Expert Details
Organizational Management Development; Lean Manufacturing; Factories Design and Layout
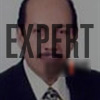
ID: 730807
Egypt
• Develop Strategic Plans and annual working plans.
• Projects managing, coordination of interdepartmental activities, monitoring progress status, and budget control.
• Managing of directed offset, know-how and technology transfer programs of spare parts production and renovation in the field of feeding industries and white appliances.
• Integrated technical studies for the production of sophisticated spare parts using reverse and reengineering technology.
• Designing, programming and executing training for the production of sheet metal press tools, plastic molds, jigs and Fixtures and casting patterns manufacturing on Wire- EDM, Die Sinking and CNC machining Centers.
• Planning material, tools, equipment supplying, stock control, and resources for industrial plants, using MRP I, MRP II, ERP techniques and SCM.
• Contracts planning, administrating, coordinating, monitoring, expediting, and follow-up to meet planned targets within the allocated budgets.
• Prepare and review needed curricula and competencies for the Engineering Industries.
• Asses Engineering workshop and audit its facilities, Human resources and design different workshops needed for the Engineering Industries for the TVET TSS’s.
Lean Manufacturing Implementation
Education
Year | Degree | Subject | Institution |
---|---|---|---|
Year: 1973 | Degree: Bsc. Mechanical Engineering | Subject: Mechanical Production | Institution: Ain Shams University |
Work History
Years | Employer | Title | Department |
---|---|---|---|
Years: 2012 to Present | Employer: Undisclosed | Title: Lean Manufacturing Consultant | Department: Manufacturing |
Responsibilities:Lean Manufacturing Implementation Consultant |
|||
Years | Employer | Title | Department |
Years: 2011 to 2012 | Employer: INDE | Title: Operations Manager | Department: Manufacturing Operations |
Responsibilities:- Plan, develop and implement strategy for organizational and operational development.- Establish and maintain appropriate systems for measuring necessary aspects of organizational and operational performance, monitor, measure and report on organizational development plans and achievements within agreed formats and timescales ( Established and implemented Lean Manufacturing KPI’s). - Manage and control departmental expenditure within agreed budget ( Reduced expences with 50% ). - Liaise with other functions / departmental managers so as to understand all necessary aspects of organizational development, and to ensure they are fully informed of organizational development objectives, purposes and achievement. - Maintain awareness and knowledge of contemporary organizational development theory and methods and provide suitable interpretation to directors, managers and staff within the organization ( Established team Work culture). - Ensure activities meet with and integrate with organizational requirements for quality management, health and safety, legal stipulations, environmental policies and general duty of care ( QSB and TS cerified to GM standard). - Contribute to the evaluation and development of operational strategy and performance in cooperation with the executive team. - Increase management’s effectiveness through Recruiting, Selecting, Orienting, Training, Coaching, Counseling and Disciplining the management team. - Accomplish subsidiaries objectives by establishing plans, budgets, results measurements, presenting assumptions, allocating resources, reviewing progress and making mid-course corrections ( Increased sales 100% - Reduced rework from 13% to 2% - achieve zero external defect). - Coordinates efforts by establishing policies, practices and controls over all departmental areas and coordinating actions with corporate staff. - Builds company image through collaborating with customers, suppliers, government, community organizations, employees and corporate staff. - Contributes to team effort and accomplishing related results by building team work prospective and cooperation practices, commitment to achieve organization objectives, communication matrix network methodology, and challenging spirit |
|||
Years | Employer | Title | Department |
Years: 2008 to 2011 | Employer: TVET Egypt Project | Title: Engineering Key Expert | Department: Capacity Building |
Responsibilities:- Preparing annual and overall work plans and related indicators including financing and discuss with relevant stakeholders- Setting up and consolidation of one functioning ETP on various levels, in the relevant sector and regions in considering legal status of private-public partnerships. - Assist in designing in staff/ personnel development plan for ETP functions and activities including relevant partners. - Assist in development respectively updating Manual of Procedures of ETPs. - Initiate and establish local public – private partnerships between companies/ entrepreneurs and public TVET institutes and support the legal frame work by respective agreements/ protocols. - Explore and initiate cooperation with existing donor funded project (SDP, IMC) and existing local bodies (NGOs, HRD-SC, BRC, etc.) to strengthen public – private partnerships by synchronizing ongoing activities to support the regional/ local business sector. - Initiate and implement overall TVET Quality Assurance on various ETP levels. - Initiate and implement consistent testing and certification system (with open access) to qualify human resources in Engineering industries. - Prepare and review needed curricula and competancies for the Engineering Industries. - Asses Engineering workshop and audit its facilities, Human resources and design different workshops needed for the Engineering Industries for the TVET TSS’s. |
|||
Years | Employer | Title | Department |
Years: 2005 to 2008 | Employer: Ahram Security Group | Title: General Manager | Department: Door Locks Manufacturer |
Responsibilities:- Increased management’s effectiveness.- Developed Strategic Plans. - Accomplished subsidiaries objectives (Increased productivity 50% - Reduce rejects 25%). - Coordinates efforts. - Builds company image. - Maintained and improved quality services. - Maintained professional and technical knowledge. - Contributed to, build and coordinate team efforts. - Feasibility studies and builds up manufacturing capacity to double the capacity to meet customers’ requirements in both local and export markets. - Manage, develop, coordinate and follow up expansions projects. |
Government Experience
Years | Agency | Role | Description |
---|---|---|---|
Years: 2008 to 2011 | Agency: Ministry of Industry | Role: Engineering Key Expert | Description: - Preparing annual and overall work plans and related indicators including financing and discuss with relevant stakeholders - Setting up and consolidation of one functioning ETP on various levels, in the relevant sector and regions in considering legal status of private-public partnerships. - Assist in designing in staff/ personnel development plan for ETP functions and activities including relevant partners. - Assist in development respectively updating Manual of Procedures of ETPs. - Initiate and establish local public – private partnerships between companies/ entrepreneurs and public TVET institutes and support the legal frame work by respective agreements/ protocols. - Explore and initiate cooperation with existing donor funded project (SDP, IMC) and existing local bodies (NGOs, HRD-SC, BRC, etc.) to strengthen public – private partnerships by synchronizing ongoing activities to support the regional/ local business sector. - Initiate and implement overall TVET Quality Assurance on various ETP levels. - Initiate and implement consistent testing and certification system (with open access) to qualify human resources in Engineering industries. - Prepare and review needed curricula and competancies for the Engineering Industries. - Asses Engineering workshop and audit its facilities, Human resources and design different workshops needed for the Engineering Industries for the TVET TSS’s. |
International Experience
Years | Country / Region | Summary |
---|---|---|
Years: 2010 to Present | Country / Region: KSA | Summary: Lean Manufacturing Consultancy |
Additional Experience
Training / Seminars |
---|
- Lean Manufacturing implementation - KPI's development - Supply Chain Management - Dies and Mould Manufacturing Technology |
Marketing Experience |
---|
- Lean Manufacturing Implementation - Organizational Development |
Language Skills
Language | Proficiency |
---|---|
Arabic | |
English |
Fields of Expertise
business operations, business process re-engineering, change management, Institute of Advanced Manufacturing Sciences, Malcolm Baldrige National Quality Award requirement, manufacturing resource planning, organization strategy, organizational assessment, organizational development, organizational productivity, strategic planning, system development, total quality management, workforce management system, world-class manufacturing