Expert Details
New Product Development, Lean, Six Sigma Blackbelt, Semiconductors/MEMS
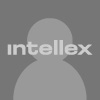
ID: 726194
Virginia, USA
In the last five years, Expert has worked within the MEMS industry, delivering pressure transducers based on SOI material, accelerometers, AFM tips, optoelectronic devices, RFMEMS and others, requiring precise control of silicon micromachining steps, including wet (KOH, TMAH) and dry etch techniques. Structures include carefully defined depths on wells to within 0.25 microns, releases that allow bridges to be completed to hold accelerometer mass elements, small RF vias, coated mirrors for IR transmission. Yield improvements on the products he has worked have been significant, in one case improving from 10-15% yields due to extensive silicon damage to over 90%.
Expert worked at Air Products and Chemicals Inc, Schumacher division for 11 years, developing CVD precursors and delivery systems/vaporizers for precursors such as TEOS, TMCTS, TMB, TEB, TMPI (for doped and undoped silicon applications), TDEAT and TDMAT (for Ti depositions), as well as others. He wrote a number of Applications Notes and White Papers for use by customers in developing and optimizing their processes. Was R&D program manager for CupraSelect, copper CVD precursor. Expert has experience in synthesis, purification, packaging, delivery and application of CVD precursors. He wrote a textbook on CVD/PVD processing for ICE in 2001.
Expert has extensive experience in PVD processing (sputtering) of many materials, including aluminum, copper, Ti, TiW, gold, tantalum, nickel, and others, including dielectic materials. He has used sputtering technologies to develop via/contacts, VLSI interconnects, power distribution wiring, as well as bonding materials and for electronic shielding. Improvements included developing process that improved SOI sensor reliability by over 70x, and in another case, improving product hermeticity by 5x.
Six Sigma Blackbelt specializing in New Product Development. Design for manufacturability is a key aspect in Expert's toolbox. He has designed dozens of products over the years, with a heavy emphasis on ensuring that the key elements of design for manufacturability (DFSS) are included up front. These include defining the product requirements to meet customer needs, ensuring that the process capabilities are appropriate for those product requirements - and that companies do not spend excessively on capabilities that are not needed - and finally, ensuring that proper metrology, SPC and documentation are in place to guarantee product success.
Expert spent many years of his career as a diffusion process engineer, using ion implant, liquid source diffusion (POCl3 and BBr3, for example) and solid source diffusion sources. Results included fixing a major yield-killer on Flash EPROM devices, as well as major yield improvements on DRAM and microprocessor devices. This experience is covered in two of Expert's semiconductor books.
As a process engineer, Expert has spent many years optimizing manufacturing processes, from OEM equipment and contract manufactured products, to thermal conditioning of Mil-Spec sensors, chemical manufacturing processes, to IC manufacturing processes. Cost of ownership, return on investment, effects on product yield and reliability, and imlementation of DFSS and DMAIC are primary drivers for Expert and led to his attaining a Six Sigma Blackbelt.
Expert has written three books on IC Manufacturing, covering all aspecs from CVD to photolithography, to etch, to implant to packaging. He has direct experience in all of these areas, with 15 years within wafer fab operations, as a process engineer, an engineering manager and as a fab manager, along with another 12 years within the OEM field supporting semiconductor fabs. He has experience with CMOS and BiCMOS parts, such as microprocessors, DRAMs, SRAMs, EPROMs, Flash EPROMs, and ASIC parts, as well as MEMS devices, such as pressure transducers, accelerometers, AFM sensors, optoelectronic devices and RFMEMs.
Expert helped lead Air Products' Schumacher division in their ISO-9001 certification effort, understanding and training on the specifications, obtaining documentation, presenting documentation to the ISO auditors, and correcting any problems. The group I led had the highest rating in the business unit. Ultimately, we took the plant to the Malcolm Baldridge Awards (finishing as a runner-up), and never lost a single potential customer order for anyone who toured our leaned-out, high quality facility.
As engineer, and fab manager over MEMS lines for the past five years, he has experience as well as MEMS devices such as pressure transducers, accelerometers, AFM sensors, optoelectronic devices and RFMEMs. Yield, reliability and delivery issues all improved greatly during Expert's times on these product lines. Accelerometer yields improved from 10-15% to over 90%, and pressure sensor drift was reduced from over 7% to under 0.1% through intense thermal cycling regimes.
Expert led the development of processes to bring on several styles of accelerometer, improving die yields from 10-15% to over 90%. Product stability also was greatly enhanced, as well as bondability, line yields/breakage, and costs and throughput time reduced enormously.
Expert has written three books on IC Manufacturing, covering all aspects from CVD to photolithography, to etch, to implant to packaging. He has direct experience in all of these areas, with 15 years within wafer fab operations, as a process engineer, an engineering manager, and as a fab manager, along with another 12 years within the OEM field supporting semiconductor fabs. He has experience with CMOS and BiCMOS parts, such as microprocessors, DRAMs, SRAMs, EPROMs, Flash EPROMs, and ASIC parts, as well as MEMS devices, such as pressure transducers, accelerometers, AFM sensors, optoelectronic devices and RFMEMs.
Expert has been directly involved in determining the market viability of numerous OEM products, as well as integrated circuit and MEMS products, including optoelectronic devices. In performing this, Expert was able to lead Schumacher/Air Products OEM equipment line from $2.8MM revenue (with a loss) to >$20MM revenue (very profitable) over a five year span.
Expert has been directly involved in determining the market viability of numerous OEM products, as well as integrated circuit and MEMS products, including optoelectronic devices. In performing this, Expert was able to lead Schumacher/Air Products OEM equipment line from $2.8MM revenue (with a loss) to >$20MM revenue (very profitable) over a five year span.
Expert has written the New Product Development procedures for the last couple of companies he has worked for based on a combination of Stage-gate and ISO-9001 requirements. The comprehensive specifications are designed around the techniques he has used for 15 years in bringing many products worth well over $100MM in revenues to market. One of the biggest issues that Expert finds is that companies like to skip pieces of the process, however in the long run, the companies invariably get to perform those steps, usually at great cost and rush at the end of the development cycle. Like college courses, is makes more sense to do the homework up front, and be ready for the final when it arrives.
Expert has given many professional presentations, both to senior managers and to customers, and has participated in industry roundtables. This includes being the keynote speaker at the Semicon/West Microcontamination Conference in 1998.
Expert has a Six Sigma Balck Belt, obtained after using Six Sigma and associated techniques for many years driving product quality. It is important to consider quality at every stept in the product life-cycle, starting with designing the product for manufacturability using DFSS techniques, continuing improvements through the use of DMAIC and SPC, and continuing through product release and even through end-of-life. Reponsible product management includes considering what happens to the product when it is done with it's useful life. For instance, when the copper CVD program was run, we designed the system to allow us to recapture almost all of the effluent, which could be reconstituted back into precursor materials.
Expert provided support to Metallic Power as Quality Manager and FMEA engineer. Identified and corrected reliability problems and failure modes. He found that the primary cause of Zn-air fuel cell was from leakage in the fittings, which caused both leakage of the electrolyte that caused component corrosion as well as leakage of flammable hydrogen gas. Expert developed test procedures and redesigned pressure sensors to eliminate the impact of static buildup which caused sensor drift for Mil-spec parts. He used a complex Taguchi DOE to idenfity the source of problem, identify a potential solution, test the solution, and finally he documented results. His work provided a 70x improvement in sensor reliability while eliminating 20% of manufacturing steps and reducing product costs. Expert worked closely with IP attorneys to defend intellectual property involving OEM equipment. He was deposed on several occasions, developed good documentation trails, and developed technical arguments to defend property rights.
Education
Year | Degree | Subject | Institution |
---|---|---|---|
Year: 1979 | Degree: BS | Subject: Physics | Institution: Univ of Idaho |
Work History
Years | Employer | Title | Department |
---|---|---|---|
Years: 2006 to 2008 | Employer: Rohm and Haas Electronics Materials | Title: Engineering Manager / Fab Manager | Department: |
Responsibilities:· Drove line balancing and production scheduling effort, cost controls, safety initiatives· Led team to meet product release requirements and improve yields · Rewrote Quality Systems, Document Control, New Product Development procedures · Selection, implementation of MES/MRP systems, SPC. Vendor selection and interaction · Trained production and engineering on product quality and Six Sigma techniques · Implemented solutions to over 100 major engineering projects · Managed engineering team and manufacturing organization of around 40 employees |
|||
Years | Employer | Title | Department |
Years: 2004 to 2006 | Employer: Ametek Aerospace | Title: Sr Principal Engineer | Department: |
Responsibilities:· Managed and drove procurement of sensor subassemblies though multiple vendors, including scheduling, pricing negotiations, and technical, delivery and quality issues· Installed SPC and Six-Sigma tools in numerous processes · Rewrote and implemented New Product Development procedures · Reduced pressure sensor costs and process steps. Improved yields, reliability and stability · Redesigned MEMS sensor product and process flow, including housing, packaging and test · Responsible for engineering issues from wafer fabrication (front-end and back-end), sort/package, electrical test, process chemistry, FMEA, cleanroom operations. |
|||
Years | Employer | Title | Department |
Years: 2001 to 2004 | Employer: Zorich Consulting | Title: President | Department: |
Responsibilities:· Contract Quality Engineering: FMEA and root cause analyses, IP evaluations, technical writing, web services. Products included KOH fuel cell for portable power generation. |
|||
Years | Employer | Title | Department |
Years: 1991 to 2001 | Employer: Air Products and Chemicals, Inc. | Title: Project Manager / R&D Manager | Department: |
Responsibilities:· Equipment Product and R&D Manager over OEM equipment line and ultra-high purity chemical manufacturing line.· Increased OEM equipment line annual revenue from under $3MM to over $20MM · Set and controlled budgets, product pricing, schedules and resource allocation. · Directed activities and managed operation of over 50 employees, including manufacturing, field service, engineering · Drove HazOp teams, as well as product safety and toxicology reviews · Developed marketing and sales programs and tools. Heavy customer interaction. · Designed top-level system and software architectures, tested hardware capabilities, specified components, confirmed products met quality standards. · Hands-on process engineering improved high purity manufacturing, including equipment and procedures for synthesis and purification. · Reduced product cost very significantly, increased yield by 3x, capacity by 50x. · Led engineering effort for ISO 9001 New Product Development certification |
|||
Years | Employer | Title | Department |
Years: 1980 to 1991 | Employer: Previous - Intel, Nanometrics, startups | Title: Process and Applications Engineers | Department: |
Responsibilities:· High precision optics, robotics and metrology equipment, integrated circuits· Process engineering and new process development on numerous high tech manufacturing processes. Improvements and inventions resulted in significant yield and uptime impact · Startup and qualification of new fabrication areas, including development of process recipes, implementation of SPC, product release, and specification writing · Design and development of various metrology and thin film deposition products · Applications management support and heavy customer interface for several types of products, including writing Data Sheets, White Papers, presenting at conferences · Managed applications lab for an Eximer Laser based OEM tool. Invented new processing techniques, responsible for lab/cleanroom operations, customer sample prep and analysis. Key technical member of Core Business Team for business startup. |
Career Accomplishments
Licenses / Certifications |
---|
Six Sigma Blackbelt - Lean, New Product Development New Product Development - SEMI Leadership Skills - Center for Creative Leadership HALT/HASS/FMEA - Apollo Rott Cause Analysis |
Awards / Recognition |
---|
Who's Who in America |
Publications and Patents Summary |
---|
10 patents 3 Technical books 1 Science Fiction book 10 published Articles Public speaking, keynote address at Semicon/West Microcontamination Conference |
Additional Experience
Expert Witness Experience |
---|
Expert can provide depositions and key expert witness testimony in technology/IP disputes. Expert has had significant expertise in determining proper documentation trail for IP defense and for IP development and patent preparation. He has many years of working closely with IP attorneys in developing new products, and has had ten patents issued, others pending and/or applied for, having written the bulk of the patents. |
Training / Seminars |
---|
Six Sigma training on DMAIC and DFSS techniques Keynote speaker at SEMICON/West Microcontamination Conference Training on quality manufacturing processes Published author of three electronics manufacturing textbooks - one on implementation of Quality electronics manufacturing techniques, another a training book on wafer fabrication, the third a training book on CVD and PVD processes. |
Vendor Selection |
---|
Expert has extensive experience on selecting vendors from years as Project and Program Managers for Air Products, Ametek Aerospace and Rohm and Haas Electronic Materials. Some of the products he has selected or advised on include: Manufacturing Execution Software (MES); SPC systems; high purity piping and welding; MEMS manufacturers; custom software development; OEM cabinet manufacturers; chemical vendors; vacuum and other semiconductor manufacturing equipment; metrology and test equipment. |
Marketing Experience |
---|
Many years in marketing in the electronics/semiconductor industry 10 published articles 10 patents 4 books including how to High Quality electronics components Adjunct faculty member at Virginia Tech Pamplin School of Business |
Other Relevant Experience |
---|
CVD / PVD expert Manufacturing process improvement IP technical assessment Six Sigma training New Product Introduction - training and documentation DFSS / DMAIC deployment OEM equipment selection and development Semiconductor process expert |
Fields of Expertise
atmospheric pressure chemical vapor deposition, bulk silicon micromachining, chemical vapor deposition precursor material, copper sputtering, design for manufacturability, drive diffusion, industrial engineering, integrated-circuit manufacturing, semiconductor wafer processing, ISO 9001, micro electrical-mechanical system, microaccelerometer, microfabrication, new product assessment, stage gate process, new product assessment, new product development, project management, presentation quality, quality, quality-by-design, six sigma quality, nanomanufacturing, overall cycle time, lift-off (semiconductor fabrication), microelectronic equipment, ideation, chromium sputtering, aluminum sputtering, life-cycle cost, four point probe, Microsoft Project Manager, rapid thermal semiconductor wafer processing, micromechanical system, nanofiltration, high-purity arsenic, high-purity aluminum, new chemical process operations, chemical mechanical polishing, design-for-quality, metal quality, fiber-optic component product development, rapid product development, product development cycle time, new product design, nanotechnology, water quality, semiconductor material processing, electronic product development, micromechanics, microelectromechanics, new product development management, house of quality, innovation, carbon tetrachloride, optical microlithography, microsensor, metal organic chemical vapor deposition, integrated circuit, epitaxial reactor