Expert Details
Polymer/Photolithography Process Engineer
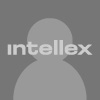
ID: 735661
California, USA
• Expertise in polymer processing including selection, evaluation and implementation into specific devices. (MEMS, Thin Film Heads, Display, Biochip)
• Hands-on experience in preparation of various polymer types. (polyimides, novolak, acrylates, styrenes)
• Worked with various photo imaging, polymer coating wet bench and clean tooling.
• Trained as synthetic organic and polymer chemist.
• Characterized and developed unique adhesion promoting systems for polymers unto metal
AREAS OF EXPERTISE
• Worked with various polymer companies (DELO, Panacol, TOK, Fuji-Film, DOW, Promerus)
• Experienced in surface analysis/characterization: XPS, EDS, FT-IR, TOF-MS
• Processed photo-definable and thermally stable polymers (BCB & Parylene)
• Familiar with various coating systems: spin, slot-die, spray
• Wrote SOP’s including training at technician level
• Experienced with JMP performingDOE & ANOVA analysis, SPC charts
• Familar with polymer chacterization: TGA, DSC, DMA GPC. • Created FEMA for litho, wet etch and cleans modules
Education
Year | Degree | Subject | Institution |
---|---|---|---|
Year: 1985 | Degree: PhD | Subject: Chemistry | Institution: University of California, Irvine |
Year: 1977 | Degree: MA | Subject: Chemistry | Institution: California State University, Fullerton |
Year: 1975 | Degree: BA | Subject: Chemistry | Institution: California State University, Fullerton |
Work History
Years | Employer | Title | Department |
---|---|---|---|
Years: 2014 to 2019 | Employer: Apple Inc | Title: Technical Lead | Department: Hardware Development |
Responsibilities:Purchased, evaluated and qualified tools for lithography module (including photo tracks, exposure systems, metrology)• Evaluated and selected polymeric materials for processing MEMs and LED devices. • Qualified 8 inch wafer plating tool for MEMs process flow. • Determined root cause for chemical contamination within key process steps in MEMs sensor. (source from clean chemicals interaction with wafer bonding polymers) • Screened adhesive epoxy polymers for die attachment and improved die cleaning yield. |
|||
Years | Employer | Title | Department |
Years: 2012 to 2014 | Employer: Soraa Inc | Title: Member of Technical Staff | Department: Process Manufacturing |
Responsibilities:Maintained lithography module (Stepper and photo track) for photo layers.• Worked with EPI team to create specification for hole defects for incoming GaN wafers. (IQA) • Developed metal lift-off process using a high temperature negative photoresist. |
|||
Years | Employer | Title | Department |
Years: 2011 to 2012 | Employer: Rolith Inc | Title: Sr Process Engineer | Department: NA |
Responsibilities:Co-developed a nano-imprint tool (RTR) with Suss Microtech to pattern and etch into quartz substrate creating nano-features for anti-reflective properties.• Processed photo-definable materials including RIE etch of quartz substrates. |
|||
Years | Employer | Title | Department |
Years: 2009 to 2011 | Employer: Pacific Biosciences | Title: Staff Process Engineer | Department: Development |
Responsibilities:Partnered with Operations and development in scaling a surface activation process unto quartz wafers into manufacturing.• Ownership of surface active process module including automated wet-bench, ultrasonic tool, bake oven and plasma ash system. |
|||
Years | Employer | Title | Department |
Years: 2009 to 2008 | Employer: Infinera | Title: Sr Process Engineer | Department: Manufacturing |
Responsibilities:Responsible for both tools and processes for dielectric and InP etch steps• Maintained all SPC charts for etch tools including updated SOPs. • Supported photo module through characterization of BCB polymer thermal cure (%) using FTIR analysis |
|||
Years | Employer | Title | Department |
Years: 2004 to 2008 | Employer: Cypress Semiconductor (SVTC Foundry) | Title: Sr Process Engineer | Department: Development |
Responsibilities:Purchased and qualified 193 nm photo track including layer ownership of contact hole layer (90 nm node)• Maintained SPC charts for track and photo layer including SOP’s and training of Manufacturing technicians, • Project managed key accounts after Cypress converted to SVTC, a contract foundry service. |
|||
Years | Employer | Title | Department |
Years: 2003 to 2004 | Employer: Innovative Micro Technology (IMT) | Title: Sr Process Engineer | Department: Manufacturing (Foundry) |
Responsibilities:Evaluated ultra-thick photoresist (80-100 um) as trench fill polymeric material for fabrication of accelerometer device. |
|||
Years | Employer | Title | Department |
Years: 1986 to 2002 | Employer: IBM Corp | Title: Sr. Photo Process Engineer | Department: Development and Manufacturing |
Responsibilities:Evaluated thermally stable polymers for use as insulation material within a thin film magnetic head device (MR and GMR design)• Developed a dye-containing polymer (PMGI) for improved adhesion to magnetic metal surfaces for metal lift-off process. • Developed and scaled-up a polymer based adhesion promoting system for use with photoresists during electroplating of copper coils. |
Career Accomplishments
Publications and Patents Summary |
---|
Filed number of patents pertaining to metal liftoff processes, thermally stable polymer in the thin film head device, novel adhesion promoter systems for resist adhesion to metal surfaces during electroplating. Also use of top surface imaging for generating nano-features with a roll-to-roll tool for nanoimprint lithography. polymer materials for use in laser liftoff process with sapphire wafer. |
Additional Experience
Vendor Selection |
---|
Tool selection for lithography, clean and wet etch tools. Knowledgable with ASML, EVG and Suss exposure tools. MEI and Semsysco clean and wet etch tools. Veeco metal liftoff tool. ClassOne and Semsysco electroplating tools. TEL and DNS Screen coating tools. Sonotek spray coating tool. |