Expert Details
Meat Processing
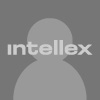
ID: 738054
Alabama, USA
Senior Operations Leader with success in both large and small companies including extensive experience within the ground beef industry. Reversed cash drain performance, converted marginal operations to profitable units positioned for fast growth, which lead to the largest IQF ground beef plant in the world. Mentored various managers who have move into key roles throughout the industry, developed the management systems, procedures and controls to establish World Class Operations at the Butler location. In previous responsibilities Expert was leading Cargill Protein organization into the future with best practice sharing, innovative ideas, process management systems, and continuous development of leading-edge technology thereby a part of improving profitability in the largest protein ground company in America.
Education
Year | Degree | Subject | Institution |
---|---|---|---|
Year: 1982 | Degree: BS | Subject: Animal & Dairy Science | Institution: Auburn University |
Work History
Years | Employer | Title | Department |
---|---|---|---|
Years: 2016 to 2018 | Employer: Cargill Inc. | Title: Cargill Protein C.O.E. | Department: Cargill Protein |
Responsibilities:Operational expert for all of grind / processing including Turkey, Chicken, Cooked Processed Products, & Ground Beef. Reviewed & make recommendations in 23 different locations across the platform. |
|||
Years | Employer | Title | Department |
Years: 2010 to 2016 | Employer: Cargill Inc. | Title: Operations Lead | Department: Cargill Beef |
Responsibilities:Oversaw all aspects of ground beef & FTB operations for the eight operations inside harvest facilities. Have shared responsibilities with the Fab managers to oversee P&L accountability to operations: safety, engagement of stakeholders, variances, labor, shrink, quality, overhead, cost of nonperformance, formulation, lean point, equipment reliability, total costs, along with capital plans: Help the team to use “Statistical Process Management system” by using high performance work teams to meet expectations.. Along with directing various automation projects to reduce our labor footprint across all locations. Dotted line reports of the GB / FTB superintendents. Instrumental in costing and design proposal to automate & improve operations at the facilities. Worked with the Case Ready grind teams at their seven locations to review operational efficiencies, layouts for improvements, shrink, variance & general growth of the ground beef business. |
|||
Years | Employer | Title | Department |
Years: 2008 to 2010 | Employer: Cargill Inc. | Title: Asst. V.P. of Ground Beef Operations | Department: Cargill Value Added Meats, Foodservice |
Responsibilities:Oversaw all aspects of three ground beef facilities operations for CVAM FS with P&L accountability to operations: Safety, engagement of stakeholders, variances, labor, shrink, overhead, cost of nonperformance, formulation, lean point, equipment reliability, total costs, along with capital plans. Led the Six Sigma Plus journey: “Statistical Process Management system” using high performance work teams. Along with directing various automation projects to reduce our labor footprint across all locations. Total CVAM FS fixed budget of 65 million and Variable budget of 950 million. Direct report of GM’s and CVAM FS Corp. Engineer. Cargill has two other ground beef operations supplying McDonald’s that attend Expert's weekly operation meeting for best practice and efficiencies improvements. Instrumental in costing and the design proposal, which resulted in Cargill being awarded the west coast McDonald’s ground beef business. |
|||
Years | Employer | Title | Department |
Years: 2001 to 2008 | Employer: Cargill Inc. | Title: General Manager of Butler, Wisconsin location | Department: Cargill Meat Solutions |
Responsibilities:Increased total capacity at both North and South Plant’s to meet sales demand by setting up rotating staffs. A six day production week was the result with a sanitation and maintenance schedule in meet efficiencies required. Volume is now over 5.5 million per week.• Designed and added Arby’s operations to the location, which increase the efficiencies from it previous location by over 60%. • Cargill’s Milwaukee Distribution Center a 20 million capacity operation with 90 employees was made a direct report. Work with the team to develop true efficiencies measurements. Redesigned several progresses around picks, staging, transfers, which lead to increased accuracies and lowered damaged. • Improved Sister IQF Ground Beef location through creating a manual for their operations and implementing best practices. • Work ongoingly with Cargill Inc. as a whole on several initiatives involving various parts of the business. ex: acquisitions, innovative technologies, best ground beef practice evaluations, new business initiatives. |
|||
Years | Employer | Title | Department |
Years: 1994 to 2001 | Employer: EMMPAK Foods Inc. | Title: Director of Operations | Department: Operations |
Responsibilities:• Managed 400+ employees and overseeing 19 production lines in three different plant locations.• Increased efficiency of North Plant by 30% or approximately 1 million-dollar savings annually. • Increased South Plant efficiency by 28% or approximately 1.5 million-dollar annual savings. • Set-up procedures, redesigned facility, added MAP, IQF, Fresh lines to Emmber Chub Grinding plant. Installed new management then turned over to Peck Foods. • Assisted in the design and oversaw construction of the 1.5 million pound operation, which could be increased to 3 million pounds, known as the South Plant. The South Plant is one of the most technologically advanced ground beef plants in the world. It is running as one of the lowest cost plants of its kind in the country as a result of: • Set-up of a fully computerized tracking, data collection, automatic grinding. • Developed and designed, with engineer, an automated case packing system to lower costs, and increase quality for real time results, with the addition of fully automated box forming and robotics box stacking. • Oversees South Plant Management: including managers and superintendents. North Plant: • Redesigned the 10-line operation removing bottlenecks for improved process flow. • Oversees the North plant production manager and superintendents. Other responsibilities are the same as the listed below Plant Manager responsibilities. Consultant for RSI (purchasing arm of Burger King) at Diversity Foods, Virginia. 1996 • Evaluated management processes, set-up procedures to improve efficiency, and lower costs of the total operation. As a result the plant dramatically improved in all process categories contributing to Wis-Pak Foods receiving “Supplier of the Year Award.” |
|||
Years | Employer | Title | Department |
Years: 1992 to 1994 | Employer: Wis-Pak Foods Inc. | Title: Plant Manager | Department: Operations |
Responsibilities:• Managed total operations including 230+ employees in the following departments: operations, sanitation, maintenance, warehouse, purchasing, human resource, outside cold storage, receiving & shipping, and 11 production lines.• Increased productivity and lowered costs by setting objectives throughout the organization. • Set-up capital expenditures, total budget, 5 year strategic plan for improvement of facility including an expansion plan. • Managed 500+ product items including various additive lines: “T.V.P., various seasoned products, cooked chili/taco lines.” • Researched, tested and set-up various innovative technologies through out plant to increase throughput and lower labor costs. |
|||
Years | Employer | Title | Department |
Years: 1990 to 1992 | Employer: Wis-Pak Foods Inc. | Title: Technical Support Manager | Department: Sales support |
Responsibilities:• Field support representative for large to medium sized National & Food Service Restaurants.• Developed quality checks to ensure quality in restaurants of our product lines. • Developed cook & handling procedures to assist store managers in quality to customers. • Solved in plant problems relating to customer concerns. |
|||
Years | Employer | Title | Department |
Years: 1989 to 1990 | Employer: Wis-Pak Foods Inc. | Title: Plant Manager of Jacksonville, FL. location | Department: Operations |
Responsibilities:• Managed 130+ employees in production, receiving, maintenance, warehousing & shipping.• Increased efficiencies of over 200 product items. • Set up budget, objectives & reporting structure, for production of fresh, frozen, ground beef and T.V.P. products. |
|||
Years | Employer | Title | Department |
Years: 1984 to 1989 | Employer: Golden State Foods Inc. | Title: Senior Shift Supervisor | Department: Operations, McDonald's ground beef location |
Responsibilities:• Managed production shift, receiving & shipping• Handled union issues • Key project/safety leader • Developed several tracking reports for improved efficiency. |
|||
Years | Employer | Title | Department |
Years: 1982 to 1984 | Employer: Village Meats Inc. | Title: Quality control Tech. to Assistant Processing Manager | Department: Quality control to Operations |
Responsibilities:A producer of fresh ground beef for large National Accounts and Food Services - a 5-line operation.Assistant Processing Manager • Managed production, receiving, shipping & sanitation. Quality Control Technician First 7 months- |
Career Accomplishments
Licenses / Certifications |
---|
Continuing Education Includes Courses Such as: 2005 Cargill Leadership Academy – 18 month program for select key leaders. 2000 American Management Association – Financial Operations for Executives 1988 American Management Association – Developing Interpersonal Skills for Management 1987 American Management Association – Developing Operational Management Techniques Professional Organizations: Member of American Meat Institute, PARANET, Former Board Member of Butler Chamber of Commerce |