Expert Details
Aluminum Die Casting Operations, Metal Cleanliness & Die Lube Dillution and Application
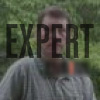
ID: 725855
Tennessee, USA
Doehlar Jarvis, working in their die cast department, where he manually ran the die cast machines, gaining the
skills and knowledge necessary for producing fine quality aluminum castings. He has developed skills such as
solder removal from dies, increasing the machines operational availibility, reducing cracks in castings, reducing
porosity in castings and proper die lube application. Expert worked as a service technician where he set the dies
and adjusted pressures and perameters ensuring that the die cast machines were ready for production runs. Also
at Doehlar Jarvis, Expert spent 10 years working in their Quality Assurance department as a lab technician. In this
capacidy he assisted the die cast department by metal testing, such as chemistry analysis, utilizing a
spectometer for alloys such as 383, A383, 380, 356, and 319, grain size analysis, density testing, hardness
testing and porosity analysis utilizing a fluoroscope machine. Expert has also performed sand test on foundry
sands, such as PH determination, ADV {acid demand value}, grain fines and LOI {loss on ignition} to determine
resin levels. He also monitored die lube dillution ratios via an evaporation test. Expert worked with metallurgists to
lower scap rates by reducing porosity in aluminum die castings, reducing oxides in metal by a k-mold test. Expert
has experience in metal cleanliness such as oxide removal and furnace cleaning.
Expert has spent another 6 years working for a Japaneese die cast company, as a Quality Assurance Associate, at
this company Expert has done full layouts of aluminum die castings by reading blueprints and ensuring all
dimensions are correct with the use of an optical scope, coordinate measuring machine, height gauges and a
contour machine. Expert has performed CPK studies to verify the casting machines capability for production runs.
Also Expert has worked with machining departments to verify tool changes and adjustments for a smooth machined
surface of aluminum die castings.
Expert has experience in maintaining Quality certifications such as QS9000 and TS16949. Expert has experience in
the calibration of spectrometer's, mixing of metals to achieve the proper alloy, degassing of molten metals,
sedimentation testing of castings, impregnation of castings, surface testing of machined surfaces. Expert achieved a
level 2 fluorocope certification and recieved a kaizen award in 2006.
A diecast engineer who was new at his company came to him often for advice on diecast problems or issues, because he new the expert had operated a diecast machine for many years. The expert offered advice on porosity reduction.He advised his plant to install a filter in holding furnace to prevent oxides from being poured into castings.He suggested self-analysis of all incoming sows or ingots, never trust vender samples when buying metal.He gave advice to a company on how to melt scrap AC2B metal and pour it into ingot molds and sell it as certified AC2B metal instead of selling it for scrap.He introduced density testing to a plant to check for porosity in castings.
He also offered advice on doing k-mold tests on molten metal to check for oxides.
He done a test on the dilution of die lube. This was a three month study in wich data was colected, graphed and submitted to the compay. This test proved that improper die lube ratio's caused dies too solder more and need to be polished more often. The company was pleased with the results.
Education
Year | Degree | Subject | Institution |
---|---|---|---|
Year: 2005 | Degree: | Subject: Diecast Opperation/QA Inspection | Institution: Doehlar Jarvis |
Work History
Years | Employer | Title | Department |
---|---|---|---|
Years: 2006 to 2012 | Employer: Kawasaki TN. | Title: Quality Assurance Associate | Department: Quality Assurance |
Responsibilities:Expert has done final Inspection of castings, used a cmm to verify dimensions, used a spectrometer to analize alloys, used an optical scope to verify dimensions, |
|||
Years | Employer | Title | Department |
Years: 1986 to 2006 | Employer: Doehlar Jarvis | Title: Lab Technician | Department: Quality Control |
Responsibilities:Expert operated diecast machines for ten years, worked in a testing lab for ten years, adjusted pressures parameters, set up die cast machines and troubleshot problems. Tested alloy metals for chemistry content, grain refinement, hydrogen content, oxides ect. Used a Flouroscope machine to monitor porosity in castings. Helped to solve many porosity problems. |
Career Accomplishments
Licenses / Certifications |
---|
Level 2 Flouroscope certificate, 2006 kaizen award continual improvement |
Awards / Recognition |
---|
2006 Kaizen award |
Publications and Patents Summary |
---|
Just finished writing a book about "The Aluminum Die Cast Process" and in the process of having it published. |
Additional Experience
Training / Seminars |
---|
Achieved level 2 flouroscope certificate, spc training, blueprint reading, GD&T |
Vendor Selection |
---|
Prior experience: Contacts, coworkers, known suppliers, known products that work. |
Marketing Experience |
---|
Machines should opperate efficiently and profitably. |
Other Relevant Experience |
---|
Strive to boost employee morale and rapid continual improvement of the company. |
Fields of Expertise
metal chemical analysis, coordinate measuring machine, quality, aluminum die casting, die casting, metal testing, quality assurance, aluminum solder, die casting lubricant, die castings, die lubricant, die-casting die, inspector training, casting specification, casting porosity, casting defect, continuous quality improvement, casting process, gating and risering