Expert Details
Aerosol Dispensers, Atomizers, Pumps, Closures, Trigger Pumps, Expert Witness, Consumer Products
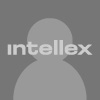
ID: 107989
Idaho, USA
Expert's primary focus has been the design of mechanical and pressurized units to atomize liquid. His design projects included evaluating pressurizing systems to power the spray units, product characteristics, the mechanical break up mechanisms, point-of-contact requirements, and manufacturability. All these factors determine the total unit configuration and the basis for the design required to deliver a liquid spray. To maintain an understanding of the atomizer state of the art and market direction, his studies units manufactured worldwide to gain insight into design and manufacturing process.
One of his strongest abilities involves taking an idea from concept to production. For a system to meet overall package requirements for a consumer product, he evaluates it from two perspectives. The first is profitability for the manufacturer, and second is consumer satisfaction. Before, during, and at the end of the process, these factors are balanced to provide the desired results. Preliminary design concepts, process estimates, production review, modeling, trial parts, functional testing, compatibility, and consumer tests all play a part in the process to provide a finished good that meets the market requirements. Expert prefers to use management by objectives on projects to track progress and provide communication. He has authored design and development manuals for two of the world's largest dispensing systems manufacturers. This includes designing test and gauging equipment used in these methods, as well as determining the system standards. He was one of the original members of the ASTM subcommittee for establishing standards for pumps and safety closures.
In general, he considers himself to be a developer of designs and concepts rather than strictly an inventor. His ability to generate alternate ideas and options for a given design and then applying those to production methods gives expert an all-around understanding of the total product. He has completed designs on a wide range of dispensers, including standard sprayers, lotion pumps, fine mist sprayers, safety caps, dispensing closures, trigger pumps, squeeze bottles, pressurized aerosols, aerosol valves, overcaps, spray through overcaps, and aerosol attachments. This also includes molds, assembly devices, and gages for the construction and assembly of dispensing systems. Expert is proficient with CAD, using both Computer Vision Personal Designer Rev.6 and AutoCAD 12. He has approximately 50 patents covering many of the above and numerous designs that are not patented.
In his management of research and development groups, he became an expert in all forms of delivery devices, covering products from liquid to gels. Self-leveling and nonself-leveling products require different methods of dispensing. He has a thorough understanding of product containment and control of viscous products such as gels and paste for consumer products and their affects on dispensing systems.
Due to the complexity of dispenser designs, he maintains that it is very difficult to identify and correct design and functional flaws. This requires a systematic evaluation of the package, which in affect becomes an autopsy of the unit. From superficial observation to microscopic examination of each component part, the process can be very detailed and complicated. Expert understands stress and fracture points generated by design, processing, assembly, and product compatibility.
Expert has seven patents for finger pumps and several more pending. His focus has been on pressure regulating fine mist systems but also covers lotion, trigger, and standard sprayers. He has been responsible for product and customer applications of all types of mechanical dispensing units.
Expert's experience in dispensing devices covers aerosols, pumps, and closures. A wide range of options give each a specific advantage depending on point-of-application requirements. Due to the relative design and construction of each of these systems, they can be altered to modify their form of delivery. He has become adept in evaluating the design and construction of these systems and their variations. Many of his assignments have been to critique designs from inventors, or other companies, for the purpose of purchasing or business acquisition.
Expert maintains that nozzle use on dispensers is relatively limited but has a large application in aerosol packaging. He has worked on applications and research to improve extension tubes and basic nozzles for both pump and aerosols. He believes that trigger sprayers are more reliant on nozzle designs than are other dispensing systems due to their range of product application. Expert has completed numerous designs and applications of nozzles on consumer type systems requiring delivery of a liquid in a specific manner. He has been involved in the design and construction of multi-position nozzles, multi-function nozzles, foaming devices, and tamper evident features for trigger pumps. He has also conducted research in areas of manufacturing processes to provide new configurations of extruded nozzles.
His experience with package closures covers continuous threaded plastic closures, metal closures, crimp-on ferrules, snap-on closures, plugs, ultrasonic welded closures, safety caps, and integral devices. Most of the consumer products he has been involved with require some type of closure to contain the product and affix a delivery system to the package. His strongest points are systems closures where more than one function is provided by the closure device.
Over the last 40 years of product development, expert has been involved with five major trigger pump programs and holds approximately six patents for their construction or modification. Other projects include cost reductions, production-related problems, functional enhancements, aesthetics, and ergonomics.
Most of his 40 years of design experience has centered on plastic parts and assemblies, particularly the design of closures for use with finger pumps, trigger sprayers, threaded bottles, and dispensing packages. This has included unit cavity molds and production equipment. Expert has been involved in quality procedures and methods for the production of plastic closures. Additionally, he is skilled in identifying and configuring several paths a part or assembly design can take based on identified parameters of process and function. Multi-part assemblies require an understanding of part and system features such as undercuts, snap fits, sliding fits, seals, ribs, etc. These design features affect the assembly function as well as individual part characteristics. He has extensive experience in the balance of design between component and assembly.
Most of the parts he has worked on are smaller than a bar of soap, many the size of a pencil eraser. The design of small parts has a different scale of thinking in that their features require a more critical configuration due limited space and movement. Interaction with other parts is then affected by the reduction of cross-sectional area and the working space available. Expert has worked on consumer, beverage, household, medical, and institutional applications. He is proficient in the design of extruded or injection molded parts. The primary materials of construction that he has worked with include acetals, nylons, polypropylene, polyethylene, anamides, and other related injection materials. He applies good manufacturing practices to parts designs for both molding and high-speed assembly.
Expert's experience with sealing has forced him to focus on secondary parts in addition to the package and closure means. The sealing of a container is the primary function of all dispensing devices. Sealing methods that he has used in this type of project include liners, gaskets, sonic welding, adhesives, pressure-sensitive fillers, and plugs. As an inventor of spraying devices, his goal is to provide a design with the ability to deliver a product to a specific point of contact in a controlled form. This objective requires special mechanical break-up nozzles to convert a pressurized product into small particles. Expert has designed numerous nozzles for use on aerosol, finger pumps, and trigger sprayers and has recently been granted a US Patent on a new concept for providing improved product flow through a nozzle device.
Approximately one third of his research time has been spent on the design, development, and production of sprayers to include standard type finger sprayers, dispensing pumps, and trigger sprayers. He has also been instrumental in the planning, execution, and maintenance of production line requirements.
Expert has evaluated the assembly process to determine the effect on finished goods.He has reviewed mold construction to ensure on time delivery and quality structure.He has designed and engineered the development and parts for plastic products.He has reviewed production mold design and dimensions to determine the effect on product function.
Education
Year | Degree | Subject | Institution |
---|---|---|---|
Year: 1972 | Degree: AA | Subject: Liberal Arts/Engineering | Institution: San Bernadino College |
Work History
Years | Employer | Title | Department |
---|---|---|---|
Years: 2001 to Present | Employer: Undisclosed | Title: President | Department: |
Responsibilities:Consulting for plastic products; concept development, design, engineering, failure analyis, development, proto typing, production support. |
|||
Years | Employer | Title | Department |
Years: 1992 to 1996 | Employer: Seaquist-Perfect | Title: Director of Advanced Technology | Department: Consumer and Personal Care |
Responsibilities:Developing new products and processes for the consumer, household, personal care dispensing industry. |
|||
Years | Employer | Title | Department |
Years: 1987 to 1992 | Employer: Calmar | Title: Vice President of Research and Development | Department: R&D |
Responsibilities:Directing the design and production start-up on new porducts. |
|||
Years | Employer | Title | Department |
Years: 1976 to 1987 | Employer: Seaquist Valve | Title: Technical Director, Manager, Development Engineer, Pump Products | Department: Pump Products |
Responsibilities:Designing and developing new dispensing closure, aerosol and pump products. |
|||
Years | Employer | Title | Department |
Years: 1968 to 1976 | Employer: Calmar | Title: Project Engineer | Department: Sprayer |
Responsibilities:Responsible for the design, development and product of fine mist sprayers. |
International Experience
Years | Country / Region | Summary |
---|---|---|
Years: 1979 to 1987 | Country / Region: France | Summary: Coordinated product research, design and the development of dispensing systems. |
Years: 2002 to 2005 | Country / Region: The Netherlands | Summary: Consulted on the design and production of dispensing system for the European personal care market. |
Years: 1979 to 1992 | Country / Region: Germany | Summary: Coordinated product development between Europe and U.S. Designed new dispensing pumps, aerosols and closures for both U.S.and Europe. |
Years: 2002 to 2007 | Country / Region: England | Summary: Directed the development of pump systems for pharmaceutical and personal care products. Provided designs and qualification procedures for production. |
Years: 2005 to 2007 | Country / Region: China | Summary: Product development and vendor sourcing. Hired staff and trained techs for R&D and production. Wrote test procedures and methods for product qualification and manufacturing. |
Career Accomplishments
Associations / Societies |
---|
Expert is a past memeber of the ASTM and SPE. |
Licenses / Certifications |
---|
ASTM SPE |
Publications and Patents Summary |
---|
Expert has been awarded 50 U.S. patents for dispensing closures, aerosols, pumps, consumer products, safety devices, plastic items. |
Additional Experience
Expert Witness Experience |
---|
Expert performs as an expert witness for Federal, personal injury and patent infringement cases. |
Training / Seminars |
---|
Expert wrote course outline and taught two courses on plastics processes. |
Vendor Selection |
---|
He has experience locating vendors of: Injection plastics mold design Build assembly machines |
Other Relevant Experience |
---|
Expert has been involved in mold design and construction for development and production of plastic parts as well as assembly equipment for development and production of plastic assemblies. |
Fields of Expertise
atomizer, atomizing, consumer product design, dispenser design, nozzle, plastic closure, finger spray pump, dispensing device, nozzle design, consumer product, consumer product safety, design engineering, design for assembly, design for manufacturability, dispensing, high volume, low cost product design, liquid spraying, molded plastic part, package design, patent, personal care product, plastic bottle, plastic injection molding, plastic molding, plastic package, tamper-evident closure, tamperproof cap, package closure, package dispenser, plastic component design, sealing, spray nozzle, sprayer, aesthetics, business acquisition, aerosol industry, aerosol design, consumer product ergonomics, nozzle pressure drop, aerosol behavior, pressure atomizer, consumer product packaging, plastic bottle leak testing, plastic package leak testing, patentability evaluation, household product, nozzle flow, dispensing package, aerosol, liquid flow through a nozzle, liquid flow, convergent-divergent nozzle, computer-aided design and drafting, aerosol can