Expert Details
Conveyors & Conveyor Systems: design, build & install
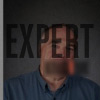
ID: 734610
Pennsylvania, USA
His experience includes, but is not limited to, the following:
1. 14+ years as a Project Engineer (employed by Hillside Metal Products a.k.a Art metal, Owens-Illinois, Foster-Forbes and Diamond-Bathurst) and worked at various manufacturing facilities. Included in this time is work on several projects containing conveyor, inspection equipment, packaging and load building equipment. The conveyor types included product, case and pallet conveyors.
a. In this position, he was responsible for system design, justification, equipment selection, purchasing of equipment and installation services, installation execution, punch list generation, commissioning, final acceptance and transferring the system to owner operation personnel.
2. 16+ years as the Owner of KJE Associates Inc an equipment systems and equipment design, build and installation company.
a. The company worked with a variety of industries.
b. They supplied new equipment, rebuilt customer owned equipment and installed new and rebuilt equipment.
c. Their customers were mostly operating in the contiguous 48 states of the United States. In addition, it sold products and equipment systems to China, Canada, Mexico and Jamaica.
3. 5 years+ as a Sales Engineer for Precision Automation Company, they built and designed various types of equipment used in manufacturing plants. The company also sold equipment manufactured by other companies. This company would install the machinery and conveyors for their customers as part of the sale.
a. He was responsible for identifying prospects and seeking business opportunities with these companies.
b. His work with the customer continued beyond the identification and acquisition of new business. His duties included, but were not limited to:
i. Helping the customer define the project scope, requirements, specifications, layouts…etc.
ii. Preparing a proposal.
iii. Accepting and processing the purchase order.
iv. Acting as project engineer/manager.
v. Managing the installation (if necessary).
vi. Working with the customer to prepare a project punch list.
vii. Managing the installer as he completed the punch list.
viii. Monitoring start-up and troubleshooting as needed.
ix. Coordinating commissioning and customer acceptance.
x. Handing off the equipment/system to the customer.
4. 9+ years as an Independent Sales Engineer and Consultant.
a. Performed time studies for a variety of manufacturers.
b. As a partner in Indoff, a material handling sales organization, he supplied material handling equipment to industry in general.
c. Coordinated the removal, transportation and re-installation of conveyors and process equipment.
d. As a manufacturer’s representative, He worked with two automation system providers, Employer and Keystone Automation, who delivered a combination of conveyors and special automated equipment to my customers.
e. He worked probono for Ben Franklin Technology Partners of Northeast Pennsylvania, a non-profit group that lends/grants money to new or growing manufacturing companies in Pennsylvania. This group asks him to review certain loan/grant applications as part of their due diligence process.
f. Also, as pro bono, he provided my services to the local public library. BB&T, a local bank, donated a large building to the Boyertown Area Community Library. The library was operating out of small and crowded facility.
i. He provided layout assistance for relocating the used book stacks from the old library to the new library.
ii. Directed a group of volunteers in the removal of specified stacks from the old building to their location in the new building.
iii. Worked with the vendor who supplied the new circulation area furniture by providing him with the layout specifications and directed the installers as to the placement of the new furniture.
Expert witness experience:
a. A lawsuit by a distribution center organization was brought against my client, an electrical/mechanical
contractor. The suit alleged that the contractor failed to successfully complete the conveyor/automation
project in a timely fashion. The damages requested were in excess of six million dollars.
b. I was able to demonstrate, based upon the information provided to me, that the contractor was not at fault.
The customer’s scope of work changed significantly as did the system’s requirements. Also, a significant
amount of the customer provided equipment was used and incomplete and needed to be repaired and/or
modified prior to use.
c. An additional factor was that the customer did not allow the contractor to run, troubleshoot and refine each
individual sub-section of the overall system. The customer insisted on using each sub-section of the
system immediately. Thereby incurring downtime and product loss.
.
Project Engineer: at various manufacturing facilities. Included is work on several projects containing
conveyor, inspection equipment, packaging and load building equipment. The conveyor types included
product, case and pallet conveyors.
a. In this position, he was responsible for system design, justification, equipment selection, purchasing of
equipment and installation services, installation execution, punch list generation, commissioning, final
acceptance and transferring the system to owner operation personnel.
Business Owner of an equipment systems and equipment design, build and installation company.
a. The company worked with a variety of industries.
b. They supplied new equipment, rebuilt customer owned equipment and installed new and rebuilt equipment.
c. Their customers were mostly operating in the contiguous 48 states of the United States. In addition, it sold
products and equipment systems to China, Canada, Mexico and Jamaica.
5 years+ as a Sales Engineer for an automation company, they built and designed various types of equipment used in manufacturing plants. The company also sold equipment manufactured by other companies. This company would install the machinery and conveyors for their customers as part of the sale.
a. He was responsible for identifying prospects and seeking business opportunities with these companies.
b. His work with the customer continued beyond the identification and acquisition of new business. His duties
included, but were not limited to:
i. Helping the customer define the project scope, requirements, specifications, layouts…etc.
ii. Preparing a proposal.
iii. Accepting and processing the purchase order.
iv. Acting as project engineer/manager.
v. Managing the installation (if necessary).
vi. Working with the customer to prepare a project punch list.
vii. Managing the installer as he completed the punch list.
viii. Monitoring start-up and troubleshooting as needed.
ix. Co-ordinating commissioning and customer acceptance.
x. Handing off the equipment/system to the customer.
Independent Sales Engineer and Consultant.
1. Performed time studies for a variety of manufacturers.
2. As a partner in a material handling sales organization, he supplied material handling equipment to
industry in general.
3. Coordinated the removal, transportation and re-installation of conveyors and process equipment.
4. As a manufacturer’s representative, He worked with two automation system providers, who delivered a
combination of conveyors and special automated equipment to his customers.
1. He worked pro-bono for Ben Franklin Technology Partners of Northeast Pennsylvania, a non-profit group
that lends/grants money to new or growing manufacturing companies in Pennsylvania. This group asks
him to review certain loan/grant applications as part of their due diligence process.
2. Also, as pro-bono, he provided my services to the local public library. BB&T, a local bank, donated a large
building to the Boyertown Area Community Library. The library was operating out of small and crowded
facility.
a. He provided layout assistance for relocating the used book stacks from the old library to the new
library.
b. Directed a group of volunteers in the removal of specified stacks from the old building to their location
in the new building.
c. Worked with the vendor who supplied the new circulation area furniture by providing him with the
layout specifications and directed the installers as to the placement of the new furniture.
Expert travels nationally and Canada.
Education
Year | Degree | Subject | Institution |
---|---|---|---|
Year: 2008 | Degree: Completed Basic and Intermediate courses in AutoCad | Subject: AutoCad | Institution: Camden County College |
Year: 1986 | Degree: Completed 15 credits towards MS in Engineering including courses in Robotics and Simulation. | Subject: Industrial Systems Engineering | Institution: Pennsylvania State University- Great Valley Graduate Center |
Year: 1972 | Degree: BS Industrial Engineering | Subject: Industrial Engineering | Institution: New Jersey Institute of Technology |
Work History
Years | Employer | Title | Department |
---|---|---|---|
Years: 2013 to Present | Employer: Undisclosed | Title: Senior Project Engineer | Department: |
Responsibilities:Available upon request. |
|||
Years | Employer | Title | Department |
Years: 2009 to Present | Employer: Undisclosed | Title: Project Engineer- Material Handling Group | Department: |
Responsibilities:Through work measurement and material flow studies, identified production and in plant logistics problems and recommended continuous improvement solutions to customers. |
|||
Years | Employer | Title | Department |
Years: 2014 to 2016 | Employer: Keystone Automation Inc. | Title: Senior Engineer | Department: |
Responsibilities:• Provide solutions for customer processes and material handling systems.• Assistance from machining one part to designing & building equipment & complete systems. • Listen to the concerns of the clients' operations, engineering and finance personnel • Results that meet or exceed the expectations of all involved. • Experienced in and know intimately the requirements of a successful project. • Team player working with all levels of the organization providing globally accepted solutions. |
|||
Years | Employer | Title | Department |
Years: 2013 to 2014 | Employer: IES Group | Title: Senior Industrial Engineer | Department: |
Responsibilities:Working with manufacturers and distribution centers on a project to project basis. Utilizing skills and experience on cost reduction, production and quality improvement projects.RECENT PROJECTS: LEESPORT, PA. - COMMERCIAL FIXTURE MANUFACTURER • Completed continuous time studies in two machining centers. o Established standard times for the purpose of production planning and staffing. o Identified events that caused production delays and recommended solutions. NEWTOWN, PA - STRETCH AND SHRINK CONTINUOUS LABEL MANUFACTURER • Completed continuous time studies on the new 10 color press operation with the objective of streamlining the changeover process. • Provided guideline recommendations for systematically balancing the work of the three man operating crews. • Identified and provided lean solutions for existing production bottlenecks. • Net results would reduce changeover downtime by 10-20%. NORTHEAST, PA - FOOD MANUFACTURER • Provided solution to convey and effectively transfer liquid food product in a sealed flexible container. • Equipment allowed for package to either flow onto the main transportation conveyor or to the secondary operation. |
|||
Years | Employer | Title | Department |
Years: 2012 to 2013 | Employer: NCC Automated Systems | Title: Application/ Project Engineer Contract | Department: |
Responsibilities:o Developed process documentation for standard products.o Provided lean solutions for pre-engineered modular conveyor applications. o Managed conveyor projects from purchase order through installation. o Assisted in the formation of a quality management system. |
|||
Years | Employer | Title | Department |
Years: 2011 to 2012 | Employer: Follett Corporation | Title: Industrial Engineer/ Contract | Department: |
Responsibilities:o Conducted time studies to update labor standards throughout the production departments.o Successfully applied OEE techniques to an underperforming work-cell. o Analyzed process documentation for methods improvements. o Assisted with layout and implementation of new assembly work-cell. |
|||
Years | Employer | Title | Department |
Years: 2004 to 2009 | Employer: Precision Automation Company Inc. | Title: Project Engineer- Conveyor Systems Group | Department: |
Responsibilities:o Through work measurement and material flow studies, identified production and in plant logistics problems and recommended continuous improvement solutions to customers.o Engineered lean and continuous improvement projects from inception to start up with expertise in planning, justification, cost estimating, proposal writing, system design, machine selection, installation, and troubleshooting. Integrating new and existing equipment. o Integrated product, case and pallet conveyors with inspection, packaging and palletizing equipment to create packaging and palletizing systems. o Continuously improving customer service by investigating and solving issues and problems. |
|||
Years | Employer | Title | Department |
Years: 1986 to 2004 | Employer: KJE Associates, Inc. | Title: Industrial and Manufacturing Engineer | Department: |
Responsibilities:o Started, grew and operated a design/build conveyor and packaging equipment manufacturing company.o Using time studies and process documentation, established efficient machining, welding and assembly work cells. o Engineered projects from inception to start up with expertise in planning, justification, system design, machine selection, installation, and troubleshooting. Incorporating new and existing equipment. o Managed and prioritized multiple projects integrating product, case and pallet conveyors with inspection, packaging and palletizing equipment. o Analyzed and consulted on improvements in manufacturing processes and material handling systems. o Developed a 20-man equipment installation crew. o The projects were installed throughout the United States and Canada. |
|||
Years | Employer | Title | Department |
Years: 1978 to 1986 | Employer: Anchor Glass Co. | Title: Manager of Industrial Engineering | Department: |
Responsibilities:o Initiated, managed and controlled the capital budget at the local plant level.o Engineered and managed production improvement and cost reduction projects at various US plants, resulting in the reduction of operating costs by over $2.5 million/year. o Managed and prioritized multiple projects integrating product, case and pallet conveyors with inspection, packaging and palletizing equipment. o Through work measurement and material flow studies, identified production and in plant logistics problems and recommended continuous improvement solutions to customers. problems and recommended continuous improvement solutions to customers. |
|||
Years | Employer | Title | Department |
Years: 1977 to 1978 | Employer: St. Gobain Glass Co. | Title: Maintenance Supervisor | Department: |
Responsibilities:o Managed the maintenance activities of a factory that operated 24 hours/ day, 7 days/week.o Observes, analyzed and upgraded a manufacturing process increasing system production over 10%. |
|||
Years | Employer | Title | Department |
Years: 1974 to 1977 | Employer: Owens- Illinois | Title: Senior Industrial Engineer | Department: |
Responsibilities:o Responsible for process improvement and cost reduction projects.o Managed the production monitoring computer system. o Directed hourly workforce in the Inspection and Packaging Department. o As Maintenance Foreman directed a multi-functional maintenance group. o Chaired process improvement, safety and suggestion committees implementing ideas from hourly and salary personnel. o Designed/installed automated load building center, saved $150K/yr. |
|||
Years | Employer | Title | Department |
Years: 1972 to 1974 | Employer: Artmetal | Title: Industrial Engineer & Assistant Plant Engineer | Department: |
Responsibilities:o Engineered process improvement projects.o Supervised maintenance tradesmen |
Career Accomplishments
Associations / Societies |
---|
Boyertown Area Community Library Ben Franklin Technology Partners - Northeastern Pennsylvania IIE Lehigh Valley Professional |
Licenses / Certifications |
---|
Professional Engineer |
Publications and Patents Summary |
---|
Publications: 1 Applied Lean Solutions |
Additional Experience
Vendor Selection |
---|
My experience includes several conveyor system and automation equipment projects where vendor selection was an important part of the project. |
Marketing Experience |
---|
As a company owner and sales engineer I was heavily involved in the marketing of conveyors and packaging equipment products. |
Other Relevant Experience |
---|
Many years of project engineering and project management including supervising installations utilizing contractors and plant technical personnel. |