Expert Details
Injection Molding Thermoplastics, new product development, material call outs, process de-bug
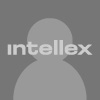
ID: 725239
Texas, USA
He has over 25 years hands on injection molding experience and for the last 6 years he has been sharing his wealth of knowledge with others as a consultant. There was a time when material suppliers offered extensive technical support to their customers but those days are gone and that's where he comes in to fill that hole left by material suppliers. He has a proven track record in helping customers with all aspects of their injection molding operations. Others may tell you "what you should have done" but he has been on the shop floor and he knows the word is "make it work" so he can help you with real world solutions to your issues using the tools you have to work with.
He has called out numerous plastic materials for medical products in the fields of, opthamology, gynaecology, insulin delivery infusion sets, laser eye surgery, ENT devices, child berthing as well as numerous hospital equipment housings.
He helps designers make "Molder Friendly" products. He can help your designer by adding his knowledge of plastics behaviour to the design process so plastic "No No's" are found early in the process and resolved.
He traveled to main land China where he spent 2 weeks working with a tooling company trouble shooting a 6 mold package that had stalled and could not meet qualification requirements. He was able to work with the Chinese and get the package qualified and the tools are now in service making medical products currently being sold world wide.He helped a medical packaging company that was having delivery problems due to high scrap rates start-up an injection molding operation so they could bring their outsourced molded products in house to have better control over delivery. I called out all of the equipment, installed it and built a clean room around it. One of the major components for this company was plagued with a 30 % scrap rate which lead to bring it in house. Through tooling modifications and processing he was able to reduce the cycle time by 50% while reducing scrap to under 1 %. The company was so pleased with the results he was offered a partnership in the company.He helped an ENT doctor develop a new product for his medical specialty that had been on the drawing board for 10 years plagued with failures. He was able to prove to the doctor that the root cause was in the plastic that had been chosen by a material vendor and not what he had thought it was for many years. He was able to find the solution where many other industry leaders had failed. The doctor now has working models of his product and has been awarded a grant to conduct 4 clinical trails. He called out the material for a new product for which the material was a break it or make it proposition. The material for the product needed to repel water but have an affinity for human proteins. This was cutting edge new technology for which he has a U.S. patent pending. With out a material that possessed these unique, previously undiscovered properties the product would not exist.He helped a mid sized captive clean-room molder keep from losing there one and only contract with Abbott Labs due to high rejects and delivery issues. He was hired to be the technical liaison between the molder and Abbott to instill a comfort level in Abbott that the skills needed to resolve the issues were being put in place. He developed new procedures across the board from P.M. schedules to QA criteria. He inspected molds and called out needed repairs. He developed new machine independent processes for all tooling and provided training in maintaining them. This was an eight month 12 and 16 hr days knock down drag out project but one of his most rewarding. The contract was saved and the company was later bought out by a large injection molding conglomerate.
Education
Year | Degree | Subject | Institution |
---|---|---|---|
Year: 1993 | Degree: Apprenticeship | Subject: Plastics Engineering | Institution: NA |
Work History
Years | Employer | Title | Department |
---|---|---|---|
Years: 2002 to Present | Employer: Undisclosed | Title: Injection Molding Consultant | Department: |
Responsibilities:He is a consultant to the injection molding industry |
|||
Years | Employer | Title | Department |
Years: 2000 to 2002 | Employer: PM&T | Title: Production Manager | Department: Molding |
Responsibilities:To oversee and manage the injection molding department |
|||
Years | Employer | Title | Department |
Years: 1998 to 2002 | Employer: Nupak Medical Inc. | Title: Molding Manager | Department: |
Responsibilities:Over see all molding and engineering activities of the company. Held % of company. |
|||
Years | Employer | Title | Department |
Years: 1992 to 1997 | Employer: GW Plastics | Title: Molding Manager / Technical Liaison | Department: |
Responsibilities:Plant start-up, oversee molding operation. |
|||
Years | Employer | Title | Department |
Years: 1989 to 1992 | Employer: Augat Altair | Title: Process Engineer | Department: |
Responsibilities:Develop molding processes for a Tier 1 automotive supplier. |
|||
Years | Employer | Title | Department |
Years: 1986 to 1989 | Employer: Sherwood Products | Title: Shop Supervisor | Department: |
Responsibilities:Oversee molding operation. |
|||
Years | Employer | Title | Department |
Years: 1982 to 1986 | Employer: Tex-Tek Plastics | Title: Process Tech. | Department: |
Responsibilities:Develop and maintain injection molding processes. |
International Experience
Years | Country / Region | Summary |
---|---|---|
Years: 1992 to 1997 | Country / Region: Mexico | Summary: He worked as technical liaison between US molder and Tier 1 automotive suppliers in Mexico. |
Years: 1992 to Present | Country / Region: Canada | Summary: He has done consulting for numerous Canadian companies. |
Years: 2005 to Present | Country / Region: China | Summary: He has dealt with several mold builders and molders in China as a consultant to U.S. based clients. He has traveled to main land China as a molding consultant. |
Career Accomplishments
Associations / Societies |
---|
Society of Plastics Engineers Senior Member since March 1991 |
Publications and Patents Summary |
---|
He currently holds Seven U.S. and international patents as inventor for medical devices he developed for customers. |
Additional Experience
Training / Seminars |
---|
He is a certified trainer for G.E.'s "Share the Knowledge" plastics training program. He has developed numerous custom technical training programs including class room and press side training courses tailored to a clients needs. |
Vendor Selection |
---|
He has been involved with four plant start-up operations. He has called out primary and secondary processing equipment along with material drying, reclaim and conveying systems. He has called out materials for numerous new medical, housewares, and sporting goods products for some of which he was awarded a U.S. patent. He has managed outsourced tool builds in the states and off shore. He has traveled to main land China where he helped salvage a multi tool package that was having trouble being qualified. |
Marketing Experience |
---|
He will not inundate you with industry buzz words that are hot today and passe next year. He says having a "Black Belt" doesn't make you a molding expert. You cannot replace decades of training with a few seminars. He has read the "Book" but through his experience he understands that parts and molds are not always by the book so to make these work you need an understanding of how plastics behave on a molecular level so you can manipulate them to achieve the desired result. In 1985 he spent two weeks working directly with Rod Groleau now founder of RJG Inc.. and John Bozzelli at a Dow plant in Michigan proving out their new theories which later became known as "Decoupled Molding" and John Bozzelli's "Scientific Molding" before these terms were even coined and have been using, refining and teaching these techniques ever since. |
Other Relevant Experience |
---|
He understands that you can't always build a new tool or redesign the part or buy a new molding press to solve your issues so drawing from his many years of hands on experience he provides you with real world solutions to existing problems as well as insure your new projects are done right the first time. |
Fields of Expertise
design review, process engineering, injection molding, polymer selection, medical polymer selection, plastic product development, thermoplastic material selection, medical polymer molding, polymer selection for chemical compatibility, elastomer selection, inventory control system, granular plastic, manufacturing troubleshooting, design for cost, manufacturing process development, plastic molding, device product development, design for manufacturability, design for assembly, new product development, design for manufacture and assembly, product design, control process, double-shot molding, production engineering, innovation, production management, production control, plastic injection molding, manufacturing, engineering thermoplastic