Expert Details
ISO 9001-2000/TS 16949 audits, documentation, training, assistance for certification, APQP, SPC
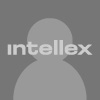
ID: 723337
New Jersey, USA
He has assisted companies in preparation for the Malcolm Balridge National Quality Improvement Award by providing training in several key areas. He has over 30 years of experience in Aluminum alloys as well as the heat treatment practices and issues connected with it. He has experience with new product development. He has developed new products for various users with the exclusive of use of Advanced Product Quality Planning used by automotive suppliers. The product development cycle time has been reduced for various products by use of concurrent engineering, with reduction of over 30%. He also has experience with rapid prototyping and product development. New products have been developed well before the needs of customer on a number of occasions.
He is an AIAG certified second party assessor for QS 9000. He has assisted several companies to achieve certification to QS 9000, by developing manuals, training on APQP, MSA, FMEA, SPC and PPAP. He has also assisted in developing vendors for compliance as QS 9000 second party assessor. He has developed supplier quality engineering inclusive of SCAR, SPC and other data on line review. He has done vendor quality auditing in respect of their products, process and systems. He has worked in quality control for automobile pistons- castings, forgings and final product for over 15 years. He has audited product, process and system quality. He has trained various auditors as well. He is proactive in quality engineering by using mistake proofing. He was worked to link the needed quality standards to the processes to ensure optimum results.
Menon Pistons, Kolhapur, India: (Manufacturers of Aluminum Die Cast Automobile pistons)
Quality Engineering Problem solving Engineer
Non conformance management, Analysis of data, Corrective action, preventive action, 5 Why, Root cause analysis, Training, Control Plan revisions, FMEA analysis, product realization & manufacturing process design parameters optimization, process audits.
Auto Liners, Vijayawada, India: (Manufacturers of Cast iron centrifugally cast, machined cylinder liners)
Quality Engineering Problem solving Engineer
Non conformance management, Analysis of data, Corrective action, preventive action, Cost & scrap, PPM reduction, Pareto, Cause Effect, Training, Control Plan revisions and product realization process parameters optimization
Suprajith Engineering Private Limited, BANGALORE UNIT 1, UNIT 2, DODDABALLAPUR UNIT, GURGOAN UNIT, GUJARAT UNIT, Chemicals division: (Manufacturers of Automobile clutch, brake, speedometer and other cables, Speedometers, chemicals) - MULTI-SITE OPERATIONS
ISO 9000/QS 9000/TS 16949 Quality Management Implementation Consultant/ Six sigma coordinator:
A) Preparation, review and finalization of needed documentation for ISO 9000- Quality Manual, Standard Operating Procedures, Process Manual, Work Instructions, Formats for records, Awareness training, Internal Quality Auditing, Product, process and system audits, conducting of Management review Training, Leading corrective and preventive action, Continual improvement teams, Supplier's audits and development, Pre-certification audits, leading management representation role in certification audits, effective closure of findings for successful certification, continuing process and system surveillance audits, association in audits, effective closure of findings, 5 Why, Root cause analysis, 8D, Pareto, Cause Effect, implementation of-process & continuous improvement.
B)Training, implementation and Team leader for core tools- APQP, SPC, FMEA, Development of control plans, Gage R&R, Calibration verification, PPAP-, Customer complaints resolution, Company level data analysis, activities as in a) in respect of system elements as above for QS 9000/TS 16949-2002
New Product launch: Training, implementation, Participation in APQP team activities for- Analysis of warranty& rejection data of similar products, Process bench mark data analysis for needed inputs/revisions for equipment, training, process instructions and monitoring, customer interaction regarding needed quality data, Preliminary bill of materials & related quality plan, assistance in supplier development, in-process inspection set ups as per flow process charts, Special product and process characteristics listing, determination of needed SPC activities, assessment of new technology and it’s related process parameters controls, development of preliminary engineering standards & related equipments for inspection, measurement, DFMEA development, verification, review, validation checks, development of prototype control plans, engineering & material specification testing facilities, New IM&T equipment, gages and facility requirement planning coordinated with Gantt of equipments delivery date, team feasibility commitment review, Product/process quality system review in respect of additional controls or changes in procedures, updating as per checklist, Finalized flow process chart, association for PFMEA finalization, pre-launch control plans, process instruction review & needed control measures definition, Measurement system analysis plan, Initial process capability study, participation in trial run, process audits, Measurement system evaluation- Gage R&R, linearity if applicable, PPAP, production control plan finalization, Quality planning sign off in respect of all above, supplier, in process control chart analysis, process stabilization, improvement.Incoming, in process and final inspections and audits, Resource management, skill matrix development, Management review process, customer satisfaction data analysis.
12) SKP ENGINEERING COLLEGE, TIRUANNAMALAI. (Education for Bachelor of Engineering of different branches)
ISO 9000 Quality Management Implementation Consultant:
13) SJ POLYTECHNIC, TIRUANNAMALAI. (Education for Bachelor of Engineering of different branches)
ISO 9000 Quality Management Implementation Consultant:
14) DEEN DAYAL ENGINEERING COLLEGE, MADRAS. (Education for Diploma in Engineering of different branches)
ISO 9000 Quality Manager:
15) NEW HORIZON ENGINEERING COLLEGE, BANGALORE. (Education for Bachelor of Engineering of different branches)
ISO 9000 Quality Management Implementation Consultant
Education
Year | Degree | Subject | Institution |
---|---|---|---|
Year: 1960 | Degree: ME | Subject: Production Engineering Foundry | Institution: Indian Institute of Science, Bangalore, India |
Year: 1958 | Degree: BE | Subject: Mechanical Engineering | Institution: Mysore University, India |
Year: | Degree: BS | Subject: Physics, Chemistry, Mathematics | Institution: Mysore University, India |
Work History
Years | Employer | Title | Department |
---|---|---|---|
Years: 1994 to 2006 | Employer: Undisclosed | Title: Principal Quality Management Consultant | Department: Undisclosed |
Responsibilities:He is responsible for development of needed documentation- Quality manuals, Procedures, Process manuals, formats, records, needed for successful implementation and certification to ISO 9001-2000 for different products- automotive parts, consumer products, education, and hospitals. He is also responsible for TS 16949 inclusive of upgrades from QS 9000, training in core areas- APQP, PPAP, FMEA, SPC, MSA, Control plans, Value stream mapping, Continual improvement, waste reduction, process audits, CAPA, vendor development, conduct of seminars on Waste reduction, Six sigma, and development of quality management systems for Colleges. |
|||
Years | Employer | Title | Department |
Years: 2005 to 2005 | Employer: Undisclosed | Title: Consultant | Department: Undisclosed |
Responsibilities:He worked on a 10 day assignment as consultant for fixing of score card for each process area. |
|||
Years | Employer | Title | Department |
Years: 1979 to 1994 | Employer: Undisclosed | Title: Dean Mechanical Engineering | Department: Undisclosed |
Responsibilities:Responsible for development of the college, laboratory, lesson plans, modules, training of students, industry-institution interaction, conducting seminars, industrial consultancies, conduct of tests and assignments, developing all laboratories- Mechanical testing, material testing, fluid machinery, instrumentation, heat transfer, production processes, machining, workshops, welding |
|||
Years | Employer | Title | Department |
Years: 1969 to 1994 | Employer: Undisclosed | Title: Works Director- Owner | Department: Undisclosed |
Responsibilities:He is totally responsible for new product development, design, manufacturing, marketing, reverse engineering, development of customer base, customer satisfaction surveys, and non-conformance management |
|||
Years | Employer | Title | Department |
Years: 1968 to 1969 | Employer: Undisclosed | Title: Works Manager | Department: Undisclosed |
Responsibilities:Development of new processes, design of machineries, fixtures, work flow optimization |
|||
Years | Employer | Title | Department |
Years: 1962 to 1968 | Employer: Undisclosed | Title: Foundry Manager | Department: Undisclosed |
Responsibilities:Erection, start of manufacture of Aluminum die casting and forgings, process management, development of dies for new products |
|||
Years | Employer | Title | Department |
Years: 1960 to 1962 | Employer: Undisclosed | Title: Executive Trainee | Department: Undisclosed |
Responsibilities:He is trained for foundry, die design, product design, die manufacturing, laboratories- chemical, engine testing, development and quality control |
|||
Years | Employer | Title | Department |
Years: 1958 to 1959 | Employer: Indian Institute of Science, Madras, India | Title: Undisclosed | Department: Mechanical Engineering |
Responsibilities:Start of institution, development of laboraties, hiring of personnel |
International Experience
Years | Country / Region | Summary |
---|---|---|
Years: 1958 to 1960 | Country / Region: Germany | Summary: He is trained for starting manufacturing plant in India for manufacture of pistons- foundry, forge, laboratories, die design and making, erection of machinery |
Years: 2005 to 2005 | Country / Region: USA | Summary: Development of objectives and documentation for ISO 9000 and score card measures |
Years: 1975 to 1975 | Country / Region: Sri Lanka | Summary: Assembly process optimization |
Career Accomplishments
Associations / Societies |
---|
He is Member of Institute of Engineers India, Associate member of Institute of Indian Foundrymen. |
Licenses / Certifications |
---|
ISO 9000 Lead auditor; QS 9000 Second party assessor |
Publications and Patents Summary |
---|
He has published 18 papers in various educational institution magazines, conducted seminars on Waste reduction and Six sigma implementation. |
Additional Experience
Expert Witness Experience |
---|
Expert witness for quality system audits of performances in industries |
Training / Seminars |
---|
Seminars on Waste reduction; Six sigma implementation Training given on: Mistake proofing, APOQP, SPC, Internal auditing, Management review meetings, CAPA, FMEA, PPAP, Control plans, process, product and system audits to ISO 9000, QS 9000, TS 16949, Continual improvement, 5S, |
Vendor Selection |
---|
Selected vendors by initial survey, questionnaire design, analysis, audits, training and development, corrective action requests tracking, guidance and improvement, training on APQP, PPAP, SPC, improved vendors performance to 100ppm, just in time supplies |
Marketing Experience |
---|
Reduced development time, translated customer changes effectively, done customer needs analysis |
Other Relevant Experience |
---|
As Professor and Dean trained several groups for industry-institute interaction. Developed management systems on time with different mindsets of personnel |
Language Skills
Language | Proficiency |
---|---|
English | He is highly skilled |
German | He is skilled |
Kannada | He is highly skilled |
Hindi | He is highly skilled |
Fields of Expertise
industry standard, international standard, ISO 9000 series quality system standard, ISO standard, Malcolm Baldrige National Quality Award requirement, metal heat treatment quality control, new product development, product development cycle time, rapid product development, QS-9000 quality system requirements, supplier quality engineering, vendor quality auditing, quality engineering, quality auditing, quality control, quality standard, management representation, advanced product quality planning, automotive transportation, new consumer product development, ISO 9660, ISO 9000-3, acceptance test, acceptable quality level, quality evaluation, ISO 9004, ISO 9003, ISO 9002, benchmark, ISO 9001, engineering standard, metal-related quality control, acceptance sampling, device product development, new product development management, equipment standard, measurement standard, device standard, materials standard