Expert Details
Europe Based Chemical Process Development: Troubleshooting, Yield, Quality, Cost Reduction
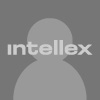
ID: 724444
Belgium
The expert will approach chemical process developments from different angles : 1. Theoretical approach : what is the process delivering vs. what is expected. 2. Troubleshooting approach: what have we learned from deviations from the expected? 3. Find creative solutions to improve the process without spending major capital. What happens if chemicals are fed concurrently rather than batch, what happens if we add water ... 4. Explore the creative solutions via design of experiments in the lab, pilot plant or industrial plant.
The expert has been course instructor on a "Deviation analysis course" . In this 2,5 day residential course, exempts and/or operators learn to systematically analyze problems. After clearly identifying the problem, the deviation is analyzed in terms of what (what not) - where (where not) - When (when not) - etc..... The expert has applied this deviation analysis process numerous times in Chemical Process Troubleshooting sessions. As ex-course instructor, the expert also knows how to control and utilize the group dynamics in such situation. The combination of using "deviation analysis”, controlling group dynamics AND 20 years of experience in chemical process development, is unique.
The expert has been course instructor on a "Decision analysis" course. In this course, the decision is split into "Musts" and "Wants". Once these are defined and quantified, the different alternatives can be scored and the "Best Balanced Decision" is identified. Before taking the decision however, a systematical Risk Analysis is done. As ex-instructor, the expert masters the art of controlling the group dynamics, a necessity in the (often emotional) decision taking process.
When evaluating the level of process control the expert uses the concept of "Quality Windows". He will quantify to what extend the process is erratic and how that contributes to the (lack of) capability of the process. Depending on the outcome, he will decide whether instrumentation and/or human control need to be improved. For improving human control, the expert will advice and lead a group of operators to a set self-made SPC rules with the emphasis on "proven stability" before further process improvements. For improving instrumentation control, the expert will identify a stable operational range via Design of Experiments.
The expert has started up a major monomer plant. He has been involved in the technology selection process, the subsequent risk analysis and risk abatement, making sure the analytical lab was capable, operator training and finally starting up the process.
The expert has been part of a "Advanced process control" team for several years. In a problematic crystallization process, he identified a particle size analyzer which was capable of measuring particle slurries of up to 30%. He subsequently determined the vital control parameters (using Design of experiments - DOE). Using the mathematical function coming out of the DOE, the on-line analyzer info could be used to control the addition of solvent which stabilized the particle size. The expert has also used process parameters (distillation temperature, pressure ...) to predict the distillation product quality. In this way, a set of parameters (temperature, pressure) was converted into an on-line analyzer.
The expert has run SPC courses for operators and has led operator teams to develop their own "process control rules". This approach ensures the total buy-in from operators. Working in the micro-electronics industry, the expert was responsible of setting "capable" specifications. The expert separated analytical variation (GR&R analysis)from process variation so that appropriate development plans could be made with the process engineers and operators AND the lab operators/instruments.
Expert can teach and apply systematic troubleshooting via the "Kepner Tregoe" style Deviation Analysis. Such analysis is done with a team of 5-10 people. The analysis is a very good technique is 2 or 3 causes jointly result in a deviation. The minimum which the team will get out of the analysis is an agreement of what the problem is + agreement on what facts are known and what facts remain uncertain. Via this analysis we once solved a "blocking rotary vacuum filter" problem, which had existed for years. The cause was a combination of operating a too high vac and too pure solvent (and hence too much evaporation).Via analysis of the crystallization mechanism in combination with using a special particle size analyzer, the expert was able to find the critical X-es in a crystallization process. Via a Design of experiments, the effect of 2 variables on crystal size was mathematically characterized. The mathematical formula was used to steer an advanced process control loop which controlled the particle size at the desired level.Via Technology Risk Analysis, the critical areas for a new plant start-up were identified. The expert assisted at the 6 weeks plant start-up, continuously verifying the quality and output of the plant at various stages.Together with a team of operators, the expert led the plant operators to agree amongst themselves how to run the process stable. Without knowing, the operators designed themselves their own version of "SPC" around the plant bottleneck.
Education
Year | Degree | Subject | Institution |
---|---|---|---|
Year: 1983 | Degree: Master of Science | Subject: Chemistry (Organic synthesis) | Institution: Leuven University |
Work History
Years | Employer | Title | Department |
---|---|---|---|
Years: 2006 to Present | Employer: Undisclosed | Title: Process consultant | Department: |
Responsibilities:The expert has been the link between the Engineering department and the Technology department. He has been responsible to lead technology risk assessments and to verify new technologies used in the modification of a Polycarbonate plant and a Polycarbonate Pilot Plant. He also documented the environmental impact of these new processes and assisted in the environmental permit procedure. |
|||
Years | Employer | Title | Department |
Years: 2003 to 2006 | Employer: JSR Micro | Title: Production Engineer | Department: |
Responsibilities:As Production Engineer in this small company the expert assumed a wide range of responsibilities from implementing new technologies (NIR, RFID ..), running Six Sigma and SPC training sessions, reducing operating cost to plant and product troubleshooting. The expert gained know how in cleanroom technology, Particle behavior and analysis, Photoresist and Developer technology. |
|||
Years | Employer | Title | Department |
Years: 2001 to 2003 | Employer: General Electric | Title: Advanced Process Control Engineer | Department: Advanced Process Control |
Responsibilities:The expert worked in the Advanced Process Control group, and implemented a new method to measure and control the particle size during the precipitation of the Poly Phenylene Oxide (PPO) polymer. |
|||
Years | Employer | Title | Department |
Years: 2000 to 2000 | Employer: University of Breda | Title: Professor | Department: Science |
Responsibilities:While working for his employer, the expert combined his job with a teacher assignment at the “Technical University” of Breda, teaching a “Polymer Processes” course. This course dealt with the theory and practice of manufacturing polymers. |
|||
Years | Employer | Title | Department |
Years: 1995 to 2000 | Employer: General Electric | Title: Process technologist | Department: Process technology |
Responsibilities:The expert worked Polycarbonate technology group, primarily working on the development of the Bis Phenol A process. He optimized the crystallization processes, improved the Ion Exchange Catalyst (and obtained the General Electric Six Sigma Green Belt certification via this project), reduced manufacturing cost and increased plant throughput. The expert built and ran test reactors. He started up a new Bis Phenol A plant in Spain and worked on a new polycarbonate polymerization process.. |
|||
Years | Employer | Title | Department |
Years: 1994 to 1995 | Employer: Monsanto | Title: Managerial Analytics Course training | Department: Training Department |
Responsibilities:The expert was trainer on the Monsanto five day residential "Managerial Analytics" course, teaching problem solving (Kepner Tregoe), decision making and action planning. He later became trainer of the future trainers for this course. |
|||
Years | Employer | Title | Department |
Years: 1984 to 1995 | Employer: Monsanto | Title: Process development Chemist | Department: Rubber Chemicals |
Responsibilities:The expert acquired a large spread of experience in lab optimization, pilot plant operation and providing plant support / troubleshooting. He used techniques such as "experimental design" and "Statistical process control" |
International Experience
Years | Country / Region | Summary |
---|---|---|
Years: 1995 to Present | Country / Region: Netherlands | Summary: Job at General Electric - later Sabic (see work experience) |
Years: 1998 to 2000 | Country / Region: Spain | Summary: Start-up of a Polycarbonate plant in Cartagena, Spain. |
Years: 1987 to 1994 | Country / Region: United Kingdom | Summary: Numerous troubleshooting and process development trials at Monsanto Ruabon, Wales. |
Career Accomplishments
Licenses / Certifications |
---|
Teacher qualification from the University of Leuven. Six Sigma Green Belt. Qualified First Aider. |
Professional Appointments |
---|
Managing director of "Zwembad BVBA". |
Publications and Patents Summary |
---|
The expert has numerous patents in the field of Rubber Chemicals, Bis Phenol Acetone, Polycarbonate. Patents can be retrieved via quick search on http://gb.espacenet.com |
Additional Experience
Training / Seminars |
---|
- The expert instructed numerous times the Managerial Analytics course: a 5 day residential course teaching troubleshooting (Kepner Tregoe), decision analysis, potential deviation analysis and action planning. - Train the trainer on the above mentioned course - Statistical Process Control - Six Sigma - Polymer processes, dealing with the polymerization mechanisms, molecular weight build-up and distribution and specific equipment used in polymerization technology. -Crystallization course - A course "Chemical Process Troubleshooting" is in preparation. |
Vendor Selection |
---|
The expert has been intensively involved in the selection of a Ion exchange Resin selection for a new Bis Phenol Acetone plant. He has also selected a solid mixing and transport system for powders. |
Marketing Experience |
---|
The expert is able to identify opportunities for yield improvement, quality improvement, throughput increase and/or cost reduction via a chemical process "audit". After completing such a process audit, he can follow-up the action plan derived from the audit. In troubleshooting the processes, he can be very systematically applying his know how in deviation analysis, six sigma etc ... . |
Other Relevant Experience |
---|
The expert can perform a patent/competitor study. |
Language Skills
Language | Proficiency |
---|---|
Dutch | Mother tongue of the expert |
French | Expert lives in the bilingual part of Belgium and speaks french daily |
Spanish | Epert has lived several months in Spain, and became fluent via self-study |
German | German is a language very close to Dutch. The expert has learned technical German via self-study |
Fields of Expertise
chemical process control, chemical process development, chemical process troubleshooting, decision analysis, manufacturing control, new chemical process operations, on-line analyzer, statistical quality control, bilingual education, advanced process control, design of experiments, QS-9000 quality system requirements, chemical process design, chemical analyzer, chemical plant operation, ISO 9000 auditing, chemical process monitoring, chemical process control instrumentation, chemical process equipment, capability study, machine capability study, measurement error analysis, data correlation, pilot plant scale-up, applied statistics, accuracy, chemical-process flow chart, chemical processing, chemical process, statistics, quality control, quality auditing, production control, manufacturing, curve fitting