Expert Details
Engineering; Plant Engineering: Construction, Renovation, Maintenance, and Operations of Industrial and Manufacturing Buildings as well as Laboratory Facilities, and more.
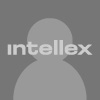
ID: 736171
Virginia, USA
Additional experience includes power generation; the printing, packaging, and converting industry; and experience with continuous manufacturing process environments.
SKILLS
• Project management
• Feasibility analysis and scope development
• Facility operations and maintenance management
• Building design, construction, and renovation
• Green building construction analysis tools and techniques
• Laboratory design, construction, and operations
• Central plant operations and maintenance
• MEP systems design, installation, and maintenance
• Precision HVAC environmental system design, installation, operations, and maintenance
• Continuous manufacturing processing and operations
Summary:
Semi-retired Professional Engineer. BSME. 40-years industrial experience in building MEP system design, installation and control. Facility Maintenance and Contract Services Management. Precision environmental control and laboratory HVAC systems design, construction, and operations.
Education
Year | Degree | Subject | Institution |
---|---|---|---|
Year: 1978 | Degree: BS | Subject: Mechanical Engineering | Institution: Louisiana Tech |
Work History
Years | Employer | Title | Department |
---|---|---|---|
Years: 2009 to 2015 | Employer: Altria Client Services | Title: Facility Manager | Department: Corporate Facilities and Real Estate |
Responsibilities:Oversee and direct the maintenance and operations of a multi-story, 500K+ gif corporate research and technology complex.Provided leadership and oversight for the delivery of day-to-day facility maintenance and operations services at the Altria Center for Research and Technology. Responsibilities: preparation of the annual operating budget and 5-year plans; oversight and administration of the outsourced maintenance management contract; oversight and direction of site regulatory and compliance activities; research and studies to identify the highest and best usage for repurposed spaces within the building, including scope, schedule, and estimates of cost to support changing business requirements. Achievements: directed the application and achievement of a “Green Globes” award for the site post occupancy; provided leadership enabling operations staff to achieve year-over-year reductions in resource/utility consumption, despite increasing building occupancy and utilization. |
|||
Years | Employer | Title | Department |
Years: 2004 to 2008 | Employer: Altria Client Services | Title: Associate Staff Engineer | Department: |
Responsibilities:Lead mechanical engineer on the design and construction team for Altria's $250 million Center for Research and Technology. Provided owner input and guidance to the Project Architectural, Engineering, and Construction Management firms during the planning, programming, design, construction, and initial-occupancy phases of the project. At the completion of the construction, I elected to stay on site as the Altria CRT Facility Engineer to work with the equipment start-up, commissioning, test, and balance firms to facilitate the transition from construction to occupancy of the building. Assisted the new occupants of the building with space and utility modifications and fit-out in laboratory and office areas. Provided direction to the contract operations staff to optimize central plant performance and efficiency. |
|||
Years | Employer | Title | Department |
Years: 1994 to 2004 | Employer: Altria Client Services (Philip Morris) | Title: Associate Staff Engineer | Department: |
Responsibilities:Testing/Process Engineer for the Product Testing Laboratory. Developed maintenance and calibration procedures for test instrumentation. Conducted validation testing of new and re-built instrumentation to establish performance baseline criteria. Utilized statistical process control methodology to improve lab productivity, enhance test methods and results. Renovated laboratory spaces and plumbing and mechanical systems to improve control of the testing environment and to support new instrumentation. Provided project management to install a dedicated chilled water system for laboratory instruments and equipment within the Operations Center Technical Wing. Provided project management to convert laboratory air handling systems from spray coil to dry coil in Operations Center Technical Wing. Acted as Technical Lead for project team tasked with upgrading the building management system at the Operations Center. |
|||
Years | Employer | Title | Department |
Years: 1988 to 1994 | Employer: Philip Morris USA | Title: Facility Engineer | Department: |
Responsibilities:Performed facility engineering for the Research and Development location. Typical projects included repairs and replacement of building architectural, plumbing, and mechanical systems. Air-handling unit repairs and replacements. Roofing projects. Process piping projects. Pilot plant equipment installations and removals. Laboratory equipment installations, renovations, and construction. |
|||
Years | Employer | Title | Department |
Years: 1985 to 1988 | Employer: E.R. Carpenter Co. | Title: Project Engineer | Department: |
Responsibilities:Performed process piping system installs and upgrades in manufacturing plants and at customer locations. Worked with machine designers and fabricators to design and build an automated, multi-station foam-in-place molding machine with subsequent installation, start-up, and training at a customer location. Research, design, and testing to improve the manufacture and performance of foam-in-place chemical dispensing equipment for use in customer locations. |
|||
Years | Employer | Title | Department |
Years: 1983 to 1985 | Employer: Elk Roofing Corporation | Title: Project Engineer | Department: |
Responsibilities:Performed process piping installations and upgrades. Provided project management for new process equipment installation and start-ups. Worked with team to rebuild a portion of the manufacturing plant after a fire destroyed the production line. Planned, scheduled, and installed bulk material-handling system with screw conveyors and continuous weighing apparatus. Performed lease/buy analysis for plant material handling equipment. |
|||
Years | Employer | Title | Department |
Years: 1980 to 1983 | Employer: Reynolds Metals Company | Title: Project Engineer | Department: |
Responsibilities:Performed project engineering tasks for the St. Louis Printing Plant operations. Planned, scheduled, and supervised the modification and installation of rotogravure and flexographic printing presses and accessories, including: unwinds, rewinds, sheeters, cutter-creasers, laminators, extruders, and embossers. Supervised maintenance operations, including plant machine shop, millwrights, plumbers, and electricians. Supervised maintenance and operations of plant utility systems, including compressed air and waste heat boiler operations. |
|||
Years | Employer | Title | Department |
Years: 1978 to 1980 | Employer: Arkansas Power & Light Company | Title: Assistant Engineer | Department: |
Responsibilities:Performed engineering tasks for the Lake Catherine Steam Electric operations. Responsibilities included liquid fuels inventory management. Diesel fuel boiler light off piping and tank installation. Collected data and performed calculations for annual unit heat balance testing. Provided input and oversight of the turbine/generator overhaul shutdown schedule. |
Career Accomplishments
Licenses / Certifications |
---|
Professional Engineer Certified Project Manager Certified Plant Engineer LEED Continuing Education Certificates: Performance of Critical Facilities, Solar Thermal Energy, Project Management for the Engineer |