Expert Details
Machine Tools, Heavy Equipment, and Aerospace Manufacturing Technologies
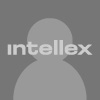
ID: 726234
Minnesota, USA
He has defined piece part geometry using CAD wireframes and surfaces and created toolpath for some of the most complex parts, including advanced aerospace jet engine cases and structural members.
The methods he uses to take advantage of the CAD/CAM/CNC system and post processors to deliver geometry correct and verifiable in the toolpath to the machine tool with minimal operator intervention, such as edits or repositioning of the workpiece.
Expert has used Lean Manufacturing techniques since learning about it in 1985. Most recently he became a Certified Lean Six Sigma Black Belt.
Expert was a member of a team that transformed Briggs & Stratton into Focused Factories using the Toyota Production System (TPS). Within two years Briggs & Stratton increased the inventory turnover rate from 2 to 200 and slashed lead time from 6 months to 24 hours.
Since then Expert has incorporated lean tools such as Kanban, one-piece-flow, and SMED into innumerable projects and maintains a focus on Total Cycle Time.
Expert has shipped and installed several machine tools and systems worth up to $18,000,000, from machines that weigh several hundred pounds to 100 kips, and in a range of technologies from welding gantries to precision machining centers to packaging equipment. He understands industry practice and leads installation projects working with riggers, mechanics, electricians, programmers, operators, etc., and trains people on the new equipment.
Installations have included complete Focused Factory layouts, machining cells, and individual machines. Expert has created factory building and plant floor layout drawings using CAD and has examples of transmittal documentation showing the phases of machinery moves needed to complete a project.
Expert is pretty good with a forklift or crane, and many hand tools!
Expert has been writing machine tool code since Flexo-Writers were used to punch ASCII 8-bit code on 1-inch paper tape, then spooled on the machine thru the tape reader.
Expert has written code in several unique languages of machine code including Fanuc Custom Macro, Kearney & Trecker APL, and Okuma User Task 2. The programs are used for performing functions such as probing, tool measurement, tool life management, and specialized production requirements.
Other types of coding include sub-routines, safe-start blocks, and post-processor development to ensure correct and safe code from the CAD/CAM system.
Expert has developed and performed machine tool qualification and machine tool runoff procedures for Caterpillar, Ingersol-Rand, Briggs & Stratton, MTS Systems, and others in the aerospace, nuclear, defense, & heavy equipment industries. Often these procedures are required for reliability and/or precision machine tool applications.
These procedures ranged from the demonstration of geometric accuracy to Process Capability Index (CPk) studies during a runoff on turn-key systems. Expert placed a calibration artifact into service on a large FMS that was scheduled to run automated inspections of the machine tool accuracies and report pass / fail and quantitative analysis for each of over a dozen large machines.
Successful qualification procedures are a critical milestone in the delivery of machine tool systems, often linked to the largest percentage of progress payments, and frequently the last step before a machine is put into full production.
Criteria for qualification and acceptance by the customer are clearly defined in the contract terms, which frequently are in the form of a proposal by the supplier and a purchase order from the customer. These documents often have different terms and conditions that are overlooked in the haste of a new order. Terms of acceptance that are not clearly defined can result in a serious point of contention between parties, affecting all stakeholders. Expert has helped resolve misunderstandings resulting from changes of scope, misinterpretations of standards, and performance failures of the machine tool to meet specifications.
Expert learned to design fixtures, tools, and gages in a shop with 1000 different types of machine tools, including plain mills and machining centers.
Fixtures present the datum structure of the part to the tool and are an important member of the Machine-Fixture-Part-Tool structural loop. Tools are used to cut or form the work from raw stock to its final shape. Gages verify the product meets final or in-process dimensional characteristics and might be Standard Measuring Equipment or special functional gages.
Fixture functions include operator interface, loading, and unloading, presenting multiple faces of the part to the tools, ease of changeover, transferring the part across multiple machines, and, in the case of jigs, presenting the tool to the part using aids such as drill bushings.
Expert designs fixtures using CAD/CAM during the process planning phase of piece part development. First, the finished part geometry is imported or created, a tool list is defined, and each feature is accounted for in the machining process on a blueprint. A sequence of operations is defined from the most difficult finishing operations and working backward through the process to raw stock. Operations are defined in sequence, and fixture concepts are developed along with stock allowances and tool clearances.
Machining fixtures require modeling along with piece parts, detailed and dimensioned isometric drawings, Bill Of Material (BOM), and manufacturing instructions including tool lists and toolpath (CNC machine code).
Expert has been welding since the 1970s on everything from motorcycles, cars, and heavy vehicles, to machine guns, aircraft engines, and fuselages,
Welding machinery either: replaces a human being; or presents forces, action, and environment beyond our capability.
Replicating human effort requires knowing how to perform the task, then teaching a machine to give the same result within its operating scope. Expert has demonstrated the ability to weld alloy steels and develop the fixtures, parameter settings, metallurgical qualification records, procedures, and programming for a fully automatic robotic welder. This system Gas Metal Arc Welded (GMAW) several subassemblies for a 40mm Navy machine gun. Expert used the Spray Arc Method (using an atomized particle spray) and the Globular Transfer Method on the same machine with several welding operations.
At MTS Systems, Expert was a design team member for a large Friction Stir Welding (FSW) system for a commercial aircraft builder. The model shop he supervised helped build a proof-of-concept machine and tooling. The final machine used a 3-axis gantry machine that he wrote specifications for and supervised the geometric qualification testing giving acceptance to the project engineer. Expert also gave direction to the mechanical engineer designing the 4th and 5th axis head/spindle, basing recommendations on machine building standards, structural integrity, and practical knowledge of manufacturing the major components.
Expert's MTS team helped build a similar concept and full-scale Linear Friction Welding (LFW) machine to make near-net-shape turbine engine blades for Rolls Royce.
Expert was certified to weld GTAW and GMAW per Mil-W-1595A (precedes AWS D17.1) as part of a defense contractor in order to develop Procedure Qualification Records (PQR's) and Weld Procedure Specifications (WPS's) on 40mm machine gun receivers. Recently Expert was instrumental in assisting a major prime aerospace contractor (Goodrich) in obtaining Nadcap Accreditation in welding & brazing processes based on this experience.
Expert has two graduate-level courses in Metallurgy and Materials Engineering.
Expert programmed a robot and led a project utilizing 5 tool designers and 5 toolmakers to develop production welding fixtures.
Expert has written technical specifications and inspection/acceptance criteria for individual machine tools worth up to $1,000,000, including Cincinnati U-5 and Makino A45 machining centers, and special machines designed and manufactured for a specific purpose.
Expert has performed machine tool acceptance procedures on individual machine tools and flexible manufacturing systems worth up to $18,000,000. I use geometric accuracy and Process Capability Index (CPk) measures to verify and quantify machine capabilities as specified per contract or within standard specifications.
Expert has performed training for machine operators, maintenance technicians, programmers, and engineers in proper and safe methods, as well as, full ranging capability and capacity, of machine tool systems. Clients include Caterpillar, General Dynamics, US Navy, Ingersol - Rand.
Expert has worked to define system specifications and scope of work documents based on sales proposals and customer purchase orders on systems worth up to $2,500,000. This was part of a Project Management assignment, and he also created the Work Breakdown Structure, resource assignments, time estimates, Critical Path analysis, and Gannt charting for several concurrent projects.
Summary of Skills:
Lean Manufacturing / Six Sigma CLSSBB, Operations Management, & Supply Chain Mgmt CPIM
o 90%+ improvements in Cycle Time, Working Capital, Inventory Turnover Rate (ITR), and cash flow.
o Experience and Application of 100+ Lean & Six Sigma tools. Statistical expertise in multivariate analysis.
o Customized Instruction and University courses in Engineering, Operations, Quality, Lean, and Six Sigma.
New Product / Process Implementation, Research, & Development – Prototyping, Process Capability
Material & design specifications, Solid Modeling, Proof-Of-Concept, Prototyping, Design for Manufacturing & Assembly (DFMA), Geometric Dimensioning & Tolerancing (GD&T), Special Process & Special Machine design, Materials expertise, Supplier Development, vendor qualification (DQ, IQ, OQ, PQ), SPC, Cpk.
Project Management & Systems Integration
o Specifications, Scope, WBS, resource allocation, CPM, Gantt, strategic planning, Systems Engineer
o Direct & coach cross-functional teams using broad-based technical knowledge and formal training
o Graduate coursework in Program / Project / Team Management with experience in multiple simultaneous jobs.
o Integration of equipment and facilities into automated systems for flexible & verifiable production.
Computerized Numerical Control (CNC) Machining Applications
No part too tough, 5-AXIS, post-processors, families of parts, FMS unattended operation, tool & fixture design, part modeling from complex drawings, G-code, CAD/CAM, CNC programs for machining centers and lathes.
Weld Engineering
o Nadcap Accreditation, Graduate Metallurgy & Materials Engineering, Certified Aerospace Fusion processes.
o Procedure Qualification Records (PQR’s), Weld Procedure Specifications (WPS’s), Fixtures, robotics, GMAW, GTAW, Torch Brazing, Laser Beam Welding, Friction Stir Welding expertise.
Education
Year | Degree | Subject | Institution |
---|---|---|---|
Year: 2005 | Degree: Master of Education | Subject: Business & Industry | Institution: University of Minnesota |
Year: 1985 | Degree: BS | Subject: Manufacturing Engineering | Institution: UW-Stout |
Work History
Years | Employer | Title | Department |
---|---|---|---|
Years: 2018 to Present | Employer: Undisclosed | Title: Assistant Professor of Engineering & Technology | Department: |
Responsibilities:Computer-Aided ManufacturingWeld Engineering Product Design & Development (Graduate) Impacts of Engineering |
|||
Years | Employer | Title | Department |
Years: 2013 to 2018 | Employer: (Undisclosed) | Title: Academic Staff | Department: Operations & Management |
Responsibilities:Lean EnterpriseLean Project Manager, Outreach Center Teaching APICS CPIM Exams (5) Resource Planning & Materials Mgmt Engineering Economics Total Quality Management (TQM) Manufacturing Enterprise Practicum Innovation Management Production & Operations Management Online & face-to-face courses |
|||
Years | Employer | Title | Department |
Years: 2004 to 2013 | Employer: Consultant | Title: Contract Engineer and Independent Contractor | Department: |
Responsibilities:Process Flow Analysis, Line Balancing, Takt Time, Assembly layout of aircraft structuresNadcap Accreditation in weld processes (GTAW, GMAW, LBW, RW, IB, TB). Supplier Development supporting vendor qualification and cost reduction on 8000 parts. CAD/CAM/CNC programming, tool & fixture design of aircraft structural, firearms, & machine components. End customers: Lockheed, BAE, General Atomics, P&W, GE, Goodrich, Vought, Boeing. AS9100 |
|||
Years | Employer | Title | Department |
Years: 2011 to 2013 | Employer: Electric Machinery, Inc. | Title: Lean Enterprise Coordinator | Department: |
Responsibilities:Training all organizational levels in Process Mapping, 5S, GD&T, cell design, data collection.Value Stream Mapping (VSM), Process Mapping, Standard Work, Process Flow Analysis Focused Factory planning, plant floor layout, coordination of rearrangement. CAD/CAM/CNC, Tool & Fixture design. AutoCAD Mechanical, Surfcam. Machine rebuild specifications. |
|||
Years | Employer | Title | Department |
Years: 2007 to 2009 | Employer: MultiFeeder Technology | Title: Industrial Engineer, Project Manager, and Systems Integration Manager | Department: |
Responsibilities:The reduced lead time of core product through Lean Assembly methods. Managed multiple simultaneous projects worth up to $2,400,000. Led a cross-functional team to design, build, & deliver high-speed automated systems. Assembly Procedures, Kanban, DFMA, FMEA, Process Mapping. Position eliminated in the slowdown. |
|||
Years | Employer | Title | Department |
Years: 2002 to 2004 | Employer: University of Minnesota | Title: Instructor of Technology & Graduate Assistant | Department: |
Responsibilities:Taught 24 credits in Communication, Information, Construction, Manufacturing, Design, Technical Drawing, Biotechnology, Energy, Power, Transportation, and Machinery Technologies. Graduated May 2005. |
|||
Years | Employer | Title | Department |
Years: 1997 to 2001 | Employer: MTS Systems Corp. | Title: Manufacturing Engineer & Model Shop Supervisor | Department: |
Responsibilities:20 direct reports supporting projects in Materials Testing & Simulation.Design review for manufacturability (DFM) on life-cycle & fatigue testing systems. Design Team Member on Systems including Friction Stir Welding (aircraft skins); Linear Friction Welding (turbine engine blades for Rolls-Royce); high speed simulated roadways for tires & F1 racing teams |
|||
Years | Employer | Title | Department |
Years: 1991 to 1997 | Employer: Briggs & Stratton Corp. | Title: Advanced Manufacturing Engineer | Department: |
Responsibilities:Developed and implemented Kanban System, reduced tooling inventory by $1,000,000 in one year.Toyota Production System (TPS) implementation cut mfg. lead times from 180 days to 1 day. Inventory Turns increased from 2 to 200+. Programmed 60 CNC machines for six Focus Factories producing 16,000 engines daily. Developed fully automated piston cam-turning technology to meet the demand for 10,000 units per day. Cell design, special machine design, and special process development to meet one-piece-flow takt times |
|||
Years | Employer | Title | Department |
Years: 1985 to 1991 | Employer: Kearney & Trecker | Title: FMS Applications Engineer | Department: |
Responsibilities:Methods, tooling, work holding, and programs for Flexible Manufacturing Systems (FMS).5-axis, VTL, HMC, VMC applications, and acceptance testing using ASME B5.54, NAS-979, CpK. Trained technicians, programmers, and engineers in CNC machinery & FMS technology. Processing & Programming of piece parts worth up to $100,000 each with verifiable accuracy. Cpk, accuracy, and performance verification on machines and systems worth up to $18,000,000. Clients include General Dynamics, Caterpillar, Ingersoll-Rand, US Navy, FMC, United Nuclear Corp. |
Career Accomplishments
Associations / Societies |
---|
SME Lean Enterprise Institute |
Licenses / Certifications |
---|
Certified Lean Six Sigma Black Belt |
Additional Experience
Expert Witness Experience |
---|
Deposed on manufacturing system contract dispute. The court reporter told Expert was the best witness she ever had. Last witness before out-of-court settlement. |
Training / Seminars |
---|
Lean Six Sigma Green Belt training. Geometric Dimensioning and Tolerancing. 24 credits in Manufacturing Technology; Construction Technology; Communication, Power, Energy, Transportation, and Machinery Technolgy. Summary of Education Certified Trainer in Industry 4.0, Controls, Robotics, Sensors thru NC3 7/2018 Certified in Production & Inventory Management 8/2016. Certified Lean Six Sigma Black Belt through Villanova University 8/2008. Master of Education in Business and Industry, University of Minnesota awarded May 2005. o Technology Instructor for two years teaching 24 credits o Ph.D. coursework completed. 25 Graduate courses completed with a GPA of 3.75 |
Vendor Selection |
---|
Specified and selected machine tool vendors for machines worth up to $1,000,000. Sourced multiple vendors for outside services in heat treatment, coatings, forgings, materials, and special processes. |
Marketing Experience |
---|
Expert has delivered machine tool services as a supplier and customer across several industries, for companies such as Boeing, General Dynamics, General Electric, US Navy, Volvo, Toyota, Bridgestone/Firestone, and many others. I have visited dozens of plants and worked with hundreds of engineers and technicians. He was certified as a Lean Six Sigma Black Belt (CLSSBB) through Villanova University. |
Other Relevant Experience |
---|
Expert completed coursework toward a Ph.D. and is well versed, an excellent technical writer, creates outstanding presentations and is very practical. Expert has extensive knowledge of materials, processes, and machinery but is also very practical and hands-on. His shop floor communications are excellent. |
Fields of Expertise
computer-aided manufacturing, lean manufacturing, machine installation, machine-tool code, machine-tool qualification, machine-tool runoff, machining fixture design, numerically controlled machine tool, precision machine tool, tooling, welding machinery, gas-tungsten arc weld, industrial engineering, machine shop, metallurgical engineering, welding engineering