Expert Details
Formulation of baby food & thermal processing. Aseptic processing & processing in glass
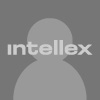
ID: 734242
Arkansas, USA
Expert is detailed, qualified, and highly ethical Manufacturing Analyst with extensive experience in the food and beverage industry overseeing operations and implementing quality process improvements. He has excellent technical, leadership, and written and verbal communications skills; innate ability to build rapport with colleagues and management to ensure efficiency and quality standards are met. Expert in formulation management control, implementing cost savings programs, and providing detailed analysis of products and manufacturing processes to provide problem resolution; diligent to succeed in company goals and dedicated to demonstrating company vision and principles.
Expert has worked extensively with converting glass baby food formulations to new and different formulations that were compatible with aseptic processing and packaging.
Formulation of both aseptic and glass baby food products
Consultant Food Marketing:
Formulation of Food & Food Process Experience- 50 years
Experience in development and introduction of new products, process and packaging (glass and plastic), continuously reviewing existing practices and processes to ensure there is product compliance to standards, continuously seeking improvement in manufacturing performance, product quality, cost, and renovation of existing products.
Develop and maintain batch record documentation system: aseptic process- electronic, non-aseptic process- manual batch record documentation: step by step control, specific instructions for each work station, each slurry/batch performed in like manner each iteration, detailed documenation relative to what ingredients and qualities formulate a completed batch.
Systematic work- flow process of how each product is formulated. Procedures- establishes a set of guidelines that instructs the operator in correct tasks for each step of the process. Training- can be used to train new employees about how to formulate products and perform the various formulation functions. Accountability- step by step procedure allows for more accurate accountability if and when a concern might arise. Inventory control- allows for improved inventory tracking.
Formula Control: perform periodic analysis and make needed adjustments relative to standards. Develop and maintain auditing/ verification system. Coordinate total solids adjustments for various products/ingredients whereby savings can be generated.
System Measurement- Yields- Cases/ 1,000 lbs. On an annual basis, coordinate the cases per 1,000 lbs. factor to the actual filler rates and modify accordingly. This is an important step as this can directly affect standard costs of individual products. If the formulation changes significantly, modification may be required prior to an annual basis. Coordinate this data with cost accounting and manufacturing.
Education
Year | Degree | Subject | Institution |
---|---|---|---|
Year: 1964 | Degree: 1967 | Subject: Chemistry | Institution: Univ. North Carolina - Asheville |
Year: 1971 | Degree: 1976 | Subject: Computer Science | Institution: Univ. Northe Carolina - Asheville |
Year: 1978 | Degree: 1982 | Subject: MBA | Institution: Western Carolina Univ. |
Work History
Years | Employer | Title | Department |
---|---|---|---|
Years: 1968 to 1998 | Employer: Gerber Products | Title: Manufacturing Analyst | Department: |
Responsibilities:Thermal processing and formulation of baby foodEnsure correct formulation of product and management of process yields including both glass and aseptic/plastic processing plants. Determine and implement various cost savings projects from plant processes. Establish sample data gathering programs in collaboration with quality assurance for raw fruits and vegetables to answer questions about usage values on a seasonal and year to year basis. Forecast and develop future standards based on annual and historical data; set standards for product usage in coordination with cost accounting. Collaborate with quality assurance, manufacturing, and warehouse departments to ensure consistency and quality standards. Quality Assurance/ Formulation Manager, Manufacturing Process Manager, Production Services Section Chief, Special Services Section Chief Quality Control, Senior/Junior Technologist Quality Control |
|||
Years | Employer | Title | Department |
Years: 1998 to 1999 | Employer: Alljuice Food & Beverage Corporation | Title: Director of Quality Assurance | Department: |
Responsibilities:Overall responsibility of Quality and HACCP for plantDeveloped and implemented a HACCP plan to comply with current juice plant HACCP regulations. Reorganized plant quality control and manufacturing functions to incorporate HACCP controls and a more structured focus.Maintained overall quality programs for entire plant. Coordinated complaint updates to consumers and corporate headquarters. Maintained technical functions and expertise for sanitation; consistently communicated with supplier sanitation representatives and various container and vendor representatives. |
|||
Years | Employer | Title | Department |
Years: 1999 to 2018 | Employer: Gerber Prods Com | Title: Quality Assurance/ Formulation Manager, Manufacturing Process Manager, Production Services Section Chief, Special Services Section Chief Quality Control, Senior/Junior Technologist Quality Control | Department: |
Responsibilities:Formulation/Thermal Processing of baby food formulations and juice formulations |