Expert Details
Plastic Pipe and Piping Materials, Polyethylene, Product Standards, Hydrostatic Stress, etc.
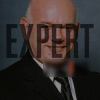
ID: 725134
Tennessee, USA
Expert has been in the plastic piping industry for over 35 years. He worked for the Dupont Company from 1976 to 1995 in the Aldyl “A” polyethylene (PE) pipe business for natural gas distribution. Expert developed the initial use of polyamide (PA) for high-pressure gas distribution, up to 300 psig, to replace metal pipe while with Elf AtoChem during 1995 and 1996.
Expert was the Technical Director for the Plastics Pipe Institute (PPI). As Technical Director, Expert was chairman of the Hydrostatic Stress Board (HSB) on which he served for 20 years to develop pressure rating methods for plastic pipe; and chairman of the Technical Advisory Group for ISO/TC 138 for international plastic piping systems. Expert has developed standards for plastic pipe and fittings in several standards bodies; ASTM, CSA, AASHTO, ISO/TC 138, and AWWA.
Most of Expert’s expertise has been in the natural gas distribution industry. He has been a member of the AGA Plastic Materials Committee for 30 years, the Gas Pipe Technology Committee for 15 years, and was an original member of the Plastic Pipe Database Committee. Expert also developed a one day Technical Seminar for the gas distribution industry.
Expert currently serves as a member of PPI, AGA, GPTC (Chairman of Manufacturers Division), AWWA, ASTM F 17 (Director of Division I), ASTM D 20, CSA B137, CSA Z662 (Chairman of Clause 12 Gas Distribution), and ISO/TC 138.
Was hired by Elf AtoChem in 1995 to develop an all plastic piping system made from polyamide (PA) 11 to be used for high-pressure gas distribution systems as a replacement for metal pipe. He wrote several ASTM and CSA standards for the polyamide 11 piping system. He worked with PPI member companies to develop polyamide 11 pipe, butt fusion fittings, mechanical fittings, meter risers, transition fittings, and valves and also developed a butt fusion procedure for joining polyamide 11 pipe and fittings using the same butt fusion equipment that gas companies use for polyethylene pipe and fittings. Developed new and existing plastic piping standards:
Added 80C sustained pressure requirements to water pipe standards to assure slow crack growth resistance.
Revised D 2513 quick burst requirement to be a ductile failure mode for polyethylene gas pipe instead of a minimum pressure because it is more meaningful.
Developed a new annex in D 2513 for polyamide pipe and fittings.
Introduced 80C requirements for polyethylene heat fusion socket fittings (D 2683) and polyethylene butt fittings (D 3261) consistent with ISO TC 138 requirements
Education
Year | Degree | Subject | Institution |
---|---|---|---|
Year: 1969 | Degree: Bachelor of Science | Subject: Chemistry | Institution: St. Thomas College |
Year: 1973 | Degree: Ph.D. | Subject: Analytical Chemistry | Institution: Michigan State University |
Work History
Years | Employer | Title | Department |
---|---|---|---|
Years: 1996 to 2003 | Employer: Plastics Pipe Institute (PPI) | Title: Technical Director | Department: |
Responsibilities:As Technical Director, Expert was chairman of the Hydrostatic Stress Board (HSB) on which he has served for 20 years to develop pressure rating methods for plastic pipe; and chairman of the Technical Advisory Group for ISO/TC 138 for international plastic piping systems. Expert has developed standards for plastic pipe and fittings in several standards bodies; ASTM F17, CSA, AASHTO, and ISO/TC 138. |
|||
Years | Employer | Title | Department |
Years: 1976 to 1995 | Employer: Dupont Company | Title: Scientist | Department: Plastic Piping Industry |
Responsibilities:He worked for the Dupont Company from 1976 to 1995 in the Aldyl “A” polyethylene (PE) pipe business for natural gas distribution. Expert developed the initial use of polyamide (PA) 11 for high-pressure gas distribution, up to 300 psig, to replace metal pipe while with Elf AtoChem. |
|||
Years | Employer | Title | Department |
Years: 2003 to Present | Employer: Undisclosed | Title: Principal | Department: |
Responsibilities:Aid plastic pipe manufacturers (resin companies and pipe companies) to achieve HDB (Hydrostatic Design Basis) and MRS (Minimum Required Strength) pressure ratings through the Hydrostatic Stress Board (HSB), assist with HSB special cases, develop or revise industry standards (ASTM, CSA, AASHTO, ISO), write petitions to the DOT, and/or aid in marketing plastic pipe products to the end user.Aid end users, primarily gas utilities, to evaluate or qualify plastic pipe products (primarily polyethylene and polyamide 11), revise industry standards, and/or conduct failure analysis of plastic pipe products. Expert will also present technical seminars at gas company locations to provide background on polyethylene pipe, polyamide 11 pipe or new plastic piping materials for the gas industry. Expert will work with laboratories or research organizations to keep abreast of domestic and international standard test methods and standard specifications, and/or write proposals for and then guide research projects for plastic pipe. |
Career Accomplishments
Associations / Societies |
---|
Expert currently serves as a member of PPI, HSB, AGA, GPTC, ASTM F 17 and D 20, CSA, TRB and ISO/TC 138. |
Professional Appointments |
---|
Expert has served as chairman of F17.94 on Terminology and F17.38 on ISO. He is also a member of the F17.90 Executive Committee for F17. Expert is currently the Chairman of ASTM F17 Division I. |
Awards / Recognition |
---|
Expert was also recognized by the US Department of Transportation (Transportation Safety Institute) for outstanding performance as an associate staff in the Pipeline Safety Division in teaching DOT inspectors about plastic gas pipe standards in ASTM and ISO, plastic pipe pressure ratings methods from ASTM and ISO, plastic pipe failure analysis and new plastic pipe materials for the natural gas industry. Expert received the AGA (American Gas Association) Award of Merit in recognition of several presentations made at plastic gas pipe industry meetings, and also serving as moderator at AGA Operations Conferences and Plastic Pipe Symposiums. Expert received the AGA Silver Award of Merit for having faithfully and constructively served the American gas industry, and for making continuous and extensive contributions to further the interests and promote the welfare of the gas industry and of the public. Within ASTM F 17, Expert has received two Awards of Appreciation in recognition of his many years of outstanding service and active participation in the plastic piping standards work of ASTM F 17, and a Special Service Award for his many technical contributions and development of plastic piping standards. Expert received the Paul Finn Memorial Award for his distinguished and continuous service to ASTM F 17 (plastic pipe standards), and particularly for steadfast contributions to the development of sound engineering standards, particularly for plastic gas pipe standards. Expert received the Rinehart Kuhlmann Award in acknowledgment of faithful and significant contributions in furthering the cause of sound and effective plastics piping standardization. Most recently, Expert received the ASTM Award of Merit, which is the highest award given within ASTM. |
Publications and Patents Summary |
---|
He has over fifty publications in the field of plastic pipes. |
Additional Experience
Expert Witness Experience |
---|
He is available for litigation cases involving plastic pipe products, particularly plastic pipe used for natural gas distribution. |
Training / Seminars |
---|
More recently, Expert has developed a one-day technical seminar for plastic pipe materials used in the gas industry. This seminar is intended to provide a background on plastic pipe materials, primarily polyethylene, to update gas engineers on recent developments in ASTM and ISO standards for the gas industry, and to provide information on new plastic pipe materials for the gas industry. These include polyamide 11 for high pressure gas applications to replace metal pipe, crosslinked polyethylene for niche applications that require increased slow crack growth resistance, PE 100 materials that are considered the next new generation of polyethylene materials and multiplayer pipe for indoor gas applications. |
Marketing Experience |
---|
For over 35 years Expert has been primarily involved in plastic piping systems for the natural gas distribution industry. Most of those years were with the Dupont Company where he worked with Aldyl “A” polyethylene gas pipe. He presented several industry papers on the use of the Rate Process Method (RPM) to forecast the life expectancy of polyethylene gas pipe and fittings. Expert presented a paper correlating RPM projections with actual field performance for polyethylene gas pipe materials. Expert also conducted several failure analyses of Aldyl “A” polyethylene pipe components and wrote several failure analysis reports for gas companies. |