractory ceramic, refractory concrete, ceramic sintering, ceramic processing, ceramic powder processing, ceramic forming, castable refractory, andalusite