Expert Details
Intel CPU PCB Automated Packaging Wafer Laser Saw, Pick and Place, Lid Attach, Laser Mark, Test
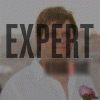
ID: 733813
Arizona, USA
Intel and Humana automation engineer offers a 15-year record of installing and supporting 20 PLC automated tool sets including and 100,000 script per day Humana Pharmacy. Software Hardware and process support for QMSI Pharmacy software, Soft PLC and Siemens PLC.
CORE STRENGTHS
Siemens PLC- Fab tool owner – Sub fab facilities install – Preventive maintenance engineer -EPA _RICRA - FMEA -R&D - DOE - Minitab - JMP - CAD - Lean Manufacturing - Six Sigma - Capital Equipment Supplier Management
*Career Note: Prior professional experience includes: Analytical Chemist at Nevada Nuclear Test Site, Kachina & Tucson water, LCD on Wafer Engineer at Three-Five Systems and service in the US Army.
Education
Year | Degree | Subject | Institution |
---|---|---|---|
Year: | Degree: BS | Subject: Chemical Engineering - INTEL STATISTICS & HUMANA SIX SIGMA BLACK BELT TRAINED | Institution: UNIVERSITY OF ARIZONA |
Work History
Years | Employer | Title | Department |
---|---|---|---|
Years: 2016 to Present | Employer: Undisclosed | Title: Nano Particle Dispersion Engineering Manager | Department: |
Responsibilities:• Managed technicians and HVM process, Installed tools and facilities, scaled up pilot process, set production schedule, managed budget, capital equipment selection, passed ISO 9000 audit, performed DOEs, and setup long term stability monitors.• Implemented process work instructions, maintenance schedule, SPC charts, FMEA, Gauge R&R, and capital equipment improvements for HVM dispersion startup lab producing catalytic converter Nano chemical dispersions. |
|||
Years | Employer | Title | Department |
Years: 2015 to 2016 | Employer: Humana Mail Order Pharmacy Engineering | Title: Automated Manufacturing HVM Project Engineer | Department: |
Responsibilities:• Installed and managed software and hardware for a 100,000 order per day automated packaging assembly line. Setup second 25,000 order per day automated packaging assembly line.• Edited QMSI, C++, & SQL control software to balance the automated packaging line to double production rate. |
|||
Years | Employer | Title | Department |
Years: 2000 to 2015 | Employer: Intel Semiconductor | Title: Tool and Process Engineer | Department: |
Responsibilities:• Installed, qualified, and white-papered 50 thin film metrology tools in under a year in Intel’s fastest start up. Met strict construction and certification deadlines in a highly ambiguous 8-billon dollar accelerated fab construction environment.• Intel Tool owner in die attach, laser mark, ball attach, and heat sink attach, diffusion; participated in supplier runoff, second source selection and VF deployment of new capital equipment and materials. Transferred pilot process to overseas HVM site under tight timelines, enabling ten generations of Intel CPU production. • Expertly managed 500 New Die Prep Product Introductions (NPIs) and supported engineering and manufacturing as SPOC for lot disposition, SPC, DRB, and process or automation issues. Reduced R&D costs by $2MM per year. • Lead a team for Intel NPI Lean Manufacturing engineers focused on floor support resulting in significantly improved key indicators within a year, including doubling NPI starts and speed through factory, cutting excursions 50%, and reducing unscheduled holds 4X.. • Design, coordinate, and execute DOEs to optimize process window for robustness against incoming variation in order to meet product yield goals within critical deadlines for next generation of 20 die prep tools. • Responsible for Statistical Process Control Systems (SPCS) and failure mode engineering analysis (FMEA). Across the Die Prep/Laminate Laser Mark/Lid Attach modules. Quality management (QCQA) owner for the Heat sink area and leveraging multi-functional team support to resolve process and inline metrology issues. |
|||
Years | Employer | Title | Department |
Years: 1998 to 2000 | Employer: Raytheon Missile Systems | Title: Conformal Coat/SMT Materials & Process Engineer | Department: |
Responsibilities:• Facilitated the merger and transfer of Raytheon Texas Instrument HARM factory operation from Dallas to Tucson with only five days of down time.• Maintained conformal coating, adhesive, and conductive coating work instructions for 800 formulations and managed migration of 15,000 materials line items into new material HASS database. |
|||
Years | Employer | Title | Department |
Years: 1997 to 1998 | Employer: Sumco Wafer Foundry | Title: Facilities Engineer / QA Engineer | Department: |
Responsibilities:• Monitored cost and performance effectiveness/efficiency of chemical, water, and waste water facilities.• Monitor all wafer foundry and CMP processes with SEM, FTIR, GC, ICP-MS, KLA, and SRM,. |