Expert Details
Combustion, Combustor Design, Combustor Acoustical Problems, Analysis, CFD, Engineering Design
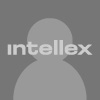
ID: 723172
North Carolina, USA
Expert designed or improved combustion chambers for high temperature test facilities. These ranged from pressures of one atmosphere to 4000 psia, and temperatures from 1100 R to 5500R. The combustors were from 3 inches in diameter to over 3 feet in diameter. The problems solved were survival; heat transfer, stability, acoustics, ignition, and safety. Expert has 5 Patents in these areas. Some of the designs were unique and new such as the stabilized lifted flame and the combustor within a combustor. He designed a combustion chamber development facility that was used to test new designs and concepts. Two of the new designs were the stabilized lifted flame for methane and hydrogen, and the combustor within a combustor for good thermal profiles and broad coverage from 1100 R to 5500 R with one combustor.
He has developed effective acoustic damping techniques ( reduced noise in 8-FT HTT from 70 psi at 30 HZ to 0.5 psia at 360 Hz.- now the quietest combustor in the world for its size He has designed and tested and now in service, Super Ignitor for 8-FT HTT . Uses rich pilot flame ( REQ=3) to stabilize and ignite large jet of methane at near sonic conditions He has designed a development facility. In this facility, he designed a number of unique designs and tested :
i. The modified Lewis design for use as ignitor
ii. The mini-max SUE annular combustor
iii. A swirl stabilized combustor
iv. A ring type fuel injector
v. A modified ring type injector
vi. A lifted flame ring injector ( no cooling needed)
vii. A lifted flame paired airfoil injector able to operate at 5000 R and 2000 psia without cooling.
He lead the installion of 84 SUE combustors ( 52 foot diameter plenum ) in the 9 X6 Wind Tunnel . Temperature =2500 R and Poc=200 psia . Used to test Army and Air Force tactical missiles at q of up to 5000 psf . Flow rates of up to 5000 lb./s of which 60% went through combustors. The SAM-D ( now the Patriot was developed here ) ; the improved Hawk ;the use of fused silica as radomes ; radomes for rain and ice also developed here He was responsible ( with team) for the redesign of the Mixer for Aerojet for the Hypersonic Test facility
Education
Year | Degree | Subject | Institution |
---|---|---|---|
Year: 1963 | Degree: BS | Subject: Aerospace Engineering, Engineering Mechanics | Institution: Virginia Polytechnic Institute |
Year: 1982 | Degree: BS | Subject: Civil Engineering | Institution: Old Dominion University (ODU) |
Year: 1985 | Degree: MS | Subject: Mechanical Engineering | Institution: ODU |
Year: 1961 | Degree: MS | Subject: Mechanical Engineering | Institution: Notre Dame |
Year: 1981 | Degree: PhD | Subject: Mechanical Engineering | Institution: Notre Dame |
Work History
Years | Employer | Title | Department |
---|---|---|---|
Years: 1963 to 2004 | Employer: NASA Langley | Title: Senior Combustion Engineer | Department: Hypersonic Airbreathing Propulsion |
Responsibilities:He is responsible for : Originate, plan, and report the results of research required to demonstrate theFeasibility of high-energy facility designs. Provide new and unique designs and Solutions to operational problems. Provide new and unique concepts for Hypersonic vehicles both air breathing and rocket powered or combinations. Design and develop facilities to test such hypersonic vehicles |
|||
Years | Employer | Title | Department |
Years: 1983 to Present | Employer: Undisclosed | Title: Designer | Department: Engineering Design |
Responsibilities:He is a senior engineer providing engineering expertise and project management services required for the development of specialized research systems. His engineering expertise is in the design and analysis of structural and mechanical systems, the use of numerous design codes, developing new criteria for specialized systems, using and mentoring others in the use of design and analysis software, and developing unique closed form solutions to problems. He is a project manager, leading a multi-disciplined team of engineers, technicians, administration personnel, and contractors through all aspects of a project including: defining requirements and project scope, cost estimating, schedule development and control, conceptual design through final design, analysis, drawings, documentation, specifications, procurement methods, construction management, testing, project close-out, and reporting at various reviews and status meetings. Supervision is limited to defining the broad objective, negotiating for personnel to work on the project, and status meetings. |
|||
Years | Employer | Title | Department |
Years: 1989 to 2003 | Employer: NASA-Langley | Title: Project Engineer | Department: Engineering |
Responsibilities:He is consulting and solving problems analytically supported by CFD codes on• Subsonic combustors, rocket, and scramjet design. • Heat flux levels in combustors and ramjets-scramjets. Cooling of the combustors for these devices |
Government Experience
Years | Agency | Role | Description |
---|---|---|---|
Years: 1963 to 2004 | Agency: NASA | Role: Lead Engineer | Description: He was responsible for the testing of RV,s and other missiles from 1963 to 1988. He was responsible for the design of wind tunnels to test the Space Shuttle and TPS. He was responsible for wind tunnel design and use for Hypersonic vehicles and Scramjets such as the X-43. He was chief designer of alrge combustion chambers. |
Years: 1998 to 1998 | Agency: US Navy | Role: Patent Review | Description: He was responsible for the intercooled gas turbine patent review for ships |
Years: 1999 to 2000 | Agency: US Navy | Role: Combustor Design | Description: He was responsible for the design of a new combustor for the China Lake test facility. The new combustor was for Mach 5 to 8 simulation. |
Years: 2001 to 2002 | Agency: Air Force | Role: Combustor Design | Description: He was responsible for the new APTU combustor for AEDC at Tulahoma Tenn. |
International Experience
Years | Country / Region | Summary |
---|---|---|
Years: to Present | Country / Region: Peru ( Marco Egoavil) | Summary: Compañía Minera Agregados Calcáreos Lima, Peru• Main responsibility was the design, installation and testing of conveyors, ball mills, roller mills, elevator, crushers, mechanical classifiers, fans and a vertical lime kiln. |
Career Accomplishments
Associations / Societies |
---|
He is a member of AIAA and has received numerous awards and honors including the NASA Exceptional Achievement Medal. He is in Who's Who in Engineering and Science from 1991-2004 |
Licenses / Certifications |
---|
P.E. |
Awards / Recognition |
---|
NASA Exceptional Achievement |
Publications and Patents Summary |
---|
He has 25 publications, 5 Patents, and over 50 presentations . |
Additional Experience
Expert Witness Experience |
---|
He was asked to review a Patent for the Navy for an intercooler for a large gas turbine for ships. |
Training / Seminars |
---|
He gave a short course on wind tunnel testing at Mach 7 |
Vendor Selection |
---|
He is familiar with most of the wind tunnels and their use. He is also knowledgeable in IR and acoustic equipment. |
Other Relevant Experience |
---|
The expert has extensive experience in combustor design through checkout for NASA and DOD. The expert can provide requirements definition, mechanical design and drawings, mechanical/structural analysis including finite element analysis, flow and thermal analysis, process systems, controls, project and construction management, and final checkout of the facility. Some of the software used is listed below. Pro-Engineer: Solid model design and drafting Nastran: Finite element analysis (FEA) static/dynamic/thermal FEMAP: FEA graphics pre and post processor MathCad: Mathematics Fluent/Gambit: 3D Computational fluid dynamics Adobe Acrobat: Documentation TEP : Gas Properties, reactions, expansions, etc. PBG Engineering will team with Riggins Company for fabrication, delivery, and assembly of a combustor. Riggins has extensive experience in pressure vessel fabrication as well as combustor internal components and can provide a U1 or U2 pressure vessel stamp. A concurrent engineering Management Plan will be used for all projects. Long lead components will have to be started before final design is complete, providing just-in-time updates to the fabricator. This will require regular and timely distribution of funds. The deliverables will include regular status reports, an assembled and tested combustor, a requirements and analysis report, and as built drawings. |
Language Skills
Language | Proficiency |
---|---|
Spanish | The expert was born in Peru and lived there until 1963. |
Fields of Expertise
aeronautics test-facility, combustion engine, combustion engineering, fluid management, fluid behavior, fluid compressibility, aerospace engine, fluid compression, turbulent boundary layer drag reduction, turbulent boundary layer, applied aerodynamics, fluid boundary layer, missile, internal fluid mechanics, gas mechanics, chemical reaction mechanism, rocket, aeronautical propulsion, turbulent flow, rocket propulsion, propulsion, propellant, liquid rocket propellant, liquid propellant rocket, jet propulsion, gaseous rocket propellant, gas flow through a nozzle, fluid mechanics, fluid flow measurement, fluid dynamics, drag, air flow, aerospace engineering