Expert Details
Coatings; Powder, liquid, Electrocoating and metal finishing process
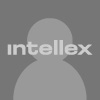
ID: 735112
Puerto Rico
Skills:
Coach and certified Trainer LEAN manufacturing / Six Sigma to Thermo King’s managers and supervisors.
Developing and implementing Total Quality Management activities using tools; GMP, SOP, SPC, ISO 9000 and ISO 14000.
Project Manager (Budget Management, Capital Plan, OPEX Plan, Value Stream Map opportunities).
Ability to work with and influence multiple stakeholders in a fast-paced environment. Fully Bilingual (English/Spanish).
Strong Communication skills both verbal and written.
Knowledge of standards, specs, and regulations in the manufacturing / pharmaceutical industry such as ASTM, ANSI, MIL, EPA, FDA, OSHA, and Automotive.
Proficient on computers software packages (Windows XP, Word, Excel, PowerPoint), MS Project, VISIO, CAD.
Strong leadership skills.
Ability to learn and apply new concepts and overcome obstacles. Result Oriented always looking for value-added
Management of production employees and daily activities.
Problem-solving and analytical skills.
Education
Year | Degree | Subject | Institution |
---|---|---|---|
Year: 1995 | Degree: Master's Degree (24 credits toward degree) | Subject: Chemical Engineering | Institution: University of Puerto Rico, Mayaguez Campus |
Year: 1992 | Degree: Bachelor of Science | Subject: Chemical Engineering | Institution: University of Puerto Rico, Mayaguez Campus |
Work History
Years | Employer | Title | Department |
---|---|---|---|
Years: 2017 to Present | Employer: Undisclosed | Title: President | Department: |
Responsibilities:General consultancy business owner aimed at manufacturing and service companies. Company has a wide range of value-added proposals such as process consulting, personnel reorganization, business transformation, coaching and management, and employees training, project management, validations, solutions packages Software/PLC and IOT, audits and implementation of process quality, automation, and light construction. In addition, Expert worked in the formulation of "high-performance coatings ", design of applications for liquid paint systems, powder and electro-coating, and dry film lubricants. Process equipment qualification and TPM. All this using Lean manufacturing tools, Six-Sigma, management, engineering, and sales/logistics. |
|||
Years | Employer | Title | Department |
Years: 2011 to 2017 | Employer: (Undisclosed) | Title: Process / Manufacturing Metal Finishing Operation | Department: |
Responsibilities:Serve as Process / Manufacturing Superintendent for the Metal Finishing Operations under Focus Factory Feeder Department. Responsible for Plan, guide and oversee overall business operations to achieve the Company's manufacturing objectives for growth, profitability, quality, on-time performance, and customer satisfaction. The metal finishing process (Surface Cleaning and E- Coat), Robotic Frame Welding Cell, and container refrigeration unit assembly line. Conduct E-Coat process start-up and constant improvement. Perform troubleshooting and debugging of the E-Coat system using root cause 9 step gap analysis and then execute assemble team executing planned tasks and follow up actions. Assemble a team, to participate o Value Stream Mapping of coat operations. Standard work for E-COAT and Robotic cell welding. Designed and constructed the racking and material handling system for the e-coat process using 3P Lean Design Principles to improve material flow. Planning equipment maintenance with OEE metrics. Assuring compliance with OSHA and EPA regulations. Robotic Frame Welding Cell did a new layout to consolidate de operations, time studies to increase capacity gemba board to check the quality, production, material, machine uptime, and safety. Acting as Manager executing strategic plans to achieve quality products and the company’s metrics (DPM & FPS) including client satisfaction, warranty goals, safety index, on-time delivery, productivity goals, OPEX, Lean Initiatives, budget proposals, capital projects. Supervise a team of coordinators, assemblers, engineers, and technicians for a total of 100 people under my responsibility. Ensure support of ergonomics and safety plans throughout audits and corrective action plans. Implement Corporate Plans for standardizing all painting and coating tests. Create process control data-logs. Execute KAIZEN project re-arranging layout. Participate in Green Belt projects. Leader of cost savings projects. Develop plans and processes for viable projects. Maintain accountability for the business impact of product technical decisions. Identify cost drivers and implement plant controls. Ensure compliance with applicable federal, global and local regulations and standards. |
|||
Years | Employer | Title | Department |
Years: 2000 to 2011 | Employer: Thermo King de Puerto Rico, Arecibo Operations | Title: Materials/Planner Buyer Leader | Department: Materials Department |
Responsibilities:Responsible for managing the purchase of goods and services for Thermo King’s manufacturing processes and Materials Department employees; clients and contracts. Commodities: hardware/fasteners; rubber and gaskets; diesel tanks; finished plastics; copper raw materials; MROs (chemicals for the e-coat finishing line). Ensured that goods and services were according to production schedules and the manufacturing department. Worked with manufacturing department on new implementations such as ECO, and VA/VE projects using Windchill; Oracle and CAD tools. Researched for new vendors. Approved price quotes. Reach agreements. Performed manufacturing process improvement and cost reduction projects valued at 500k. |
|||
Years | Employer | Title | Department |
Years: 2004 to 2008 | Employer: Thermo King de Puerto Rico, Arecibo Operations | Title: Metal Finishing Process Superintendent | Department: Focus Factory Frames Department |
Responsibilities:Served as Manufacturing Process Superintendent for Frame Focus Factory Dept. Responsible for the metal finishing operations (Liquid Paint and E- Coat); Automatic Frame Robotic Welding; Automatic Components / Accumulator Robotic Welding; Finishing Welding; Wet Paint, and Electro-Coating Paint). Conducted E-Coat process start-up. Performed troubleshooting and debugging of the E-Coat system using root cause analytical tools. Designed and constructed the racking and material handling system for the e-coat process. Supervised the installation of the “Hold-Ups System” with TTX. Lead, managed and executed strategic plans to achieve quality products and the company’s metrics (DPM & FPS) including client satisfaction, warranty goals, safety index, on-time delivery, productivity goals, OPEX, Lean Initiatives, budget proposals, capital projects, etc. Acted as Manager of a team of supervisors and technicians to assure ISO Certification; cost reduction initiatives and TPM. Provided training to e-coat personnel. Ensured support of ergonomics and safety plans throughout audits and corrective action plans. Implemented Corporate Plans for standardizing all painting and coating tests. Created process control data-logs. Coordinated KAIZEN projects. Participated in Green Belt projects. Achieved cost savings over $500,000 as individual contributions. Ensured customer growth and retention while reaching internal and external customer satisfaction. Developed plans and processes for viable projects. Maintained accountability for the business impact of product technical decisions. Identified cost drivers and implemented plant controls. Ensured compliance with applicable federal, global and local regulations and standards. Supervised the Plastic Dept .including production scheduled, TPM overseen Thermoforming, trimming/gluing and packing finished good plastic materials. |
|||
Years | Employer | Title | Department |
Years: 2002 to 2004 | Employer: Industrial Chemical Corporation (ICC), Peñuelas | Title: Process Manager | Department: P.R. Chemical Engineering Department |
Responsibilities:Served as design process leader/ facilitator for the sulfuric acid, alum, ammonium bi-sulfite, sodium bi-sulfite, and ammonium hydroxide processes. Ensured compliance of Environmental, Health and Safety regulations. Supervised and provided day to day instructions to production personnel. Wrote standard operating procedures (SOPs) for the operations of ICC processes. Supervised and conducted laboratory procedures and data. Evaluated job performance for production personnel and took steps to improve individual and group effectiveness. Provided technical presentations to upper management and ICC customers. Wrote requests for capital projects for the PAC line. Contacted suppliers, consultants, and contractors for clients including PRASA, PREPA, and the private sector. Ensured compliance with industry standards such as GMP, SOP, EPA, ANSI, etc. Served as the Project Manager for the PAC Aluminum chloride Project. Assisted in the checkout and start-up of the ICI chemical processes. Assisted in troubleshooting of commercial products and manufacturing of inorganic polymers. |
|||
Years | Employer | Title | Department |
Years: 1998 to 2002 | Employer: S&C Electric Company | Title: Manufacturing/ Process Finishing Engineer | Department: Product Engineering Dept., Metal Enclose Switch Gear Division |
Responsibilities:Supervised and provided support to the Metal Finishing Operations including mechanical surface preparation (grinding and abrasives), chemical conversion coating treatment (zinc phosphate) and application of protective coatings to high voltage protective equipment (i.e. Pad Mount Gear, Metal Enclose Switch Gear, HV gas insulated gear, Source Transfer). Wrote and supervised preventive maintenance programs. Developed, reviewed and updated Standard Operating Procedures. Performed statistical process control analysis. Supervised validation batches, collected and tested validation samples. Coordinated manufacturing performances with QA, Production, Regulatory, Environmental and other S&C Departments. Conducted inspections of manufacturing materials used at coating lines. Assured ISO 9000 compliance. Assisted in troubleshoot commercial products. Conducted paint tests and designed experiments to characterize organic coatings (High Solid Acrylic Bake Enamel). Conducted inspections on metal finished products. Assured compliance with Federal and State regulatory agencies at the conversion coating and painting processes. Reviewed MSDS and VOC limits for the coatings used in the electrostatic paint process system. Submitted proposals, coordinated and supervised capital projects such as: Paint Sludge removal in a Down Draft Wet Booth Using a Paint detactifier treatment with a Centrifuge; Design, Installation and start-up of an Electrostatic Paint System; Conversion from Normal Zinc Phosphate Line into a Low Zinc phosphate Manganese Modified; Conversion of the Batch Specialty Coating into a Continuous Application Coating Line; Design and installation of a Chemical Zinc Phosphate Chemical Feeding System, and the Design and Installation of a Fluorescent Lightning System for paint parts and inspection). Managed budget and installation of metal machining equipment such as Water Jet System, CNC Punch Press, Forming Machines, Cold Saw and others. Evaluated and selected suppliers and provided recommendations to them about modifications of their coating formulations. Provided recommendation on material selection for designing projects. Proficient on the formulation of high-performance polymers, acrylics, epoxy, polyester, and fluorocarbons. Served as a consultant for other S&C's divisions such as R & D, Analytical Laboratory, Environmental and Production CKP, etc. Experience using the SEM and Bucker x-ray laboratory instruments. |
|||
Years | Employer | Title | Department |
Years: 1997 to 1998 | Employer: E/M Corporation | Title: Plant Engineering Manager Operations | Department: |
Responsibilities:Supervised and provided support to wastewater treatment plant personnel and systems, analytical 'abor8tory, maintenance department, and coating plant. Implemented and reviewed waste management operations (i.e., hazardous waste handling, manifests, wrote regulatory documentation for the State, Local and Federal agencies, and submitted VOC's monthly reports. Developed, implemented, and monitored written programs regarding health and safety issues (i.e., conducted monitoring-exposure tests, provided training regarding personal protection and health and safety compliance). Developed and implemented preventive maintenance programs and coordinated capital projects (i.e. VOC abatement system using Catalytic Incinerator or RTO, a Complete Boiler Room package system). Served as a technical consultant for other ElM facilities throughout the U.S. Provided specifications and recommendations regarding changes on pigments concentration such as Molybdenum Disulfide, Graphite, and Fluorocarbons [Teflon] as part of a solid film lubricant formulation. Participated in the research "Solid Film Lubricant; Enhancing mechanical and corrosion performance using different Epoxy Based Binders ". |
|||
Years | Employer | Title | Department |
Years: 1996 to 1997 | Employer: B.L. Downey, Company | Title: Chemical Engineer | Department: |
Responsibilities:Served as Process/Polymer Specialist overseeing the E-Coat, Dip Coating and Powder Coating lines. Supervised and provided training to the personnel working in the Electrode position Coating (E-Coat) line, Powder Coating lines, Wastewater Treatment Plant, and the Analytical Laboratory. Recommended and specified adequate parameters for coating materials (i.e., Powder: epoxy, polyester, and TGIC; Liqui4Coating: Nylon and rubbers; E-Coat: cathodic, two component paint, epoxy resin, and black pigmented paste). Coordinated with outside contractors the installation, startup, and validation of the E-Coat line such as validation of the chemical and manufacturing processes of the E-coat line and conducted audits. Provided recommendations to chemical suppliers to determine the paint used in the E-Coat line. Implemented and reviewed the quality control system for the E-Coat plant. Reviewed and updated standard operating procedures (SOPs). |
|||
Years | Employer | Title | Department |
Years: 1993 to 1995 | Employer: Warner Lambert, Fajardo | Title: Chemist | Department: Stability Department |
Responsibilities:Involved in the selection of ordering new equipment. Familiarized with GMP requirements. Experience in the calibration of laboratory equipment. Experience using HPLC, LC-MS, GC, FTIR, UV,Karl- Fisher and other analytical instruments. Performed data approval for solid dosage and water samples. Verified laboratory results for solid dosage and water samples. |
Career Accomplishments
Licenses / Certifications |
---|
Industrial Wastewater Treatment Plant Operator (Class K License), IEPA, July 1997. Protective Coatings for Industrial Structures Certification, SCPC,1999 Manage, handling and purchase explosive chemicals |
Additional Experience
Training / Seminars |
---|
Training: Management Skills - Coaching and Management Skills Training, AMA, October 1997. Cathodic SST Electrocoat System Training, TTX, Broadview, IL, 1996 Internal Auditor Training - (ISO 9000), Institute of Economic Technology, October 1997. The Complete How to Guide - OSHA Training, AMA, October 1997. Seminar of RCRA Air Rule Test Methods, U.S. EPA, March 1998. Introduction to Metallurgy: S&C Electric Company, Chicago, 1L, 1999. Machines, Tools and Applications Class: S&C Electric Company, Chicago, IL, 1999. FTIR class: S&C Electric Company, Chicago, Illinois, 1999. Certified ISO 9000 Auditor. Lean Manufacturing Coach Certified Thermoforming Design for Designers, SPE, Chicago, IL, 2004 Project Management Course, APICS, 2004 ORACLE –Material Super User, 2008 Windchill |