Expert Details
OSHA/Industrial Hygiene-lead-asbestos-guarding-falls combustible dusts
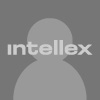
ID: 733267
Texas, USA
Conducted some 2500 Safety and Health inspections for the US DOL/OSHA to include 300 or so job related fatalities/catastrophes.
Expert received additional training at over 20 different safety and health courses at OSHAs Training Institute located at Des Plains/ ILL., i.e. welding, confined space, industrial hygiene, machine guarding. He also trained at various Universities such as: metallurgy school at the University of Alabama, Oil and Gas course at Abilene Texas, Ventilation Engineering two week course at NIOSH in Cincinnati, Ohio, which refreshed my graduate school difficult course in Ventilation design, to name a few.
As an Industrial Hygienist Compliance Officer inspected over 2500 fatalities, complaints, and general schedule Inspections. This included over 100 fatality investigations, hundreds of complaint inspections, numerous catastrophe inspections.
Expert has conducted inspections in high hazard SIC code inspection programs to include asbestos, lead, confined space, machine guarding, noise, silica, falls, heat stress, ergonomics. Some brief examples:
1) Bread processing plant where an employee entered a confined space mixing vat with mechanical rotating blades without lock-out/tag-out and was ground to his death ending in a citation over one million dollars
2) An insulation manufacturer using a cupola furnace for heat had employees do periodic maintenance without lock-out/tag- out procedures causing carbon monoxide poison to employees
3) A sugar processing plant( Imperial Sugar} where he was Team Leader and discovered an imminent danger in the powdered sugar room where combustible dust had excessive accumulations of explosive dust due to lack of proper cleaning programs and exposed employees to an explosion much like the employers’ sister plant happened killing over 20 employees. The inspection resulted in OSHAs’ 4th largest citation. Expert was also assigned to work with FEMA as a safety/health liaison in their large hurricane relief center during and after hurricane Katrina to give technical safety assistance where needed.
Following the hurricane, Expert was assigned to New Orleans for prolonged periods to inspect and protect employees involved in clean-up and reconstruction efforts.
He has expertise in identifying and controlling hazards in industrial hygiene and safety hazards in industries such as manufacturing, construction, beef and poultry processing, agriculture, chemical processing, feed lots, grain storage and processing, lead abatement, asbestos abatement, silica exposure, noise and hearing conservation, heat stress monitoring and controls, ergonomics and 5(1) general duty clause situations. He has conducted hundreds of inspections in these industries. In addition, Expert has conducted over 100 fatality investigations to determine the root cause hazard(s) and controls to prevent further injury. The number one cause of job related fatalities is falls. The majority are construction industry related by carpenters and masonry crafts utilizing scaffolding that is subpar without proper access to upper levels and guardrail fall protection. Lack of or inadequate guardrails are the hazard(s) causing these falls.
As part of his duties with limited supervision, he inspected complaints and general inspections in the Semi-Conductor SIC's to include clean rooms, highly toxic gases used in wafer production and continuous monitoring systems, personal and passive monitoring sampling methods. Photoresist chemicals, ethylene glycols, arisen, phosphine gases, and others that cloud industry reproductive hazards among female workers.
Expert used his education and OSHA training to master all types of air, noise, heat stress, instruments monitoring for all chemicals with PELs both active and passive.
The goal in all of any above situations is to access the safety culture in the workplace and strive to improve it. Ideally, safety training and awareness should be one where all employees are “safety inspectors”, surfacing hazards to be abated and make a safe productive high quality working environment.
As he was # 1 or 2 in leading the Area Office in the number of inspections and violations each year that meant he entered more data in the IMIS and was always trying to find easier time saving methods to prevent redundancy and once the National Office adopted one of his ideas. Expert trained junior CSHOs on IMIS also when they arrived.
Expert is currently serving as a subject matter “Safety/Health expert” in Texas, conducting safety/health inspections, prepare reports and Power Points of my findings; Offer abatement controls. Expert completed 10 inspection sites or the largest feed lots in the U.S. giving me a subject matter expert in this industry as they have grain mill operations producing a million pounds of feed every day. Roller mills have many guarding issues with Combustible Dust a large hazard which he constantly found to exist and lack of magnet controls to keep ferrous metals out and other 1910.272 requirements.
Education
Year | Degree | Subject | Institution |
---|---|---|---|
Year: 1973 | Degree: Masters | Subject: Env Science/Safety/IH | Institution: Oklahoma University |
Year: 1970 | Degree: B.S. | Subject: Math (Minors in Chemistry and Physics) | Institution: Oklahoma University |
Work History
Years | Employer | Title | Department |
---|---|---|---|
Years: 1975 to 2011 | Employer: US DOL/OSHA | Title: Sr Safety/Heath Compliance Officer | Department: Enforcement |
Responsibilities:Conduct Safety/Health inspections for compliance with 29 CFR 1910 and 1926 subject matter expert in: cattle feed production plants, falls, fatality investigations, Industrial Hygiene, confined space, BBP |
|||
Years | Employer | Title | Department |
Years: 1973 to 1975 | Employer: US EPA | Title: Enviromental Scientist | Department: Water Division |
Responsibilities:Conduct environmental assessments and prepare EIS on wastewater projects.Prepared Environmental Impact Statements for wastewater treatment Plant grants to include representing EPA at the required Hearings to defend the primary and secondary impacts the projects may have on the environment. |
Government Experience
Years | Agency | Role | Description |
---|---|---|---|
Years: 1973 to 2011 | Agency: USA/US EPA/OSHA | Role: Safety/Health Officer | Description: Conduct inspections for Safety/Health Compliance |
Career Accomplishments
Associations / Societies |
---|
Member of the local American Conference of Industrial Hygienist attending monthly/quarterly meetings discussing various pertinent topics. |
Awards / Recognition |
---|
The majority of Expert's carrier, he received the highest annual job performance appraisals the U.S. Department of Labor, OSHA gives to their employees, that being “Outstanding” or “Exemplary”. |