Expert Details
Product Development and Injection Molding/Part Design and DfM on LSR and 2K Parts
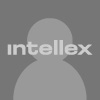
ID: 736653
Switzerland
He demonstrates a high technical understanding of the injection molding process of LSR and 2K (2-shot/2-component) and the surrounding and supporting manufacturing equipment including their raw materials.
Expert can provide Consulting and Support on the following topics (and more if necessary):
• Helping to understand customers on LSR and 2K (2-shot/2-component) part design/development
• Implementing DfM (Design for Manufacturability ) for LSR and 2K (2-shot/2-component) parts to have reduced cost, improved quality, and simplified molding.
• Support on tooling & process layouts and/or concepts
• Identifying novel technologies and equipment for the LSR and 2K (2-shot/2-component) manufacturing process including automation, tooling, and process controls for new project related developments
• Evaluating tool designs for improved part design / supporting clients on tool reviews
Education
Year | Degree | Subject | Institution |
---|---|---|---|
Year: 2002 | Degree: Skills Certificate | Subject: Plastic Technologist | Institution: BWZ Rapperswil Switzerland |
Work History
Years | Employer | Title | Department |
---|---|---|---|
Years: 2018 to Present | Employer: Undisclosed | Title: Engineering Manager | Department: |
Responsibilities:• Coordinate, manage and lead the Project Engineering team to ensure optimum engineering of new projects to meet customer and manufacturing requirements.• Personnel responsible of the Project Engineering department • Support Product Management & Sales on project acquisition in regards of technical strategies. • Assist the internal tooling department in external toolmaker selection and management • Development, execution and management of strategies in processing, tooling, automation, etc. for future and current projects. • Identify novel technologies and equipment for the LSR and 2K (2-shot/2-component) manufacturing process including automation, tooling and process controls for new project related developments • Interfaces with the supplier base on technical maters. • Effectively communicate across teams (Operations and Productions) the project goals and objectives to align expectations both within the company and with the customer. • Act as the lead technical interface for customer and within the organization. • Provide technical training on LSR and 2K (2-shot/2-component) technology to the customer and internal within the organization. |
|||
Years | Employer | Title | Department |
Years: 2012 to 2018 | Employer: Undisclosed | Title: Project Manager / Project Engineer | Department: |
Responsibilities:• Coordinate, manage and lead LSR and 2K (2-shot/2-component) projects from quoting to project development in to industrial phase• Support Product Management & Sales on project acquisition in regards of technical strategies. • Interfaces with the supplier base on technical maters. • Effectively communicate across teams (Operations and Productions) the project goals and objectives to align expectations both within the company and with the customer. • Act as the technical interface for customer and within the organization. |
|||
Years | Employer | Title | Department |
Years: 2004 to 2012 | Employer: Undisclosed (LSR Molder in Canada) | Title: Project Manager (technical) & Technical Integration Manager | Department: |
Responsibilities:• Key influence in manufacturing for technical trouble shooting assistance• Technical support for manufacturing • Develop and/or assist to develop innovative solutions for productivity enhancement within the manufacturing department • Develop new mold processes • Involved in daily Production process & tooling issue investigation and correction • Troubleshoot and solve problems on molds, molding machines, LSR delivery systems, robotics and automation efficiently • Contact customers, deal with related issues for on-going Projects • Main interface to core suppliers like tool maker, machine supplier, etc. • Developed several processes in a customer oriented and efficient matter, including automation and robotics • Key person for the 2 component (Silicone-Plastic/Silicone-Silicone) projects technical and managerial • Maintaining production processes for their best performance • Reducing scrap and improving production by implementation in process vision systems • Cycle time reductions by improving process, tooling and automation • Continues improvements for several manufacturing processes |
|||
Years | Employer | Title | Department |
Years: 2002 to 2004 | Employer: Undisclosed (Plastic injection molder in Switzerland) | Title: Plastic Technologist | Department: |
Responsibilities:• Development of new processes, molds and equipment• Material testing for process development and internal lab • Manufacturing of testing bars for lab (Tensile bar, shore pads, etc.) • Training of new apprentice (theoretical and practical) |
International Experience
Years | Country / Region | Summary |
---|---|---|
Years: 1998 to 2004 | Country / Region: Switzerland | Summary: Development of new processes, molds and equipment / material testing for process development and internal lab. |
Years: 2004 to 2012 | Country / Region: Canada | Summary: Supporting the start up of an LSR Manufacturing & technical lead for process and project development on the production floor. |
Years: 2012 to Present | Country / Region: Switzerland | Summary: Project Development for new LSR and 2-shot/2K programs including customer support on DfM to improve cost and quality of LSR and 2K/2-shot parts. |
Additional Experience
Training / Seminars |
---|
Guest-Speaker at the following Seminars Symposiums: 201x: VDI Symposium Germany 201x: LSR Symposium Anaheim CA 201x: Pharmapack 202x: Healthcare Elastomers Virtual Edition Also several 'Company-internal' presentations on LSR, 2-shot, and Engineering specific subjects. |
Vendor Selection |
---|
Based on client and project requirements, Expert has successfully solicited for selected vendors for raw materials, equipment, auxiliary equipment, tooling and machining services, and automation software. IMM Equipment: Arburg, Engel, Krauss Maffei, Demag, Sodick LIM Dosing Equipment: 2KM, DOPAG, Nexus, ELMET Mold: misc. employee self-developed tooling systems, ELMET, Roembke Mfg. & Design Raw Material: Wacker, Momentive, ShinEtsu Silicones, Dow Corning, Bluestar |
Language Skills
Language | Proficiency |
---|---|
German | Native Language |
English | 2nd Native Language |
Fields of Expertise
liquid silicone rubber, liquid injection molding, liquid silicone rubber injection molding, co-injection molding, injection mold, injection mold design, injection molding, runnerless injection molding, thermoplastics injection molding secondary operation, medical injection process, design for manufacturability, elastomer process development