Expert Details
Mattress Manufacturing and Design
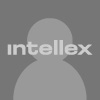
ID: 731918
Wisconsin, USA
Highly qualified Manager offering more than 20 years of Facilities, Personnel, Production, Safety, Quality Control and Logistics Management. Results-focused and effective leader with proven ability to achieve maximum results from personnel and equipment. Talent for proactively identifying and resolving problems – reversing negative process trends, maintaining a clean, safe work environment, controlling costs, maximizing productivity, streamlining processes, ensuring high standards of Quality Control, and delivering profit increases. Advanced Excel and Word skills.
Work History
Years | Employer | Title | Department |
---|---|---|---|
Years: 2007 to 2014 | Employer: Cornell Corporation | Title: Plant Manager | Department: |
Responsibilities:Responsible for operation of an insulated roofing panel manufacturing facility. Responsible for all employees, facility maintenance, budget, production expectations and accompanying issues, shipping and freight, human resources and interaction, serving as Safety Manager with creation of policies and procedures and training, personnel, Quality Control creation and administration. Facility ran both Automated (PLC) and manual finishing and assembly equipment. Company has saw downturn in business over the last two years and was purchased, closed, and relocated to Georgia at the end of June 2014. |
|||
Years | Employer | Title | Department |
Years: 2005 to 2007 | Employer: K-Tek Manufacturing | Title: Second Shift Manager | Department: |
Responsibilities:Responsible for second shift facility and operations of a metal forming, stamping and fabricating business. Equipment in plant ranged from 35 to 400 ton forming presses and press brakes, pemsetter stations, riveters, assembly stations and equipment, mills and lathes, spotwelders, robotic welders, tumbling stations and bins, timesavers and sanders, laser cutter, turret presses, tig and gas welding, shipping and warehouse. Responsible for approximately 40 employees and all facility and production expectations, and accompanying issues, and direction of plant maintenance and tool makers. Reason for leaving employment at K-Tek was to return to a “first shift” lifestyle allowing me time with family |
|||
Years | Employer | Title | Department |
Years: 2001 to 2004 | Employer: Eau Claire Mattress Manufacturing | Title: Plant Manager | Department: |
Responsibilities:Complete responsibility for Manufacturing and Warehouse Facility. Maximizing efficiencies, while adhering to safety and quality standards and ensuring maximum profitable margins on outgoing product. Design and set manning levels for all departments and processes. Ensure and administer proper production, staging, and on time delivery of products to various points in five state region. Ensure DOT compliant delivery while managing company fleet of OTR vehicles and drivers. Adhering to OSHA standards and leading Safety Committee in facility. Responsible for maintenance and upkeep of facility and accompanying equipment. Ensure proper purchasing, end usage of, and incoming quality of all supplies, services, and materials.. In charge of the creation and enforcement of Facilities Maintenance and Improvement, Quality Standards, Personnel Policies, Product and Production Design. Business was sold in 2004, pieced out, and then changed to overseas suppliers. |
|||
Years | Employer | Title | Department |
Years: 1996 to 2001 | Employer: Sealy Manufacturing | Title: General Supervisor | Department: |
Responsibilities:This company did $25 million annual sales, with a workforce of 150 employees. He worked progressively through all departments in the facility as Supervisor in each ( Steel, Wood, Shipping & Receiving, and Maintenance), until assigned duty as General Supervisor over all. Expert was responsible for quality, production, safety, efficiency, delivery, and employee negotiations in a union environment, as well as overall guidance of each department and accompanying personnel. We always met and usually exceeded all goals and expectations relating to Warehousing, Production, Safety, Quality, and Delivery. He decided to change employment to pursue a career in Eau Claire, which offered me a challenging advancement in responsibility and pay. |
|||
Years | Employer | Title | Department |
Years: 1976 to 1996 | Employer: King Koil Manufacturing | Title: Plant Manager | Department: |
Responsibilities:Responsible for Manufacturing and Warehouse Facility. Progressed from hire as a general laborer through assembly, facilities maintenance, and operator duties in all departments, to Supervisor and then eventually to Plant Manager in 1990. Responsibilities were facility maintenance, production, safety, personnel, freight and fleet issues, quality and efficiency, and timely accurate delivery of product. Decision to pursue employment with Sealy shortly after company went through ownership change, and was last member of original management team to leave King Koil. |