Expert Details
Organoclays, Powder/ Bulk Solids Manufacturing/ Combustible Dust & Process Safety Management/ Continuous Improvement
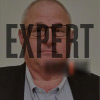
ID: 733893
Missouri, USA
He initially served in a Process Engineering role responsible for the successful start up and operation of a solvent based, PSM covered, rheological additive production unit.
Expert is a dedicated and self-driven Chemical Engineer with 25 years of experience creating and leading high performance cross functional work teams. Expert has exemplary commitment to Health, Safety, and Environmental excellence. He is an excellent communicator with keen interpersonal skills fostering “buy-in” at all levels. Successful track record of driving continuous improvement through motivation, education, team building, and development. Trained Six Sigma Champion leading numerous capital, operations, quality, and business process improvement projects from conceptual design through project execution. Keen business acumen with ability to balance short term activities with long term strategic objectives. Subject Matter Expert resource for processing, financial, product quality, and technical activities. Respected, trusted, and consistent technical leader with intrinsic ability to create a team environment of enthusiasm and success.
Areas of Expertise: Combustible Dust Management, Batch & Continuous Processing, JD Edwards ERP System, 5S, Process Safety Management, Staff Development & Succession Planning, Capital & Expense Budgeting/ Product Std Costing, KPI's & Visual Factory, Flammable Liquid/ Solid & Toxic Materials, Labor Relations & Contract Negotiation, Variance Analysis & Cost Control, Continuous Improvement (Kaizen) Teams, Trained PHA & PSSR Leader, Procurement & Production Planning (MRP), Process Improvement & Design, Root Cause Analysis, Incident Investigation, ISO 9001 Quality Management, Batch Cycle Time & Yield Improvement, TPM & OEE, Regulatory Compliance & Behavioral Based Safety, Order Fulfillment & Distribution, Project Management, Mistake Proofing (Poka-Yoke).
Expert is a dedicated and self-driven Chemical Engineer with 25 years of experience creating and leading high performance cross functional work teams. Exemplary commitment to Health, Safety, and Environmental excellence. Excellent communicator with keen interpersonal skills fostering “buy-in” at all levels. Successful track record of driving continuous improvement through motivation, education, team building, and development. Trained Six Sigma Champion leading numerous capital, operations, quality, and business process improvement projects from conceptual design through project execution. Keen business acumen with ability to balance short term activities with long term strategic objectives. Subject Matter Expert resource for processing, financial, product quality, and technical activities. Respected, trusted, and consistent technical leader with intrinsic ability to create a team environment of enthusiasm and success.
Retired from the specialty chemicals industry after a thirty-year career in solids/ powder handling operations. Experience includes both hazardous and non- hazardous operations in multiple sites across two different businesses.
Significant materials handled in bulk include:
o Combustible materials
Bentonite and Hectorite based Organoclays ground to 95% thru 200M and 325 M.
Various Polyethylene Waxes (pellets and dust)
Ground PTFE
o Non- combustible materials
Bentonite and Hectorite Clays (70% thru 200M)
Synthetic iron oxide pigments
Zinc Oxide and Magnesium Oxide
Education
Year | Degree | Subject | Institution |
---|---|---|---|
Year: 1985 | Degree: BS | Subject: Chemical Engineering | Institution: University of Missouri - Rolla |
Work History
Years | Employer | Title | Department |
---|---|---|---|
Years: 2011 to 2015 | Employer: ELEMENTIS SPECIALTIES | Title: Corporate Process Engineering Manager | Department: Operations |
Responsibilities:∙ Directed raw material study and plant experimental program resulting in $1MM savings by bringing toll manufactured dry process product “in house”.∙ Led process/equipment studies to identify, then optimize, critical process variables which increased annual dry process capacity by approximately 2,000 MT (33%). ∙ Coordinated technical and operations activities (at Elementis and supplier’s sites) throughout selection, testing, and implementation of an alternate strategic organoclay raw material, creating an annual savings of $500K. ∙ Managed $2MM belt filter press replacement project including process design, equipment testing and selection, procurement, installation, and commissioning. |
|||
Years | Employer | Title | Department |
Years: 2007 to 2011 | Employer: ELEMENTIS SPECIALTIES | Title: Site Leader | Department: Operationsv |
Responsibilities:∙ Led operation of the St. Louis site producing 15,000 MT annually with a site budget of $12MM.• 3,000 MT reacted/ blended flammable products via batch process. • 12,000 MT combustible dust products via continuous process. ∙ Set direction/goals for HSE, quality, and productivity initiatives. ∙ Developed and executed dry process organoclay expansion strategy through site selection, project execution, and commissioning generating savings over $1MM in toll manufacturing and supply chain costs. ∙ Executed vacuum filter upgrade project at the St. Louis plant on a “fast-track” basis due to deteriorating condition of existing units. Led the team through equipment selection, procurement, construction, installation, and start up leading to a throughput improvement of 10%. ∙ Authored and coordinated an aggressive capital investment plan to rapidly update and modernize the St. Louis site which had been previously planned for closure. |
|||
Years | Employer | Title | Department |
Years: 2003 to 2007 | Employer: ELEMENTIS SPECIALTIES | Title: NA Organoclay Operations | Department: |
Responsibilities:∙ Directed HSE, quality, and operations activities at the St. Louis, MO., Charleston, WV., and Newberry Springs, CA. sites. Scope of this role was approx. 50 staff and 150 hourly team members with a financial responsibility of over $30MM.∙ Managed/prioritized $5-7MM capital investment process for the organoclay sites. ∙ Led the Charleston team resolving simultaneous issues with biological waste water treatment and product dryer performance resulting in a 100% throughput increase. ∙ Directed cross functional Elementis team (HSE, Regulatory, R&D, Procurement, Quality, Operations, Applications) to evaluate and integrate a modified high volume raw material at St. Louis and Charleston plants. Financial impact was $1.5MM raw material savings between the two sites. ∙ Restructured operations team across the sites creating a cost avoidance of $350K. |
|||
Years | Employer | Title | Department |
Years: 2000 to 2003 | Employer: ELEMENTIS SPECIALTIES | Title: Plant Manager | Department: |
Responsibilities:∙ Led operation of the St. Louis site producing approx. 12,000 MT annually with a site budget of approx. $10MM. Set site HSE, quality, and productivity goals to maximize contribution to corporate objectives.∙ Negotiated cost reductions of $500K with Collective Bargaining Unit while maintaining positive relationship. ∙ Implemented Stable Manufacturing program creating 750 MT/year (10%) additional organoclay capacity increase. ∙ Improved maintenance reliability by implementing Preventive Maintenance and 24-hour maintenance coverage. ∙ Served as site Champion for corporate Six Sigma Black Belts creating $100K raw material savings. ∙ Team Member/Operations group subject matter expert for Elementis’ JD Edwards ERP implementation. |
|||
Years | Employer | Title | Department |
Years: 1993 to 2000 | Employer: ELEMENTIS SPECIALTIES | Title: Operations Manager | Department: |
Responsibilities:∙ Coordinated all batch and continuous manufacturing operations of the St. Louis site producing approx. 12,000 MT annually with an operations budget of $7-8MM.∙ Led operating team of six staff and thirty hourly team members. ∙ Achieved immediate step change improvements in manufacturing variances through operator training and motivation improvements. ∙ Optimized organoclay operation resulting in a 500 MT/year (10 %) capacity increase. ∙ Improved efficiency in the UAT polymer process resulting in a capacity increase of 550 MT/year (20%). |
|||
Years | Employer | Title | Department |
Years: 1991 to 1993 | Employer: ELEMENTIS SPECIALTIES | Title: Process Engineer | Department: |
Responsibilities:∙ Hired to lead startup of a $4MM solvent based batch production unit expansion ultimately producing over 3,000 MT annually.∙ Assisted in ISO 9000 Certification for the site. ∙ Managed Statistical Process Control program. |
Career Accomplishments
Associations / Societies |
---|
American Institute of Chemical Engineers |
Fields of Expertise
milling technology, dust handling, powder conveying, dry powder blending, solids drying, regulatory compliance, total quality management, supply chain optimization, team building, capital planning, ISO 9000 implementation, lean manufacturing, paint rheology, organoclay, fine chemical, chemical industry emergency shutdown procedure, chemical industrial wastewater treatment, in-plant dust control, explosive atmosphere, employee training, manufacturing procedure, dust explosion, process hazard analysis, pre-startup safety review, process safety management auditing, process safety information, Hazard Communication Standard, mechanical integrity, chemical process safety management, coating raw material, vendor certification, customer relationship management, vendor auditing, process engineering, performance improvement, chemical safety training, employee motivation, new product development, chemical process development, cost reduction, leadership training, supply chain cost reduction, total productive maintenance, yield enhancement, dryer productivity improvement, cross-functional team, chemical plant troubleshooting, chemical process troubleshooting, ABC analysis, mechanical reliability, six sigma quality, process optimization