Expert Details
Grinding Processes and Technology, Power Tool Accessories Testing and Manufacture
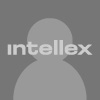
ID: 723715
Texas, USA
The expert has experience in material handling equipment linked to and from grinding machines. This material handling equipment is controlled by the machine plc and there maybe de-magnetiziers and post process gauge systems included.This equipment ensures a hands off approach for loading and un-loading workpieces.
Manufacturing specifications applied to bearings help ensure that the "book" performance of a given bearing in an application is achieved. The theoretical performance can be enhanced dramatically by the grinding and super-finishing processes by changing the surface topography of the machined surface. The expert understands fully the required process parameters to produce specific surface properties using the process kinematic parameters and the influence of the grinding wheel specification and coolant type. Surface properties include integrity and topography.
The Expert has "hands-on" experience with this type of grinding equipment from his apprenticeship years. He has used this type of equipment in manual and CNC modes to produce full form products that include internal and external surfaces. He is most familiar with Jones and Shipman machines. Materials ground include soft and hardened metals, hard chrome plate, tool steels and carbide.
High-rate center less grinding was the subject of the experts PhD thesis. The Expert is fully familiar with plunge and through feed center less grinding modes. He has extensive knowledge regarding setup parameters to produce optimally round parts with no thermal damage. The Expert has produced kinematic models that predict the idealized undeformed chip thickness for given geometric and kinematic conditions. He also understand the geometric and kinematic conditions that cause work piece waviness often referred to as "chatter". Part sizes ground vary from micron size up to 14" in diameter. He was responsible for instrumenting the machine to measure grinding forces and was able to build a data base that reflected material characteristics based on steel composition and hardness from the grinding forces.The Expert used diaphragm compensated hydrostatic bearings for both grinding and control wheel spindles and experimented with grinding wheel speeds up to 24,000 sfpm.
From research experiences both in academia and industry the expert quickly identified properties in machine tools that produced accurate quality parts in the shortest cycle times - important for high volume commodity markets. The expert can work with designers to produce optimal features to produce machines that exhibit high stiffness, long life in moving parts and if necessary a wide variety of sensor technology. The expert advocates hydrostatics where ever possible. He has a solid understanding of dressing systems and high frequency spindle technology. The expert worked with CGRD at UCONN and Bryant Grinder Corporation to design and build an outside diameter grinding machine that runs at 50,000 sfpm. This is a documented NSF project.
To achieve the required part quality in grinding process it is important to have precision balanced rotating elements. Some balance can be achieved through manufacturing rotating elements to tight specification. However, after the components are put into assemblies there will be a residual unbalance. Dynamic balancing is necessary to deliver the final balance level tolerable. The expert has used manual balancing techniques using vibration sensing equipment and has used automatic balancing equipment that becomes integral with the spindle design. Mass addition and subtraction techniques have been used.
Characteristics required in grinding equipment are also required in other types of machinery. Here the expert has directed machine designers for wood working equipment, through feed bar heat treating machines, multi-axes machining centers in addition to grinding equipment.
Machine tool qualification includes testing the assembled machine tool against a set of accuracy, repeatability and physical characteristics against machine tool specification and the actual part run-off. The Expert has written numerous machine tool specifications for several companies that include mechanical and performance requirements. He has worked closely with quality engineers to develop the statistical requirements for part dimensions and surface properties of the machined or ground workpiece.
Although a significant portion of the expert's experience has been in the bearing industry he has worked for several years in the consumer products industry. Here he was heavily involved with stamping operations, assembly, quality and broaching and forging. Throughout his industrial experience he has been exposed to TQM, TPM, Kaizens, 5S, Lean, and OPEX that embraces all of the above but includes Break Through Deployment. As a major contributor to the many programs he has been involved with, the expert has developed strong working relationships with several universities and countless vendors.
The Expert has developed grinding processes to capitalize on the use of vitrified bonded CBN wheels in a significant number of applications. More than 80% of these applications required the use of water based grinding fluids. The expert worked with the researchers a GE Super-abrasives to develop grain and bond characteristics to produce G-ratios in excess of 4000 when grinding 52100 steel in synthetic coolants. Along with developing the wheel specifications, diamond dressing systems and dressing techniques were created to extract the most from the carat cost based abrasive grain. The Expert has applied CBN to 52100, Stain-less steel, tool steels and special tool steels such as Rex 20.
Plated CBN wheel have been used where appropriate. These applications maybe short run or long small diameter bores. The excellent results obtained in applying CBN were made possible by instrumenting grinding machines and through the application of DOE.
The Expert worked for 15 plus years for The Torrington Company, America's largest broadline bearing manufacturer. Torrington is now owned by The Timken Company. During this time, the Expert was involved with all aspects of ball bearing manufacture. However, the bulk of the experience was with the actual grinding processes and associated equipment and metrology. His experience covers a wide range of product types, sizes and materials. Raceway grinding of super precision bearings requires accurate machine tools and an understanding of the super finishing process to achieve the final product specification. The Expert has worked with all classes of bearings and has even used CBN abrasives on bearing races.
The expert has recently helped build a taper roller bearing manufacturing plant from a green field site to a fully operational facility. The expert provided technical support in the following areas:- machine tool specifications, acceptance specifications, acceptance of equipment at the machine tool plant, machine tool acceptance and problem solving at the bearing factory, metrology and metallurgy training and support, the use of instrumentation to improve cycle times and grinding burn avoidance, machine health monitoring and training in grinding process and technology in the class room and on the shop floor. The expert has experience in the manufacture of taper, spherical, needle, and large diameter roller bearings. This experience encompasses both simple rollers, and optimised profile rollers.
The requirements to produce quality needle roller races are similar to those for ball bearing races. However, typically, needle roller races are not super finished. This means that the grinding process has to impart the topography required. The Expert has experience in specifying abrasives, process and machine cycles to achieve the required bearing ratio and topography through the manufacturing process.
Worked with Client to build a taper roller bearing plant from "green field" to full production. Areas of support include machinery specification, purchase, acceptance and factory install. Metrology and metallurgy equipment were identified, the purchase supported and laboratory setup completed. Cycle time reduction, burn and "chatter" elimination solutions were developed. Grinding and metrology training were provided on the shop floor and in the classroom.Resolved manufacturing issues between a supplier and their customer, Was able to suggest alternative manufacturing techniques to the supplier to avoid the discourse between them and their customer.
Trained a maintenance team to use vibration analysis equipment to identify incipient bearing failure and thus avoid scrap work on turning and machining centers.Provided 1 week seminars to a machine tool builder to advance the level of technology in his machines. 50 design engineers attend the week long program. This work was conducted off shore.Performed a factory review for a tap and die manufacturer and was able to identify multiple opportunities to reduce scrap, reduce cycle time, improve the use of MRO and implement some basic lean engineering principles, 5S and Kaisens.Currently working with an offshore bearing manufacturing company to develop their process development team, solve manufacturing issues and give technical direction to the global machine tool design team.Provided expert witness technical support in resolving several personal injury cases that involved grinding equipment.
Education
Year | Degree | Subject | Institution |
---|---|---|---|
Year: 1983 | Degree: PhD | Subject: Mechanical Engineering | Institution: Liverpool John Moore's University |
Year: 1977 | Degree: BSc | Subject: Mechanical Engineering | Institution: Liverpool John Moore's Universtity |
Work History
Years | Employer | Title | Department |
---|---|---|---|
Years: 2011 to Present | Employer: Undisclosed | Title: President | Department: Undisclosed |
Responsibilities:Expert provides technical support to the bearing and tool manufacturing companies that need help with implementing Operational Excellence philosophies. Full support in grinding processes and technologies are core competencies. |
|||
Years | Employer | Title | Department |
Years: 2005 to 2010 | Employer: Undisclosed | Title: Owner | Department: Undisclosed |
Responsibilities:Responsible for product design, sourcing, testing, sales and marketing.The Expert has provided technical consultancy to a Fortune 500 Broad Line Bearing Company. The work involved the Expert developing multiple technical specifications for a variety of grinding, super-finishing and fine grinding machine tools. These specifications were written to take advantage of the latest technology from both domestic and international machine tool vendors. |
|||
Years | Employer | Title | Department |
Years: 2002 to 2005 | Employer: Undisclosed | Title: Director of Engineering and Technology | Department: Undisclosed |
Responsibilities:The expert was responsible for driving manufacturing technology in the production plants located in the USA, China and New Zealand. The objectives were to overhaul the processes, the technology and introduce OPEX. (Operational excellence). Additionally, the Expert was responsible for developing the product testing facility that included metallurgy, metrology, rapid proto-typing equipment and custom built test equipment. |
|||
Years | Employer | Title | Department |
Years: 2000 to 2002 | Employer: Undisclosed | Title: Vice President | Department: Undisclosed |
Responsibilities:The Expert was responsible for all engineering group activities including R&D, design, model making and rapid proto-typing, testing, legacy documentation and project management. Instigated the shortest time to launch a new product by concurrent engineering and project management. |
|||
Years | Employer | Title | Department |
Years: 1990 to 2000 | Employer: Undisclosed | Title: Corporate Consultant | Department: Undisclosed |
Responsibilities:The expert was responsible for introducing new grinding processes and technology the company's broad line bearing manufacturing facilities both domestically and internationally. Considerable experience was gained dealing with Chinese and European groups.The Expert directed many of the companies funded projects at UNCONN's Center for Grinding Research and Development. A similar function was performed with the MARC Center at Georgia Institute of Technology. Several PhDs and MS degrees have been supervised in conjunction with the academic faculty. The Expert also worked on Department of Defence contracts for Electric Boat. |
|||
Years | Employer | Title | Department |
Years: 1985 to 1990 | Employer: Undisclosed | Title: Group Leader | Department: Undisclosed |
Responsibilities:Managed a group responsible for developing the technology and process knowledge to implement CBN, and other abrasives in state of the art grinding equipment. Developed a variety of training materials during this time.Worked closely with UCONN to develop the Center for Grinding Research and Development. Also provide industrial support to the Manufacturing Research Center at Georgia Institute of Technology. |
|||
Years | Employer | Title | Department |
Years: 1977 to 1985 | Employer: Undisclosed | Title: Research Associate | Department: Undisclosed |
Responsibilities:During the period leading to the award of the PhD, the Expert was responsible to teaching duties including metallurgy, metrology, fluids, engineering design and manufacturing science.The Expert supervised the daily work of 2 PhD candidates. |
|||
Years | Employer | Title | Department |
Years: 1969 to 1973 | Employer: Undisclosed | Title: Student Apprentice Toolmaker | Department: Undisclosed |
Responsibilities:The Expert trained as a toolmaker. During this time the Expert was exposed to turning, milling, heat treatment, precision surface, cylindrical and optical profile grinding. Expert completed the apprentice program prior to going to University. |
Government Experience
Years | Agency | Role | Description |
---|---|---|---|
Years: 1994 to 1996 | Agency: NSF | Role: Contributor | Description: Industry, Academia and an end user of grinding equipment teamed up to develop a radically new high precision grinding machine funded by NSF. The Experts role was as programme manager representing the enduser. |
International Experience
Years | Country / Region | Summary |
---|---|---|
Years: 1996 to 1996 | Country / Region: Wuxi China | Summary: Performed a technology and people review for a European company considering purchasing a Chinese Bearing Manufacturer. |
Years: 2000 to 2000 | Country / Region: Wuxi China | Summary: Presented a seminar to a machine tool builder on the latest technologies found in current machine tools and spindle technology. 50 people attended. |
Years: 2005 to 2005 | Country / Region: Shenzhen China | Summary: Directed a team of Chinese engineers to identify the cause of inconsistent hardness in through feed induction heat treated bar stock. When the problem was isolated the Expert identified process improvements and controls to prevent the problem from reoccurring. |
Years: 2003 to 2004 | Country / Region: New Zealand | Summary: Provided grinding support and advice for carbide grinding. Identified cycle time reduction opportunities and corrective actions to eliminate part defects. |
Years: 2011 to Present | Country / Region: Suzhou China | Summary: Defined equipment, layout, equipment specifications, acceptance plans, supported equipment acceptance and install into factory, developed cycles, trained operators and technicians and continue to support a new taper roller bearing venture. |
Years: 2014 to Present | Country / Region: Yeongju-Si, ROK | Summary: Grinding Consultant, bearing industry |
Career Accomplishments
Associations / Societies |
---|
Member of the Institution of Mechanical Engineers Member of the Institution of Engineers and Technology |
Licenses / Certifications |
---|
Chartered Engineer - C.Eng. |
Awards / Recognition |
---|
Sir Ben Williams Award for best technical paper presented to the NW Regional Council for the Institution of Production Engineers. |
Publications and Patents Summary |
---|
The Expert has 26 publications associated with grinding processes, grinding technology, tribology and sensor technology related to grinding. Additionally, the Expert as multiple trade secrets associated with manufacturing or bearings. |
Additional Experience
Expert Witness Experience |
---|
Expert witness services have been provided for bearing failure issues, personal injury when using grinding equipment, trade secret theft and property damage due to grinding equipment usage. The expert has provided research data and appeared for depositions. Court appearances are pending. Additionally,experience has been derived from acting as the technical consultant for his employer when questions about supplied products have manufacturing deviations or there is a perceived deviation. In this role the Expert was expected to act independently from the employer and provide an acceptable solution to the grievance that all parties could support. As lab manager, the Expert has had to provide to Corporate Lawyers failure analysis reports indicating the mode of failure and likely scenarios that could lead to such a failure. |
Training / Seminars |
---|
The Expert has developed a variety of training programs and presentations for inhouse training of machine operators and manufacturing process development engineers. This material includes most aspects of precision grinding for both easy and difficult to grind materials using super and conventional abrasives. A novel pocket reference for grinding equations and initial guidelines was also written. A course for vibration analysis specifically for the bearing industry was developed and presented multiple times. |
Vendor Selection |
---|
The Expert has extensive experience in developing machine tool specifcations for grinding and superfinishing machines and has worked with most of the leading machine tool manufacturers that supply this type of equipment. The specifications focus on the technology and are not part specific - this means that the equipment can be purchased based on the ability to meet a specification and not part acceptance requirements which may or may not be stringent enough. In addition to machine tool vendors, the Expert has built over the years relationships with grinding wheel manufacturers, abrasive manufacturers, coolant and coolant system suppliers and diamond roll designers and manufacturers. The Expert frequents vendors through outthe world to determine current trends in grinding processes and technology. Finally, the Expert also has a strong relationship with laboratory equipment manufactures. |
Marketing Experience |
---|
The Expert has worked with the Marketing Groups at each company he has been employed in and has been an active participant in PDR reviews, end-user testing and Focus Groups. Knowledge gained from these feedback mechanisms was integrated into the products. Most recently, the Expert was involved in bringing multiple products to market at a large consumer product company where time to market could be as short as 4 months and as long as 1 year. |
Other Relevant Experience |
---|
Working with a US manufacturer, the expert supported the building of a bearing manufacturing plant in China. His manufacturing expertise was used in the machine acceptance area, equipment specification and supplier identification, process training for grinding, metrology and metallurgy.Use of instrumentation and theoretical analysis tools were demonstrated. The Expert has provided consulting services to spindle repair companies, bearing manufacturers and machine tool builders, domestically and internationally. |
Fields of Expertise
52100 steel, antifriction bearing, ball bearing manufacturing, automated machinery, ball bearing manufacturing specification, center grinding, centerless grinding, grinding machine design, internal grinding, machine-tool component balancing, machine-tool design, machine-tool qualification, process engineering, cubic boron nitride, ball bearing, bearing race, roller bearing, roller bearing manufacturing, brazed carbide, airframe fatigue, tooling, grinding operation facility design, bearing temperature, bearing material, bearing application, machine shop, lead time, synthetic diamond, tool grinding machine, machine-tool runoff, machine-tool lubricant, grinding stress, saw (tool), metal drilling, bearing lubrication, sintered bearing, centerless grinder, end mill, blade grinding, grinding efficiency, machinery lubrication, grinding fluid, precision machine tool, non-contact bearing, coating machinery, machinery design, high-speed spindle, machine-tool tooling process, grinding (machining), bearing life, machinery selection, tooling specification, wet milling, rolling element bearing, numerically controlled machine tool, cutting, lubrication process, bearing selection, attrition, abrasion, surface, vibration testing, acoustic emission sensing, machining jig, production engineering, machinery, split bearing, machine, material wear, machine vibration analysis, tool and die making, radial bearing, precision engineering, surface polishing, metal machining, metal cutting, magnetic bearing, journal bearing, hydrodynamic fluid film bearing, gas bearing, diamond grinding, cutting tool, air bearing, metal abrasive wear