Expert Details
Composite Materials Selection, Processing,&Evaluation Optimization; Application Dev., Resins
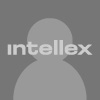
ID: 732228
Pennsylvania, USA
He has patented systems for:
- Ballistic resistant thick section laminates used as combinedstructure/hardening systems.
- Modified the pultrusion process with an effective high pressure injection die system used for improved performance and compliance to current MACT requirements.
- A PVC/glass fiber system for both continuously reinforced system as well as randomly reinforced molding compounds.
- Nine other patents for novel types of processes and materials related to reinforced composite systems.
Training of both technical and non-technical groups both domestically and globally has been an integral part of his career. He has worked extensively with bringing composite technology to all varieties of audiences. Mentoring, demonstrating, oral and written communication and team building are also areas in which he excels.
He has been active in the standardization field working with ASTM, API and ACI to develop standards for composite applications and testing standards.
He is an expert in composite testing--mechanical, physical, and time-dependant under a wide range of environments including cryogenic and
high vacuum conditions.
From 2007-present, he has served as President of a consulting firm, offering expert input on process and materials optimization.
Education
Year | Degree | Subject | Institution |
---|---|---|---|
Year: 1972 | Degree: D.Sc | Subject: Chemical Engineering | Institution: Washington University (St. Louis, MO) |
Year: 1971 | Degree: MS | Subject: Chemical Engineering | Institution: Washington University (St. Louis, MO) |
Year: 1967 | Degree: BS | Subject: Chemical Engineering | Institution: University of Wisconsin |
Work History
Years | Employer | Title | Department |
---|---|---|---|
Years: 2007 to Present | Employer: Undisclosed | Title: President | Department: |
Responsibilities:Expert consulted on process and materials optimization for a wide range of customers, materials, and processes. |
|||
Years | Employer | Title | Department |
Years: 2004 to 2007 | Employer: Werner Co. | Title: Leader | Department: Advanced Development |
Responsibilities:Expert developed new and improved systems for environmental friendly production of climbing products. He also upgraded existing systems for extended color retention during outdoor exposure. |
|||
Years | Employer | Title | Department |
Years: 2001 to 2003 | Employer: Pella Corporation | Title: Principal Engineer | Department: |
Responsibilities:Expert formulated resin system, which met a highly diverse requirement for strength appearance, manufacturing performance and stability. The resulting system is the basis for the success of the IMPERVIA product line. |
|||
Years | Employer | Title | Department |
Years: 1979 to 2001 | Employer: Owens Corning | Title: Research Associate | Department: |
Responsibilities:He trained sales staff both domestically and globally through sales training schools and seminar series. Expert also traveled throughout the Far East training licensees, affiliates and their customers in composite processing. His injection die pultrusion invention increased sales and profitability of resin, mat and roving into the pultrusion industry (in-die injection has also become a basis for EPA’s MACT for pultrusion). Ballistic Laminate Technology developed with S-2 GLASS team has been licensed globally and is currently saving lives as spall liner on military vehicles. Expert also improved multiple customer applications such as sucker rods, ladder rails, rebar and others during 15 years of in field technical support to sales and marketing. He also translated Owens Corning’s technology in containment of cryogenic liquids with composite systems to the superconductivity industry through a series of publications and contracts. |
|||
Years | Employer | Title | Department |
Years: 1977 to 1979 | Employer: De Soto, Inc. | Title: Group Leader | Department: |
Responsibilities:Expert developed new coating systems and caused reformulation or existing coatings, which improved product lines and allowed systems to meet Military Specification. He also supervised Composites and Aerospace groups, which produced the highest proportion of income to sales in the company. Expert wrote detailed understandable process and product description for unique complex fiber prepreg process, which allowed DeSoto to sell system profitably when they exited their composite business venture. |
|||
Years | Employer | Title | Department |
Years: 1972 to 1976 | Employer: Naval Research Laboratory | Title: Section Head | Department: Chemistry Division |
Responsibilities:He developed processing methods used to manufacture graphite reinforced composite laminates with controlled fiber orientation and composition that were used to develop the design values for Naval Aircrafts, Surface Effect Ships and Ballistic Missile components. He established methods for protecting composite systems from laser weapons |
Government Experience
Years | Agency | Role | Description |
---|---|---|---|
Years: 1972 to 1976 | Agency: Naval Research Laboratory | Role: Section Head | Description: He worked on the development of military hardware through characterizing material systems’ structural and functional performance attributes. He established databases used to design systems such as the C-4 ballistic missile, F-18 and AV8B fighters, Surface Effect Ships (hovercrafts,) and other current hardware systems. Expert also helped develop the initial database on the effects of high-energy laser radiation on the structural performance of composite systems. |
Additional Experience
Training / Seminars |
---|
He developed a training package for Owens Corning's affiliates and licensees and presented it at seminars in Singapore, Malaysia, Indonesia and South Korea. He was part of OC's sales training staff. He created training programs for Werner which were used to teach new hires at the Juarez production facility |
Vendor Selection |
---|
He has over 45 years of working with the major resin, reinforcement and additive suppliers used by composite manufacturers around the world. |
Marketing Experience |
---|
He is a past vice-president of the Pultrusion Industry Council. He has worked on ASTM CD20.18.02 subcommittee on standards for the pultrusion process. He was a member of the American Concrete Institute subcommittee that developed standards of Fiberglass reinforced rebar and dowel bar system. He worked with the American Petroleum Institute to develop standards for fiberglass sucker rods and High and Low pressure oil field tubular products made from fiberglass reinforcement and epoxy resins. |
Other Relevant Experience |
---|
He is able to translate complex technical concepts to customers, technologists, and non-scientific personnel --even those with English as their second or third language. |
Fields of Expertise
composite material, composite material process development, polyvinyl chloride, thermoplastic composite, epoxy resin, epoxy resin physical property, polyester, polymeric material curing, thermoset polyester, thermosetting resin, unsaturated polyester, vinyl ester resin, bulk molding compound, composite-filament winding process, compression molding, prepreg material, pultrusion, sheet molding compound, cryogenic temperature, thermoset injection molding, peroxide curing, hand lay-up molding, preform design, ultraviolet-curable coating material, autoclave, urethane, resin transfer molding, polyurethane, polymer coating material, phenolic resin