Expert Details
Bulk Metal Forming, Forging, Modelling & Simulation, Process Improvement
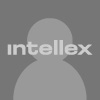
ID: 731755
United Kingdom
Computational modelling and simulation of cooling rates in large forged components can provide the essential temperature data needed to predict the volume fraction of microstructural phases present through the section of a cooled part. Temperature data measured from a rejected shaft end were used to validate the model which could subsequently provide the thermo-physical material data needed to predict cooling rates in similar components. Simulations were conducted using the finite-element modelling software QForm (V7.2) where sensitivity studies were undertaken to determine any differences in predicting temperature between the 2D and 3D versions. The predicted temperature data from the simulations show excellent correlation with the measured data at the surface, mid-radius and centre of the part during oil quenching.
The client now uses the model to optimise design criteria such as part geometry to predict the cooling of similar components. These cooling curves can be compared against continuous cooling transformation (CCT) diagrams so that the volume fraction of detrimental microstructural phases can be predicted.The continuous drive toward higher operating efficiency, greater reliability and longer life of steam turbines has introduced a need for higher integrity components to operate at higher temperatures and pressures. This poses several material and processing challenges to ensure that the components have metallurgical stability and the required mechanical properties in the high temperature environment.
Modelling the open-die press forging process, used to manufacture steam turbine discs from cast ingots, is complex due to the variation of strain, strain rate and temperature within the ingot. These variations mean that recrystallisation and grain growth do not occur uniformly throughout the ingot. Severe plastic deformation is used to promote recrystallisation in order to refine the grain size and improve strength and toughness properties.
A major part of the modelling described in this paper involves prediction and validation of strain, strain rate and temperature distributions during open-die forging. A sensitivity study has confirmed the requirement for accurate thermal and physical data such as Interfacial Heat Transfer Coefficient (IHTC), work-piece emissivity, specific heat and friction coefficient. In this paper experimental determination of these data for the grade of heat resistant steel being modelled, over process parameter ranges appropriate to open-die forging operations, is described. Incorporation of these data into a finite element-based model for strain variation within an ingot is reported with consideration and measurement of dead zone for thermo-mechanical simulation trials.
Education
Year | Degree | Subject | Institution |
---|---|---|---|
Year: 2014 | Degree: PhD | Subject: Metallurgy and Materials (Efficient Fossil Energy Technologies Engineering Doctorate) | Institution: University of Birmingham, UK |
Year: 2009 | Degree: MRes | Subject: Innovative Manufacturing | Institution: Cranfield University, UK |
Work History
Years | Employer | Title | Department |
---|---|---|---|
Years: 2009 to Present | Employer: Undisclosed | Title: Process Improvement Consultant | Department: |
Responsibilities:- Advising decision makers on process improvement and manufacturing efficiency- Technical report writing |
|||
Years | Employer | Title | Department |
Years: 2004 to 2005 | Employer: Portway Motor Centre | Title: Computer Administrator/Technician | Department: |
Responsibilities:- Development and maintenance of the company website and database- Vehicle advertising - Sales |
|||
Years | Employer | Title | Department |
Years: 2003 to 2013 | Employer: Sports Leisure Management | Title: Part-Time Swimming Instructor | Department: |
Responsibilities:- Developing the competency and technical swimming ability of both adults and children- Teaching swimming principles and skills including life saving, diving and synchronised swimming |
Career Accomplishments
Associations / Societies |
---|
Industrial Metal Forming Technologies affiliate member, Institute of Energy affiliate member, Graduate Member of the Institute of Materials, Minerals and Mining, |
Awards / Recognition |
---|
Institute of materials, mineral and mining best project award 2009 |
Publications and Patents Summary |
---|
He has two publications as part of conference proceedings and one journal publication. |
Fields of Expertise
continuous quality improvement, improvement, manufacturing efficiency, manufacturing process development, manufacturing process optimization, metal-related quality improvement, operational process improvement, optimization, process modeling, process optimization, product improvement, productivity improvement, quality improvement, hot working, materials engineering, metal forging, metal forming, metallurgy, press forging, process simulation, roll forging, steel