Expert Details
Human Factors (Industrial Equipment)
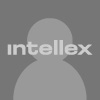
ID: 725954
New Mexico, USA
As the U.S. Air Force moved toward the replacement of cathode ray tubes with flat panel, discrete element technology in the cockpits of advanced fighter aircraft, two important questions about the ability to read information from these displays needed answers: (1) what dot-matrix font was least susceptible to discrete element failure (a common problem with the technology) and (2) what were the effects of multiple imaging during conditions of cockpit vibration?
The first question was answered using tachistoscopic methodology to develop a degradation-resistance font. The second question was answered by lashing a pilot and display to a vibration table and shaking the bejeebers out of them.A citrus juice processing plant was renovated during which time the labor-intensive, mechanical control system was upgraded to a computerized operation. Because the operators of the "old" system were also to be the operators of the "new" system, it was critical to get their input as to control actions and display formatting.
Through open-group, criteria definition reviews and structured, one-on-one interviews with the operators, a control and display protocol was developed. And because the "squeezing season" began immediately following equipment installation, the operational protocol had to be—and was—instantly adopted by the operators.As weapon systems were becoming more automated, the U.S. Army was interested in reducing the size of the crew of the M1A1/2 Abrams main battle tank.
By studying the operational requirements of the vehicle/weapon system, a reclassification of the jobs as well as cross training the crew and reassigning their duties as a function of situational circumstances showed that crew size could be reduced with no sacrifice to efficiency or compromise to safety.A newspaper publisher was building a new press room in which a robotic system was being installed to automate the paper roll handling task. At the time, paper roll handling was an entirely manual process so there was a need to incorporate the knowledge of how the current system worked with the new technology to be employed.
Through directed questioning of both current paper roll handlers and the pressmen, whose job it was to keep paper passing through the presses, interactive displays were developed that kept the presses rolling with significantly less down-time and using fewer workers than in the old press room.A laser-based, automotive wheel aligner was developed for a major automotive service retailer. It was determined to use interactive displays to assist mechanics in setting alignment limits and tolerances. How that interaction was to occur was at issue.
Through several iterations of human factors requirements reviews with design engineers, operators and owners of alignment businesses, a design that incorporated near fool-proof, error-free protocols to input manufacturers' specifications was developed. At the same time many nagging operational problems of current models were eliminated.
Education
Year | Degree | Subject | Institution |
---|---|---|---|
Year: 1973 | Degree: PhD | Subject: Cognitive Psychology | Institution: Iowa State University |
Year: 1972 | Degree: MS | Subject: Experimental Psychology | Institution: Iowa State University |
Year: 1968 | Degree: BA | Subject: Psychology | Institution: California State Unniversity, Fullerton |
Work History
Years | Employer | Title | Department |
---|---|---|---|
Years: 1990 to 2008 | Employer: Applied Psychology (self-employed) | Title: Principal | Department: |
Responsibilities:Working as an independent consultant, Expert helped technical professionals understand and integrate fundamental psychological principles for efficient and safe equipment design. He also consulted with middle- and senior-level managers in the application of fundamental psychological principals to the solution of real-world business issues. |
|||
Years | Employer | Title | Department |
Years: 1982 to 1990 | Employer: FMC Corporation | Title: Behavioral Sciences Group Leader | Department: |
Responsibilities:As an in-house consultant, Expert worked closely with company engineering staffs on dozens of projects to assure that new products and new process systems could be efficiently operated by the ultimate users.He also developed and completed a company-wide engineering management audit where shortcomings to management practices were identified and modifications were recommended to improve engineering efficiencies. Moreover, he initiated, designed, implemented, and managed a quarter-million dollar innovation program which resulted in product and process innovations worth many times that to the company. |
|||
Years | Employer | Title | Department |
Years: 1977 to 1982 | Employer: Harris Corporation | Title: Human Factors Group Leader | Department: |
Responsibilities:Expert was responsible for enhancing the performance of electronic systems by capitalizing on the capabilities and mitigating the shortcomings of human operators. |
|||
Years | Employer | Title | Department |
Years: 1974 to 1977 | Employer: Bunker Ramo Corporation | Title: Senior Psychologist | Department: |
Responsibilities:Expert was responsible for the psychological evaluation of emerging electronic display technology. Working in the Flight Dynamics Laboratory at Wright-Patterson Air Force Base, his research addressed pilot performance using advanced display technology. He also supervised in-house laboratory and simulation studies, and represented the Air Force in consultation with other firms working under the Advanced Development Program. |
Additional Experience
Expert Witness Experience |
---|
Expert conducted laboratory, field and library research in support of litigation cases involving support construction, mining and lawn care equipment. |
Training / Seminars |
---|
Expert has prepared and delivered on-site, human factors training courses. |