Expert Details
Disposable Hygiene Products, Manufacturing, Quality, Product Development and Cost Analysis
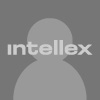
ID: 723737
Indonesia
Expert has many studies and development in Absorbent Core, maximizing SAP utilization and fluff utilization. His designs combined with his great machinery, engineering and process expertise able clients to reach Excellency in core performance.
Expert has applied his quality management background to set up “acceptance sampling” in many companies and industries as well. He has selected alternative tools and systems to match with the needs of the environment as well the level of talented human resources available within the companies he had worked with. Many of the companies he has worked for didn’t have any sampling system at all and even some companies didn’t believe that by implementing sampling systems, the quality could be improved at all. Expert patiently worked with the top and bottom levels of the companies to ensure the company as a whole embraced the new concepts and take the benefits for quality improvement as well to improve customer satisfaction. Not only quality levels where improved dramatically, but people moral as well, since less scrap was generated, productivity increased and last but not least bottom line results.
Expert has applied his quality management background to set up “acceptance test” in many companies and industries as well. Among with acceptance quality levels, acceptance tests, Expert had implemented acceptance tests as part of Quality Management System. In one of the companies Expert worked for, he had to set up all the acceptance tests which include: visual, attributive, and measurable and performance tests. By using many modern tools, Expert was able to ensure quality levels which are considered outstanding in the region. Expert was the first in his field to bring new test concepts to the regions and a pioneer in using digitalized image analysis for performance. Expert is also one of the top quality managers in the region and has supported other companies outside of his core business to improve their quality, as well supported suppliers to improve their quality level of supply.
Besides adopting the most common used tests in the industry, the Expert had developed few tests of his own based on the new needs of the market, in which quality had been improved tremendously.
Expert has applied his business management skills on in many companies, as well different industries. Expert took the challenge of managing a small size company, manufacturing auxiliary and automation equipment for the plastic processing industry and after two years under his management, the company has tripled the sales revenue with an improvement of profitability of around 15% per dollar of sales. He managed the strategy of finding new niches and applications for the equipments, as well able to close deals with large national and multinational corporations. He also demonstrated his business management skills, when he along a team of other managers, were able to buy out a bankrupted company in South East Asia and make that company in 2002, the largest manufacturer of disposable goods in the region. By using his manufacturing and business acumen, he was able to remarkable bring the profits to an increment of more than 15% YoY. He also advised the management of another company in Asia, the largest disposable goods manufacturer in Asia (by total plant throughput).
Expert has applied management tools such as lean management and process mapping to re-engineer business process. One of the projects that Expert was leading was regarding raw materials ordering and storage in which after thorough analysis, the company was able to save close to USD 300.000/year. Expert has also headed the developed some other re-engineering in business process with distribution, including 3PL and distribution centers, which are currently under the final stages.
Expert had applied his management skills to improve the productivity of companies. Expert had developed many models to understand and improve capability of plants, in two main areas: process capability – intrinsic capability of equipment and plant capability – intrinsic capability of management processes and plant. The improvements archived with current assets were remarkable in tow plants in South East Asia, in which one of the plants were able to improve their capacity in 6 times, before invest in new equipments. Expert also had developed capability studies for new assets, such the one he spearheaded the efforts to bring the only asset of its kind in South East Asia, with a total investment of USD 4.8 Million.
Expert is also one of the most expert managers in the region when comes to continuous quality improvement. He has demonstrated such ability in all the companies he worked for, but the most remarkable is his current company, in which had a defect rate of about 30% previous to his arrival and under Expert’s management the company has reached bellow 3% in the first year and today is bellow 100PPM. Expert’s quality approach is a never ending improvement; everything can be improved and should be improved, under his philosophy many companies achieved outstanding quality results and consumer satisfaction, which had rewarded the companies he worked for with superb increments on sales and bottom line results. Currently, Expert is working with 100 different quality improvement projects, which includes: his current company, 5 clients, 10 suppliers and other business not related to his core.
Expert had demonstrated his skills in corporate strategic planning. In 1996, he developed a strategic plan to increase sales and penetration of a range of automation products, which after two years had doubled the sales revenue of the company he worked for. In 2001, he was part of the team that bought a bankrupted company in South East Asia, and after two years made that company the top company in the region. In 2003, he was one of the masterminds behind the revamp of another South East Asia company, which have more than tripled the sales revenue. By using management tools, financial tools and all his manufacturing expertise, Expert contributed tremendously to the corporate strategy. Currently is preparing a major IPO for one of the companies he advise, which will be one of the major on this area. Many other strategic plans can not be disclosure in this profile, but more details can be informed during formal meetings with clients.
The Expert had developed many projects in which he had planned ahead of completion the cost control estimation. In many cases the Expert had reached even better results than expected. In the case of core formation, he excels in given the best match of core/market needs/performance. The Expert has experience with the major pulp suppliers: Weyerhaeuser, Georgia Pacific, International Paper, Buckeye and Rayonier, as well extensive experience with major SAP suppliers: Summitomo Seika, Nippon Shukobay, BASF, Kolon and Formosa.
The Expert is able to design very cost effective, quality absorbent core using combinations of the above mentioned materials, as well able to design improvements on the core formation to reach low standard deviations and consequently, potential cost savings.
The Expert is one of the best in his areas when comes to design machinery improvements for his area. He had demonstrated that when he was working in Curt JOA Inc., for Procter & Gamble. He was able improve the design of some part machine components, which made the equipment more reliable, as well easier to set and operate. In the Frontal tape Unit, due to his design changes, became a much more reliable piece of equipment.
In Fameccanicas machines he has made even better work, improved from almost every part of the equipment and even made machines increase their nominal speed in 35% in some cases, but average it has increased 25%, bringing the productivity in throughput higher, as well efficiencies.
Lately, the Expert is changing Zuiko machines, specially the core formation area, which after his improvement is delivering a absorbent core that performs 45% better than the previous, without adding more SAP neither fluff, matter of fact some fluff was removed.
The latest design challenge of the Expert is regarding machinery coming from China. He was able to save one of his customers circa USD 1 million, by buying some components from Chinese machine manufactures and by using his design changes and some other parts special made or self available, he has made those equipment as efficient as top tier European machines.
The Expert is able to work in two fronts when it comes to design for cost – make a cost effective finished good tailored for each market by deploying his extraordinary machinery and process knowledge.
One of the examples was the sanitary napkin in one of his customers. He has re-designed the machine to produce a new product, by using his own design he has saved the company about USD 200k in parts and others.
Another example was his core design, in which he was able to improve rewet and strike thru with a very cost effective utilization of SAP and fluff. His designs enable clients to spurs profits by ensuring customers satisfaction and optimum cost managements of manufacturing.
The Expert had developed many design changes in equipments to spur productivity in Curt JOA, FAM, Zuiko and other equipments.
In average, the machinery that the Expert had made changes where able to at least double its out put, as well quality improvements and losses rate.
Expert is one of the few in the world with experience with the four major technologies in the world – Curt JOA, FAM, Zuiko and Japanese.
Expert is one of the few in the world with real hands on experience with the following products/process: Baby Diaper, Sanitary Napkin, Adult Diaper, Panty Liners and Baby Pull Ups. No other individual in the region has all the combined experiences of machinery and process as the Expert has.
The Expert among the years has substantial experience in improving process design for disposable products, ranging from slow, low tech machines to more advanced, high speed machinery.
Most of his process and machine design belongs to the Expert and patent issues are directly addressed with him. If the client is interested he can support the project improvement with license to use his technology per equipment retrofitted or improved.
The Expert has proved to set high standards in maintenance and his systems implementations had proved to be effective in terms of total cost of maintenance. In one plant he implemented the systems, the maintenance costs a year, before his arrival was over USD 1 million, after the implementation the Expert was able to reduce it to USD 300,000, with a productivity increment of 85% in the same year.
By implementing high standard engineering practices, detailed problem analysis and problem solving, as well people training and development he is able to achieve such results.
Currently the Expert is implementing TPM in his current Plant, which will be the first Plant in this business in South East Asia to have TPM fully implemented.
The Expert also is able to outsource quality parts and components with attractive savings, due to his extensive network in 4 different continents. He also is able to improve reliability of equipment by using his own designs to improve maintenance costs. Has introduced MTBF and MTTR control systems, as well OEE management, improving those KPI’s in average 65% year-to-year.
Education
Year | Degree | Subject | Institution |
---|---|---|---|
Year: 2003 | Degree: MBA | Subject: Management | Institution: Lincoln University |
Year: 1999 | Degree: BM | Subject: Management | Institution: Costa Braga University |
Year: 1990 | Degree: Politechnical | Subject: Fine Mechanical Engineering | Institution: Senai Suico-Brasileiro |
Work History
Years | Employer | Title | Department |
---|---|---|---|
Years: 2002 to Present | Employer: Undisclosed | Title: Director | Department: Manufacturing and Operations |
Responsibilities:In charge of the all operations and manufacturing, including the following departments: production, product development, maintenance, supply chain, quality assurance, projects, process, HR. |
|||
Years | Employer | Title | Department |
Years: 1999 to 2002 | Employer: Drypers Malaysia | Title: Director | Department: Manufacturing |
Responsibilities:In charge of the all operations and manufacturing, including the following departments: production, product development, maintenance, quality control, projects, process |
|||
Years | Employer | Title | Department |
Years: 1997 to 1999 | Employer: Burtec | Title: Managing Director | Department: |
Responsibilities:P&L, marketing, sales, project design and controller |
|||
Years | Employer | Title | Department |
Years: 1990 to 1997 | Employer: Procter & Gamble | Title: Team Manager | Department: various |
Responsibilities:worked in many different countries, in charge of start-ups of plants and equipment |
International Experience
Years | Country / Region | Summary |
---|---|---|
Years: 1994 to 1996 | Country / Region: USA | Summary: He worked with Curt Joa - Sheboygan Falls - WI, developing products and equipment including the implementation in Latin America and Asia of the project code P101. Start up leader, which was choosen by all the plant managers in the various locations he served to become their team manager |
Years: 1990 to 1997 | Country / Region: Brazil | Summary: He was based in this country, but was choosen among many engineers worldwide to become part of the GST - global start up team, which started up many assets in 5 countries and 3 different continents |
Years: 1995 to 1996 | Country / Region: Thailand | Summary: In charge of the start up of a brand new asset (pilot equipment for Procter & Gamble), upgraded in another equipment, and the start up of a new plant and relocation of assets to the new site |
Years: 1996 to 1997 | Country / Region: Philippines | Summary: Started up the plant and the new assets, followed by the success in the Thailand operation |
Years: 1999 to 2002 | Country / Region: Malaysia | Summary: He turned around the all manufacturing by making that operation the biggest in Southeast Asia |
Additional Experience
Marketing Experience |
---|
Spearheaded the development and market concept for the product that became the market leader in the country he currently works |
Other Relevant Experience |
---|
He has experience turning around troubled operations, proven expertise in designing products, improving and maximizing assets utilization and generating bottom line results. |
Language Skills
Language | Proficiency |
---|---|
English | Day-by-day usage, business and others |
Portuguese | Mother tongue |
Spanish | Learned in Mexico, now perfecting by becoming part of the Spanish speaking local group |
Mandarin | Beginner |
Fields of Expertise
acceptable quality level, acceptance test, acceptance sampling, vendor quality auditing, business management, high volume, low cost product design, business process re-engineering, capability study, design to capacity, continuous quality improvement, quality engineering, quality evaluation, quality standard, statistical quality control, total quality control, quality auditing, quality control, corporate strategic planning, design cost control estimation, design engineering, new product development, product design, consumer product design, design-for-quality, design for cost, design for manufacturability, production control, design process, maintenance management, maintenance engineering, maintenance planning, plant operations management, niche marketing, industrial maintenance management, commercialization, consumer survey, bill of materials, dimension, computerized maintenance management, facility maintenance management, textile quality control, development engineering management, design review, material product development, process design, redesign process, design for disassembly, computer-aided design