Expert Details
Lean Manufacturing Engineering and Production Systems Implementation
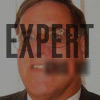
ID: 727714
Michigan, USA
He personally led teams in large industrial manufacturing facilities to successfully identify production constraints and improve throughput.A short term engagement was as arbitrator for a work standards dispute at a hand tool manufacturer that used a piece work incentive system.He has designed and implemented turnkey solutions in conveyance and distribution for industrial plants, wholesale distributors, retail distribution centers and health care customers.He provided Expert Opinion on Manufacturing Capacity issues in a federal litigation.He participated as a senior consultant on a study team to a European OEM Manufacturer for cost reduction opportunities in the supply chain.
Education
Year | Degree | Subject | Institution |
---|---|---|---|
Year: 1977 | Degree: MS | Subject: Industrial Engineering | Institution: University of Toledo |
Year: 1971 | Degree: BME | Subject: Mechanical Engineering | Institution: Kettering University (General Motors Institute) |
Work History
Years | Employer | Title | Department |
---|---|---|---|
Years: 2009 to Present | Employer: Undisclosed | Title: President | Department: |
Responsibilities:He is the principal for a Manufacturing Engineering consultancy. |
|||
Years | Employer | Title | Department |
Years: 1999 to 2009 | Employer: General Motors | Title: Global Manufacturing Chief Engineer | Department: Manufacturing Program Management / Performance Vehicles |
Responsibilities:He was responsible for program manufacturing and manufacturing engineering on the Performance Vehicle Line Team. He led production launch activities for XLR, XLR / V, Corvette, Z06, Solstice / Sky Turbo, Opel GT, Daewoo G2X, ZR1 and Grand Sport. |
|||
Years | Employer | Title | Department |
Years: 1997 to 1999 | Employer: General Motors | Title: Engineering Group Manager | Department: Quality, Reliability and Competitive Operations Implementation |
Responsibilities:He managed the corporate Throughput Improvement Process and personally led teams at Lordstown and Linden assembly plants to successfully increase production.He completed Goldratt Institute Jonah program and is able to apply the Theory of Constraints to reduce costs and enhance profitability. |
|||
Years | Employer | Title | Department |
Years: 1985 to 1997 | Employer: General Motors | Title: Engineering Group Manager | Department: Advanced Engineering Staff |
Responsibilities:Led the team of Supplier Cost Engineers providing support to Purchasing in cost reduction / avoidance activities at Tier 1 suppliers.* Managed the NAO Productivity Lab assisting plants to implement lean manufacturing solutions and create continuous improvement shop processes. * Co-founded the GM Synchronous Knowledge Center created and delivered lean manufacturing / office training to over 3000 GM participants, which improved productivity. * Original member of the GM Production System team that created the GM Global Manufacturing System with a focus on material flow to reduce inventory and costs. |
|||
Years | Employer | Title | Department |
Years: 1982 to 1985 | Employer: AP Parts | Title: Industrial Engineering Manager | Department: Toledo Manufacturing Division |
Responsibilities:He was responsible for labor standards, Just-In-Time ( JIT ) implementation, layout and OEM quoting. |
|||
Years | Employer | Title | Department |
Years: 1980 to 1982 | Employer: Engineered Distribution Systems | Title: Vice President / Owner | Department: |
Responsibilities:He provided turnkey solutions in conveyance and distribution for industrial plants, wholesale distributors, retail distribution centers and health care customers. |
|||
Years | Employer | Title | Department |
Years: 1975 to 1980 | Employer: Tenneco Automotive | Title: Facilities Engineering Manager / Staff Production Engineer | Department: Production Engineering |
Responsibilities:As Facilities Engineering Manager / International Capital Projects he was responsible for facilities projects and maintenance for four plants and corporate headquarters.As Staff Production Engineer he performed production engineering for cold forming, tubing, powder metal and plating at all plants. |
|||
Years | Employer | Title | Department |
Years: 1966 to 1975 | Employer: Chevrolet Motor Division | Title: Industrial Engineering / Production Supervision | Department: |
Responsibilities:As Industrial Engineer completed methods, standards, layout and conveyance in various manufacturing departments. |
Government Experience
Years | Agency | Role | Description |
---|---|---|---|
Years: 1971 to 1977 | Agency: US Army NG | Role: Warrant Officer 2 | Description: Communications / Electronics Officer and Mechanical Maintenance Officer |
International Experience
Years | Country / Region | Summary |
---|---|---|
Years: to Present | Country / Region: Japan | Summary: He led three benchmarking visits to Japanese manufacturers (automotive and non-automotive) to learn and transfer knowledge on lean manufacturing principles. |
Years: 2012 to 2012 | Country / Region: Europe | Summary: He participated as a team member on a study at a OEM manufacture and Tier 1 suppliers to identify cost reduction opportunities in the supply chain. |
Career Accomplishments
Associations / Societies |
---|
Society of Manufacturing Engineers; Institute of Industrial Engineers |
Licenses / Certifications |
---|
Registered Professional Engineer; Goldratt Institute Jonah |
Awards / Recognition |
---|
Alpha Pi Mu Industrial Engineering Honor Society |
Publications and Patents Summary |
---|
One patent - automatic transmission |
Additional Experience
Expert Witness Experience |
---|
Provided Expert Opinion / Deposition on manufacturing capacity issue for a federal litigation. Testified in U.S. District Court as Expert Witness. |
Training / Seminars |
---|
Co-founded the GM Synchronous Knowledge Center and created and delivered lean manufacturing / office training to over 3000 GM participants. |
Vendor Selection |
---|
Participated as a senior consultant on a European study at an OEM manufacturer to reduce costs in the supply chain. |
Marketing Experience |
---|
Automotive Manufacturing Responsible for program manufacturing and manufacturing engineering on the Performance Vehicle Line Team. Led production launch activities for XLR, XLR / V, Corvette, Z06, Solstice / Sky Turbo, Opel GT, Daewoo G2X, ZR1 and Grand Sport. * Launched 100% of programs below the manufacturing investment and operating expense budgets by leading a disciplined launch process. * Implemented an ultra low volume vehicle assembly system ( XLR ) that achieved the world benchmark in hours per vehicle. * Led the team to reduce dimensional variation by 50% in key areas of the Kappa architecture enabling the successful coupe launch on a convertible structure. * Set the foundation for the Corvette to achieve segment leading build quality through rigorous manufacturing issue resolution in pre-production events. |
Other Relevant Experience |
---|
Led the team of Supplier Cost Engineers providing support to Purchasing in cost reduction / avoidance activities at Tier 1 suppliers. Converted component manufacturing plant from piece work to measured day work, negotiated during a nine month strike, which reduced labor costs. |
Fields of Expertise
automobile manufacturing, continuous flow manufacturing, discrete manufacturing, flexible manufacturing, integrated product team, just-in-time inventory, lean manufacturing, manufacturing, office productivity, productivity improvement, Shingo manufacturing, synchronous manufacturing, world-class manufacturing, prototype manufacturing, bus manufacturing, product evaluation, build-to-order, mass customization, product variety optimization, remanufacturing, productivity measurement, distribution requirements planning, line balancing, team building, engine manufacturing, manufacturing facility design, incentive compensation plan, customization, learning curve, power-and-free conveyor, world-class maintenance, manufacturing cost control, manufacturing cost analysis, manufacturing execution system, operation analysis, manufacturing lead time, work team, lead time, motivation, industrial engineering setup time reduction, industrial engineering setup time, defect control, enterprise resource planning, total productive maintenance, diameter measurement, just-in-time software, factory, focused factory, metal manufacturing, factory management, inventory control system, automobile body, manufacturing model, inventory reliability improvement, production line, fastener manufacturing, moldmaking, assembly line, manufacturing troubleshooting, industrial design, product design variation reduction, product manufacturing, material forming, fabrication, precision gear manufacturing, automated manufacturing, product development cycle time, new product design, assembly robot, manufacturing resource planning, manufacturing process development, flexible manufacturing system, automatic automotive transmission system, manufacturing information system, manufacturing systems analysis, small-volume manufacturing, manufacturing process optimization, manufacturing profitability, manufacturing productivity, productivity measurement (quantity), computer-aided manufacturing, operations research, manufacturing systems modeling, computer-aided design and manufacturing, manufacturing facility, design engineering, product life cycle, international manufacturing, product optimization, manufacturing control, automobile, production engineering, design process, dimension limit, industrial engineering, value engineering, total quality management, project scheduling, capacity planning, operations management, kanban, inventory management, industrial benchmarking, flexible-fixturing technology, manufacturing cell, manufacturing automation, manufacturing adhesive