Expert Details
Process Improvement, Virtual Process Validation, and Discrete Event Simulation
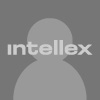
ID: 735231
Brazil
Additionally, Expert provides support to plants to identify and resolve top bottlenecks implementing methodologies for processes monitoring and plant management.
With significant expertise in discrete event simulation, Expert has a strong capacity to support partners through the creation of models with a very high level of representatives to validate processes even before its implementation, which makes the process concept meets the expected manufacturing targets.
Education
Year | Degree | Subject | Institution |
---|---|---|---|
Year: 2012 | Degree: MBA | Subject: Business Management | Institution: UNIP - Universidade Paulista |
Year: 2005 | Degree: Technical | Subject: Advanced Fluid Power Seals | Institution: SKF |
Year: 2000 | Degree: BS | Subject: Mechanical Engineering | Institution: UMC - Mogi das Cruzes University |
Year: 1993 | Degree: Technical | Subject: Tool Maker - Stamping Tools | Institution: SENAI |
Work History
Years | Employer | Title | Department |
---|---|---|---|
Years: 2008 to Present | Employer: Undisclosed | Title: Manufacturing Engineer | Department: Industrial Engineering |
Responsibilities:• Development of capacity studies for future programs/processes through Throughput Simulation with simtalk (Siemens / Tecnomatix Plant Simulation) including BodyShop, GA, PaintShop, Polymers, LMS and others;• Proficiency on development of very representative / realistic models in 2D and 3D; • Data science and analysis - strong analytical skill, use of production statistics from automatic data collection systems (GPMC / Webtip) to identify bottlenecks and pursue processes with best performance. • Strong ability of monitoring complex manufacturing systems, cycle time measurement, measure impact of acyclic operations (tool change, tip dressing, operator rack handling, etc), calculate minimum quantity of carriers in a closed loop, calculate total of in process inside buffers line balancing, etc… • Application of Lean Manufacturing principles for new and current processes focusing in seven wastes elimination; • Familiarity with PLC programming, HMI throughput template, GPMC screens and throughput terminologies; • South America plant support to identify and improve bottlenecks and boost production capacity in plant floor; • Launch support (consulting approach) for throughput improvement during rump up at South America Plants • Regional Focal point South America representative with active participation in the global council responsible to define methods and standards and disseminate the concept of plant simulation engineering at our region. • Leverage activities of work sharing between GM South America / North America and Asia. • Proficiency in Excel / PowerBI and Java |
|||
Years | Employer | Title | Department |
Years: 2004 to 2008 | Employer: (Undisclosed) | Title: Manufacturing Manager | Department: Operations |
Responsibilities:• Management of industrial processes including production planning, injection machines, rubber machines, PTFE, machining, stamping, finishing and tool shop;• Application of Lean Manufacturing concepts to improve lead time, waste reduction and quality improvement by reducing WIP, process simplification, production on demand, definition of inventory policy, production per batch… • Decrease of delay of production in 80% by implementing the creation of production orders through FIFO; • Development of new products, Hydraulic and Pneumatic Sealing for industrial equipment (Wiper, Gasket, O’ring, piston guide, etc; • Project and development of injection mold for thermoplastic, mold for rubber presses and stamping tool; • Support after Sales regarding the application of the product, suggesting improvement in the customer´s equipment to guarantee the best performance of the sealing and choosing the best seal (material and design) for each specific application • Management and publishing of the production metrics (monthly quantity produced per process “rubber, plastic, PTFE and hybrid metal/rubber and metal/plastic”, percentage of non-conform parts, total of parts produced per month and delivery delay; • Contact with headquarter engineers (USA – SLC) to bring new process technologies and support with product application to provide best solution to our customers; • Participation of the implementation of the production management system module integrated with other areas. |
|||
Years | Employer | Title | Department |
Years: 2003 to 2004 | Employer: Impol Implantes Ortopedicos | Title: Mechanical Engineer | Department: Product and Process Development |
Responsibilities:• Tool Shop Supervision;• Development of new products (orthopedic implants and surgical instruments); • Responsible for creation and implementation of all technical specification (product design, process sheets, inspection sheets, packing specification and product labeling); • Outsourcing of machining services; • Development of prototypes through NBR and ISO standards; • Project of tooling (stamping, cut, fold and drilling, cold forge, fixtures and gauges (NBR6404)); • Process Continue Improvement (machining, stamping, cold forge, finishing, lost wax casting). |
|||
Years | Employer | Title | Department |
Years: 2001 to 2002 | Employer: Usina Açucareira Corona | Title: Mechanical Engineer | Department: Operations |
Responsibilities:• Project and development of machines and equipment (hydraulic, pneumatic e electro-mechanic) and machine components (AUTO-CAD)• Monitoring of building, set up, installation and start-up of the machines and equipment in the plant floor • Planning and supervision of maintenance services (preventive, corrective and predictive) • Monitoring the maintenance of equipment on the supplier´s site; • Development of new suppliers for maintenance services; • Supervision of sugar cane juice extraction process. |
|||
Years | Employer | Title | Department |
Years: 1991 to 1999 | Employer: Keiper Recaro | Title: Tool Maker | Department: Tool Shop |
Responsibilities:Building, maintenance, adjustment and try-out of stamping tools (simple and progressive);• Building and maintenance of different types of fixtures (welding, folding, drilling, etc.) • Machines operation such as conventional and CNC milling and lathes, cylindrical and flat grinding, electrical-erosion, machining centers, and others; • Ability in CNC machines programming (milling and lathes); • Ability of manipulating different types of measurement instruments • Participating in the implantation of the quality system ISO 9002 / QS 9000 • Application of tools and methodologies for process improvement (PDCA, Kaizen, Just in Time, FIFO, MSA, FMEA, SPC). |
International Experience
Years | Country / Region | Summary |
---|---|---|
Years: 2013 to 2013 | Country / Region: Argentina | Summary: Coordination of the construction of a prototype body structure at General Motors facility that would be submitted to crash test to attend local legislation. |
Years: 2005 to 2005 | Country / Region: United States | Summary: Workshop and trainning at SKF seals division about power fluid seals development. |
Additional Experience
Expert Witness Experience |
---|
Witness inspection support for aerospace segment, a vendor in Brazil (Tracker) was requested from an American company (Ducommun) to construct 15 Inspection fixtures that were going to be used to validate the construction of the airplane flaps. The support provided was to certify the fixtures were being constructed within the schedule, validate critical dimensions of sub-assemblies and final assemblies, guarantee the use of correct measurement methods and that the instruments used for measurement were certified. The biggest challenge was to guarantee the stability of the fixtures that were too big (more than 3 meters length) in a facility with a variation of more than 20C along the day, with very tight tolerances it would be impossible to validate it due to fixture dilatation. To resolve it the vendor constructed a climate room with controlled temperature which guaranteed the stability of the fixtures making possible the validation of them. |
Language Skills
Language | Proficiency |
---|---|
Portuguese | Fluent |
English | Advanced |