Expert Details
Nastran Analysis, Linear & Non-linear Statics, Dynamics & Thermal Analysis
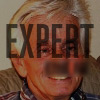
ID: 730343
Florida, USA
Expert's job history includes over 37 years experience in Structural Dynamics, Random Vibration, Shock and Response Spectrum Analysis and Dynamic Systems Modeling and Simulation in support of NASA projects (Apollo, Space Shuttle, X-33, Titan IIIC, Atlas V and Ares 1 Space Programs) at the Kennedy Space Center. He also has 4 years experience on analysis of heavy construction and mining equipment performing structural/mechanical stress analysis and dynamic system modeling.
He is one of sixteen members of the MSC/NASTRAN Select Users Advisory Board (1993).
He has extensive FEA skills include the following:
- Linear and Nonlinear Statics Analyses
- Modal and Complex Modal Analyses
- Linear and Nonlinear Dynamic Analyses
- Frequency and Random Response Analyses
- Shock Spectra (Response Spectrum) Analysis
- Steady State and Transient Thermal Analyses
- Linear and Nonlinear Buckling Analyses
- Fracture Mechanics Analysis
Education
Year | Degree | Subject | Institution |
---|---|---|---|
Year: 1968 | Degree: BS | Subject: Aeronautical and Astronautical Engineering | Institution: University of Illinois |
Work History
Years | Employer | Title | Department |
---|---|---|---|
Years: 1986 to 2011 | Employer: United Space Alliance - Lockheed Martin Space Operations | Title: Engineering Staff VI | Department: Technical Analysis |
Responsibilities:Expert provided Computer Aided Engineering (CAE) Analysis, using Finite Element Analysis (FEA) technique, in the fields of Structural and Mechanical systems analysis (statics and dynamics) and thermal analysis (steady state and transient) of structural, mechanical, and piping systems for Space Shuttle ground support and test equipment and flight equipment. He developed computer programs to provide engineering analysis for most of the major structural, mechanical, and piping systems used by the Space Shuttle at Kennedy Space Center, along with some programs related to Space Shuttle Payloads such as the Hubble Space Telescope and Tracking and Data Relay Satellite System. Engineering Lead providing education, direction, and advice on FEA. He provided test/analysis correlation of data to solve system problems. He recommended purchases of computer hardware and software for engineering work. He Wrote specifications (Request for Proposal) for computer hardware and software requirements in the procurement of CAE, FEA, and Computer Aided Design (CAD) computer systems. He also provided Engineering Analysis for ground support and flight systems on the X-33 program, ground support systems on the Apollo/Soyuz and Atlas V programs, rollout/pad stay analysis for Ares I-X (Constellation program) and dynamics and loads analysis of Ares I flight hardware. He is experience in Aerospace structures analysis, including Nastran models and connection analysis. |
|||
Years | Employer | Title | Department |
Years: 1974 to 1986 | Employer: Planning Research Corporation | Title: Principal Engineer | Department: Analytical Staff |
Responsibilities:Karls' job responsibilities is similar to the United Space Alliance/Lockheed Martin experience. He was Lead Engineer in charge of 8 people that provided Nastran CAE analysis of Space Shuttle ground support systems and test equipment. |
|||
Years | Employer | Title | Department |
Years: 1969 to 1973 | Employer: Westinghouse Air Brake Company (WABCO) | Title: Engineer | Department: Test/Analysis Staff |
Responsibilities:Expert provided Design Engineering for heavy construction and mining equipment. He provided CAE analysis. He also was a Test Engineer providing test setup and analysis of test data. He was an Engineering Analyst providing computer programs for structural/mechanical systems analysis. |
Government Experience
Years | Agency | Role | Description |
---|---|---|---|
Years: 1974 to 2011 | Agency: NASA | Role: Engineering Staff VI for Various NASA Contractors | Description: Staff Engineer VI. He Provided Computer Aided Engineering (CAE) Analysis, using Finite Element Analysis (FEA) technique, in the fields of Structural and Mechanical systems analysis (statics and dynamics) and thermal analysis (steady state and transient) of structural, mechanical, and piping systems for Space Shuttle ground support and test equipment. Developed computer programs to provide engineering analysis for most of the major structural, mechanical, and piping systems used by the Space Shuttle at Kennedy Space Center, along with some programs related to Space Shuttle Payloads such as the Hubble Space Telescope and Tracking and Data Relay Satellite System. Engineering Lead providing education, direction, and advice on FEA. Provide test/analysis correlation of data to solve system problems. Recommend purchases of computer hardware and software for engineering work. Writing specifications (Request for Proposal) for computer hardware and software requirements in the procurement of CAE, FEA, and Computer Aided Design (CAD) computer systems. I have worked on ground support and flight systems for the X-33, Ares I programs and on ground support systems for Atlas V and Ares I-X. |
Career Accomplishments
Associations / Societies |
---|
American Institute of Aeronautics and Astronautics (AIAA), Senior Member. American Institute of Steel Construction (AISC). |
Awards / Recognition |
---|
One of sixteen members of MSC/NASTRAN Select Users Advisory Board (1993). Hold 3 US Patents. Authored or co-authored over 30 publications Three NASA Public Service Group Achievement Awards. Lockheed’s Andy Petro Engineering Excellence Award. NASA Space Shuttle Launch Honoree Award. |
Publications and Patents Summary |
---|
He has over 30 publications and three patents. |
Additional Experience
Expert Witness Experience |
---|
Expert developed and integrated models for rollout and launch pad stay Nastran analysis of the AresI-X rocket at Kennedy Space Center. The following are quotes from Ames Research Center for a review of the Nastran models and model results: KSC is preparing to launch the first of the Constellation vehicles, Ares 1-X, by making extensive use of heritage hardware from STS for ground operations. This will include use of the existing crawler-transporter (CT), an existing mobile launch platform (MLP), existing mount mechanisms (MM) and the existing fixed service structure (FSS) at pad 39B with a new vehicle stabilization system (VSS) that is yet to be constructed. As part of the modeling and simulation effort for the ground support operations of this test flight, the subject report has been prepared by United Space Alliance. It includes analysis of the NASTRAN finite element models depicting the hardware mentioned above, integrated to an existing vehicle model (IVM13) that was assembled from elemental models originally provided by ATK, Glenn Research Center and Langley Research Center. The elemental CT and MLP models are existing certified NASA critical math models. Modeling of the RSS/FSS and VSS structures was performed by USA. The technical work was found to be very thorough and detailed. In particular, the finite element modeling was excellent. The fidelity achieved by integrating several existing models provided very good results for internal loads and external reactions. These loads form the basis of input to other detailed stress reports that show positive margin for use of the heritage hardware. Mode shapes, transient responses and frequency/random response were achieved with very good resolution. Documents that were reviewed in detail included all of the program and agency wind loading criteria (NEDD, DSNE, 1001) as well as the Reference 2 verification of the Ares 1-X IVM vehicle models and the Reference 3 Technical Analysis Report. In addition to this, several of the NASTRAN finite element models used in this analysis were independently run with unit loadings (SOL 101-static analysis) and separately for mode frequencies and shapes (SOL 103-modal analysis). The results of these model validation efforts are noted in Appendix A. Appendix A comments:In order to validate the two integrated models, check runs for both statics and modes were made. Solution 101 was performed on the IVM13-ML-CT model using 1 kip unit loads at the tip of the vehicle in both the north and south direction. For the IVM13-FSS-VSS model, a Solution 101 case was run using the design wind loads from the east. For both models, Solution 103 (normal modes) was run and the primary mode shapes were compared to previously validated models. Weight of the models was found to be within 2% of the values shown in Table 4-8, 4-9 and 4-10. All weights were checked against source data provided in Reference 1. Mode frequencies shown in Appendices A, B and C were found to be within 1% of the values listed in the appropriate tables, with correspondingly appropriate mode shapes. Moments of inertia and principle axis were checked for each elemental model (CT, MLP, IVM) and found to be proper as to location and magnitude. Structural drawings of the CT and MLP were checked against section properties at selected locations in the elemental models and no discrepancies were found. All RBE elements were studied for connectivity issues and none were found. CONM2 mass values were spot checked and found to be reasonable. |
Training / Seminars |
---|
Nastran Random Analysis Class: The class presents random analysis theory and Nastran examples. Certain types of dynamic excitation can be best described by a statistical description (random vibration). These include the acoustic environments due to rocket exhaust, pressure fluctuations due to turbulent boundary layer and ground input excitations on a moving vehicle and earthquakes on buildings. The structural system response to these random excitations requires the methods and techniques of random vibrations. |
Marketing Experience |
---|
Expert is an engineer with over 41 years of experience in field of Computer Aided Engineering (CAE) analysis (37 years experience with ground support, flight hardware and test equipment for the Space Shuttle, X-33, Ares I-X, Ares I, Atlas V, Orion Crew Module and Apollo programs). |
Other Relevant Experience |
---|
Computer Software and Operating Systems • Forty one years experience with FEA programs such as MSC/NASTRAN, NX/NASTRAN. • Thirty years experience with CAE program Siemens/I-DEAS. • One year experience with CAE program Siemens/NX. • Forty seven years experience with FORTRAN Programming Language. • Thirty years experience with Basic Programming Language. • Eighteen years experience with Microsoft Office Products. • Fifteen years experience with MathCad. • Ten years experience with UNIX operating systems. • One year experience with CAE program Patran. • Eighteen years experience with DOS/Windows operating system. • Six Months experience with CAE program Femap. • MacNeal Schwendler Corporation MSC/NASTRAN Beta Tester. • Universal Analytics Incorporated UAI/NASTRAN Beta Tester. • Computerized Structural Analysis CSA/NASTRAN Beta Tester. • Two years experience with Nasgro. • Twenty seven years experience with AISC Specifications. • Two years experience with ACI Specifications. • Thirty seven years experience with many NASA and US Government Specifications. • Extensive FEA skills include the Following: Linear and Nonlinear Statics Analyses Modal and Complex Modal Analyses Linear and Nonlinear Dynamic Analyses Frequency and Random Response Analyses Shock Spectra (Response Spectrum) Analysis Steady State and Transient Thermal Analyses Linear and Nonlinear Buckling Analyses Fracture Mechanics Analyses Computer Hardware • DEC 4 CPU Pentium Pro Windows NT Server 3 years • Silicon Graphics 4D/340 GTX Parallel Processing Workstation 5 years. • HP/Apollo Workstations 6 years. • IBM compatible PC’s 18 years. • DEC/VAX computers 15 years. • IBM 360 and 370 series computers 4 years. • Univac 1100 Series computers 4 years. |
Fields of Expertise
NASTRAN, structural vibration, finite element analysis, modal analysis, nonlinear finite element analysis, seismic analysis, stress analysis, structural analysis, vibration modal analysis, stress modeling, compression failure, floor vibration, finite element method, bending moment, finite element modeling, nonlinear material, vibration modeling, machine vibration analysis, thermal analysis, structural mechanics