Expert Details
Glass Container Production
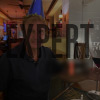
ID: 737287
United Kingdom
He previously held various key roles at Ardagh (Glass) including Plant Manager, Operations Manager, Engineering Manager, Technical Director, and latterly European Operational Excellence Group (OEG) Roles.
In 2020, Expert finished working full-time with the Ardagh (EU) after more latterly working with the Operational Excellence Group (OEG) and with the 20 Ardagh plants in Europe establishing Best Practices in Glass Container Forming. Additionally working on continuous improvement methods to improve productivity and quality in the glass container forming process, applying a six-sigma approach wherever possible.
Together with the input from all Ardagh (EU) Glass Container Forming departments, he implemented and integrated an online glass container fault correction database to list standard defect causes and corrective actions (approximately 2,500 cause/action combinations registered). This is now used as a standard system in the Ardagh Production System and data is now being used to identify trends and improvement opportunities.
Other projects include production performance benchmarking approach development, simplifying six sigma for use at the hot end (now adopted by other departments), swabbing standardization (based on test-study results), mold-gear coatings testing and assessment, and leadership of various plant/line Production Performance Improvement projects as identified by Senior Management.
In the recent past, Expert won the Ardagh Global 'BSafe!' Award for Personal Contribution to Safety. This was for safety improvements made at the Hot End. Safety projects included reducing implementation of standard swabbing equipment and procedures to reduce swabbing injuries to zero over the previous 8 years in over 20 European plants; 26 Forming safety best practices established, and latterly the development of mechanical IS Machine section-safety devices which were in the plant-implementation phase as he left the company for retirement.
Available for glass container production consultancy roles, or short problem-specific consultation sessions.
Based on his experience outlined above, Expert is now offering to help a wide range of businesses and individuals connected with the glass container industry. This would include, but not be limited to:
- Glass container manufacturing plants with specific problems to solve, or which may benefit from general plant operational audits to identify possible improvement opportunities.
- Customers of glass plants with issues arising that cannot be readily resolved with the supplying glass plant, or who need proactive quality/operational audits to give assurance that there is no significant product quality risk from their chosen source of glass container supply.
- Complainants of faulty glass products that need Expert Witness input in order to resolve their cases.
- Developers of glass plant equipment who would benefit from glass-expert input at key stages of their product development cycle.
- Glass Plant Safety audits as this of increasing concern for what has traditionally been a challenging environment, especially in the 'hot end' of the process.
Education
Year | Degree | Subject | Institution |
---|---|---|---|
Year: 1996 | Degree: MSc | Subject: Manufacturing & Management | Institution: Sheffield University |
Year: 1988 | Degree: BEng | Subject: Electronic Systems & Control Engineering | Institution: Sheffield Hallam University |
Work History
Years | Employer | Title | Department |
---|---|---|---|
Years: 2020 to Present | Employer: Undisclosed | Title: Consultant | Department: |
Responsibilities:Offering expert assistance to companies needing help with technical matters relating to glass container production or use of glass. A major on-going consultancy role is to be part of the technical team designing the Research & Development Pilot Plant in the UK. |
|||
Years | Employer | Title | Department |
Years: 2010 to 2020 | Employer: Ardagh Glass Ltd. | Title: Forming Best Practice Manager | Department: |
Responsibilities:Establishing methods best practices and agreeing European Group improvement initiatives to be implemented in the hot end operations in European Plants. Holding workshops and conferences to discuss matters of substance and detail before voting on standard and best practices. Major initiatives led to daily acceptance of Lean Six Sigma approaches, improved safety, and implementation of a defect correction expert system used in all plants (believed most advanced of its time). |
|||
Years | Employer | Title | Department |
Years: 2009 to 2010 | Employer: Ardagh Glass Ltd. | Title: Finished Products Best Practice Manager | Department: |
Responsibilities:Establishing methods best practices and agreeing European Group improvement initiatives to be implemented in the cold end operations in European Plants. Holding workshops and conferences to discuss matters of substance and detail before voting on standard and best practices. |
|||
Years | Employer | Title | Department |
Years: 2009 to 2010 | Employer: Ardagh Glass Ltd. | Title: Group Know How Co-ordinator | Department: |
Responsibilities:Establishing methods to acquire and store manufacturing knowledge and best practices which were then rolled out across 20 European plants. System still in use to this present day and continually being updated by team members of the Operational Excellence Group. |
|||
Years | Employer | Title | Department |
Years: 2008 to 2009 | Employer: Ardagh Glass Ltd. | Title: UK Director of Technical Services | Department: |
Responsibilities:Managing the Technical Centre for UK until UK unit was amalgamated with the European team into Central Technical Services. Planning furnace rebuilds and other major plant capital investment programmes. Participating in Senior Management meetings to co-ordinate daily work with company strategy and business direction. |
|||
Years | Employer | Title | Department |
Years: 2006 to 2008 | Employer: Ardagh Glass Ltd. | Title: Plant Director | Department: |
Responsibilities:Responsible for the Knottingley Plant and its activities to meet customer requirements and achieve planned profit performances. |
|||
Years | Employer | Title | Department |
Years: 1999 to 2006 | Employer: Rockware Glass Ltd. | Title: Operations Manager | Department: |
Responsibilities:Responsible for the day-to-day operation of the glass container manufacturing facility. Reporting direct to the Director of Operations with all production related departments reporting through Expert. Responsible for factory operational performance and success of internal continuous improvement initiatives. |
|||
Years | Employer | Title | Department |
Years: 1997 to 1999 | Employer: Rockware Glass Ltd. | Title: Assistant Production Manager | Department: |
Responsibilities:Working on the production management team to improve productivity and quality. |
|||
Years | Employer | Title | Department |
Years: 1997 to 1998 | Employer: Rockware Glass Ltd. | Title: Engineering Manager | Department: |
Responsibilities:For Plant Engineering function with team of 25 electrical and mechanical craftsmen and supervisors. Responsible for plant engineering services to the glass factory manufacturing process. |
|||
Years | Employer | Title | Department |
Years: 1990 to 1997 | Employer: Rockware Glass Ltd. | Title: Project Manager | Department: |
Responsibilities:Working on specification and installation of major capital investment projects managing teams of contractors under CDM Regulations. Annual spend circa £10M. |
|||
Years | Employer | Title | Department |
Years: 1990 to 1984 | Employer: Beatson Clark plc | Title: Electronics Engineer | Department: Production Engineering Development Department |
Responsibilities:Working on the selection, specification, installation, and maintenance of process control systems. |
|||
Years | Employer | Title | Department |
Years: 1988 to 1988 | Employer: Redfearn Glass plc | Title: Assistant Project Engineer | Department: |
Responsibilities:Worked on applying computer Expert Systems to process control. |
|||
Years | Employer | Title | Department |
Years: 1985 to 1988 | Employer: Redfearn Glass plc | Title: Undergraduate vacation work | Department: |
Responsibilities:Undergraduate vacation work and 15-month industrial placementWorked on real-time process control software commissioning/debugging, fault-finding on process control hardware, and systems' documentation. |
|||
Years | Employer | Title | Department |
Years: 1981 to 1984 | Employer: Redfearn Glass plc | Title: Apprentice | Department: |
Responsibilities:Served EITB electrical apprenticeship. |
Career Accomplishments
Licenses / Certifications |
---|
Green Belt LSS Chartered Engineer (CEng). Level V NVQ Operations Management In 1994 passed City & Guilds qualification in Communication of Technical Information (Parts 536O-1 & 536O-2) after studying by correspondence course. |
Awards / Recognition |
---|
- Travel Award from Sheffield City Polytechnic and the Armourers' and Braisiers' Company, Sheffield. - Master Cutler's prize for the best (year undisclosed) Travel Award Report. - Won IEE Institution Prize - Adagh Group Global BSafe Award in recognition of Personal Contribution to Health and Safety (Hot End Safety Improvements) |
Publications and Patents Summary |
---|
Author of articles published in Glass International magazine |
Additional Experience
Training / Seminars |
---|
EDUCATION 1975 - 198O Royston Comprehensive School: GCE 'O' level English Language (C) CSE - Maths (2) English Language (1) Physics (2) Biology (2) French (4) 198O - 1984 Barnsley College of Technology: B/TEC National Certificate in Electrical Engineering with grades of 6 Distinctions, 8 Merits and 2 Passes. 1984 - 1988 Sheffield City Polytechnic: Bachelor of Engineering (B.Eng.) First Class Honours Degree in Electronic Systems and Control Engineering. 1994 – 1997 Sheffield University MSc Manufacturing Technology & Management (passed with Distinction). |